- お役立ち記事
- Manufacturing Process of Flow Switches and Flow Rate Detection Enhancement
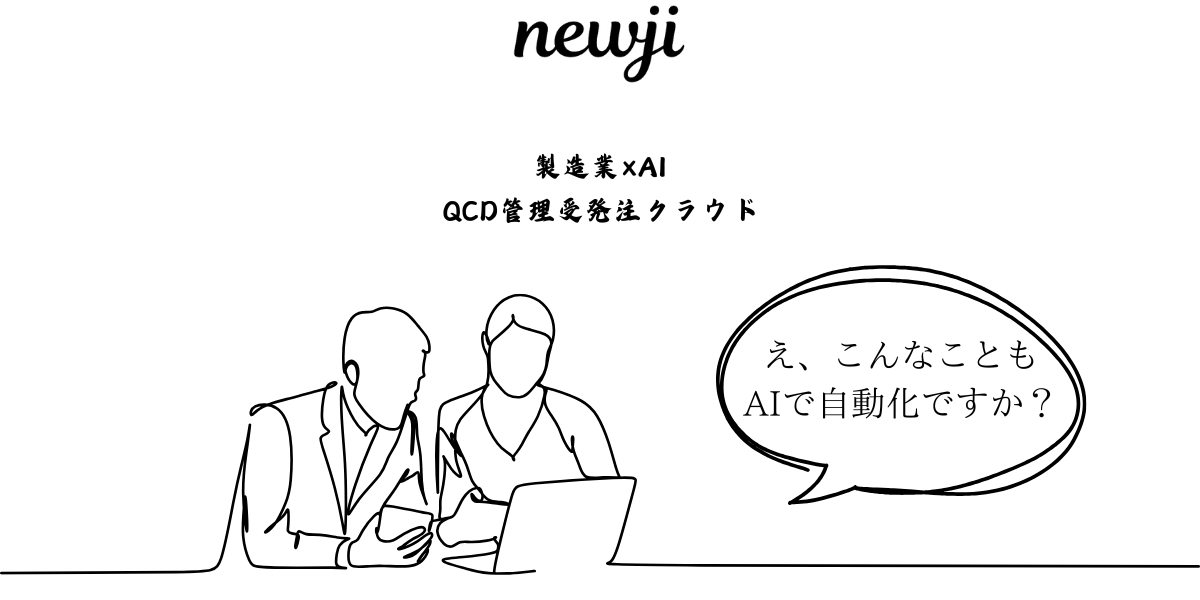
Manufacturing Process of Flow Switches and Flow Rate Detection Enhancement
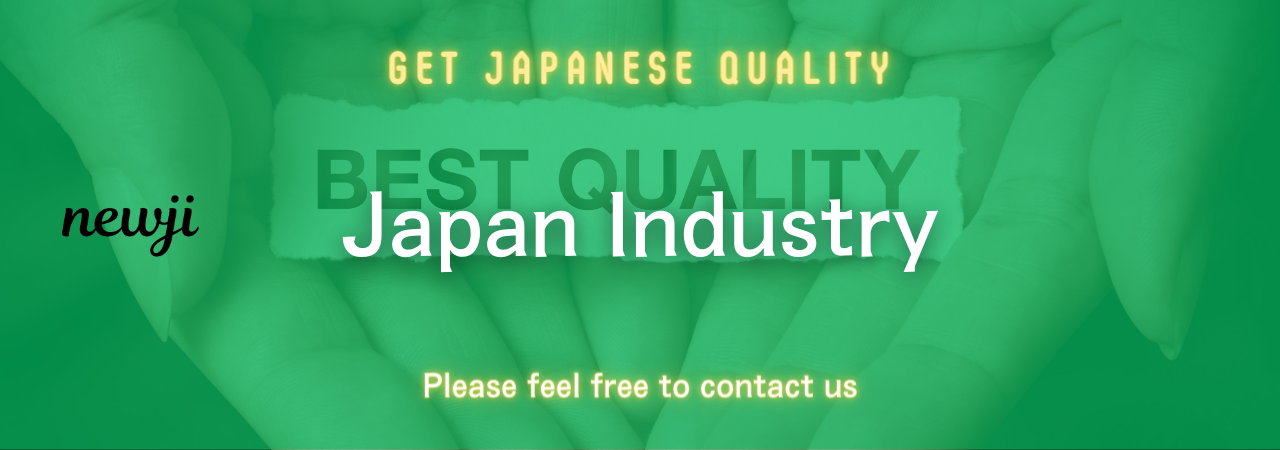
Flow switches are essential devices in various industries, ensuring smooth and safe operations by monitoring and controlling the flow of liquids and gases.
The manufacturing process of flow switches and the enhancement of flow rate detection involve several intricate steps and technologies.
This article will give you an in-depth view of how these vital components are produced and improved.
目次
Understanding Flow Switches
To grasp the manufacturing process, it’s crucial to understand what a flow switch is.
A flow switch is a mechanical device that monitors the flow of air, steam, or liquid.
It sends a trip signal to a device, such as a pump, to prevent damage and ensure proper operation.
When the flow rate changes, the switch responds accordingly, protecting the system’s integrity.
These switches are utilized in HVAC systems, water treatment plants, and industrial machinery.
Initial Design and Engineering
Concept and Specifications
Before manufacturing begins, the design team creates detailed plans for the flow switch.
This includes defining the switch’s specifications, such as the operating flow range, materials, and activation pressure.
Engineers use computer-aided design (CAD) software to create models and simulations, ensuring the device will function correctly in real-world applications.
Material Selection
Selecting appropriate materials is vital for the durability and effectiveness of the flow switch.
