- お役立ち記事
- Manufacturing Process of Exhaust Manifolds and Exhaust Efficiency Enhancement
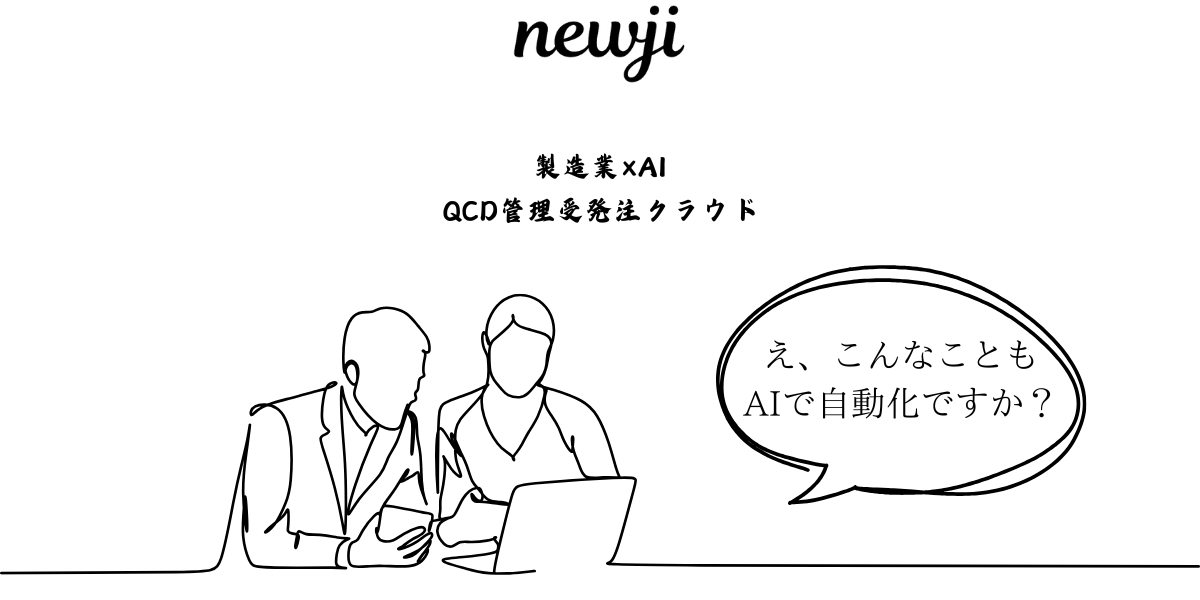
Manufacturing Process of Exhaust Manifolds and Exhaust Efficiency Enhancement
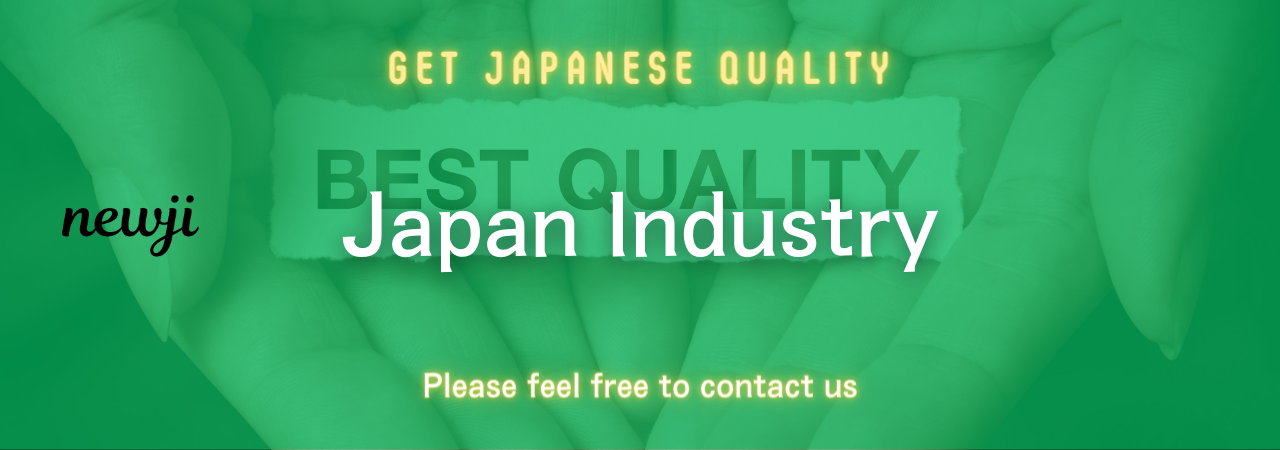
An exhaust manifold is a vital part of a vehicle’s engine system.
It collects exhaust gases from the engine cylinders and directs them to the exhaust pipe.
Understanding the manufacturing process and methods to enhance exhaust efficiency can lead to significant improvements in vehicle performance and emissions reduction.
目次
The Manufacturing Process of Exhaust Manifolds
Material Selection
The first step in creating an exhaust manifold is selecting the appropriate material.
Traditionally, manufacturers use cast iron because of its durability and heat resistance.
However, stainless steel is becoming more popular due to its lighter weight and resistance to corrosion.
Choosing the right material is essential to ensure the manifold can withstand high temperatures and pressures.
Design and Prototyping
Once the material is selected, engineers design the exhaust manifold using computer-aided design (CAD) software.
The design process involves creating a comprehensive blueprint that includes dimensions, angles, and connections for each engine cylinder.
A prototype is then developed to test the design.
Using rapid prototyping techniques, such as 3D printing, engineers create a physical model to evaluate fit and functionality.
