- お役立ち記事
- Manufacturing Process of Gas Valves and Durability Reinforcement
月間76,176名の
製造業ご担当者様が閲覧しています*
*2025年3月31日現在のGoogle Analyticsのデータより
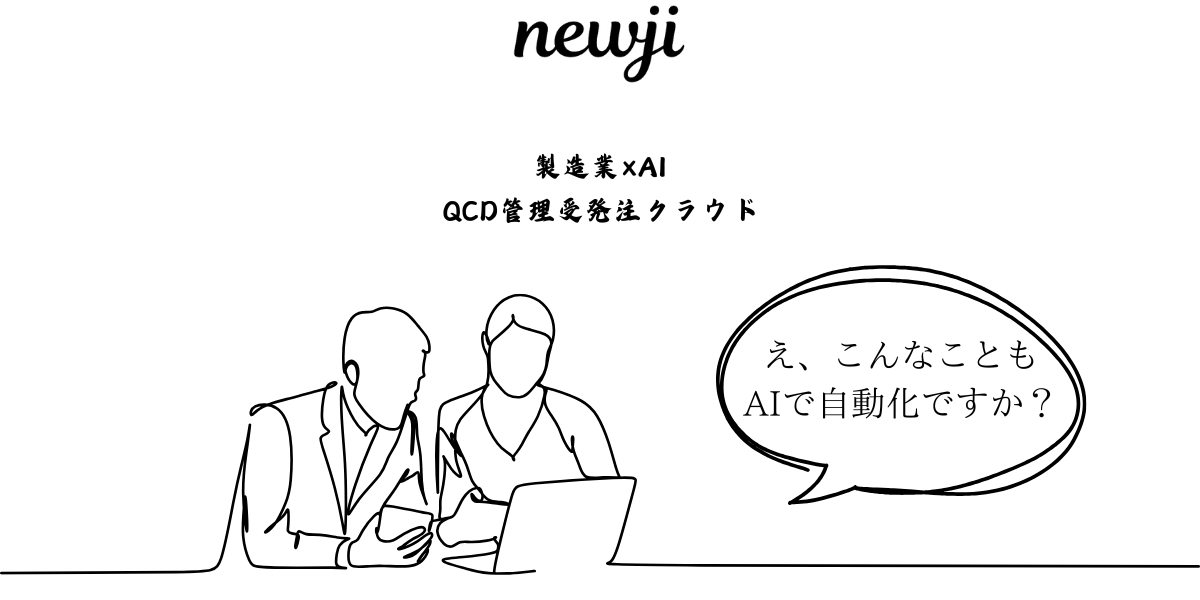
Manufacturing Process of Gas Valves and Durability Reinforcement
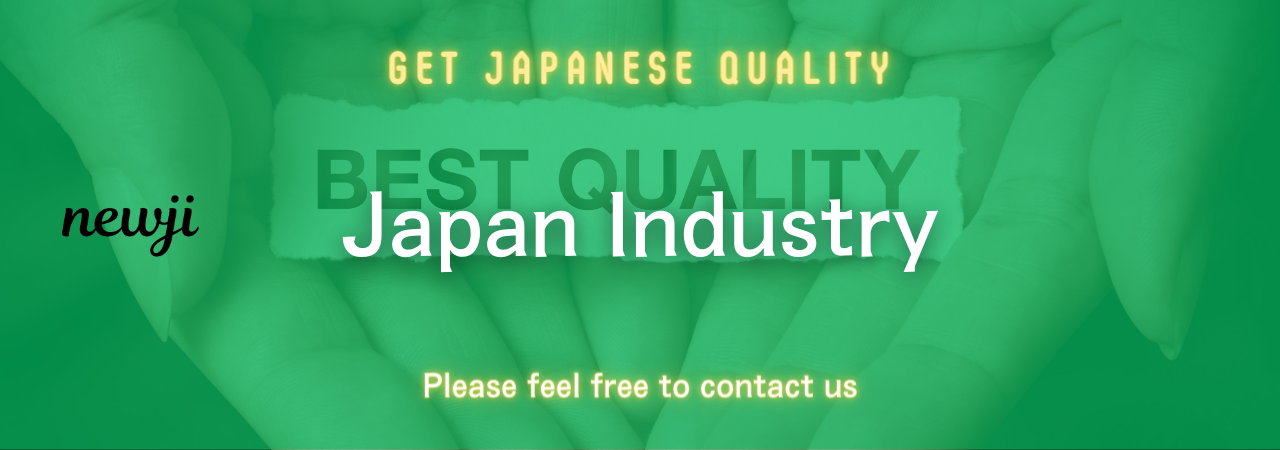
目次
Introduction to Gas Valves
Gas valves are essential components in many household and industrial applications, controlling the flow of gas to different appliances or systems.
From stoves and heaters to factories and power plants, gas valves ensure safety and efficiency.
