- お役立ち記事
- Manufacturing Process of Fuel Supply Lines and Pressure Resistance Improvement
月間76,176名の
製造業ご担当者様が閲覧しています*
*2025年3月31日現在のGoogle Analyticsのデータより
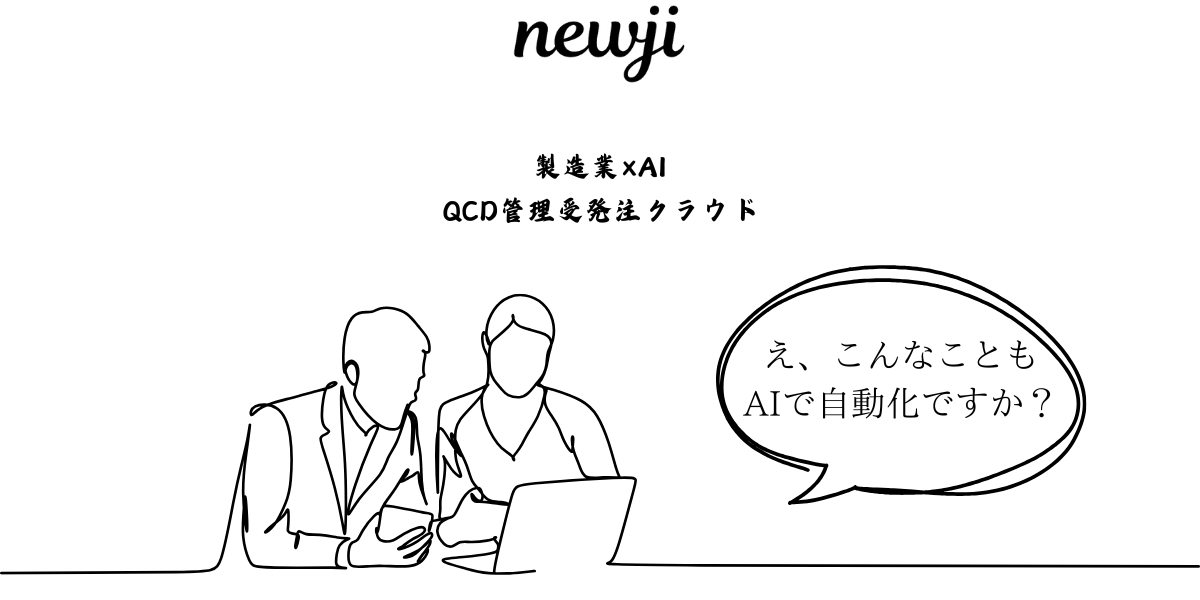
Manufacturing Process of Fuel Supply Lines and Pressure Resistance Improvement
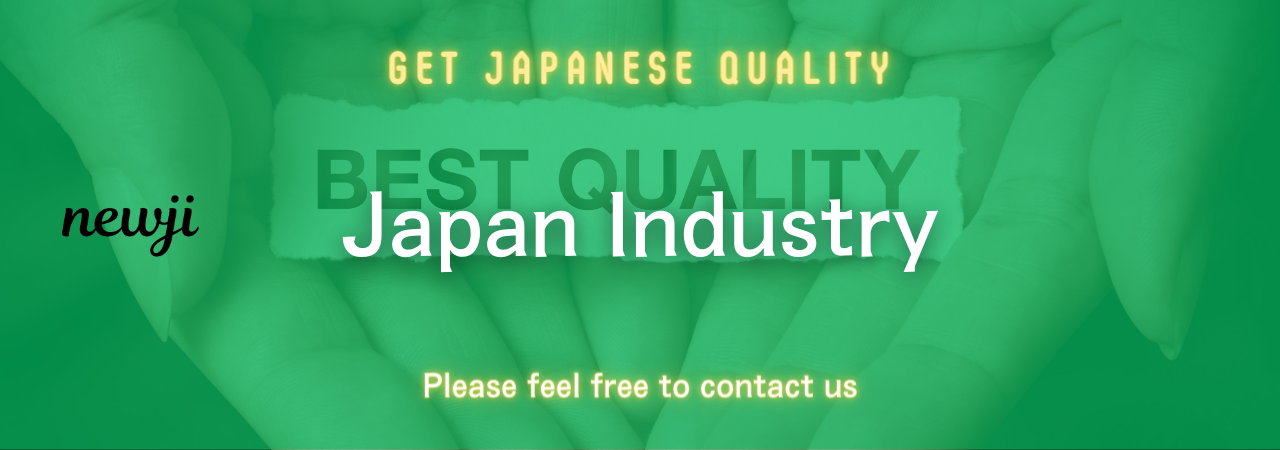
The manufacturing process of fuel supply lines is a critical aspect in the automotive industry.
This process ensures that vehicles run efficiently and safely.
To understand how these parts are made and improved, we need to look at several key stages.
目次
Material Selection
The first and most crucial step in the manufacturing process is choosing the right materials.
Fuel supply lines require materials that can withstand high pressures and are resistant to corrosion.
Common materials used include stainless steel, aluminum, and various high-strength polymers.
Each of these materials has unique properties that make them ideal for particular applications.
Stainless Steel
Stainless steel is often chosen for its durability and resistance to corrosion.
