- お役立ち記事
- Manufacturing Process of Fuel Tanks and Durability Reinforcement
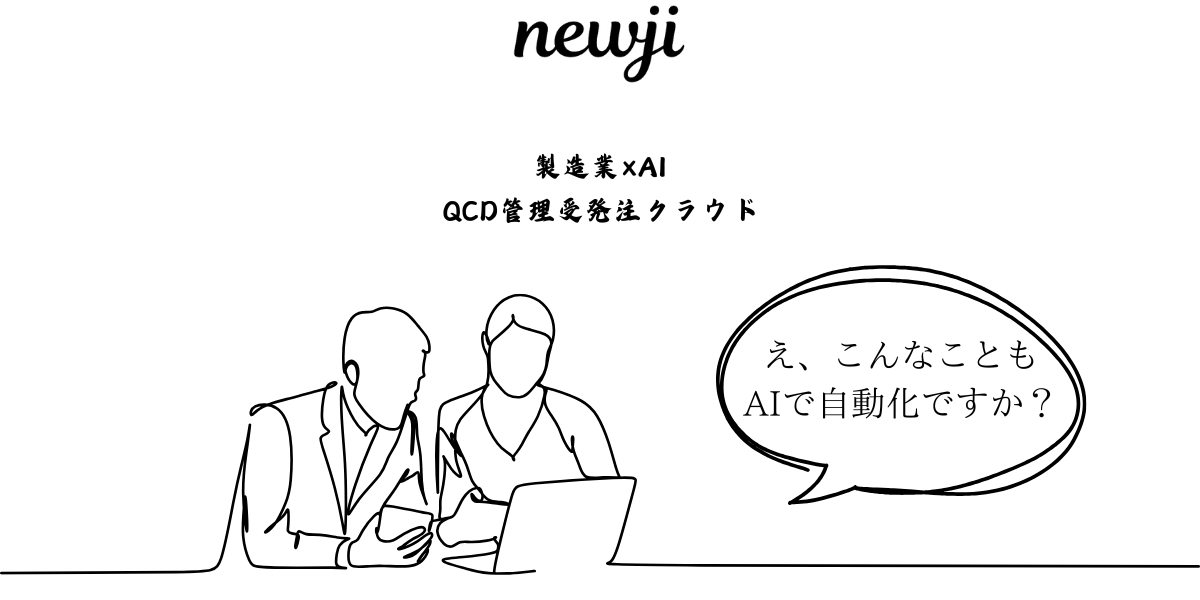
Manufacturing Process of Fuel Tanks and Durability Reinforcement
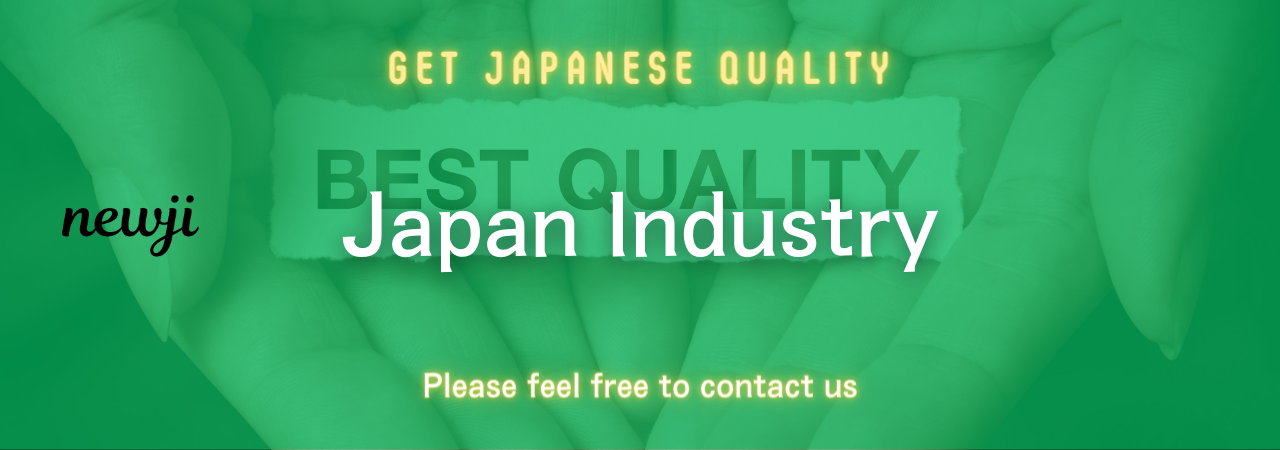
Fuel tanks play an essential role in storing and supplying fuel to engines, making them a critical component in various vehicles and machinery. This article delves into the manufacturing process of fuel tanks and the methods employed to reinforce their durability. Let’s explore the production steps and the innovations that ensure these tanks are reliable and long-lasting.
目次
Design and Material Selection
Choosing the Right Material
The first step in manufacturing a fuel tank is selecting the appropriate material. Common materials used include steel, aluminum, and high-density polyethylene (HDPE). Each material has its own set of advantages and is chosen based on the intended application of the fuel tank.
Steel is known for its strength and durability but is prone to rust. Therefore, it often requires additional coatings or treatments to prevent corrosion. Aluminum is lightweight and resistant to rust, making it ideal for high-performance vehicles. HDPE is a plastic material that offers flexibility, resistance to chemicals, and durability, making it suitable for a wide range of applications.
Design Specifications
Once the material is selected, engineers design the fuel tank based on specific requirements such as capacity, shape, and placement within the vehicle or machinery. CAD (Computer-Aided Design) software is widely used to create detailed 3D models of the fuel tank. These models help engineers visualize the tank, identify potential issues, and make necessary modifications before proceeding to production.
