- お役立ち記事
- Manufacturing Process of Head-Up Displays for Cars and Visibility Improvement
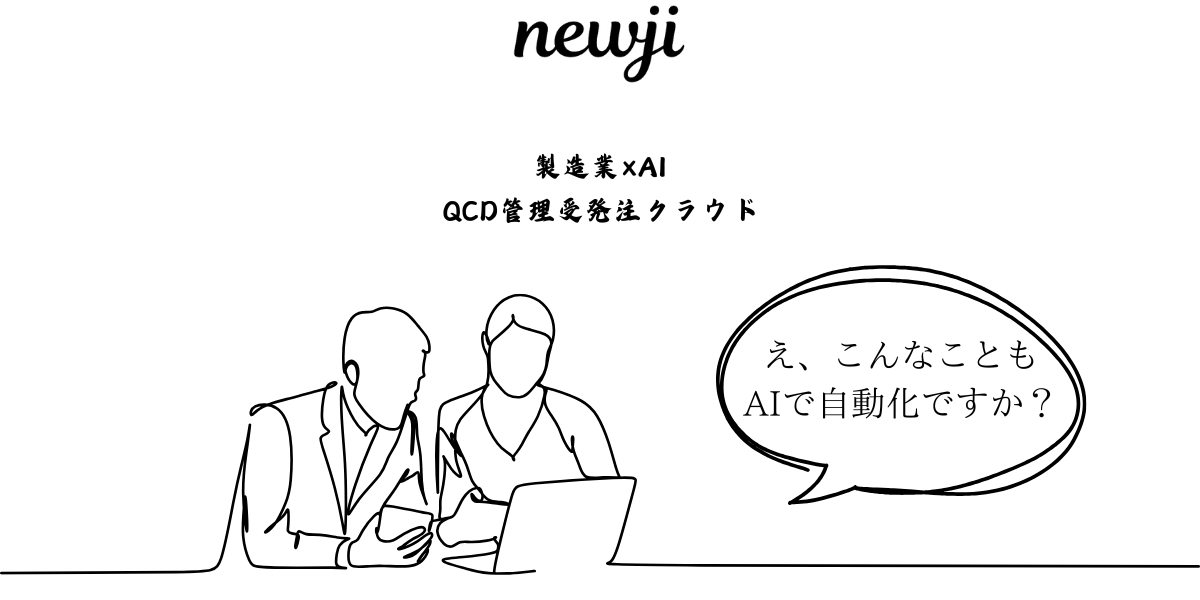
Manufacturing Process of Head-Up Displays for Cars and Visibility Improvement
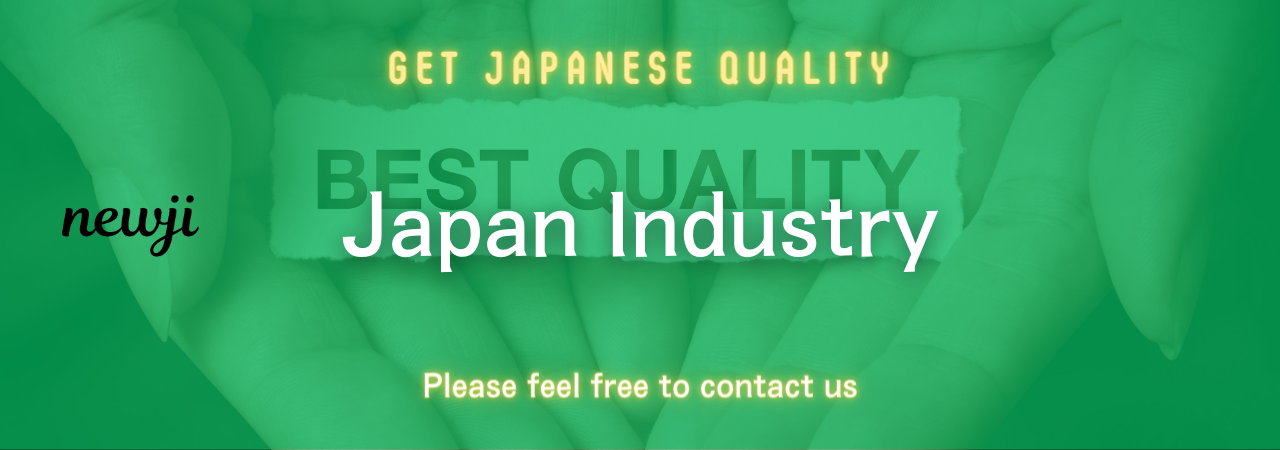
In the ever-evolving world of automotive technology, the manufacturing process of head-up displays (HUDs) plays a crucial role in enhancing driver visibility and safety.
HUDs project critical driving information onto the windshield, allowing drivers to access vital data without diverting their eyes from the road.
This technology has become increasingly popular, providing an innovative solution to improve driving experience and reducing accidents.
目次
Understanding the Basics of Head-Up Displays
To grasp the manufacturing process, it’s essential to understand the basic mechanics of head-up displays.
