- お役立ち記事
- Manufacturing Process of Fuel Tanks and Durability Reinforcement
月間76,176名の
製造業ご担当者様が閲覧しています*
*2025年3月31日現在のGoogle Analyticsのデータより
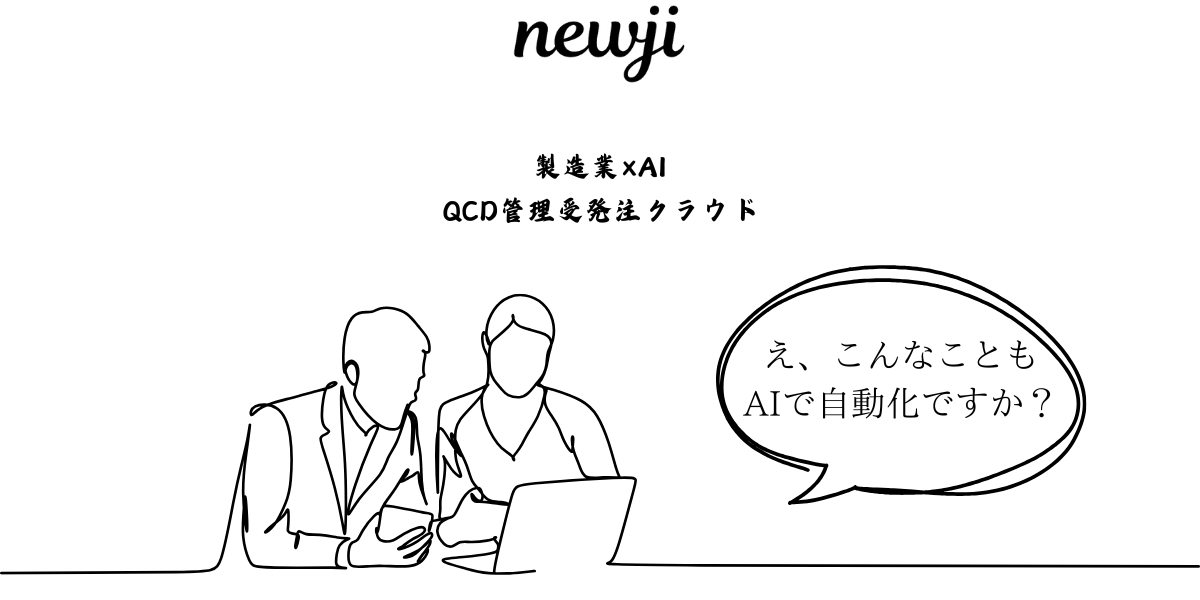
Manufacturing Process of Fuel Tanks and Durability Reinforcement
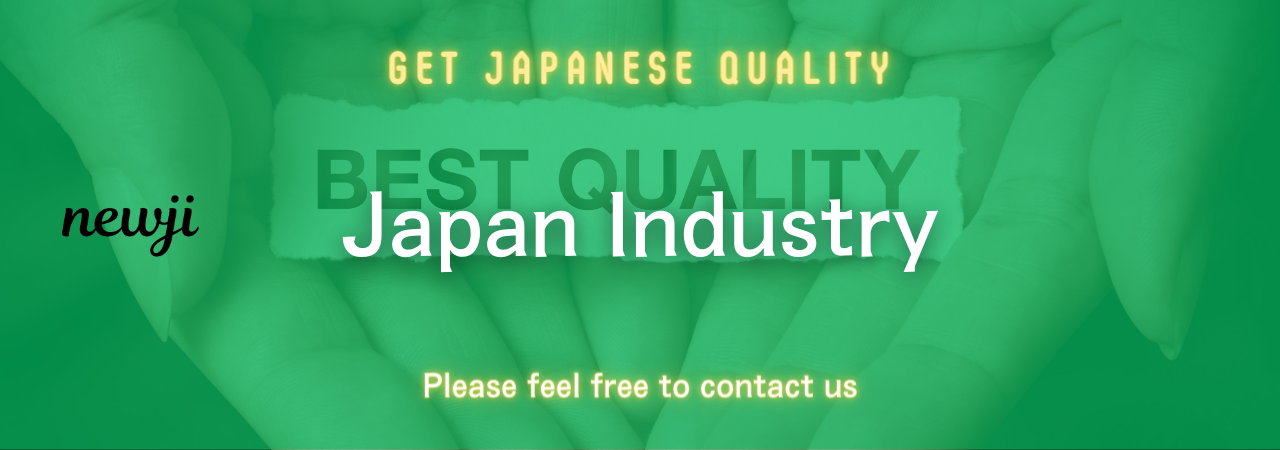
The fuel tank is an essential component in a vehicle, serving as the storage space for fuel that powers the engine.
Manufacturing a durable and efficient fuel tank involves a series of complex processes and technologies aimed at ensuring safety, reliability, and performance.
In this article, we will delve into the manufacturing process of fuel tanks and how they are reinforced for durability.
目次
Raw Material Selection
The first step in manufacturing a fuel tank is selecting the appropriate raw materials.
Fuel tanks are typically made from metals like steel or aluminum, and high-density polyethylene (HDPE) is also commonly used for plastic fuel tanks.
