- お役立ち記事
- Manufacturing process of heat-dissipating composite materials using rotating electrode electric field alignment technology
月間77,185名の
製造業ご担当者様が閲覧しています*
*2025年2月28日現在のGoogle Analyticsのデータより
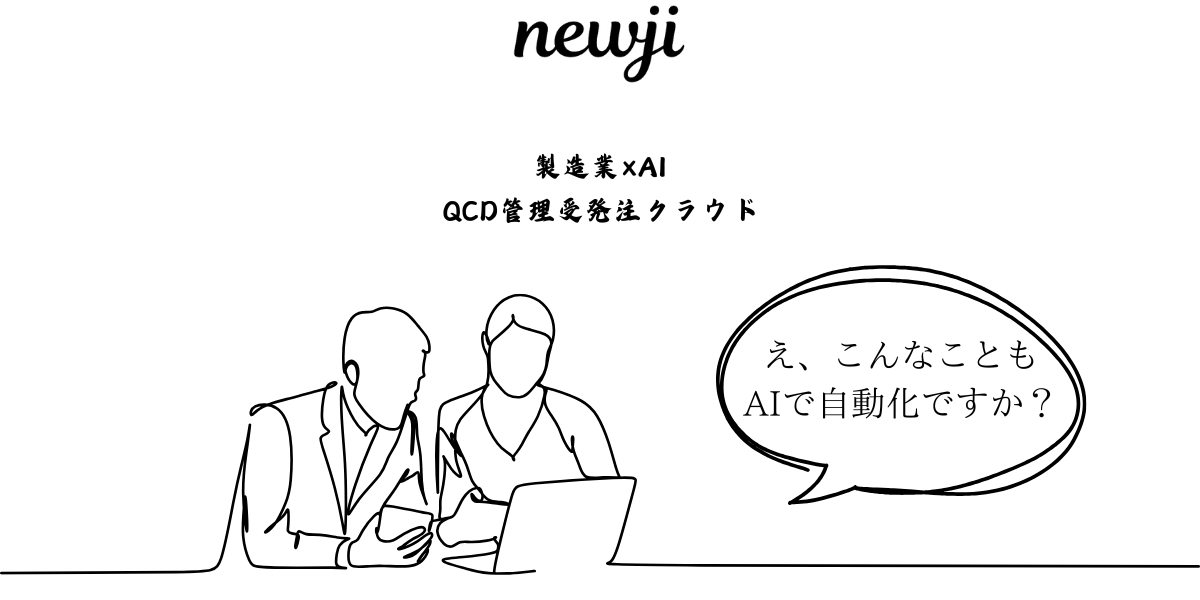
Manufacturing process of heat-dissipating composite materials using rotating electrode electric field alignment technology
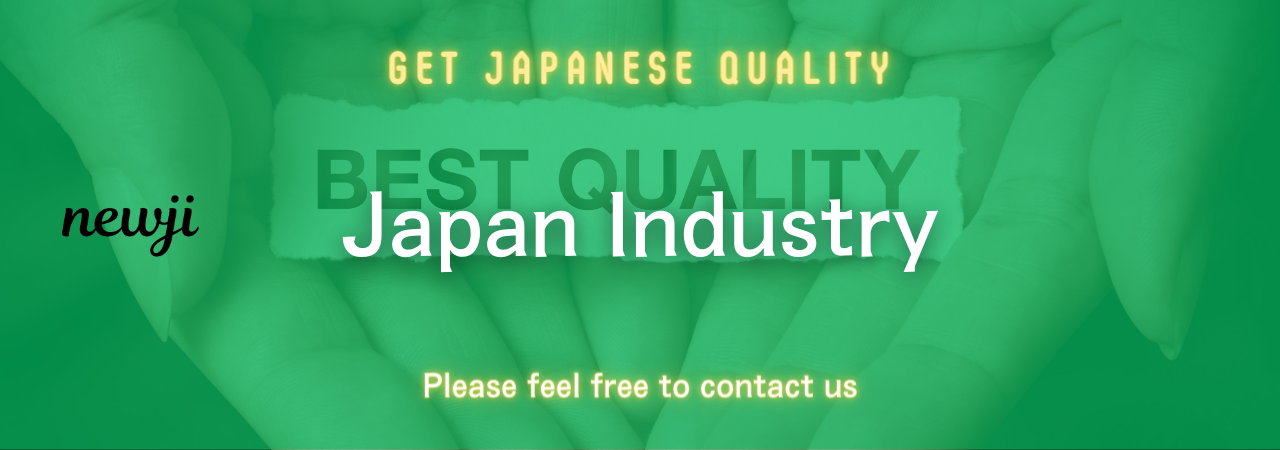
目次
Introduction to Heat-Dissipating Composite Materials
Heat-dissipating composite materials are crucial in modern technology, ensuring electronic devices operate efficiently without overheating.
