- お役立ち記事
- Manufacturing Process of Electric Wine Openers and Torque Control Technology
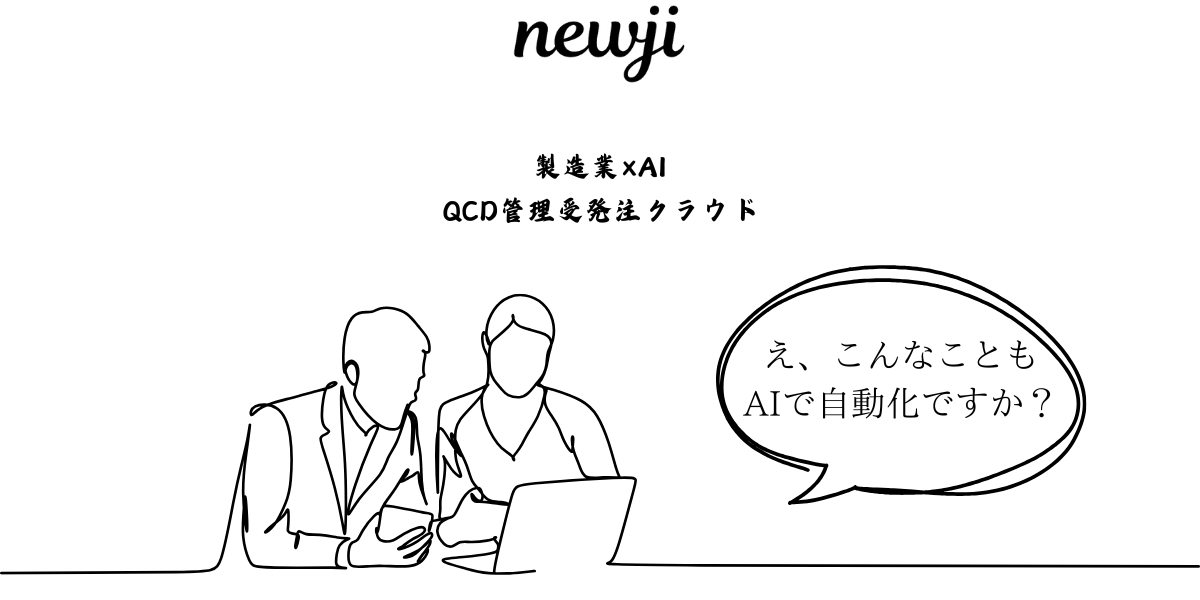
Manufacturing Process of Electric Wine Openers and Torque Control Technology
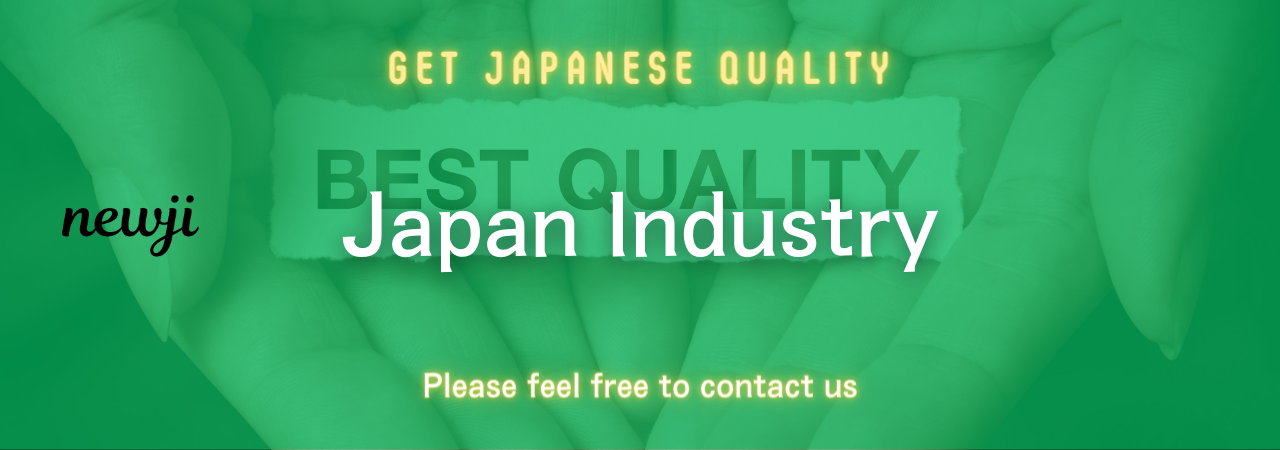
Electric wine openers have become a staple in many households and professional settings, offering an effortless way to uncork bottles of wine.
Their popularity stems from a blend of elegant design, convenience, and the advanced engineering behind their creation.
Let’s dive into the intricate manufacturing process of electric wine openers and explore the cutting-edge torque control technology that ensures their smooth operation.
目次
Design and Conceptualization
Before any product reaches the production line, it goes through a meticulous design phase.