This makes it a suitable choice for fuel lines that must endure harsh environments.
Aluminum
Aluminum is another popular choice due to its lightweight nature and good resistance to corrosion.
This material is advantageous where weight reduction is a key concern.
High-Strength Polymers
High-strength polymers offer flexibility and durability.
These materials are often used in regions where flexibility is more important than rigidity.
Design and Engineering
After selecting the right material, the next step is designing the fuel supply lines.
Engineers use computer-aided design (CAD) software to create precise models of the fuel lines.
These designs must meet strict safety and performance standards.
Pressure Simulation
One crucial aspect of the design phase is simulating the pressure conditions that the fuel lines will encounter.
Engineers use various tools to predict how the lines will perform under different pressures.
This ensures that the designs are robust and reliable.
Prototyping
Once the design is complete, a prototype of the fuel supply line is created.
This prototype undergoes rigorous testing to identify any potential issues.
Only after successful testing does the design move to the mass production phase.
Manufacturing Techniques
There are several techniques used in the manufacturing of fuel supply lines.
Each technique has its advantages and is chosen based on the specific requirements of the fuel line.
Extrusion
Extrusion is a common technique used to manufacture polymer-based fuel lines.
In this process, raw material is pushed through a die to create a continuous shape.
This shape is then cut to the desired length.
Bending and Welding
For metal fuel lines, bending and welding are often required.
This process involves bending the metal into the desired shape and welding the joints to ensure a secure and leak-free connection.
Advanced machines ensure precision in the bending process to maintain the integrity of the fuel line.
Injection Molding
Injection molding is used primarily for components made from high-strength polymers.
In this process, molten material is injected into a mold, where it cools and hardens into the desired shape.
Quality Control
Quality control is a vital part of the manufacturing process to ensure that the fuel supply lines meet the highest standards.
Visual Inspection
Every fuel line undergoes visual inspection for any defects or inconsistencies.
This step helps identify and rectify issues before the product moves to the next stage.
Pressure Testing
Pressure testing is a critical part of quality control.
Fuel supply lines are subjected to high-pressure conditions to ensure they can withstand the operating pressures without failure.
Any lines that fail this test are rejected and not used in production.
Improving Pressure Resistance
Enhancing the pressure resistance of fuel supply lines is an ongoing challenge.
Engineers continually look for ways to improve this aspect to ensure safety and efficiency.
Material Enhancements
One way to improve pressure resistance is by developing and using better materials.
Advances in material science have led to the creation of composites that offer superior strength and resistance to high pressures.
Design Improvements
Design improvements can also enhance pressure resistance.
Engineers experiment with different shapes and structures to find designs that distribute pressure more evenly.
This reduces the likelihood of failure under high-pressure conditions.
Coating Technologies
Applying specialized coatings to fuel supply lines can significantly improve their pressure resistance and durability.
These coatings offer an extra layer of protection against corrosion and wear, thereby extending the lifespan of the fuel lines.
Future Trends
The future of fuel supply line manufacturing is exciting, with several trends promising to revolutionize the industry.
Advanced Materials
The development of more advanced materials will continue to play a critical role in the future.
Researchers are working on materials that offer even greater strength, flexibility, and resistance to extreme conditions.
Automation
Automation is another trend set to transform fuel supply line manufacturing.
Automated robots and machines will increase precision, reduce errors, and enhance efficiency.
This will lead to fuel supply lines that are not only better in quality but also more cost-effective.
Sustainability
Sustainability is becoming increasingly important in the manufacturing industry.
Efforts are being made to develop eco-friendly materials and processes that reduce the environmental impact of manufacturing fuel supply lines.
The use of recyclable materials and energy-efficient manufacturing techniques are just some of the steps being taken.
Understanding the manufacturing process and ways to improve pressure resistance is crucial to ensuring the efficiency and safety of automotive fuel systems.
From material selection to quality control, each stage plays a vital role.
As technology and materials continue to advance, the future looks promising for even more robust and efficient fuel supply lines.
資料ダウンロード
QCD管理受発注クラウド「newji」は、受発注部門で必要なQCD管理全てを備えた、現場特化型兼クラウド型の今世紀最高の受発注管理システムとなります。
ユーザー登録
受発注業務の効率化だけでなく、システムを導入することで、コスト削減や製品・資材のステータス可視化のほか、属人化していた受発注情報の共有化による内部不正防止や統制にも役立ちます。
NEWJI DX
製造業に特化したデジタルトランスフォーメーション(DX)の実現を目指す請負開発型のコンサルティングサービスです。AI、iPaaS、および先端の技術を駆使して、製造プロセスの効率化、業務効率化、チームワーク強化、コスト削減、品質向上を実現します。このサービスは、製造業の課題を深く理解し、それに対する最適なデジタルソリューションを提供することで、企業が持続的な成長とイノベーションを達成できるようサポートします。
製造業ニュース解説
製造業、主に購買・調達部門にお勤めの方々に向けた情報を配信しております。
新任の方やベテランの方、管理職を対象とした幅広いコンテンツをご用意しております。
お問い合わせ
コストダウンが利益に直結する術だと理解していても、なかなか前に進めることができない状況。そんな時は、newjiのコストダウン自動化機能で大きく利益貢献しよう!
(β版非公開)