- お役立ち記事
- Manufacturing Process of Front Bumpers and Impact Absorption Improvement
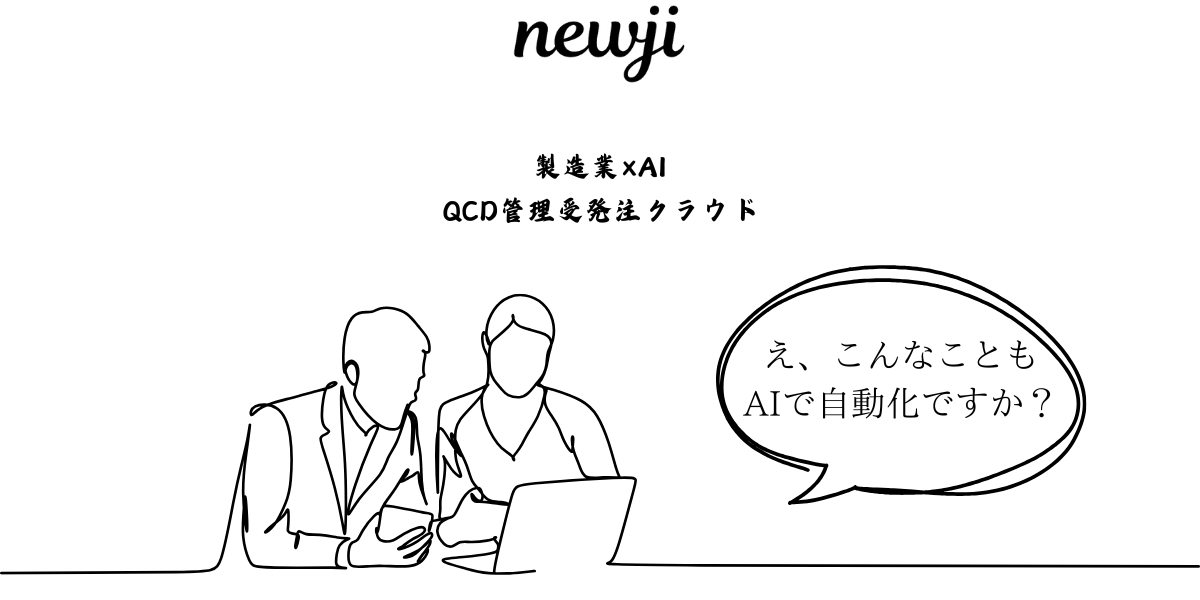
Manufacturing Process of Front Bumpers and Impact Absorption Improvement
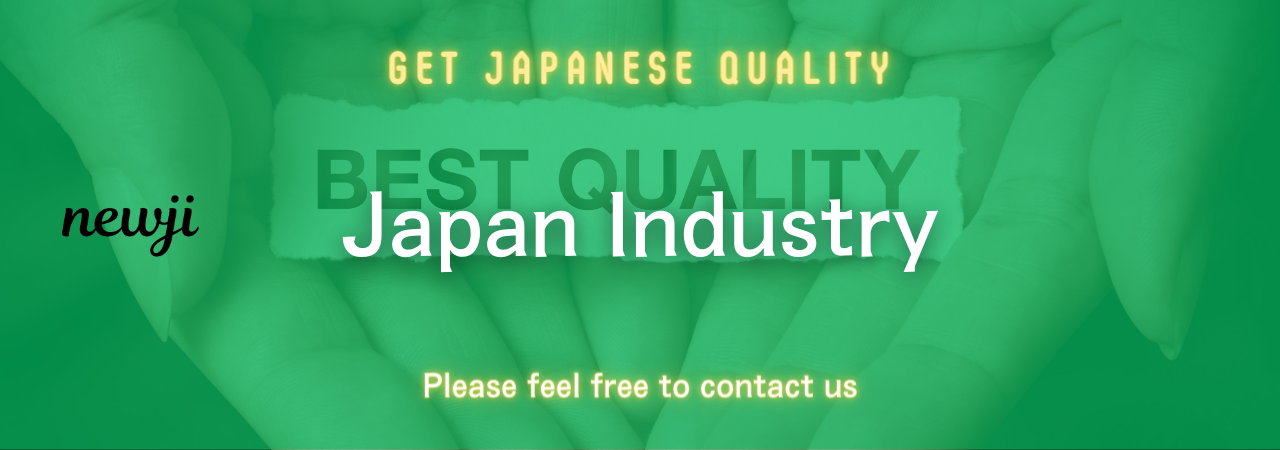
The manufacturing process of front bumpers is a detailed and essential procedure, especially regarding cars’ safety and performance.
The front bumper plays a critical role in protecting vehicles and their occupants during collisions.
This article will explore the stages involved in manufacturing front bumpers and highlight advancements aimed at improving impact absorption, ultimately enhancing vehicle safety.
目次
Material Selection
The first step in manufacturing front bumpers is selecting suitable materials.
Manufacturers often choose materials based on factors like cost, weight, and safety performance.
Common materials used for front bumpers include:
– **Plastic**: Lightweight and cost-effective.
– **Aluminum**: Lightweight and offers good impact resistance.
– **Steel**: Strong and highly durable.
Modern advancements have also introduced materials like reinforced composites, providing higher strength-to-weight ratios.
Design and Engineering
Once the material is selected, the next stage involves the design and engineering phase.
