- お役立ち記事
- Manufacturing Process of Engine Pistons and Durability Reinforcement
月間76,176名の
製造業ご担当者様が閲覧しています*
*2025年3月31日現在のGoogle Analyticsのデータより
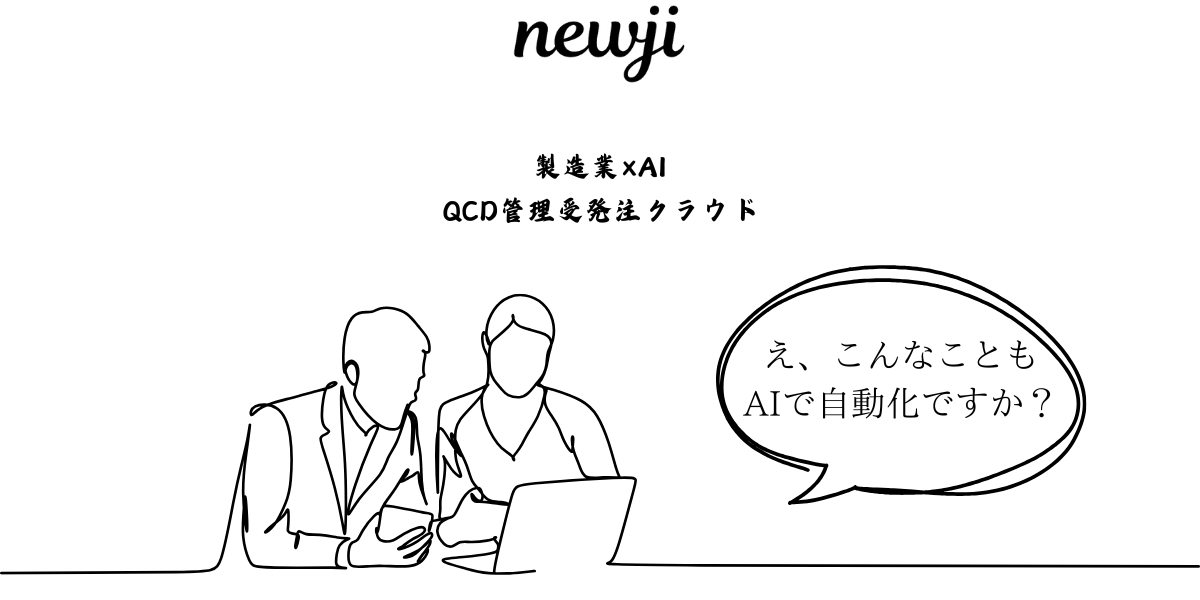
Manufacturing Process of Engine Pistons and Durability Reinforcement
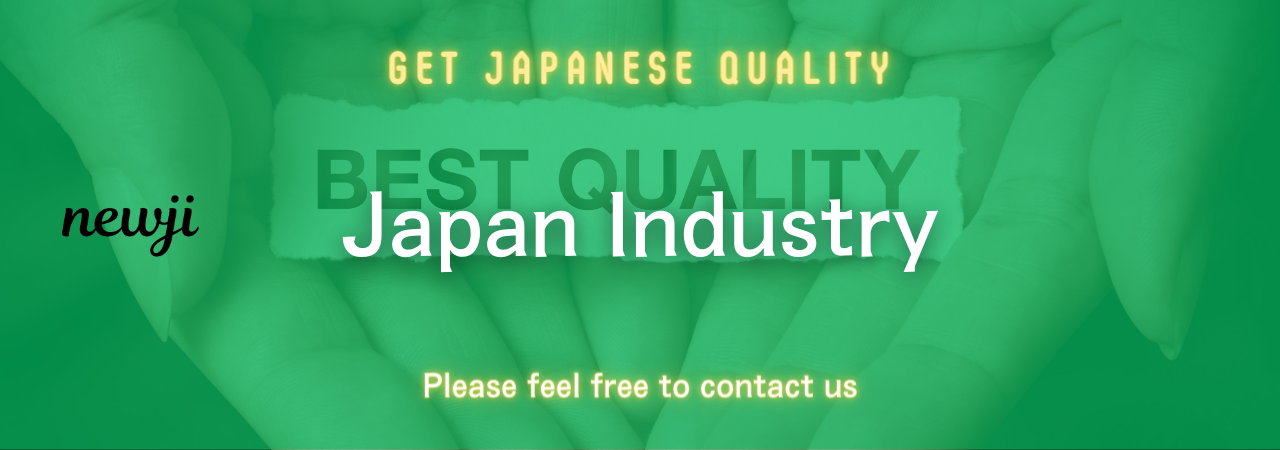
The manufacturing of engine pistons is an intricate process that involves several steps to ensure they can endure the demanding environment inside an engine.
Pistons are fundamental components in internal combustion engines, responsible for converting fuel into the mechanical energy that powers vehicles.
Let’s explore the manufacturing process in detail, as well as how the pistons are reinforced for durability.
