- お役立ち記事
- Manufacturing Process of Electric Water Pumps and Improving Pressure Resistance
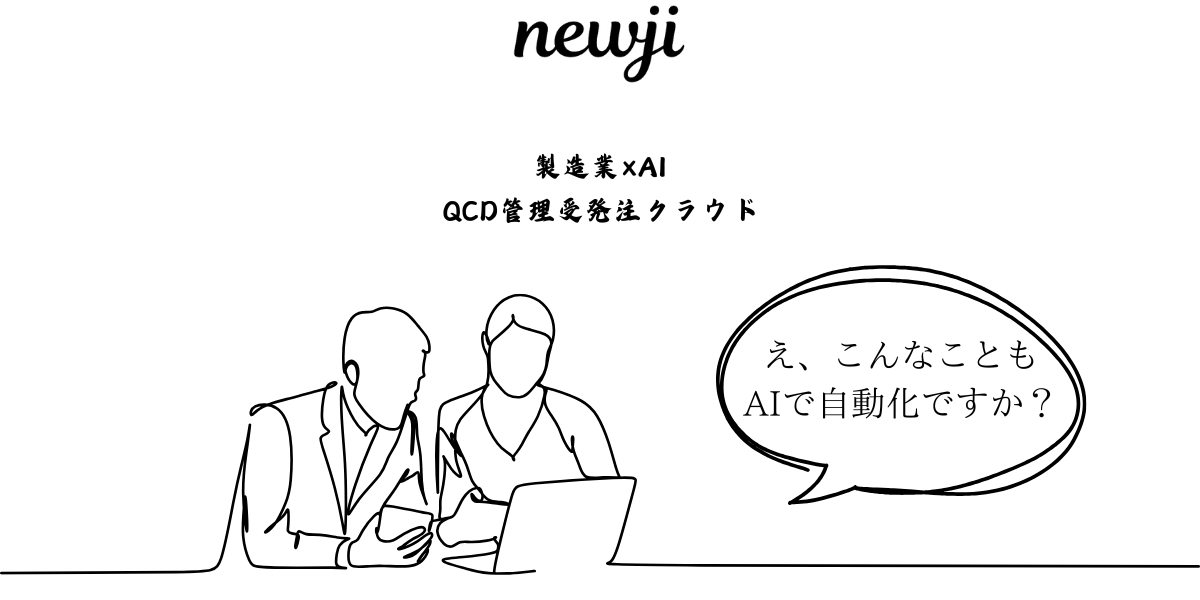
Manufacturing Process of Electric Water Pumps and Improving Pressure Resistance
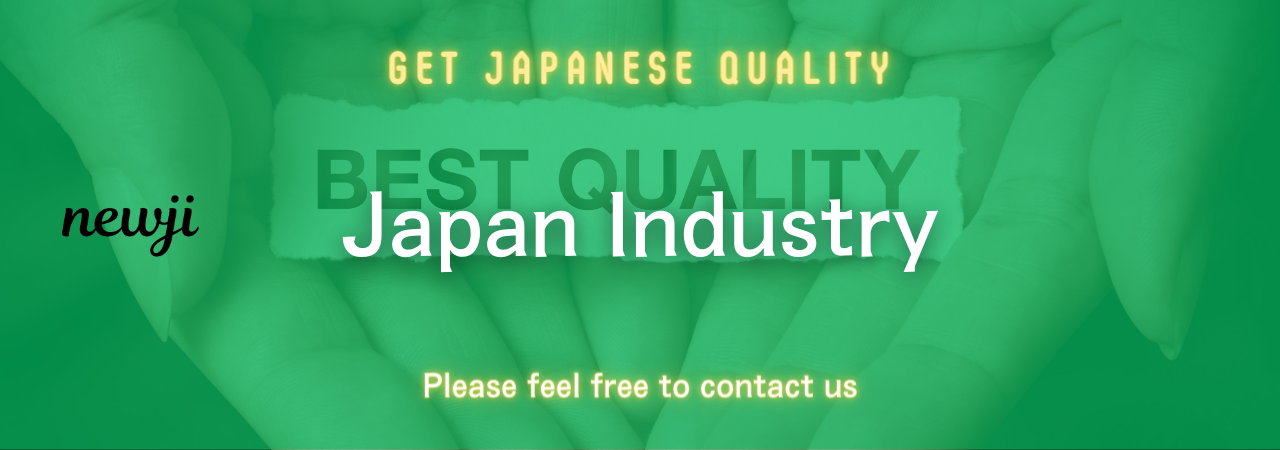
Electric water pumps are essential devices in various applications, such as cooling systems in automobiles, circulating hot water in heating systems, and more.
Their reliability and efficiency largely depend on their manufacturing process and pressure resistance.
In this article, we’ll explore how electric water pumps are manufactured and methods of enhancing their pressure resistance.
目次
Understanding Electric Water Pumps
Electric water pumps use electrical energy to move water through a system.
They are made up of several critical components, including a motor, impeller, housing, seals, and electrical connections.
Each part plays a crucial role in the pump’s operation and overall performance.
Materials Used in Electric Water Pumps
The choice of materials significantly impacts the durability and efficiency of electric water pumps.
Common materials include stainless steel, aluminum, brass, and various plastics.
Each material offers specific benefits:
Stainless Steel
Stainless steel is highly resistant to corrosion and wear, making it an ideal material for pump components exposed to water and harsh environments.
Aluminum
Aluminum is lightweight and offers good thermal conductivity, which is beneficial for pumps that operate under high temperatures.
Brass
Brass is known for its excellent corrosion resistance and mechanical properties, making it a popular choice for fittings and other small components.
