- お役立ち記事
- Manufacturing Process of Engine Mounts and Vibration Absorption Improvement
Manufacturing Process of Engine Mounts and Vibration Absorption Improvement
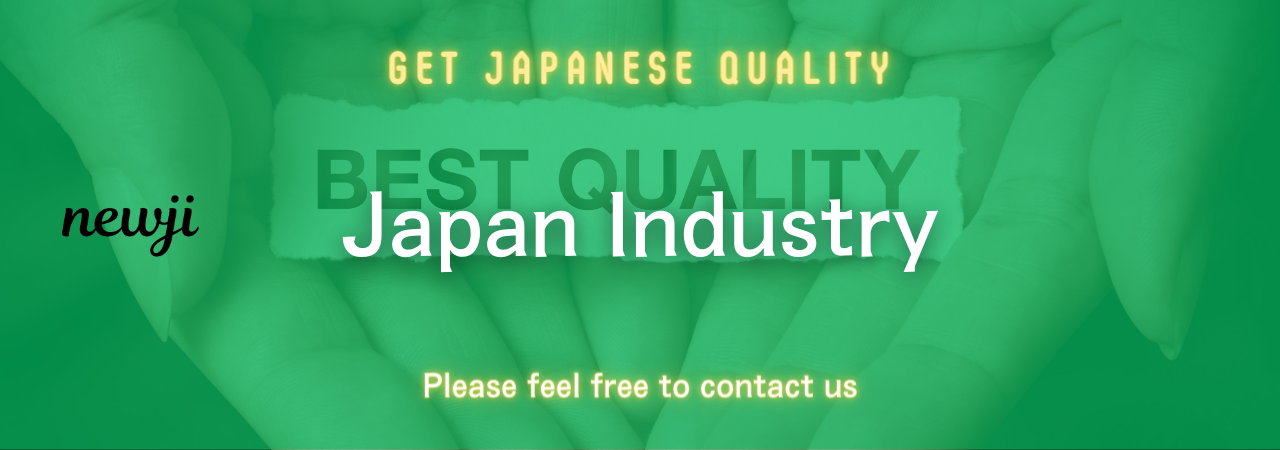
Engine mounts play a critical role in reducing vibrations and ensuring smooth operation in vehicles.
They are essential components that connect the engine to the vehicle’s frame and help absorb engine vibrations and shocks.
Improving the manufacturing process of engine mounts and enhancing their vibration absorption capacity is crucial for producing high-quality automotive parts.
In this article, we will explore how engine mounts are made and discuss methods to improve their vibration absorption.
目次
What Are Engine Mounts?
Engine mounts are components that secure the engine to the chassis of the vehicle.
They are designed to absorb and dampen vibrations generated by the engine, preventing these vibrations from being transferred to the frame and, ultimately, to the passengers.
Engine mounts are generally constructed from materials such as rubber and metal, which provide the necessary flexibility and durability.
Manufacturing Process of Engine Mounts
The manufacturing process of engine mounts involves several steps, each contributing to the component’s overall quality and performance.
Here are the key stages in the production of engine mounts:
1. Material Selection
The first step in manufacturing engine mounts is selecting the appropriate materials.
The most common materials used are rubber and metal.
Rubber provides the elasticity needed to absorb vibrations, while metal offers structural support and durability.
Each material is chosen based on the specific requirements of the engine mount, such as load-bearing capacity, temperature resistance, and vibration absorption characteristics.
2. Designing and Prototyping
Once the materials are selected, the next step is designing the engine mount.
Engineers use computer-aided design (CAD) software to create detailed models of the mount.
These designs take into account factors such as the engine’s weight, the vehicle’s frame, and the desired vibration absorption properties.
After the design is finalized, prototypes are created for testing.
Prototyping allows engineers to evaluate the performance of the engine mount and make any necessary adjustments before mass production.
3. Molding and Forming
In this stage, the selected rubber material is molded into the desired shape.
This process typically involves using high-pressure injection molding machines that can accurately shape the rubber to match the design specifications.
Once the rubber is molded, it is combined with the metal components to form the complete engine mount.
The metal parts are usually stamped or machined to ensure precision and durability.
