- お役立ち記事
- Manufacturing Process of Foldable Electric Food Processors and Precision Blade Improvement
月間76,176名の
製造業ご担当者様が閲覧しています*
*2025年3月31日現在のGoogle Analyticsのデータより
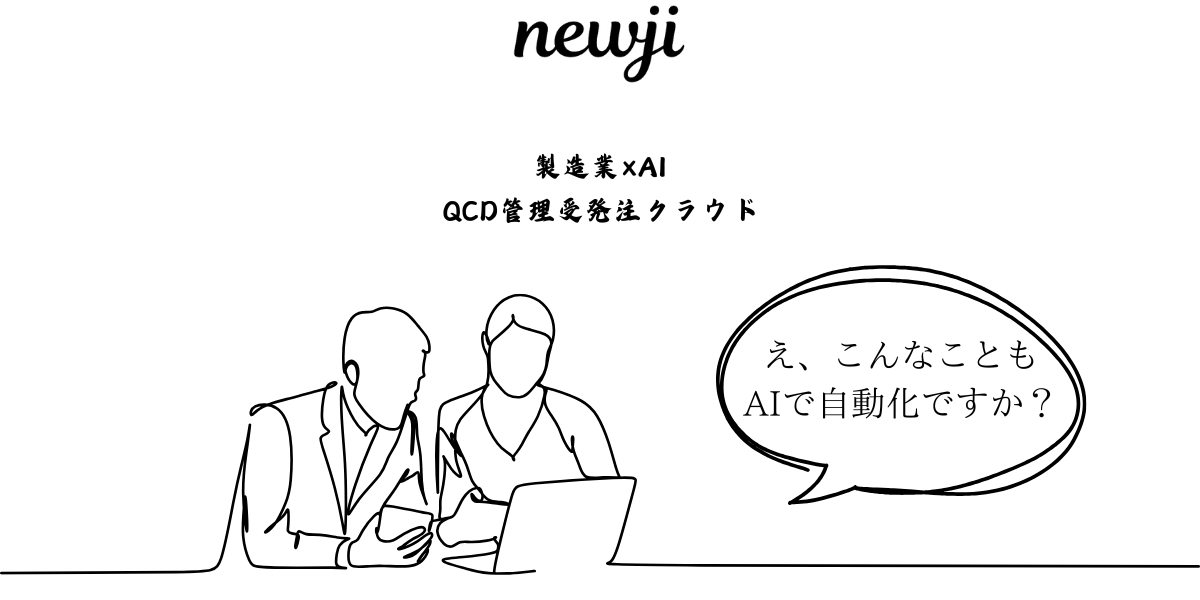
Manufacturing Process of Foldable Electric Food Processors and Precision Blade Improvement
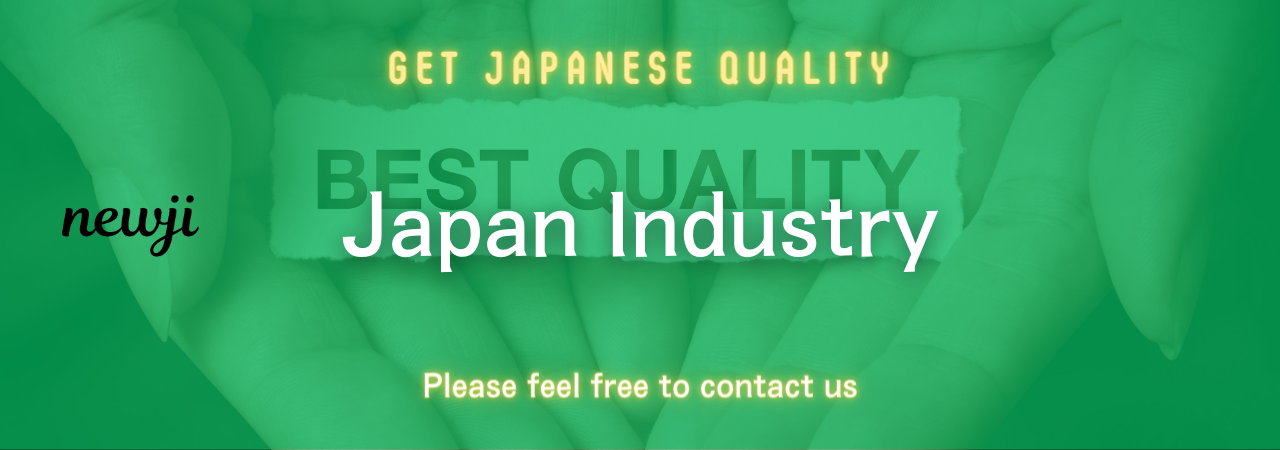
目次
Introduction
Foldable electric food processors are revolutionizing modern kitchens.
They save space, offer versatility, and make food preparation much easier.
But have you ever wondered how these marvels of engineering are made?
The manufacturing process involves a series of steps that ensure each device is efficient, durable, and safe.