目次
Raw Material Selection
The journey begins with choosing the right material.
Pistons are typically made from aluminum alloys due to their light weight and excellent heat conductivity.
High-strength steel is another common choice, especially for high-performance engines.
The selected material must endure high temperatures and pressures without deforming.
Forging or Casting
Once the material is chosen, the pistons can be manufactured using either the forging or casting method.
Forging
Forging involves heating a piece of metal until it’s malleable.
It is then shaped under high pressure in a die.
This method is popular because it produces pistons with superior strength and durability.
The high pressure aligns the metal grains, resulting in a denser and more resilient structure.
Casting
Casting involves melting the material and pouring it into a mold.
Once the metal cools and solidifies, it can be extracted from the mold.
This method is less expensive than forging but may not produce pistons as strong.
However, advancements in casting techniques have made it possible to create highly durable pistons suitable for many engine types.
Machining
After forging or casting, the rough piston blanks undergo machining to achieve precise dimensions.
CNC (Computer Numerical Control) machines are often used because they offer high accuracy and consistency.
Machining involves several steps:
Rough Machining
This initial step removes excess material to get the piston close to its final shape.
Lathes and milling machines are commonly used during this phase.
Heat Treatment
After rough machining, pistons undergo heat treatment to enhance their mechanical properties.
Processes such as quenching and tempering increase hardness and strength.
Finish Machining
The pistons return to CNC machines for finish machining, where fine details are added.
This step includes creating piston rings, grooves, and oil holes.
The final dimensions and surface finishes are achieved during this stage.
Surface Treatment
Surface treatment is essential to enhance the durability and performance of pistons.
Several treatments can be applied:
Anodizing
Anodizing creates a protective oxide layer on the surface of aluminum pistons, improving wear resistance and reducing friction.
Coating
Special coatings such as ceramic or molybdenum can be applied to enhance thermal resistance and reduce wear.
These coatings also help to lower friction between the piston and cylinder wall.
Inspection and Quality Control
Quality control is a critical aspect of piston manufacturing.
Each piston undergoes rigorous inspections to ensure it meets specifications.
Common inspection methods include:
Dimensional Inspection
Using tools such as micrometers and coordinate measuring machines (CMM), technicians verify that pistons comply with dimensional tolerances.
Non-Destructive Testing (NDT)
Techniques like X-ray and ultrasound are used to detect internal defects without damaging the pistons.
These methods identify issues like porosity or cracks that could compromise piston integrity.
Final Assembly
Once the pistons pass all inspections, they are ready for final assembly.
Piston rings and pins are installed, and the pistons are often connected to the connecting rods before being integrated into the engine.
Proper lubrication is applied to ensure smooth operation during initial startup.
Durability Reinforcement
To further extend the lifespan and performance of pistons, various reinforcement techniques are implemented:
Thermal Barrier Coatings (TBC)
These high-heat-resistant coatings are applied to the piston crown to protect against extreme temperatures.
They help prevent heat-induced fatigue and thermal deformation.
Hard Anodizing
A more advanced form of anodizing, hard anodizing creates a thicker and harder oxide layer.
This significantly improves wear resistance and longevity.
Reinforced Piston Skirts
The skirts can be reinforced with materials like graphite or advanced polymers to reduce friction and improve wear resistance.
This enhancement leads to better performance and longer piston life.
Conclusion
The manufacturing process of engine pistons is a comprehensive journey from raw material selection to final assembly.
Each step, from forging or casting to machining and surface treatment, plays a crucial role in ensuring pistons can withstand the rigors of engine operation.
Through various quality control measures and durability reinforcement techniques, manufacturers produce pistons that are both reliable and long-lasting.
Understanding these processes helps appreciate the engineering marvels that keep our engines running smoothly.
資料ダウンロード
QCD管理受発注クラウド「newji」は、受発注部門で必要なQCD管理全てを備えた、現場特化型兼クラウド型の今世紀最高の受発注管理システムとなります。
ユーザー登録
受発注業務の効率化だけでなく、システムを導入することで、コスト削減や製品・資材のステータス可視化のほか、属人化していた受発注情報の共有化による内部不正防止や統制にも役立ちます。
NEWJI DX
製造業に特化したデジタルトランスフォーメーション(DX)の実現を目指す請負開発型のコンサルティングサービスです。AI、iPaaS、および先端の技術を駆使して、製造プロセスの効率化、業務効率化、チームワーク強化、コスト削減、品質向上を実現します。このサービスは、製造業の課題を深く理解し、それに対する最適なデジタルソリューションを提供することで、企業が持続的な成長とイノベーションを達成できるようサポートします。
製造業ニュース解説
製造業、主に購買・調達部門にお勤めの方々に向けた情報を配信しております。
新任の方やベテランの方、管理職を対象とした幅広いコンテンツをご用意しております。
お問い合わせ
コストダウンが利益に直結する術だと理解していても、なかなか前に進めることができない状況。そんな時は、newjiのコストダウン自動化機能で大きく利益貢献しよう!
(β版非公開)