4. Assembly
During assembly, the molded rubber and metal components are brought together.
This stage requires precision and attention to detail to ensure that the parts fit together perfectly.
Automated assembly lines are often used to improve efficiency and maintain consistency in the production process.
The assembled engine mounts undergo quality checks to verify that they meet the required standards.
5. Vulcanization
Vulcanization is a chemical process that enhances the rubber’s properties, making it more durable and heat-resistant.
During vulcanization, the assembled engine mounts are subjected to high temperatures and pressure.
This process strengthens the rubber and improves its ability to absorb vibrations.
Vulcanization is a crucial step in ensuring that the engine mounts can withstand the harsh conditions of an automotive environment.
Improving Vibration Absorption
The effectiveness of engine mounts in absorbing vibrations can significantly impact the overall comfort and performance of a vehicle.
Here are some methods to enhance the vibration absorption capacity of engine mounts:
1. Advanced Material Technologies
One way to improve vibration absorption is by using advanced materials with superior damping properties.
Innovations in material science have led to the development of new rubber compounds and composite materials that offer better performance than traditional options.
These advanced materials can provide greater elasticity and durability, resulting in improved vibration absorption.
2. Finite Element Analysis (FEA)
Finite Element Analysis (FEA) is a powerful tool used by engineers to simulate and analyze the behavior of engine mounts under various conditions.
By using FEA, engineers can identify potential weaknesses in the design and optimize the shape and structure of the engine mount for better vibration absorption.
This analysis helps in creating more efficient and reliable engine mounts that perform well under real-world conditions.
3. Dynamic Testing
To ensure that engine mounts provide optimal vibration absorption, dynamic testing is conducted.
This involves subjecting the engine mounts to simulated engine vibrations and measuring their performance.
By analyzing the results, engineers can make adjustments to the design and materials to enhance the mount’s ability to dampen vibrations.
Dynamic testing is crucial for validating the effectiveness of engine mounts and ensuring they meet industry standards.
4. Customization and Tuning
Different vehicles and engines have unique vibration characteristics, which means that a one-size-fits-all approach may not be effective.
Customization and tuning of engine mounts allow for tailoring the vibration absorption properties to specific applications.
Engineers can adjust the rubber hardness, design parameters, and other factors to optimize the performance of the engine mounts for different vehicles.
This customization ensures that the mounts provide the best possible vibration absorption for each specific application.
Conclusion
The manufacturing process of engine mounts involves careful material selection, precise design, and advanced production techniques.
To improve vibration absorption, engineers can use advanced materials, conduct finite element analysis, perform dynamic testing, and customize the mounts to specific applications.
By continuously refining these methods, manufacturers can produce high-quality engine mounts that enhance vehicle performance and passenger comfort.
Keeping up with the latest innovations and technologies in the field is essential for maintaining a competitive edge in the automotive industry.
資料ダウンロード
QCD調達購買管理クラウド「newji」は、調達購買部門で必要なQCD管理全てを備えた、現場特化型兼クラウド型の今世紀最高の購買管理システムとなります。
ユーザー登録
調達購買業務の効率化だけでなく、システムを導入することで、コスト削減や製品・資材のステータス可視化のほか、属人化していた購買情報の共有化による内部不正防止や統制にも役立ちます。
NEWJI DX
製造業に特化したデジタルトランスフォーメーション(DX)の実現を目指す請負開発型のコンサルティングサービスです。AI、iPaaS、および先端の技術を駆使して、製造プロセスの効率化、業務効率化、チームワーク強化、コスト削減、品質向上を実現します。このサービスは、製造業の課題を深く理解し、それに対する最適なデジタルソリューションを提供することで、企業が持続的な成長とイノベーションを達成できるようサポートします。
オンライン講座
製造業、主に購買・調達部門にお勤めの方々に向けた情報を配信しております。
新任の方やベテランの方、管理職を対象とした幅広いコンテンツをご用意しております。
お問い合わせ
コストダウンが利益に直結する術だと理解していても、なかなか前に進めることができない状況。そんな時は、newjiのコストダウン自動化機能で大きく利益貢献しよう!
(Β版非公開)