- お役立ち記事
- Manufacturing Process of Electric Shavers and Automatic Blade Sharpening Technology
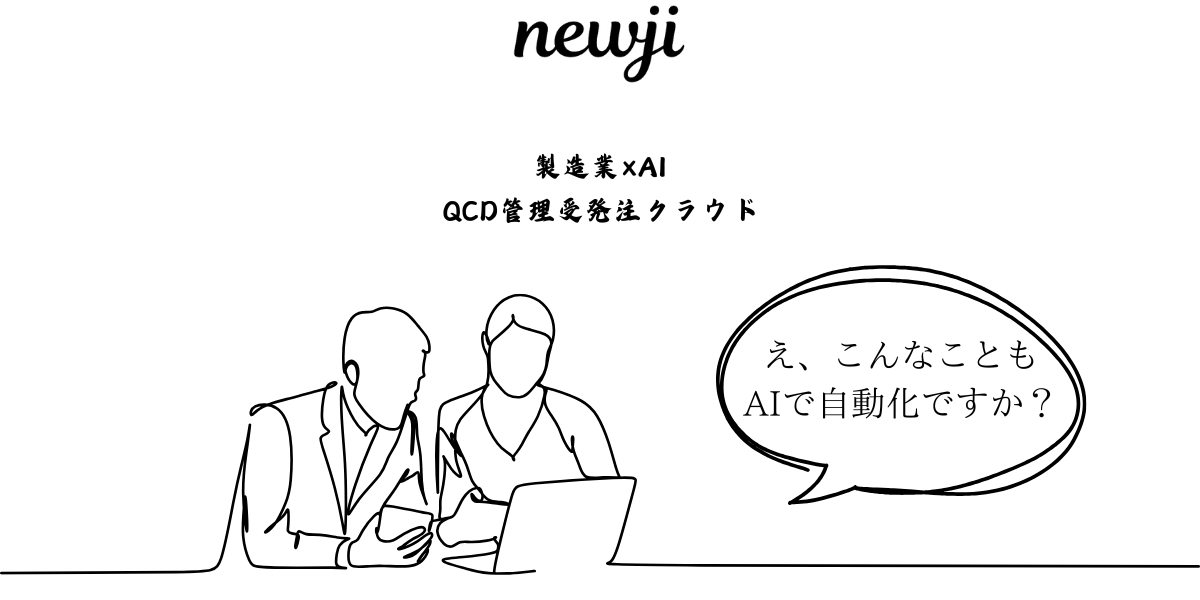
Manufacturing Process of Electric Shavers and Automatic Blade Sharpening Technology
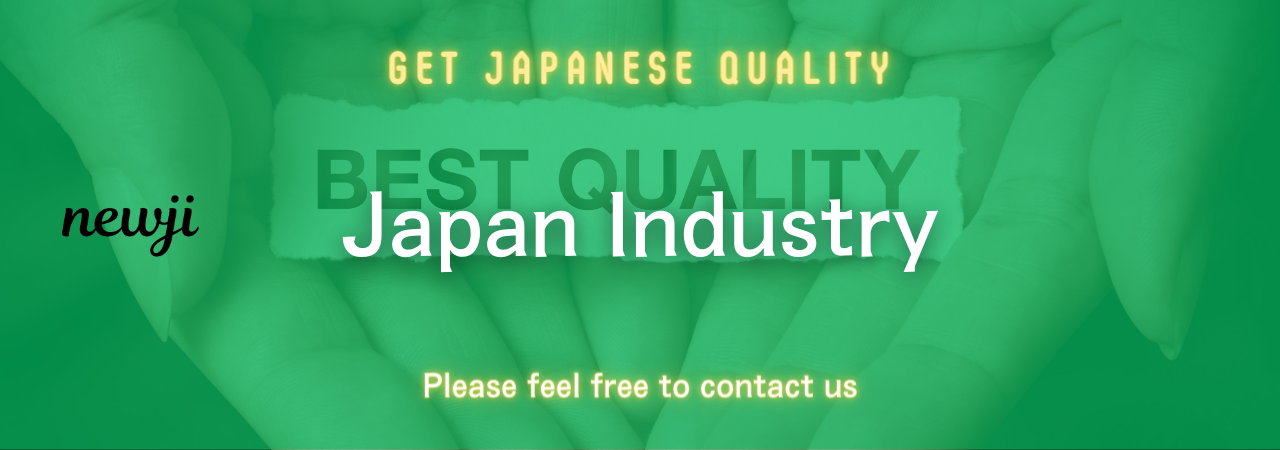
Electric shavers are a popular tool for personal grooming, providing a convenient way to achieve a clean shave without the need for traditional razors.
Understanding the manufacturing process of these devices and the technology behind automatic blade sharpening can help users appreciate the innovation and precision involved.
目次
Materials Selection
The first step in manufacturing electric shavers is selecting high-quality materials that will ensure durability and performance.
Blades are typically made from stainless steel or titanium due to their strength and resistance to rust.
The body of the shaver often consists of durable plastic or metal alloys to withstand daily use.
Choosing the right materials is critical, as it directly impacts the longevity and effectiveness of the shaver.
Design and Prototyping
Once the materials are selected, the design phase begins.
Engineers use computer-aided design (CAD) software to create detailed blueprints of the shaver.
These designs consider various factors such as ergonomics, blade configuration, and motor placement to ensure comfort and efficiency.
