- お役立ち記事
- Manufacturing Process of Foldable Compact Beds and Durability Reinforcement
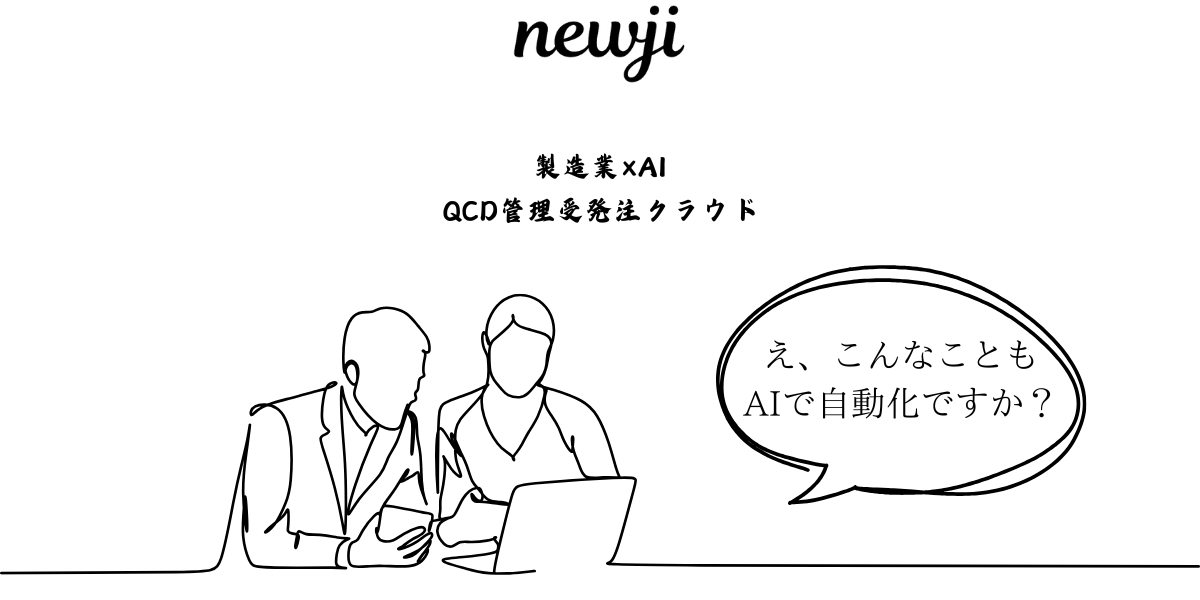
Manufacturing Process of Foldable Compact Beds and Durability Reinforcement
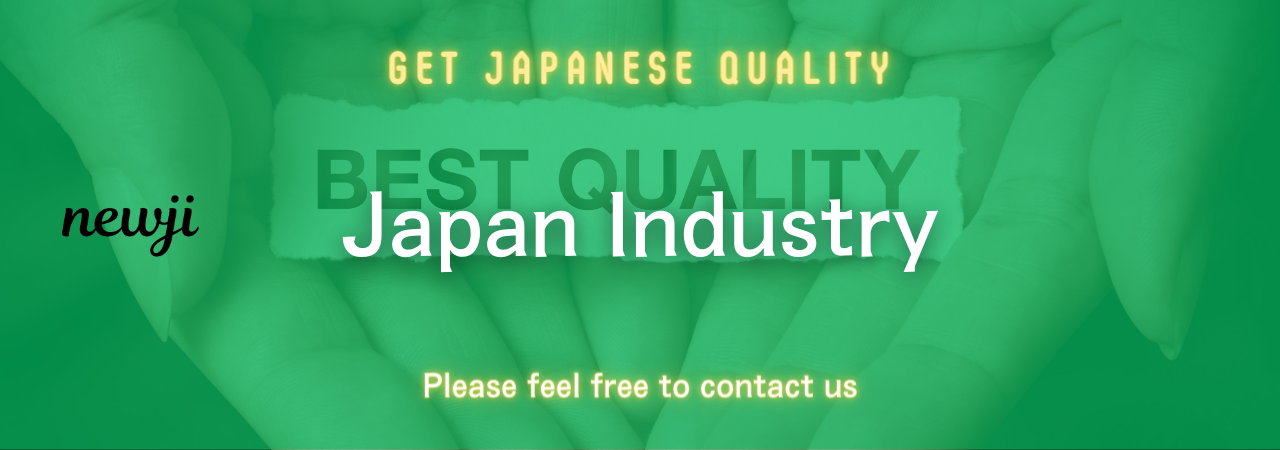
The manufacturing process of foldable compact beds encompasses a range of precise and carefully curated stages aimed at creating a versatile, durable, and space-saving product.
From material selection to assembly, every step impacts the overall functionality and longevity of the bed.
Understanding these processes can offer insight into why these beds have become increasingly popular in modern living spaces.
目次
Material Selection
The first step in the manufacturing process involves selecting quality materials.
Manufacturers typically use a combination of metals, plastics, and fabrics for various parts of the foldable compact bed.
Metal, usually aluminum or steel, is often chosen for the frame due to its strength and lightweight properties.
The choice of metal impacts the bed’s durability and weight, which are crucial factors for a foldable product.
High-strength plastic components complement the metal frame, providing additional support without significantly increasing the bed’s overall weight.
For the mattress and fabric coverings, manufacturers often opt for memory foam or high-density foam for comfort and durability.
Fabric choices vary, but breathable, easy-to-clean materials are preferred to ensure user comfort and low maintenance.
Design and Engineering
Proper design and engineering are vital to ensuring that the foldable compact bed is both functional and durable.