Plastics
Advanced plastics, such as polyphenylene sulfide (PPS) and polyether ether ketone (PEEK), provide good chemical resistance and mechanical strength while being lighter than metals.
Manufacturing Process of Electric Water Pumps
The manufacturing process of electric water pumps involves several stages, each ensuring that the final product meets high standards of quality and performance.
Design and Prototyping
The process begins with designing the pump using computer-aided design (CAD) software.
Engineers create detailed models to optimize the pump’s performance and efficiency.
Prototypes are then produced using 3D printing or other rapid prototyping methods to test the design in real-world conditions.
Component Manufacturing
Once the design is finalized, the manufacturing of individual components begins.
Each component is produced using specific techniques:
– **Casting**: For metal parts such as the housing and impeller, casting processes like sand casting or die casting are often used.
– **Injection Molding**: Plastic components are typically produced using injection molding, which allows for high precision and repeatability.
– **Machining**: Precision machining processes, such as CNC milling and turning, are used to create small, intricate parts.
– **Stamping and Forming**: Sheet metal parts are fabricated using stamping and forming techniques.
Assembly
After manufacturing, the individual components are assembled to form the complete pump.
The process usually involves the following steps:
1. **Housing Assembly**: The pump housing is assembled first, ensuring proper alignment of all parts.
2. **Motor Installation**: The electric motor is installed in the housing, with attention to proper alignment and secure mounting.
3. **Impeller Attachment**: The impeller is attached to the motor shaft, ensuring tight integration for efficient water movement.
4. **Seal Installation**: Seals are placed to prevent leaks and protect the motor and internal components from water damage.
5. **Electrical Connections**: Electrical components are connected, including wiring and control circuits.
Quality Control
Quality control is a critical part of the manufacturing process.
Each pump undergoes rigorous testing to ensure it meets performance and safety standards.
Key tests include:
– **Leak Testing**: Ensures that the seals are functioning correctly and there are no leaks in the housing.
– **Performance Testing**: Measures the pump’s flow rate, pressure, and efficiency to ensure it meets the specified requirements.
– **Electrical Testing**: Verifies that the electrical components and connections are working correctly.
Improving Pressure Resistance
Pressure resistance is a crucial factor in the performance and longevity of electric water pumps.
Improving it involves several strategies:
Material Selection
Choosing high-strength, corrosion-resistant materials can significantly improve pressure resistance.
For instance, stainless steel and advanced plastics like PPS and PEEK provide superior performance under high-pressure conditions.
Enhanced Seal Design
Improving the design of seals can effectively prevent leaks and withstand higher pressures.
This includes using high-quality sealing materials and innovative seal designs that distribute pressure evenly.
Optimized Component Design
Component geometry can also impact pressure resistance.
Optimizing the design of components such as the impeller and housing can reduce stress concentrations and improve durability.
Advanced Manufacturing Techniques
Using advanced manufacturing techniques, like additive manufacturing (3D printing), allows for the creation of complex, high-strength geometries that traditional methods cannot achieve.
This can lead to significant improvements in pressure resistance.
Regular Maintenance
Regular maintenance practices, such as checking and replacing worn seals or lubricating moving parts, can help maintain pressure resistance over the pump’s lifetime.
Innovations in Electric Water Pumps
Recent advancements in technology have led to the development of innovative features in electric water pumps, enhancing their performance and reliability.
Smart Pumps
Smart pumps equipped with sensors and IoT connectivity can provide real-time performance data, enabling predictive maintenance and reducing downtime.
This technology helps ensure the pump operates efficiently and alerts users to potential issues before they become serious.
Energy-Efficient Designs
Manufacturers are continuously working to create more energy-efficient pumps, incorporating energy-saving motors and optimizing component designs.
These efforts not only reduce operating costs but also minimize the environmental impact.
Customizable Solutions
Advances in manufacturing have also made it possible to produce highly customizable electric water pumps tailored to specific applications.
This ensures optimal performance and pressure resistance for unique operational requirements.
In conclusion, the manufacturing process of electric water pumps is a complex, multi-stage procedure that involves careful material selection, precise component manufacturing, and rigorous quality control.
By focusing on improving pressure resistance through innovative design and advanced materials, manufacturers can produce reliable, high-performance pumps that meet the demands of various applications.
資料ダウンロード
QCD調達購買管理クラウド「newji」は、調達購買部門で必要なQCD管理全てを備えた、現場特化型兼クラウド型の今世紀最高の購買管理システムとなります。
ユーザー登録
調達購買業務の効率化だけでなく、システムを導入することで、コスト削減や製品・資材のステータス可視化のほか、属人化していた購買情報の共有化による内部不正防止や統制にも役立ちます。
NEWJI DX
製造業に特化したデジタルトランスフォーメーション(DX)の実現を目指す請負開発型のコンサルティングサービスです。AI、iPaaS、および先端の技術を駆使して、製造プロセスの効率化、業務効率化、チームワーク強化、コスト削減、品質向上を実現します。このサービスは、製造業の課題を深く理解し、それに対する最適なデジタルソリューションを提供することで、企業が持続的な成長とイノベーションを達成できるようサポートします。
オンライン講座
製造業、主に購買・調達部門にお勤めの方々に向けた情報を配信しております。
新任の方やベテランの方、管理職を対象とした幅広いコンテンツをご用意しております。
お問い合わせ
コストダウンが利益に直結する術だと理解していても、なかなか前に進めることができない状況。そんな時は、newjiのコストダウン自動化機能で大きく利益貢献しよう!
(Β版非公開)