- お役立ち記事
- Manufacturing Process of Electric Vehicle Chargers and Safety Standards
Manufacturing Process of Electric Vehicle Chargers and Safety Standards
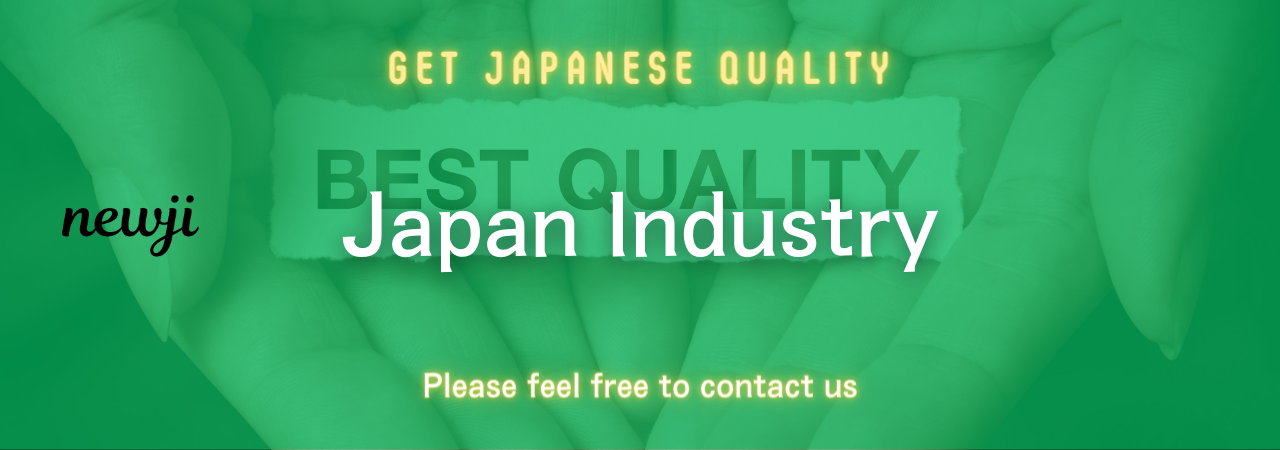
Electric vehicles (EVs) are becoming more common.
As more people switch from gasoline-powered vehicles to EVs, understanding the components and manufacturing process of electric vehicle chargers becomes increasingly important.
Safety standards are equally essential, ensuring that these devices operate reliably and do not pose any hazards to users.
目次
Understanding Electric Vehicle Chargers
EV chargers, also known as EV Supply Equipment (EVSE), serve as the bridge between the power grid and the electric vehicle.
They charge the vehicle’s battery pack, and their efficiency and safety are critical for both performance and user safety.
Types of EV Chargers
There are primarily three types of EV chargers:
1. **Level 1 Chargers:** These are the most basic chargers and use a standard household outlet.
They have lower power output and are ideal for overnight charging.
2. **Level 2 Chargers:** These chargers require a dedicated electrical circuit and are often installed in homes, workplaces, and public charging stations.
They offer quicker charging times compared to Level 1 chargers.
3. **DC Fast Chargers:** These provide the fastest charging times and are generally found in commercial settings.
They are capable of charging an EV to 80% in a relatively short period, making them suitable for long-distance travel.
Manufacturing Process of EV Chargers
Design and Prototyping
The manufacturing process of electric vehicle chargers begins with an in-depth design and prototyping phase.
Engineers and designers collaborate to create an initial blueprint that meets specific performance requirements and complies with safety standards.
Software simulations and physical prototypes are developed to test various aspects, such as electrical flow and heat dissipation.
Component Sourcing
Once the design is finalized, the next step involves sourcing high-quality components.
These typically include transformers, circuit boards, cables, and enclosures.
Manufacturers must ensure that the sourced components meet industry-specific safety and performance standards.
Battery Management Systems (BMS) may also be incorporated to manage the battery’s health during the charging process.
Assembly
The assembly of an EV charger involves multiple stages:
1. **Printed Circuit Board (PCB) Assembly:** The PCBs are populated with various electronic components through automated processes like Surface-Mount Technology (SMT).
Each board undergoes rigorous testing to ensure it meets design specifications.
2. **Housing Assembly:** The internal components, including the PCB and transformers, are housed within durable, heat-resistant enclosures.
