- お役立ち記事
- Manufacturing Process of Foldable Bicycles and Strengthening Lightweight Technology
月間76,176名の
製造業ご担当者様が閲覧しています*
*2025年3月31日現在のGoogle Analyticsのデータより
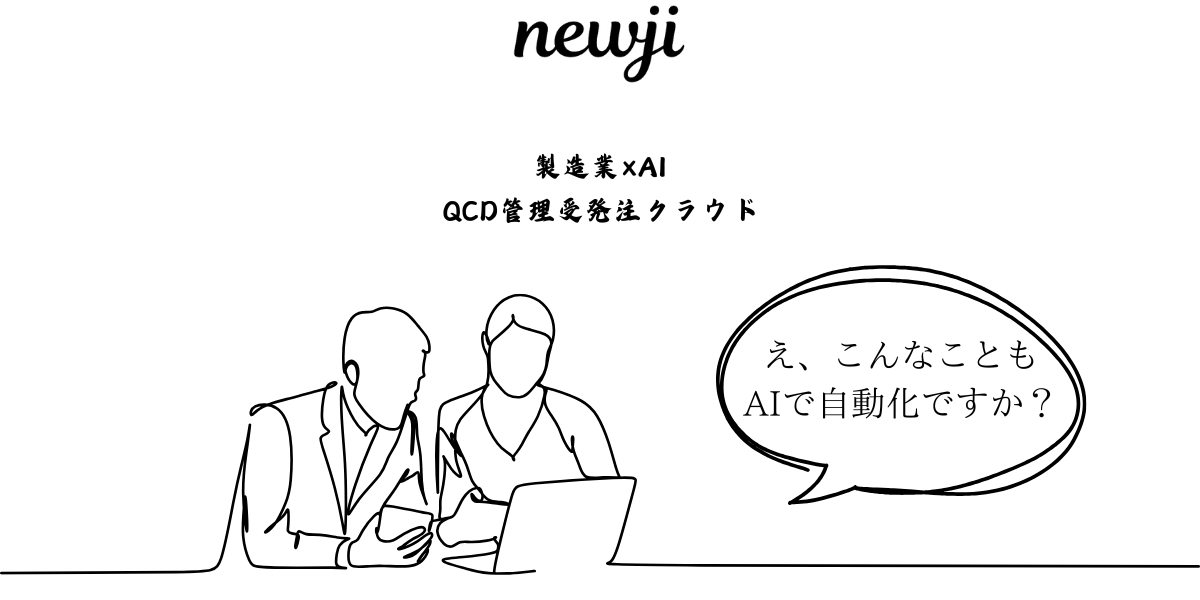
Manufacturing Process of Foldable Bicycles and Strengthening Lightweight Technology
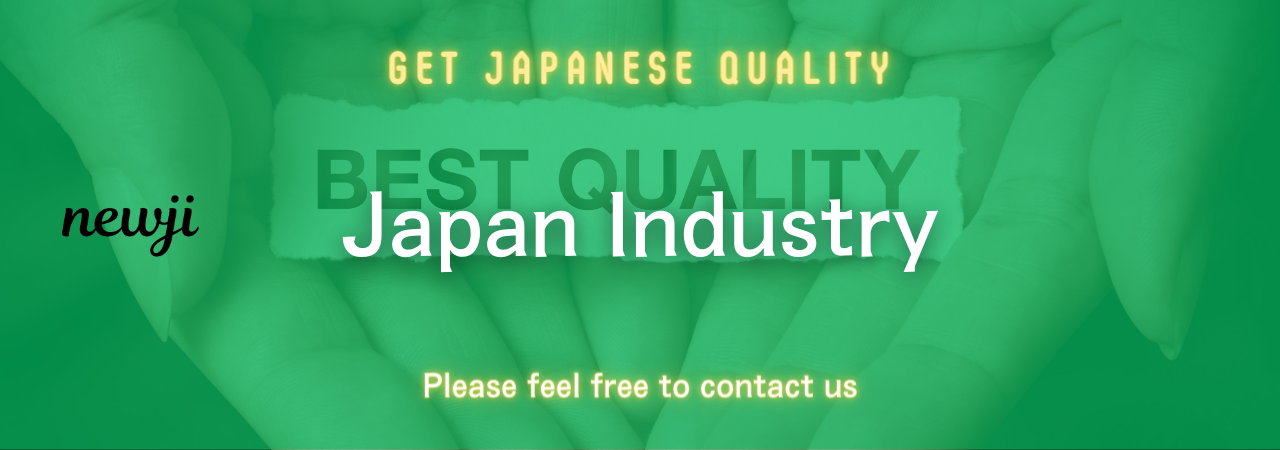
Foldable bicycles have become a favorite for city dwellers, adventurers, and even casual riders.
The convenience of folding the bike and carrying it on public transportation or storing it in a compact space is unparalleled.
Yet, what goes into making these marvels of engineering?
Let’s dive into the manufacturing process of foldable bicycles and explore the techniques used to strengthen lightweight technology.
目次
Design and Planning
The process begins with design and planning.
Engineers and designers collaborate to create blueprints and 3D models of the foldable bicycle.
This phase involves extensive research, considering factors like usability, portability, weight, and durability.
The goal is to produce a bike that is not only easily foldable but also sturdy and lightweight.
Material Selection
One of the critical decisions in this phase is the selection of materials.
Aluminum and carbon fiber are commonly used due to their lightweight and durable properties.
High-strength steel may also be employed for specific parts to ensure durability where needed.
Material choice directly impacts the weight, strength, and cost of the final product.
Frame Manufacturing
Once the design is finalized, the production of the bike frame begins.
