- お役立ち記事
- Manufacturing Process of Fire Extinguishers and Pressure Testing Methods
月間76,176名の
製造業ご担当者様が閲覧しています*
*2025年3月31日現在のGoogle Analyticsのデータより
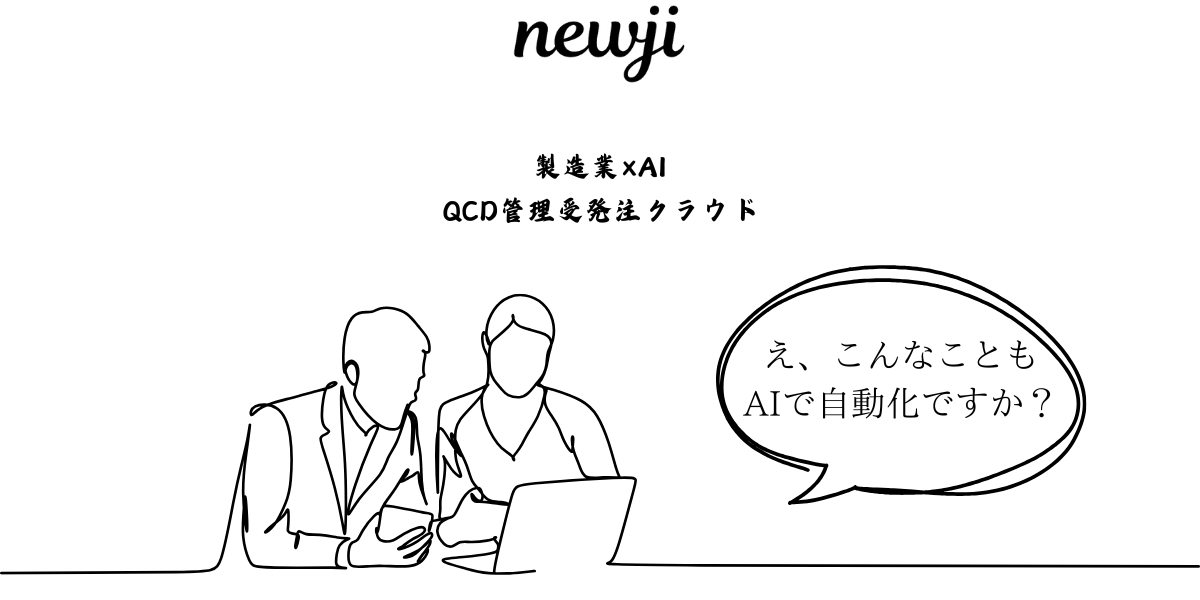
Manufacturing Process of Fire Extinguishers and Pressure Testing Methods
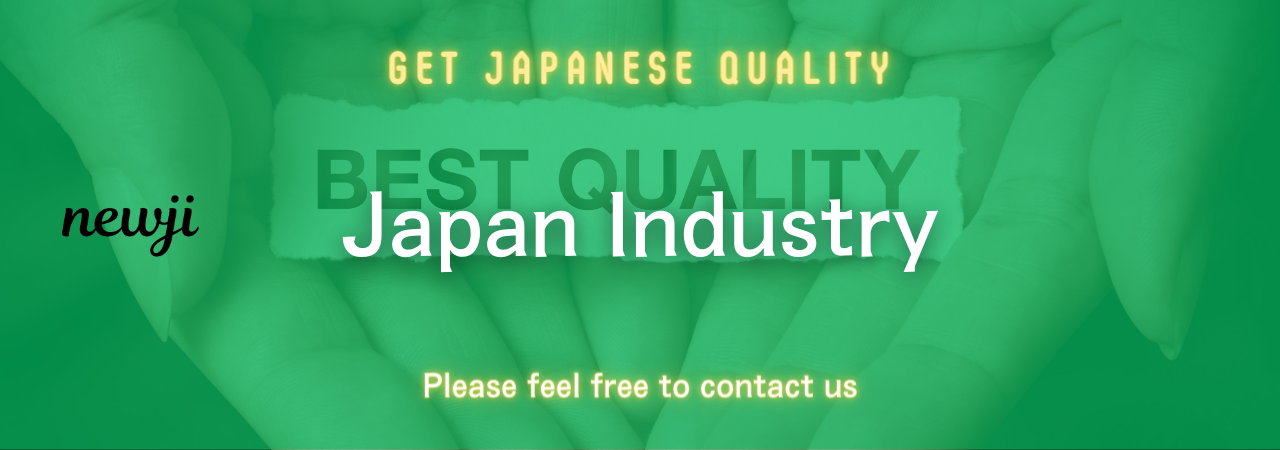
目次
Introduction to Fire Extinguishers
Fire extinguishers are indispensable safety devices that help control small fires before they escalate.
Understanding their manufacturing process and pressure testing methods is crucial for ensuring their effectiveness and reliability.
In this article, we’ll delve into how fire extinguishers are made and the testing protocols they undergo to guarantee safety and compliance with regulatory standards.
Materials Used in Fire Extinguisher Manufacturing
Metal Components
The primary material used in the construction of fire extinguishers is metal, specifically steel or aluminum.