Primarily, HUDs consist of three key components: a projector unit, a combiner or reflector, and a control unit.
The projector emits the information onto the combiner, which then reflects it towards the driver’s line of sight.
The control unit processes the data to be displayed, ensuring accuracy and timely updates.
Manufacturing Process of HUDs
1. Design and Concept Development
The manufacturing journey begins with extensive research and development.
Designers and engineers collaborate to conceptualize the HUD, considering factors such as user interface, visibility under various lighting conditions, and integration with vehicle systems.
This stage includes Computer-Aided Design (CAD) to create detailed blueprints and simulations.
2. Material Selection
Selecting the right materials is critical for durability and performance.
High-quality, heat-resistant plastics and specially coated glass are often used for the projector lens and combiner to ensure clear visibility and resilience under extreme conditions.
The choice of materials also impacts the overall cost and weight of the HUD system.
3. Prototype Development
Once the design is finalized, the next step is to develop a prototype.
This involves crafting the initial version of the HUD using 3D printing and other rapid prototyping techniques.
Engineers test this early model rigorously to identify any design flaws or potential improvements.
Feedback from these tests informs adjustments before mass production.
4. Precision Manufacturing
With the prototype perfected, the precision manufacturing phase commences.
This stage involves the production of individual components.
For the projector unit, precision optics manufacturing techniques are utilized to create high-resolution lenses and mirrors.
The electronic components for the control unit are fabricated using advanced semiconductor manufacturing processes.
5. Assembly and Integration
In the assembly phase, all components are meticulously put together.
Robots and specialized machinery are often employed to ensure precision and consistency.
The projector, combiner, and control unit are securely housed within the HUD casing.
Once assembled, the HUD is integrated into the vehicle’s dashboard, ensuring seamless connectivity with the car’s onboard systems.
6. Quality Testing
Quality assurance is paramount in the manufacturing process.
Each HUD undergoes rigorous testing to verify its functionality, clarity, and durability.
Testing scenarios simulate diverse driving conditions, assessing the HUD’s performance in varying light and weather.
These tests help ensure that the HUD meets safety standards and company specifications.
7. Calibration
Post-assembly, the HUD system undergoes a fine-tuning process to ensure accurate display.
Calibration involves adjusting the projection angles and brightness levels to match the specific vehicle model.
Technicians use specialized equipment to align the HUD correctly, ensuring that the information is clearly visible from the driver’s perspective.
Improving Visibility with HUDs
The fundamental purpose of integrating HUDs into vehicles is to enhance visibility while driving.
Here’s how HUDs contribute to better visibility and safety:
Real-Time Information
HUDs provide real-time information such as speed, navigation directions, and collision warnings directly in the driver’s line of sight.
This eliminates the need for drivers to take their eyes off the road to glance at dashboard instruments, reducing distraction and improving reaction times.
Adaptability to Lighting Conditions
Modern HUDs are equipped with sensors that adjust the brightness and contrast of the display based on ambient lighting conditions.
Whether driving in bright sunlight or at night, the HUD optimizes visibility, ensuring that information remains clear and readable.
Augmented Reality Enhancements
Some advanced HUDs incorporate augmented reality (AR) features, overlaying navigation guides, lane markers, and hazard alerts onto the windshield.
These enhancements provide intuitive visual cues, assisting drivers in making safer driving decisions.
Conclusion
The manufacturing process of head-up displays in cars involves meticulous design, precision engineering, and rigorous testing.
From concept development to calibration, each step ensures that HUDs provide reliable and clear visibility to drivers.
As this technology continues to evolve, the integration of HUDs will play an increasingly vital role in enhancing road safety and improving the overall driving experience.
By keeping vital information in the driver’s line of sight, HUDs help create a safer and more efficient driving environment.
資料ダウンロード
QCD調達購買管理クラウド「newji」は、調達購買部門で必要なQCD管理全てを備えた、現場特化型兼クラウド型の今世紀最高の購買管理システムとなります。
ユーザー登録
調達購買業務の効率化だけでなく、システムを導入することで、コスト削減や製品・資材のステータス可視化のほか、属人化していた購買情報の共有化による内部不正防止や統制にも役立ちます。
NEWJI DX
製造業に特化したデジタルトランスフォーメーション(DX)の実現を目指す請負開発型のコンサルティングサービスです。AI、iPaaS、および先端の技術を駆使して、製造プロセスの効率化、業務効率化、チームワーク強化、コスト削減、品質向上を実現します。このサービスは、製造業の課題を深く理解し、それに対する最適なデジタルソリューションを提供することで、企業が持続的な成長とイノベーションを達成できるようサポートします。
オンライン講座
製造業、主に購買・調達部門にお勤めの方々に向けた情報を配信しております。
新任の方やベテランの方、管理職を対象とした幅広いコンテンツをご用意しております。
お問い合わせ
コストダウンが利益に直結する術だと理解していても、なかなか前に進めることができない状況。そんな時は、newjiのコストダウン自動化機能で大きく利益貢献しよう!
(Β版非公開)