The frame is the most crucial component as it needs to be both lightweight and strong.
Cutting and Shaping
The chosen materials, often sheets or tubes of metal, are cut to the required sizes.
Advanced machines like laser cutters ensure precision.
The pieces are then shaped using bending machines and molds.
This shaping process needs to be accurate to ensure that all parts fit perfectly when assembled.
Welding and Assembling
The cut and shaped pieces are then welded together to form the main structure of the bicycle.
Professionals use techniques like Tungsten Inert Gas (TIG) welding to ensure strong and clean joints.
Once welding is complete, the frame undergoes a heat treatment process to relieve stresses induced during welding and to enhance material properties.
This makes the frame more robust and durable.
Manufacturing Other Components
A foldable bicycle consists of many other components besides the frame.
These include the wheels, handlebars, gears, and folding mechanisms.
Wheels
Wheels are made by combining lightweight yet sturdy rims, usually made of aluminum or carbon fiber, with high-tension spokes and durable hubs.
The assembly ensures that wheels are light but can handle significant stress.
They are further tested for alignment and balance.
Handlebars and Seat Posts
Handlebars and seat posts are often made from aluminum or carbon fiber as well.
These components must be adjustable and able to sustain the rider’s weight and control inputs.
Attention to ergonomic design ensures rider comfort over long periods.
Gears and Chain
Gears and chains are outsourced from specialized manufacturers, ensuring they meet high standards for performance and durability.
They are then carefully integrated into the bike’s design.
This ensures efficient power transfer and smooth shifting.
Folding Mechanisms
The folding mechanism is the most distinctive feature of these bicycles.
It involves intricate hinges and latches, designed to withstand regular folding and unfolding without wearing out.
These mechanisms are usually made from high-strength materials like stainless steel and are rigorously tested to ensure reliability.
Assembly and Quality Control
Once all components are manufactured, the assembly process begins.
Each part is meticulously put together, aligning with the design specs.
Precision Assembly
During assembly, the accuracy of each component fitting is verified.
Any misalignment or fitting issues can result in poor performance or even safety hazards.
Technicians use specialized tools to ensure everything from wheel bearings to folding hinges are assembled correctly.
Quality Assurance Testing
After assembly, the bicycles undergo intensive quality control checks.
These tests evaluate the bike’s durability, weight-handling capacity, and overall performance.
Bikes are tested under various conditions to simulate real-world use.
Specific tests may include stress testing the frame, repetitive folding cycles, and real-world riding scenarios.
Only those that meet strict quality standards proceed to the next stage.
Finishing Touches
The final step involves adding finishing touches to the bicycle.
This includes painting, branding, and attaching accessories like reflectors and lights.
Painting and Branding
The frame and components are painted using high-quality, weather-resistant paints.
This not only provides aesthetic value but also protects the bike from environmental factors.
Branding, including decals and logos, is then applied.
Final Assembly
The final assembly involves attaching the last of the accessories and conducting a final round of quality checks.
Brakes, lights, reflectors, and other essential accessories are attached and verified for functionality.
The Science of Strengthening Lightweight Technology
A significant aspect of manufacturing foldable bicycles is the continuous effort to enhance the strength without adding weight.
Let’s explore some of the key strategies employed.
Use of Composite Materials
Composite materials like carbon fiber composites are widely used.
These materials offer high strength-to-weight ratios, making them ideal for parts like frames, handlebars, and seat posts.
The advanced bonding techniques ensure these composites are as strong as metal counterparts, if not stronger.
Finite Element Analysis (FEA)
During the design phase, Finite Element Analysis (FEA) is used to simulate how the bike will react under various stresses and strains.
This computational method helps to optimize materials and identify points that might need reinforcement, all without physically testing multiple prototypes.
Heat Treatments
Heat treatment processes such as annealing and quenching are applied to metal parts.
These processes draw out the best mechanical properties, making metals harder and more resilient while maintaining a lightweight profile.
Advanced Welding Techniques
Techniques like TIG welding are employed to create clean, strong joints.
This ensures that the frame remains lightweight but does not compromise on strength.
Conclusion
Manufacturing foldable bicycles involves a perfect blend of art and science.
From the initial design and material selection to the intricate processes of welding, assembling, and testing, each step is crucial in producing a final product that is both lightweight and durable.
The constant innovation in strengthening techniques ensures that riders enjoy the best of both worlds: a bike that is easy to carry and robust enough for daily use.
資料ダウンロード
QCD管理受発注クラウド「newji」は、受発注部門で必要なQCD管理全てを備えた、現場特化型兼クラウド型の今世紀最高の受発注管理システムとなります。
ユーザー登録
受発注業務の効率化だけでなく、システムを導入することで、コスト削減や製品・資材のステータス可視化のほか、属人化していた受発注情報の共有化による内部不正防止や統制にも役立ちます。
NEWJI DX
製造業に特化したデジタルトランスフォーメーション(DX)の実現を目指す請負開発型のコンサルティングサービスです。AI、iPaaS、および先端の技術を駆使して、製造プロセスの効率化、業務効率化、チームワーク強化、コスト削減、品質向上を実現します。このサービスは、製造業の課題を深く理解し、それに対する最適なデジタルソリューションを提供することで、企業が持続的な成長とイノベーションを達成できるようサポートします。
製造業ニュース解説
製造業、主に購買・調達部門にお勤めの方々に向けた情報を配信しております。
新任の方やベテランの方、管理職を対象とした幅広いコンテンツをご用意しております。
お問い合わせ
コストダウンが利益に直結する術だと理解していても、なかなか前に進めることができない状況。そんな時は、newjiのコストダウン自動化機能で大きく利益貢献しよう!
(β版非公開)