Designers and engineers collaborate to create an ergonomic and visually appealing wine opener.
Prototypes are made to test the grip, balance, and overall user experience.
3D Modeling
Using advanced 3D modeling software, designers create digital versions of the wine opener.
This allows them to visualize the product from all angles and make necessary adjustments before moving to the manufacturing phase.
Material Selection
High-quality materials are chosen to ensure durability and efficiency.
Common materials include stainless steel for the corkscrew, durable plastics for the casing, and sometimes rubber grips for enhanced handling.
Component Manufacturing
Once the design is finalized, the manufacturing of individual components begins.
Each part of the electric wine opener is produced with precision to ensure optimal performance.
Motor Production
The motor is one of the most critical components of an electric wine opener.
High-efficiency motors are manufactured to provide the necessary power for cork extraction while maintaining a compact size.
Corkscrew Fabrication
The corkscrew, usually made of stainless steel, is fabricated with care to ensure it can cleanly penetrate any cork.
Manufacturers pay special attention to the sharpness and durability of the corkscrew.
Casing and Grip Molding
The outer case and grip are typically made from robust plastics or metal.
Injection molding, a process where molten material is injected into a mold cavity, is commonly used for producing these parts.
Assembly Process
Once all components are manufactured, they are brought together in the assembly phase.
Motor and Gear Integration
The motor is integrated with gears to translate its rotational movement into the necessary torque to remove a cork.
This gearing system is crucial for the smooth operation of the wine opener.
Corkscrew Attachment
The corkscrew is securely attached to the motor assembly.
Precision is key here to ensure that the corkscrew aligns perfectly for each use.
Casing Enclosure
The motor assembly and corkscrew are enclosed within the external casing.
This not only protects the internal components but also enhances the overall aesthetic of the product.
Torque Control Technology
Torque control is essential for the efficient functioning of electric wine openers.
It ensures that the right amount of force is applied to remove the cork without damaging it or the bottle.
Importance of Torque Control
Applying too much or too little force can result in broken corks or inefficient operation.
Torque control technology regulates the motor’s power, ensuring consistency.
Sensor Integration
Modern electric wine openers include sensors that measure the resistance encountered by the corkscrew.
These sensors adjust the motor’s torque in real-time to provide a seamless cork removal experience.
Electronic Control Units (ECU)
An ECU is often integrated within the wine opener to process data from the sensors and control the motor’s actions.
This ensures that the device operates within its optimal range, enhancing its longevity and reliability.
Quality Control and Testing
Before reaching consumers, each electric wine opener undergoes rigorous quality control tests to ensure performance and safety.
Performance Testing
The device is subjected to thousands of cork removal cycles to test its durability.
Performance metrics such as torque consistency, motor reliability, and battery life are measured.
Safety Checks
Safety is paramount.
Devices are tested for electrical safety standards, ensuring they are safe for consumer use.
This includes checking for any potential electrical hazards and ensuring the device’s exterior remains cool during operation.
Environmental Considerations
Manufacturers are increasingly mindful of the environmental impact of their products.
Sustainable Materials
Some manufacturers are switching to more sustainable materials, such as biodegradable plastics or recycled components.
This helps reduce the carbon footprint of the manufacturing process.
Energy-Efficient Motors
Energy-efficient motors not only ensure better battery life but also reduce the overall environmental impact of the product.
These motors consume less power, making the device more eco-friendly.
Conclusion
The manufacturing process of electric wine openers is a blend of advanced engineering, meticulous design, and quality control.
From the initial design phase to the incorporation of torque control technology, each step ensures that consumers receive a high-quality, reliable product.
With ongoing advancements in technology and sustainability, future electric wine openers will continue to evolve, offering even more convenience and efficiency.
資料ダウンロード
QCD調達購買管理クラウド「newji」は、調達購買部門で必要なQCD管理全てを備えた、現場特化型兼クラウド型の今世紀最高の購買管理システムとなります。
ユーザー登録
調達購買業務の効率化だけでなく、システムを導入することで、コスト削減や製品・資材のステータス可視化のほか、属人化していた購買情報の共有化による内部不正防止や統制にも役立ちます。
NEWJI DX
製造業に特化したデジタルトランスフォーメーション(DX)の実現を目指す請負開発型のコンサルティングサービスです。AI、iPaaS、および先端の技術を駆使して、製造プロセスの効率化、業務効率化、チームワーク強化、コスト削減、品質向上を実現します。このサービスは、製造業の課題を深く理解し、それに対する最適なデジタルソリューションを提供することで、企業が持続的な成長とイノベーションを達成できるようサポートします。
オンライン講座
製造業、主に購買・調達部門にお勤めの方々に向けた情報を配信しております。
新任の方やベテランの方、管理職を対象とした幅広いコンテンツをご用意しております。
お問い合わせ
コストダウンが利益に直結する術だと理解していても、なかなか前に進めることができない状況。そんな時は、newjiのコストダウン自動化機能で大きく利益貢献しよう!
(Β版非公開)