Additionally, the improvement of precision blades within these processors plays a crucial role in their performance.
Design and Planning
Concept Creation
The first step in manufacturing foldable electric food processors is the conceptual design.
Engineers and designers brainstorm ideas and sketch prototypes.
They aim to create a design that is ergonomic, efficient, and aesthetically pleasing.
At this stage, they define the key features such as foldability, blade sharpness, and motor power.
Prototype Development
After settling on a design, the next step is to create a prototype.
Prototyping allows engineers to test the initial design and make necessary adjustments.
Materials for the body, blades, and motor are selected.
Electronics are also tested to ensure the processor’s safety and efficiency.
Any issues identified during this stage are addressed before moving on to large-scale production.
Material Selection
Choosing the Right Plastic
The body of the food processor is usually made from high-strength, food-grade plastic.
This ensures durability and safety.
Plastics like polycarbonate and polypropylene are commonly used because of their resistance to wear and tear.
They also comply with food safety regulations.
Metal for Blades
Precision blades are typically made from stainless steel.
This metal is chosen for its strength, resistance to corrosion, and ability to maintain a sharp edge over time.
Some high-end processors may use titanium-coated blades for added durability and sharpness.
Manufacturing Process
Injection Molding
The manufacturing of the food processor’s body typically involves injection molding.
Molten plastic is injected into molds to form the different parts of the processor.
Once cooled, these parts are removed from the molds and assembled.
Blade Fabrication
Blade manufacturing is a critical aspect of the production process.
Stainless steel sheets are cut and shaped to form blades.
They undergo several stages of grinding and polishing to achieve the required sharpness and precision.
Advanced techniques like laser cutting may also be used for more intricate designs.
Motor Assembly
The electric motor is arguably the heart of the food processor.
Each motor is carefully assembled and tested to ensure it meets performance standards.
The motor components include stators, rotors, and various electronic circuits.
Assemblers follow strict protocols to ensure each motor is safe and reliable.
Final Assembly
Once all the components are ready, the final assembly takes place.
This involves putting together the body, motor, and blades of the food processor.
Each part is meticulously fitted to ensure smooth operation.
Safety features, such as automatic shut-off and locking mechanisms, are also integrated during this phase.
Quality Control
Quality control is vital to ensure that each foldable electric food processor meets industry standards.
Each unit undergoes rigorous testing.
Tests include checking for electrical safety, motor performance, and blade sharpness.
Any defects are identified and rectified before the product reaches the consumer.
Improvements in Precision Blades
Advanced Materials
One of the key areas of improvement in foldable electric food processors has been in the materials used for precision blades.
Aside from stainless steel, manufacturers are exploring materials like ceramic and titanium.
These materials offer exceptional sharpness and durability.
Titanium-coated blades, for instance, remain sharp longer and are resistant to chipping.
Cutting Techniques
Modifications in cutting techniques have significantly enhanced blade precision.
Laser cutting, for instance, allows for more detailed and intricate blade designs.
This technique ensures that each blade has a uniform sharp edge, improving overall performance.
Blade Coatings
Special coatings like non-stick or anti-bacterial films are being applied to blades.
These coatings help maintain blade sharpness and improve hygiene.
Non-stick coatings ensure that food doesn’t cling to the blades, making them easier to clean.
Anti-bacterial coatings help reduce the likelihood of contamination.
Conclusion
Understanding the manufacturing process of foldable electric food processors and the improvements in precision blades gives us a deeper appreciation for these indispensable kitchen tools.
From conceptual design to the final product, each step ensures that the food processors are efficient, durable, and safe.
Advancements in blade materials and cutting techniques continue to improve their performance, making food preparation simpler and more efficient.
資料ダウンロード
QCD管理受発注クラウド「newji」は、受発注部門で必要なQCD管理全てを備えた、現場特化型兼クラウド型の今世紀最高の受発注管理システムとなります。
ユーザー登録
受発注業務の効率化だけでなく、システムを導入することで、コスト削減や製品・資材のステータス可視化のほか、属人化していた受発注情報の共有化による内部不正防止や統制にも役立ちます。
NEWJI DX
製造業に特化したデジタルトランスフォーメーション(DX)の実現を目指す請負開発型のコンサルティングサービスです。AI、iPaaS、および先端の技術を駆使して、製造プロセスの効率化、業務効率化、チームワーク強化、コスト削減、品質向上を実現します。このサービスは、製造業の課題を深く理解し、それに対する最適なデジタルソリューションを提供することで、企業が持続的な成長とイノベーションを達成できるようサポートします。
製造業ニュース解説
製造業、主に購買・調達部門にお勤めの方々に向けた情報を配信しております。
新任の方やベテランの方、管理職を対象とした幅広いコンテンツをご用意しております。
お問い合わせ
コストダウンが利益に直結する術だと理解していても、なかなか前に進めることができない状況。そんな時は、newjiのコストダウン自動化機能で大きく利益貢献しよう!
(β版非公開)