These metals are chosen for their durability and ability to withstand high pressure.
Steel is typically used for heavier-duty extinguishers, such as those designed for industrial environments, while aluminum is common in portable, lightweight models.
Valve Assembly
The valve assembly is a critical component, usually made from brass, stainless steel, or other corrosion-resistant materials.
The design of the valve is crucial for controlling the release of the extinguishing agent accurately and reliably.
Extinguishing Agents
Different types of fire extinguishers use various extinguishing agents like water, foam, dry chemical powders, carbon dioxide (CO2), and halon alternatives.
The choice of agent depends on the type of fire the extinguisher is designed to combat.
For instance, water-based extinguishers are suited for Class A fires (ordinary combustibles), while CO2 extinguishers are best for Class B (flammable liquids) and Class C (electrical) fires.
The Manufacturing Process
Metal Forming
The manufacturing process begins with metal forming, where sheets of steel or aluminum are cut and shaped into cylinders.
These cylinders are then welded together to form a sealed container.
The welding process must be precise to ensure that the container can withstand the pressures it may encounter during use.
Interior Coating
After the cylinder is formed, an interior coating is applied to prevent corrosion.
This is especially important for extinguishers containing water or other liquids that could corrode the metal over time.
Epoxy or polyester coatings are commonly used for this purpose.
Adding the Extinguishing Agent
Once the interior coating is applied and cured, the extinguisher is filled with the appropriate extinguishing agent.
This step is executed under strict quality control measures to ensure the correct quantity and composition of the agent.
Valve and Hose Installation
Next, the valve assembly is installed.
The valve, along with its seat and gaskets, must be perfectly aligned to ensure a tight seal.
Hoses and nozzles are then attached, and the extinguisher is fitted with a pressure gauge to monitor internal pressure.
Pressure Testing Methods
Hydrostatic Testing
Hydrostatic testing is one of the most critical tests for fire extinguishers.
This test involves filling the extinguisher with water and pressurizing it to levels much higher than its normal operating pressure.
The purpose is to check for any weaknesses or leaks in the container.
Typically, fire extinguishers are pressurized to 1.5 times their operating pressure during this test.
Pneumatic Testing
In rare cases, pneumatic testing may be used, where the extinguisher is filled with air rather than water.
This method is less common due to the potential hazards associated with pressurizing a container with air.
Operational Testing
Operational testing involves discharging the extinguisher to ensure it functions correctly and that the extinguishing agent is released effectively.
This test checks that the valve operates properly, the hose and nozzle are free from obstructions, and the pressure gauge provides accurate readings.
Leak Testing
Leak testing is performed to ensure that there are no leaks in the cylinder, valve assembly, or any other part of the fire extinguisher.
This often involves submerging the pressurized extinguisher in water and looking for air bubbles, which indicate a leak.
Alternatively, a gas detection device may be used to identify leaks.
Quality Control and Certification
Inspection and Documentation
After passing all pressure and operational tests, the fire extinguisher undergoes a final inspection.
Inspectors check for defects, proper labeling, and compliance with industry standards.
Documentation is maintained for each extinguisher, detailing its manufacturing and testing history.
Certification
Fire extinguishers that meet all quality and safety standards receive certification from regulatory bodies such as Underwriters Laboratories (UL) or the European Union (EU).
This certification guarantees that the extinguisher can be trusted in emergency situations.
Conclusion
The manufacturing process of fire extinguishers is meticulous and rigorous, ensuring that each unit meets high safety and reliability standards.
From metal forming to valve assembly and pressure testing, every step is crucial for creating a functional and dependable fire safety device.
Understanding the production and testing methods not only underscores the importance of quality control but also highlights the complex engineering that goes into making these life-saving tools.
By adhering to stringent testing protocols, manufacturers can provide reliable fire safety solutions that protect lives and property effectively.
資料ダウンロード
QCD管理受発注クラウド「newji」は、受発注部門で必要なQCD管理全てを備えた、現場特化型兼クラウド型の今世紀最高の受発注管理システムとなります。
ユーザー登録
受発注業務の効率化だけでなく、システムを導入することで、コスト削減や製品・資材のステータス可視化のほか、属人化していた受発注情報の共有化による内部不正防止や統制にも役立ちます。
NEWJI DX
製造業に特化したデジタルトランスフォーメーション(DX)の実現を目指す請負開発型のコンサルティングサービスです。AI、iPaaS、および先端の技術を駆使して、製造プロセスの効率化、業務効率化、チームワーク強化、コスト削減、品質向上を実現します。このサービスは、製造業の課題を深く理解し、それに対する最適なデジタルソリューションを提供することで、企業が持続的な成長とイノベーションを達成できるようサポートします。
製造業ニュース解説
製造業、主に購買・調達部門にお勤めの方々に向けた情報を配信しております。
新任の方やベテランの方、管理職を対象とした幅広いコンテンツをご用意しております。
お問い合わせ
コストダウンが利益に直結する術だと理解していても、なかなか前に進めることができない状況。そんな時は、newjiのコストダウン自動化機能で大きく利益貢献しよう!
(β版非公開)