Common materials include stainless steel, brass, and special plastics resistant to corrosion and high temperatures.
The choice depends on the application and the environment where the flow switch will be used.
Manufacturing Process
Component Production
Once the design is finalized, the actual manufacturing process begins.
Components of flow switches are produced using various techniques such as machining, molding, and casting.
Key parts include the housing, the paddle or vane, electronic sensors, and the switch mechanism.
Machining processes like CNC milling and turning are often employed to achieve precise dimensions.
For intricate parts, injection molding is used to produce components from high-performance plastics.
Metal parts might be cast and then further machined to meet tight tolerances.
Assembly
After producing individual components, they are assembled into a complete flow switch.
This step involves combining the housing, internal parts, and sensors.
Technicians use specialized tools and fixtures to ensure every part fits perfectly.
Precision is crucial during this phase as even a minor misalignment can affect the switch’s performance.
Moreover, wiring for electronic sensors is carefully connected and secured.
Special care is taken to ensure that connections are robust and protected from environmental factors like moisture and dust.
Calibration and Testing
Calibration is key to ensuring that the flow switch operates within its specified parameters.
This step involves adjusting the switch so that it trips at the correct flow rate.
Advanced calibration equipment simulates different flow conditions and measures the switch’s response.
Technicians use this data to fine-tune the device.
Rigorous testing follows calibration.
Each flow switch undergoes a series of tests to confirm it performs reliably.
This includes functional tests, where the switch is subjected to various flow rates, and environmental tests, where it operates in extreme conditions.
Only models that pass all tests move forward to the final inspection phase.
Flow Rate Detection Enhancement
Advancements in Sensor Technology
Modern flow switches benefit from significant advancements in sensor technology.
New sensors offer higher accuracy and responsiveness.
For example, flow switches now feature ultrasonic and thermal dispersion sensors that provide precise flow measurements without mechanical parts.
These sensors convert flow rate data into electronic signals, which are processed to monitor and control system performance.
Incorporating smart sensors allows for real-time data analytics, offering deeper insights into flow dynamics.
Improved Software Algorithms
Alongside hardware advancements, software algorithms play a pivotal role in enhancing flow rate detection.
Intelligent algorithms can predict flow fluctuations and adjust the system in real-time.
This proactive approach prevents potential issues before they escalate, ensuring continuous and safe operations.
Modern flow switches often come with integrated microcontrollers that process sensor data.
These microcontrollers execute complex algorithms to filter noise, compensate for temperature variations, and deliver accurate flow rate readings.
Wireless and Remote Monitoring
Another significant enhancement is the integration of wireless technology for remote monitoring.
Flow switches equipped with Wi-Fi or Bluetooth can transmit data to centralized monitoring systems.
Operators can track flow rates and receive alerts from anywhere, enhancing convenience and operational efficiency.
This capability is particularly valuable in large industrial settings where access to each individual flow switch can be challenging.
Energy Efficiency
Energy efficiency is a growing concern in modern manufacturing.
Enhanced flow switches are designed to consume less power without compromising performance.
Employing low-power sensors and optimizing software algorithms help reduce energy consumption.
This not only lowers operational costs but also aligns with sustainability goals.
Quality Assurance
Final Inspection
Quality assurance is an integral part of manufacturing flow switches.
Before shipment, each device undergoes a final inspection to verify conformity with specifications.
Inspectors check for any physical defects, review calibration data, and ensure all components are securely assembled.
Compliance Testing
Flow switches must comply with industry standards and regulations.
This involves rigorous compliance testing for certifications such as ISO, ANSI, and others relevant to the target markets.
Compliance testing ensures that flow switches meet safety, reliability, and environmental standards.
Feedback and Continuous Improvement
The process doesn’t end once the product is shipped.
Customer feedback is crucial for continuous improvement.
Manufacturers gather performance data from users to identify potential enhancements.
This feedback loop helps in refining the design, materials, and manufacturing techniques, leading to better future products.
In conclusion, the manufacturing process of flow switches involves a sophisticated blend of design, engineering, precision manufacturing, and rigorous testing.
Enhancements in flow rate detection, driven by advanced sensor technologies, intelligent algorithms, and wireless monitoring, enable these devices to perform more reliably and efficiently than ever before.
Understanding these intricacies helps appreciate the vital role flow switches play in various applications, ensuring systems operate smoothly and safely.
資料ダウンロード
QCD調達購買管理クラウド「newji」は、調達購買部門で必要なQCD管理全てを備えた、現場特化型兼クラウド型の今世紀最高の購買管理システムとなります。
ユーザー登録
調達購買業務の効率化だけでなく、システムを導入することで、コスト削減や製品・資材のステータス可視化のほか、属人化していた購買情報の共有化による内部不正防止や統制にも役立ちます。
NEWJI DX
製造業に特化したデジタルトランスフォーメーション(DX)の実現を目指す請負開発型のコンサルティングサービスです。AI、iPaaS、および先端の技術を駆使して、製造プロセスの効率化、業務効率化、チームワーク強化、コスト削減、品質向上を実現します。このサービスは、製造業の課題を深く理解し、それに対する最適なデジタルソリューションを提供することで、企業が持続的な成長とイノベーションを達成できるようサポートします。
オンライン講座
製造業、主に購買・調達部門にお勤めの方々に向けた情報を配信しております。
新任の方やベテランの方、管理職を対象とした幅広いコンテンツをご用意しております。
お問い合わせ
コストダウンが利益に直結する術だと理解していても、なかなか前に進めることができない状況。そんな時は、newjiのコストダウン自動化機能で大きく利益貢献しよう!
(Β版非公開)