Understanding how they are manufactured and reinforced can provide insight into their reliability and longevity.
Materials Used in Gas Valve Manufacturing
Metal Selection
The first step in manufacturing gas valves involves choosing the right materials.
Typically, metals like brass, stainless steel, and bronze are used due to their durability and resistance to corrosion.
Brass is favored for its workability and resistance to wear, while stainless steel is often selected for applications requiring higher strength and corrosion resistance.
Sealing Elements
In addition to metals, non-metallic materials are used for sealing elements.
Rubbers and elastomers are common choices, as they provide the necessary flexibility and sealing properties.
These materials undergo rigorous testing to ensure they can withstand the pressures and temperatures they will encounter.
Manufacturing Process
Casting and Forging
The manufacturing process begins with casting or forging the metal components.
Casting involves pouring molten metal into molds to form the basic shape of the valve components.
Forging, on the other hand, uses compressive forces to shape the metal into the desired form.
Both methods have their advantages, with casting being suitable for complex shapes and forging providing higher strength parts.
Machining
Once the components are formed, they undergo machining to achieve precise dimensions and surface finishes.
CNC (Computer Numerical Control) machines are commonly used for their accuracy and efficiency.
The machining process includes drilling, milling, and turning to create the necessary holes and threads for assembling the valve.
Assembly
After machining, the different parts of the valve are assembled.
The body, bonnet, actuator, and sealing elements are put together in a sequence.
Careful alignment and proper torque application during assembly are crucial to ensure the valve functions correctly and safely.
Quality Control
Testing for Leaks
Quality control is a vital part of the manufacturing process.
Each valve undergoes rigorous testing to ensure it meets safety standards.
One of the primary tests is for leaks, where the valve is subjected to pressure and checked for any escape of gas.
Durability Testing
Durability tests are also conducted to simulate the valve’s operational life.
These tests include cycling the valve open and closed multiple times to ensure the moving parts do not wear out prematurely.
High-temperature and pressure tests are also performed to gauge how the valve will perform under extreme conditions.
Durability Reinforcement Techniques
Heat Treatment
To enhance durability, various reinforcement techniques are applied.
One such technique is heat treatment, where the valve components are heated to a specific temperature and then cooled in a controlled manner.
This process increases the material’s hardness and strength, making the valve more resistant to wear and fatigue.
Coating and Plating
Another method to improve durability is coating or plating the valve components.
Common coatings include nickel and chrome, which provide additional corrosion resistance and reduce friction between moving parts.
These coatings are applied using techniques like electroplating or thermal spraying, ensuring even coverage and long-lasting protection.
Advancements in Gas Valve Technology
Smart Valves
The field of gas valve manufacturing is continually evolving, with advancements in technology offering new possibilities.
One significant development is the emergence of smart valves.
These valves come equipped with sensors and connectivity features, allowing for remote monitoring and control.
Smart valves can detect leaks or pressure changes and automatically adjust the flow, enhancing safety and efficiency.
Innovative Materials
Innovative materials are also being explored to increase durability and performance.
Researchers are investigating composite materials that combine the benefits of metals and polymers, offering lighter weight and higher strength.
These new materials could revolutionize the way gas valves are manufactured and used in the future.
Conclusion
The manufacturing process of gas valves involves careful selection of materials, precise machining, and rigorous testing to ensure safety and reliability.
Durability reinforcement techniques like heat treatment and coating further enhance the valve’s lifespan.
With advancements in smart technology and innovative materials, the future of gas valve manufacturing looks promising.
Understanding these processes helps appreciate the intricate work that goes into producing these essential components, ensuring they perform safely and efficiently in various applications.
資料ダウンロード
QCD管理受発注クラウド「newji」は、受発注部門で必要なQCD管理全てを備えた、現場特化型兼クラウド型の今世紀最高の受発注管理システムとなります。
ユーザー登録
受発注業務の効率化だけでなく、システムを導入することで、コスト削減や製品・資材のステータス可視化のほか、属人化していた受発注情報の共有化による内部不正防止や統制にも役立ちます。
NEWJI DX
製造業に特化したデジタルトランスフォーメーション(DX)の実現を目指す請負開発型のコンサルティングサービスです。AI、iPaaS、および先端の技術を駆使して、製造プロセスの効率化、業務効率化、チームワーク強化、コスト削減、品質向上を実現します。このサービスは、製造業の課題を深く理解し、それに対する最適なデジタルソリューションを提供することで、企業が持続的な成長とイノベーションを達成できるようサポートします。
製造業ニュース解説
製造業、主に購買・調達部門にお勤めの方々に向けた情報を配信しております。
新任の方やベテランの方、管理職を対象とした幅広いコンテンツをご用意しております。
お問い合わせ
コストダウンが利益に直結する術だと理解していても、なかなか前に進めることができない状況。そんな時は、newjiのコストダウン自動化機能で大きく利益貢献しよう!
(β版非公開)