CAD (Computer-Aided Design) software is used to design the bumper, ensuring that it meets various safety standards and aesthetic specifications.
Aerodynamics
The design must account for aerodynamics to reduce wind resistance.
Smoother designs can enhance the car’s fuel efficiency, contributing to better fuel economy.
Crash Analysis
Engineers perform simulated crash tests using software to predict how the bumper will behave in a collision.
This helps in identifying areas that require reinforcement and ensures the design offers optimal impact absorption.
Prototyping and Testing
After the design phase, a prototype of the bumper is created.
This is a crucial step as it provides an opportunity to test the design in real-world conditions.
Physical Testing
The prototypes undergo rigorous physical testing to evaluate their strength and durability.
Tests include impact tests, stress tests, and deformation analysis, which help fine-tune the design for maximum safety.
Regulatory Compliance
Bumpers must comply with various regulatory standards.
Manufacturers must ensure the bumper meets these standards before mass production begins.
This includes testing for pedestrian safety, collision standards, and more.
Manufacturing Process
The manufacturing process of front bumpers involves several steps to ensure they are produced efficiently and meet high-quality standards.
Molding
The chosen material is first shaped into the bumper’s form using a molding process.
For plastic bumpers, injection molding is commonly used, where molten plastic is injected into a mold and allowed to cool and harden.
Trimming and Assembly
Once the molding process is complete, the bumper is trimmed to remove any excess material.
Trimming ensures that the bumper has clean edges and fits perfectly onto the vehicle.
Additional components such as mounting brackets and reinforcement bars are then assembled onto the bumper.
Surface Treatment
Before painting, the bumper undergoes surface treatment to ensure better adhesion and durability of the paint.
This includes washing, priming, and applying a flexible surface coating.
Painting
The bumper is painted using a robotic spray system to ensure a consistent and high-quality finish.
Multiple layers of paint are applied to achieve the desired color and finish.
Quality Control
Finally, the bumper undergoes a quality control inspection.
This step ensures each bumper meets the required specifications and is free from defects before shipping to manufacturers.
Impact Absorption Improvement
Advancements in technology and materials have led to significant improvements in the impact absorption capabilities of front bumpers.
Advanced Materials
The use of advanced materials like carbon fiber and high-strength composites has improved the impact absorption performance of bumpers.
These materials provide better energy dissipation and reduce the overall weight of the bumper, contributing to better fuel efficiency.
Energy Absorbing Structures
Modern bumpers are designed with energy-absorbing structures, such as crumple zones and honeycomb patterns.
These structures deform upon impact, absorbing and dissipating energy, thus reducing the force transmitted to occupants.
Foam Inserts
Some manufacturers incorporate foam inserts within the bumper to enhance its impact absorption properties.
These inserts help distribute the impact force more evenly, minimizing damage to the vehicle and reducing the risk of injury to occupants.
Technological Advancements
Technological advancements, such as sensor integration, have further improved bumper safety.
Sensors can detect potential collisions and activate safety systems to mitigate the impact, thereby enhancing overall vehicle safety.
Environmental Considerations
Alongside advancements in safety, manufacturers are also focusing on environmentally-friendly practices during the bumper manufacturing process.
Recycling and Sustainability
Recycling old bumpers and using sustainable materials in production helps reduce waste and environmental impact.
Some manufacturers are exploring biodegradable materials and recyclable composites for future bumper designs.
Energy-Efficient Manufacturing
Implementing energy-efficient processes in manufacturing helps minimize the carbon footprint.
This includes using renewable energy sources and optimizing production processes to reduce energy consumption.
In conclusion, the manufacturing process of front bumpers is a meticulous and detailed procedure.
From material selection and design to prototyping, testing, and mass production, each stage is vital.
Advancements in materials and technology continue to improve the impact absorption capabilities of bumpers, ensuring higher safety standards for vehicles and their occupants.
By focusing on innovative materials and sustainable practices, manufacturers are not only enhancing safety but also contributing to environmental conservation.
With ongoing research and development, the future of front bumper manufacturing promises even greater improvements in both safety and sustainability, paving the way for safer and more environmentally-friendly vehicles.
資料ダウンロード
QCD調達購買管理クラウド「newji」は、調達購買部門で必要なQCD管理全てを備えた、現場特化型兼クラウド型の今世紀最高の購買管理システムとなります。
ユーザー登録
調達購買業務の効率化だけでなく、システムを導入することで、コスト削減や製品・資材のステータス可視化のほか、属人化していた購買情報の共有化による内部不正防止や統制にも役立ちます。
NEWJI DX
製造業に特化したデジタルトランスフォーメーション(DX)の実現を目指す請負開発型のコンサルティングサービスです。AI、iPaaS、および先端の技術を駆使して、製造プロセスの効率化、業務効率化、チームワーク強化、コスト削減、品質向上を実現します。このサービスは、製造業の課題を深く理解し、それに対する最適なデジタルソリューションを提供することで、企業が持続的な成長とイノベーションを達成できるようサポートします。
オンライン講座
製造業、主に購買・調達部門にお勤めの方々に向けた情報を配信しております。
新任の方やベテランの方、管理職を対象とした幅広いコンテンツをご用意しております。
お問い合わせ
コストダウンが利益に直結する術だと理解していても、なかなか前に進めることができない状況。そんな時は、newjiのコストダウン自動化機能で大きく利益貢献しよう!
(Β版非公開)