Each material has its own advantages; for example, steel is strong and durable but heavy, while plastic is lighter and resistant to corrosion but may require additional reinforcement to match the strength of metal tanks.
Design and Engineering
Once the raw materials are selected, the next step is designing the fuel tank.
Advanced computer-aided design (CAD) software is used to create a detailed blueprint of the tank, considering factors such as shape, size, and structural requirements.
Engineers must ensure that the design complies with stringent safety regulations and can hold the required amount of fuel.
This stage also involves simulations to predict how the fuel tank will perform under various conditions, such as crashes or extreme temperatures.
Forming and Shaping
After the design phase, the actual manufacturing process begins with forming and shaping the raw materials.
For metal fuel tanks, this usually involves a process called stamping, where metal sheets are cut and shaped into the desired form using high-pressure presses.
Plastic fuel tanks are typically manufactured using blow molding, where molten plastic is extruded into a mold and then inflated to form the shape of the tank.
Both processes require precision to ensure the tank meets design specifications.
Joining and Assembly
The next step is joining and assembling the various parts of the fuel tank.
For metal tanks, welding is commonly used to join the different sections together.
Advanced welding techniques, such as MIG or TIG welding, provide strong and durable seams.
For plastic tanks, the sections are fused together using techniques like ultrasonic welding or hot plate welding.
Once assembled, additional components like fuel pumps, sensors, and valves are installed.
Surface Treatment
To enhance the durability of the fuel tank, surface treatment is an important step.
Metal tanks undergo processes like galvanizing or coating with anti-corrosion layers to protect against rust and wear.
Plastic tanks may be treated with UV-resistant coatings to prevent degradation due to sunlight.
Surface treatments ensure that the fuel tank can withstand harsh environmental conditions and maintain its integrity over time.
Testing and Quality Control
Before the fuel tank is ready for use, it must undergo rigorous testing and quality control.
Several tests are conducted to check for leaks, strength, and durability.
Hydrostatic testing involves filling the tank with water to check for leaks or weak points.
Pressure testing ensures that the tank can withstand the internal pressure of the fuel.
Crash simulations and vibration tests are also performed to ensure the tank can survive impact and movement without failing.
Durability Reinforcement
Durability reinforcement is a crucial aspect of fuel tank manufacturing, especially for tanks made of lighter materials like plastic.
Reinforcement usually involves adding layers of materials or using composite structures to enhance strength.
For example, plastic tanks may have internal baffles or ribs to reduce sloshing and improve structural integrity.
In some cases, fiber-reinforced plastics or metal liners are used to provide extra strength.
The goal is to produce a tank that is not only strong but also lightweight and efficient.
Material Advances
Recent advances in materials science have led to the development of new materials for fuel tanks.
For example, carbon fiber-reinforced polymers offer excellent strength and durability while being lightweight.
These materials are increasingly being used in high-performance and electric vehicles, where weight reduction is critical.
Innovative Designs
Innovation in design also plays a role in enhancing the durability of fuel tanks.
Modular designs, for example, allow for easy replacement of damaged sections without the need to replace the entire tank.
Smart tanks equipped with sensors can monitor fuel levels, temperature, and pressure in real-time, providing data to optimize performance and detect potential issues before they become serious problems.
Environmental Considerations
Modern fuel tank manufacturing also takes environmental considerations into account.
Using recyclable materials and sustainable manufacturing processes helps reduce the environmental impact.
Additionally, fuel tanks are designed to minimize evaporative emissions, which contribute to air pollution.
Advanced sealing technologies and vapor recovery systems are employed to ensure that fuel vapors are contained and not released into the atmosphere.
Conclusion
The manufacturing process of fuel tanks is a complex and highly technical endeavor, involving multiple steps from raw material selection to final testing.
Durability reinforcement is a key focus, ensuring that the fuel tank can withstand various conditions and provide reliable performance over its lifespan.
With advancements in materials and design, fuel tanks continue to evolve, offering greater strength, efficiency, and environmental compliance.
Understanding this process provides insight into the intricate engineering and technology that make safe and durable fuel tanks possible.
資料ダウンロード
QCD管理受発注クラウド「newji」は、受発注部門で必要なQCD管理全てを備えた、現場特化型兼クラウド型の今世紀最高の受発注管理システムとなります。
ユーザー登録
受発注業務の効率化だけでなく、システムを導入することで、コスト削減や製品・資材のステータス可視化のほか、属人化していた受発注情報の共有化による内部不正防止や統制にも役立ちます。
NEWJI DX
製造業に特化したデジタルトランスフォーメーション(DX)の実現を目指す請負開発型のコンサルティングサービスです。AI、iPaaS、および先端の技術を駆使して、製造プロセスの効率化、業務効率化、チームワーク強化、コスト削減、品質向上を実現します。このサービスは、製造業の課題を深く理解し、それに対する最適なデジタルソリューションを提供することで、企業が持続的な成長とイノベーションを達成できるようサポートします。
製造業ニュース解説
製造業、主に購買・調達部門にお勤めの方々に向けた情報を配信しております。
新任の方やベテランの方、管理職を対象とした幅広いコンテンツをご用意しております。
お問い合わせ
コストダウンが利益に直結する術だと理解していても、なかなか前に進めることができない状況。そんな時は、newjiのコストダウン自動化機能で大きく利益貢献しよう!
(β版非公開)