The enclosure must be designed to protect the internal components from external elements, ensuring longevity and reliability.
3. **Cable Assembly:** High-grade, heat-resistant cables are attached to the charger, which will be used to connect the EV to the power grid.
Once assembled, the chargers undergo various quality checks, including electrical testing, thermal testing, and functional performance tests.
Quality Assurance and Testing
Quality assurance is a critical stage in the manufacturing process.
Every electric vehicle charger must undergo multiple tests to ensure it meets both performance and safety standards.
Electrical Testing
This involves checking the electrical circuits for consistency and accuracy.
Overload tests are conducted to ensure the charger can handle variations in electrical input without failing or causing any safety hazards.
Thermal Testing
Thermal testing evaluates how well the charger dissipates heat under different operating conditions.
This is vital to ensure the charger doesn’t overheat and become a safety risk.
Functional Testing
Functional tests focus on evaluating the performance of the charger under real-world conditions.
This includes testing the actual charging time, the stability of the power output, and the effectiveness of any built-in safety features like surge protection.
Safety Standards for EV Chargers
Adhering to safety standards is non-negotiable in the manufacturing of EV chargers.
These standards are put in place to ensure user safety and the efficient performance of the device.
International Standards
Several international organizations set standards for EV chargers:
1. **International Electrotechnical Commission (IEC):** IEC 61851 and IEC 62196 are crucial standards that outline the requirements and test methods for conductive charging systems.
2. **Underwriters Laboratories (UL):** UL 2202 addresses the safety requirements for EV chargers, including mechanical integrity, electrical safety, and thermal management.
3. **SAE International:** The SAE J1772 standard is widely adopted in North America, specifying the physical, electrical, and performance standards of EV chargers.
Regulatory Compliance
Manufacturers must ensure their products comply with local regulatory requirements.
This often includes certifications from bodies such as the Federal Communications Commission (FCC) in the U.S., which examines electromagnetic interference, and CE marking in Europe, ensuring the product meets EU safety, health, and environmental requirements.
Future Trends in EV Charger Manufacturing
As the demand for electric vehicles continues to grow, the future of EV charger manufacturing looks promising.
Manufacturers are focusing on increased efficiency, faster charging times, and enhanced safety features.
Wireless charging technology and advanced Battery Management Systems are some of the innovations expected to become standard.
Eco-Friendly Manufacturing
Sustainability is also becoming a crucial focus.
Manufacturers are exploring eco-friendly materials and energy-efficient manufacturing processes to reduce the environmental impact of producing EV chargers.
Integration with Smart Grids
The integration of EV chargers with smart grids is another exciting trend.
Smart grids manage electrical supply and demand more effectively, optimizing the energy consumption of EV chargers and contributing to overall grid stability.
Understanding the manufacturing process and the importance of adhering to safety standards offers both consumers and manufacturers the assurance of reliable and efficient EV chargers.
The future will likely bring even more advancements in this field, making electric vehicle charging more accessible and safer for everyone.
資料ダウンロード
QCD調達購買管理クラウド「newji」は、調達購買部門で必要なQCD管理全てを備えた、現場特化型兼クラウド型の今世紀最高の購買管理システムとなります。
ユーザー登録
調達購買業務の効率化だけでなく、システムを導入することで、コスト削減や製品・資材のステータス可視化のほか、属人化していた購買情報の共有化による内部不正防止や統制にも役立ちます。
NEWJI DX
製造業に特化したデジタルトランスフォーメーション(DX)の実現を目指す請負開発型のコンサルティングサービスです。AI、iPaaS、および先端の技術を駆使して、製造プロセスの効率化、業務効率化、チームワーク強化、コスト削減、品質向上を実現します。このサービスは、製造業の課題を深く理解し、それに対する最適なデジタルソリューションを提供することで、企業が持続的な成長とイノベーションを達成できるようサポートします。
オンライン講座
製造業、主に購買・調達部門にお勤めの方々に向けた情報を配信しております。
新任の方やベテランの方、管理職を対象とした幅広いコンテンツをご用意しております。
お問い合わせ
コストダウンが利益に直結する術だと理解していても、なかなか前に進めることができない状況。そんな時は、newjiのコストダウン自動化機能で大きく利益貢献しよう!
(Β版非公開)