Casting Process
After finalizing the design, the manufacturing process moves on to casting.
Casting involves pouring molten metal into a mold to form the shape of the exhaust manifold.
The mold is typically made of sand, ceramic, or metal.
Once the molten metal cools and solidifies, the mold is broken away to reveal the rough shape of the manifold.
Machining and Finishing
The rough cast manifold undergoes machining to achieve precise dimensions and surface finish.
Machining processes include milling, drilling, and grinding.
Engineers use specialized equipment to ensure each port and flange meets exact specifications.
After machining, the manifold undergoes finishing processes such as coating and polishing.
These steps enhance the durability and appearance of the manifold, reducing rust and improving heat resilience.
Quality Control and Testing
Quality control is crucial in the manufacturing process.
Each exhaust manifold is subjected to rigorous testing to ensure it meets industry standards.
Tests include pressure testing, thermal cycling, and material analysis.
Pressure testing checks for leaks and structural integrity, while thermal cycling assesses the manifold’s ability to withstand temperature fluctuations.
Material analysis ensures the composition matches the specified requirements.
Enhancing Exhaust Efficiency
Reducing Back Pressure
One of the primary goals in exhaust efficiency is reducing back pressure.
Back pressure occurs when exhaust gases encounter resistance while leaving the engine.
This resistance can hamper engine performance and fuel efficiency.
Using mandrel-bent pipes can minimize back pressure.
Mandrel bending creates smooth curves, allowing exhaust gases to flow freely.
Additionally, increasing the diameter of the exhaust pipes can help reduce resistance.
Optimizing Exhaust Manifold Design
A well-designed exhaust manifold can significantly improve exhaust efficiency.
One common approach is using a header design, where each exhaust port has its own pipe, merging into a single collector.
This design helps balance exhaust gas flow, reducing turbulence and improving scavenging.
Furthermore, equal-length headers ensure that exhaust pulses from each cylinder reach the collector at the same time, enhancing overall efficiency.
Using High-Flow Catalytic Converters
Catalytic converters play a crucial role in reducing harmful emissions.
High-flow catalytic converters minimize exhaust restriction while effectively converting toxic gases.
These converters feature a larger internal structure and a higher cell density, allowing for improved exhaust flow.
Investing in a high-quality catalytic converter can improve both efficiency and environmental impact.
Implementing Exhaust Wraps and Heat Shields
Managing heat in the exhaust system can enhance performance.
Exhaust wraps and heat shields help maintain high exhaust gas temperatures, which improves velocity.
Exhaust wraps are heat-resistant fabrics that can be wrapped around the manifold and pipes.
They reduce heat loss and keep the gases moving quickly.
Heat shields, on the other hand, reflect radiant heat away from sensitive components, protecting them from damage and maintaining efficiency.
Routine Maintenance
Regular maintenance is vital for sustaining exhaust efficiency.
Inspect the exhaust system for leaks, cracks, or corrosion periodically.
Addressing issues promptly can prevent performance degradation.
Additionally, ensure engine operation parameters are within manufacturer specifications to optimize exhaust performance.
Future Trends and Innovations
Advanced Materials
The automotive industry is continually seeking advanced materials to enhance exhaust manifold performance.
Materials such as titanium and Inconel offer superior strength and heat resistance but come at a higher cost.
As manufacturing techniques improve, these materials may become more accessible for production.
Integration with Hybrid and Electric Vehicles
As the industry shifts towards hybrid and electric vehicles, the role of exhaust systems is evolving.
Hybrid vehicles benefit from optimized exhaust efficiency to improve fuel consumption and emissions.
For electric vehicles, innovations focus on noise reduction and heat management for battery systems.
Smart Exhaust Systems
The integration of sensors and IoT technology is paving the way for smart exhaust systems.
These systems can monitor exhaust gas composition, temperature, and flow in real-time.
Data collected can optimize performance and alert drivers to potential issues before they become serious, enhancing both efficiency and reliability.
Understanding the manufacturing process of exhaust manifolds and methods to enhance exhaust efficiency is crucial for improving vehicle performance and reducing environmental impact.
By selecting suitable materials, optimizing design, and implementing advanced technologies, manufacturers can create exhaust systems that meet modern demands.
Regular maintenance and adopting future innovations ensure continued efficiency and sustainability.
資料ダウンロード
QCD調達購買管理クラウド「newji」は、調達購買部門で必要なQCD管理全てを備えた、現場特化型兼クラウド型の今世紀最高の購買管理システムとなります。
ユーザー登録
調達購買業務の効率化だけでなく、システムを導入することで、コスト削減や製品・資材のステータス可視化のほか、属人化していた購買情報の共有化による内部不正防止や統制にも役立ちます。
NEWJI DX
製造業に特化したデジタルトランスフォーメーション(DX)の実現を目指す請負開発型のコンサルティングサービスです。AI、iPaaS、および先端の技術を駆使して、製造プロセスの効率化、業務効率化、チームワーク強化、コスト削減、品質向上を実現します。このサービスは、製造業の課題を深く理解し、それに対する最適なデジタルソリューションを提供することで、企業が持続的な成長とイノベーションを達成できるようサポートします。
オンライン講座
製造業、主に購買・調達部門にお勤めの方々に向けた情報を配信しております。
新任の方やベテランの方、管理職を対象とした幅広いコンテンツをご用意しております。
お問い合わせ
コストダウンが利益に直結する術だと理解していても、なかなか前に進めることができない状況。そんな時は、newjiのコストダウン自動化機能で大きく利益貢献しよう!
(Β版非公開)