Manufacturing Process
Forming the Tank
The manufacturing process for fuel tanks varies depending on the material chosen.
For metallic tanks:
1. **Stamping and Forming:** Large sheets of steel or aluminum are cut into the desired shape using stamping machines. These sheets are then formed into the required shape through bending or pressing.
2. **Welding:** The individual parts of the tank are welded together to create a single, cohesive unit. Various welding techniques, such as MIG (Metal Inert Gas) welding, TIG (Tungsten Inert Gas) welding, or resistance welding, may be used to ensure strong and leak-proof seams.
For plastic tanks:
1. **Blow Molding:** HDPE tanks are typically made using the blow molding process. This involves melting the plastic and forming it into a parison (a tube-like piece). The parison is then placed into a mold, and air is blown into it, forcing the plastic to take the shape of the mold.
2. **Rotational Molding:** Another method for plastic tanks is rotational molding, where powdered plastic is heated inside a rotating mold. The rotation ensures an even distribution of material, forming a consistent wall thickness.
Surface Treatment and Coating
Metallic fuel tanks may undergo surface treatments to enhance their durability and resistance to corrosion. Treatments such as galvanizing (coating with zinc) or applying a protective paint layer are common methods to prevent rust and deterioration. Plastic tanks generally do not require surface treatments due to the inherent resistance of HDPE to chemicals and environmental factors.
Durability Reinforcement
Leak Testing
After the tank is formed, it must undergo rigorous leak testing to ensure it is completely sealed. This typically involves filling the tank with air or water and monitoring for any pressure drops or visible leaks. High-pressure testing can also be conducted to simulate the conditions the tank will face during service, ensuring it can withstand extreme pressures without failing.
Impact Resistance
Fuel tanks must be able to withstand impacts without rupturing or leaking. To achieve this, manufacturers often incorporate various reinforcement techniques:
1. **Baffles:** These are internal barriers within the tank that help to reduce the movement of fuel during sudden stops or impacts, minimizing the risk of damage.
2. **Reinforced Corners and Edges:** Adding extra material or using thicker sections at vulnerable points, such as corners and edges, helps to increase the tank’s overall strength and resistance to damage.
3. **Crash Testing:** Some fuel tanks, especially those used in automotive applications, are subjected to crash tests to evaluate their performance in the event of a collision. These tests help manufacturers identify potential weaknesses and make necessary improvements to enhance safety.
Corrosion Resistance
Corrosion is a significant concern for metallic fuel tanks, as it can lead to leaks and contamination of the fuel. To combat this, manufacturers use a variety of coatings and treatments to protect the tank’s surface. These include:
1. **Galvanization:** Coating the tank with a layer of zinc helps to prevent rust and corrosion. This is a common method used for steel tanks.
2. **Epoxy Coatings:** Applying a layer of epoxy paint adds an extra barrier against rust and chemical corrosion, prolonging the tank’s lifespan.
3. **Anodizing:** For aluminum tanks, anodizing creates a protective oxide layer on the surface, enhancing its resistance to corrosion and wear.
Quality Control
Inspection and Testing
Throughout the manufacturing process, fuel tanks undergo various inspections and tests to ensure they meet quality standards. These tests include:
1. **Dimensional Checks:** Verifying that the tank’s dimensions match the design specifications to ensure proper fit and function.
2. **Ultrasonic Testing:** Using ultrasonic waves to detect any flaws or defects within the material that may not be visible on the surface.
3. **Pressure Testing:** Ensuring the tank can withstand high pressures without leaking or failing.
Certifications
Fuel tanks must comply with industry standards and regulations to ensure safety and performance. These standards may vary depending on the application and region but typically include certifications such as:
1. **DOT (Department of Transportation):** Compliance with DOT regulations ensures the tank is safe for use in transportation applications.
2. **ISO (International Organization for Standardization):** Adherence to ISO standards ensures the tank meets international quality and safety requirements.
3. **OEM (Original Equipment Manufacturer) Specifications:** Meeting the specific requirements of the vehicle or machinery manufacturer ensures the tank will function correctly within the intended system.
The manufacturing process of fuel tanks is a complex and meticulous procedure that involves careful design, material selection, and various production techniques. By employing advanced manufacturing processes and reinforcement methods, manufacturers can create fuel tanks that are not only durable but also safe and reliable. Quality control measures and adherence to industry standards further ensure that these tanks will perform effectively in their intended applications.
資料ダウンロード
QCD調達購買管理クラウド「newji」は、調達購買部門で必要なQCD管理全てを備えた、現場特化型兼クラウド型の今世紀最高の購買管理システムとなります。
ユーザー登録
調達購買業務の効率化だけでなく、システムを導入することで、コスト削減や製品・資材のステータス可視化のほか、属人化していた購買情報の共有化による内部不正防止や統制にも役立ちます。
NEWJI DX
製造業に特化したデジタルトランスフォーメーション(DX)の実現を目指す請負開発型のコンサルティングサービスです。AI、iPaaS、および先端の技術を駆使して、製造プロセスの効率化、業務効率化、チームワーク強化、コスト削減、品質向上を実現します。このサービスは、製造業の課題を深く理解し、それに対する最適なデジタルソリューションを提供することで、企業が持続的な成長とイノベーションを達成できるようサポートします。
オンライン講座
製造業、主に購買・調達部門にお勤めの方々に向けた情報を配信しております。
新任の方やベテランの方、管理職を対象とした幅広いコンテンツをご用意しております。
お問い合わせ
コストダウンが利益に直結する術だと理解していても、なかなか前に進めることができない状況。そんな時は、newjiのコストダウン自動化機能で大きく利益貢献しよう!
(Β版非公開)