Engineers use computer-aided design (CAD) software to create detailed models of the bed, focusing on aspects like balance, weight distribution, and foldability.
During this stage, engineers also perform stress analysis tests to identify potential weak points in the design.
By addressing these issues early, they can enhance the durability and functionality of the bed.
Another critical aspect of the design phase is the creation of an effective folding mechanism.
This mechanism must be both easy to use and strong enough to withstand repeated use without failure.
Common mechanisms include hinge systems, sliding rails, and locking joints.
Manufacturing Components
Once the design is finalized, the manufacturing phase begins.
Individual components are produced using various manufacturing techniques like cutting, welding, molding, and sewing.
Metal components are typically cut and shaped using laser cutters or precision stamping machines.
Welding may be used to join metal parts, creating a strong and stable frame.
Plastic parts are usually created through injection molding, which allows for high precision and consistency.
For the mattress and fabric parts, manufacturers cut foam and fabric to the required dimensions.
These pieces are then sewn together using industrial sewing machines that ensure strong and enduring seams.
Quality Control
Quality control is a crucial step in the manufacturing process to ensure each foldable compact bed meets high standards.
Components and finished beds undergo rigorous testing to evaluate their strength, durability, and functionality.
For the metal frame, stress tests simulate the weight and pressure the bed will experience during regular use.
These tests help identify any weaknesses or defects in the frame.
Plastic components are also tested for their ability to withstand pressure and impact without cracking or breaking.
Foam and fabric parts are examined for comfort, density, and structural integrity.
Manufacturers often perform durability tests to ensure the foam does not lose its shape or firmness over time.
Quality control inspectors check sewing quality to verify that seams are strong and unlikely to rip or fray.
Assembly and Folding Mechanism
The assembly process brings all the individual components together to create the final product.
This step requires precision to ensure that each part fits perfectly and functions as intended.
Workers follow detailed assembly instructions to attach the metal frame, plastic components, mattress, and fabric coverings.
The folding mechanism is a critical component of the assembly process, requiring careful installation to ensure it operates smoothly.
Many manufacturers use automated assembly lines to improve efficiency and consistency.
However, some aspects of assembly, particularly those involving the folding mechanism, may require manual intervention to guarantee accuracy and reliability.
After assembly, the bed undergoes a final series of tests to confirm that all parts work together seamlessly.
These tests typically include opening and closing the bed multiple times to ensure the folding mechanism is durable and easy to use.
Durability Reinforcement
To improve the bed’s durability, additional reinforcement measures are often implemented.
These measures can include adding extra support bars, using higher-grade materials, or incorporating more robust folding mechanisms.
Extra support bars can be strategically placed within the frame to enhance its structural integrity.
Using higher-grade materials, like tempered steel or reinforced plastic, extends the bed’s lifespan by making it more resistant to wear and tear.
Improving the folding mechanism is another effective way to reinforce durability.
Using robust hinges, heavy-duty locking joints, and smooth sliding rails helps ensure the mechanism does not fail over time.
Coating and Finishes
Applying coatings and finishes is another technique for enhancing the bed’s durability.
Metal components often receive a protective coating, such as powder coating or electroplating, to prevent rust and corrosion.
These coatings also add an extra layer of strength, making the metal more resistant to scratches and dents.
Fabric coverings may be treated with water-resistant or stain-resistant coatings.
These treatments make the fabric more durable and easier to clean, improving the bed’s overall longevity and user experience.
Packaging and Shipment
Once the foldable compact beds are fully assembled and tested, they are carefully packaged for shipment.
Packaging plays a significant role in protecting the product during transportation.
Manufacturers use sturdy boxes, cushioning materials, and secure straps to ensure the beds remain undamaged en route to their final destination.
Clear instructions and sometimes assembly tools are included in the packaging to help customers set up the bed easily once it arrives.
By the time these beds reach consumers, they are ready for immediate use, showcasing the meticulous manufacturing process they have undergone.
Overall, the manufacturing process of foldable compact beds is a detailed and well-orchestrated series of steps designed to create a product that is not only functional and comfortable but also highly durable.
The attention to detail at every stage, from material selection to quality control and final assembly, ensures that these beds meet the rigorous demands of modern living, offering a convenient and long-lasting solution for space-conscious consumers.
資料ダウンロード
QCD調達購買管理クラウド「newji」は、調達購買部門で必要なQCD管理全てを備えた、現場特化型兼クラウド型の今世紀最高の購買管理システムとなります。
ユーザー登録
調達購買業務の効率化だけでなく、システムを導入することで、コスト削減や製品・資材のステータス可視化のほか、属人化していた購買情報の共有化による内部不正防止や統制にも役立ちます。
NEWJI DX
製造業に特化したデジタルトランスフォーメーション(DX)の実現を目指す請負開発型のコンサルティングサービスです。AI、iPaaS、および先端の技術を駆使して、製造プロセスの効率化、業務効率化、チームワーク強化、コスト削減、品質向上を実現します。このサービスは、製造業の課題を深く理解し、それに対する最適なデジタルソリューションを提供することで、企業が持続的な成長とイノベーションを達成できるようサポートします。
オンライン講座
製造業、主に購買・調達部門にお勤めの方々に向けた情報を配信しております。
新任の方やベテランの方、管理職を対象とした幅広いコンテンツをご用意しております。
お問い合わせ
コストダウンが利益に直結する術だと理解していても、なかなか前に進めることができない状況。そんな時は、newjiのコストダウン自動化機能で大きく利益貢献しよう!
(Β版非公開)