Prototypes are then produced, allowing designers to test and refine their ideas before mass production.
Production of Components
The next stage involves manufacturing the individual components of the electric shaver.
Blades are crafted through precise machining processes, ensuring sharpness and consistency.
Injection molding is commonly used to create the handles and other plastic parts of the shaver.
Meanwhile, electric motors and batteries are assembled in separate facilities before being integrated into the final product.
Blade Manufacturing
The blades are a critical component of any electric shaver, and their production requires meticulous attention to detail.
Steel or titanium sheets are cut into the appropriate shapes using laser cutting or stamping.
These blade blanks are then honed to a fine edge through grinding and polishing processes.
Quality control checks ensure each blade meets stringent standards for sharpness and durability.
Injection Molding
Injection molding involves heating plastic pellets until they melt, then injecting the molten plastic into molds to form the desired shapes.
This process is used to make the shaver’s housing, buttons, and other plastic parts.
Careful design of the molds ensures that each piece fits together perfectly, which is crucial for the shaver’s assembly and functionality.
Assembly Process
With all the components ready, the assembly process begins.
Highly automated assembly lines are often employed to increase efficiency and consistency.
First, the motor and blade assembly are joined together, ensuring the blades are properly aligned with the motor’s movement.
Next, other components like the housing, buttons, and battery are assembled around the core unit.
Quality control tests are conducted throughout the process to ensure each shaver performs as expected.
Motor and Drive System Integration
Integrating the motor and drive system is a delicate part of the assembly process.
The motor must be securely attached to the blade assembly, ensuring smooth and efficient power transmission.
Lubricants are often applied to reduce friction and wear, enhancing the shaver’s longevity.
Housing and Final Assembly
Once the internal components are assembled, the housing is attached, encasing the motor and blade assembly.
This step involves fitting the outer shell, installing buttons, and securing any additional features like trimmers or LED indicators.
Each unit undergoes rigorous testing to verify functionality, including checks for blade movement, power output, and battery performance.
Automatic Blade Sharpening Technology
One of the advancements in electric shaver technology is the introduction of automatic blade sharpening systems.
This technology ensures that the blades remain sharp over time, providing a consistent shaving experience without the need for manual sharpening.
How Automatic Sharpening Works
Automatic sharpening systems are integrated into the shaver’s design, using specially designed mechanisms to maintain blade sharpness.
Typically, these systems involve a sharpening mechanism that is activated during normal use or through a dedicated maintenance cycle.
The blades pass through a series of sharpening elements, which gently hone the edges to keep them sharp.
Benefits of Automatic Sharpening
The primary benefit of automatic blade sharpening is consistent shaving performance.
Users no longer need to worry about dull blades, as the shaver maintains its cutting ability over time.
Additionally, this technology extends the life of the blades, reducing the need for frequent replacements and lowering maintenance costs.
Quality Control and Testing
Ensuring that every electric shaver meets high standards is crucial for manufacturers.
Quality control involves a series of tests and inspections throughout the production process.
Performance Testing
Each shaver is tested for performance, including blade speed, motor efficiency, and battery life.
Simulated shaving conditions are used to evaluate how well the shaver handles different types of hair and skin.
Only units that meet strict performance criteria are approved for sale.
Durability and Safety Checks
Durability tests subject shavers to conditions like prolonged use, drops, and exposure to water to ensure they can withstand everyday wear and tear.
Safety checks verify that all electrical components function correctly and that the shaver poses no risk to users.
These comprehensive tests ensure that customers receive a reliable and safe product.
Packaging and Distribution
Once quality control is complete, the shavers are packaged for distribution.
Packaging design is important, offering protection for the product and providing information to consumers.
Boxes typically include user manuals, charging cables, and any additional accessories.
Manufactured shavers are then distributed to retailers worldwide, ready to help people achieve a smooth shave with ease.
Understanding the manufacturing process and the technology behind electric shavers highlights the innovation and precision involved in creating these everyday tools.
With advancements like automatic blade sharpening, users can enjoy consistent performance and longer-lasting products.
資料ダウンロード
QCD調達購買管理クラウド「newji」は、調達購買部門で必要なQCD管理全てを備えた、現場特化型兼クラウド型の今世紀最高の購買管理システムとなります。
ユーザー登録
調達購買業務の効率化だけでなく、システムを導入することで、コスト削減や製品・資材のステータス可視化のほか、属人化していた購買情報の共有化による内部不正防止や統制にも役立ちます。
NEWJI DX
製造業に特化したデジタルトランスフォーメーション(DX)の実現を目指す請負開発型のコンサルティングサービスです。AI、iPaaS、および先端の技術を駆使して、製造プロセスの効率化、業務効率化、チームワーク強化、コスト削減、品質向上を実現します。このサービスは、製造業の課題を深く理解し、それに対する最適なデジタルソリューションを提供することで、企業が持続的な成長とイノベーションを達成できるようサポートします。
オンライン講座
製造業、主に購買・調達部門にお勤めの方々に向けた情報を配信しております。
新任の方やベテランの方、管理職を対象とした幅広いコンテンツをご用意しております。
お問い合わせ
コストダウンが利益に直結する術だと理解していても、なかなか前に進めることができない状況。そんな時は、newjiのコストダウン自動化機能で大きく利益貢献しよう!
(Β版非公開)