These materials assist in spreading heat away from essential components, enhancing performance and longevity.
As the demand for high-efficiency electronic components increases, the development of advanced heat-dissipating materials becomes essential.
A breakthrough in this field involves using rotating electrode electric field alignment technology.
This innovative approach optimizes the structure and properties of composite materials, facilitating better thermal management solutions.
Understanding Rotating Electrode Electric Field Alignment
Rotating electrode electric field alignment technology is a cutting-edge technique employed to align fibers within a composite material.
This method enhances thermal conductivity by ensuring a uniform distribution of particles throughout the composite matrix.
By applying an electric field, this technique orients the filler particles along the direction of the electric field.
Simultaneously, electrodes rotate to fine-tune the alignment process, resulting in more efficient heat dissipation pathways.
This precise control over particle orientation significantly improves the thermal conductivity of the composite material.
Steps in the Manufacturing Process
Preparation of Raw Materials
The manufacturing process begins with selecting appropriate raw materials, including polymers and conductive fillers like graphite or carbon nanotubes.
These materials are chosen based on their thermal conductive properties and compatibility with electronic applications.
The fillers are first processed to achieve the required size and shape, ensuring they are suitable for alignment during the manufacturing process.
Mixing and Dispersion of Fillers
Once the raw materials are prepared, they undergo a mixing process to uniformly distribute the fillers within the polymer matrix.
Advanced mixing techniques ensure even dispersion, which is vital for effective alignment later.
High-shear mixers and ultrasonic techniques are often used to break agglomerates and achieve a homogeneous mixture.
The presence of uniformly dispersed fillers aids in the subsequent alignment process, maximizing thermal conductivity.
Application of Rotating Electrode Electric Field
With the mixture ready, it’s subjected to a rotating electrode setup where an electric field is applied.
Electrodes generate the field, and by rotating, they bring about a dynamic alignment process.
This alignment process orients the fillers parallel to the electric field, resulting in continuous networks for heat conduction.
The rotation of electrodes ensures even distribution and maximizes coverage of the composite, enhancing thermal pathways.
Curing and Solidification
After alignment, the composite is cured using heat or other chemical processes to solidify the structure.
This step ensures the material retains its aligned configuration, locking particles in place for optimal heat dissipation.
The curing process tailors the mechanical properties of the composite, making it suitable for integration into electronic devices.
Quality Control and Testing
Manufacturers conduct extensive quality control tests to ensure the final product meets the required thermal and mechanical standards.
Testing for thermal conductivity, mechanical strength, and electrical insulative properties is crucial before the material is incorporated into electronic systems.
Advanced analytical methods, such as scanning electron microscopy and thermal imaging, are employed to verify the structural integrity and functionality of the composite materials.
Advantages of Using This Technology
One of the main advantages of this technology is the enhanced thermal conductivity of the composite materials.
By ensuring a continuous thermal path, the heat dissipation improves significantly, allowing electronic components to operate at optimal temperature ranges.
Additionally, this technique provides more control over the microstructure of the composite materials, enabling customization for specific applications.
Manufacturers can tailor the properties of the material to suit different industries, from consumer electronics to automotive applications.
Moreover, the use of rotating electrodes enhances the efficiency of the alignment process, reducing material waste and ensuring consistent quality.
This approach also offers scalability, making it feasible for large-scale manufacturing processes.
Applications of Aligned Composite Materials
Aligned heat-dissipating composite materials find applications in various industries where thermal management is critical.
Consumer Electronics
In consumer electronics, such materials are essential for cooling high-performance processors and GPUs.
They ensure devices like smartphones, laptops, and tablets operate smoothly without overheating, even during extensive usage.
Automotive Industry
In the automotive sector, these composites are used in electric vehicle batteries and power electronics systems.
Efficient thermal management solutions enhance battery life and performance, crucial for the development of reliable electric vehicles.
Telecommunications
Telecommunications equipment, such as base stations and data centers, benefits from enhanced heat dissipation materials.
These composites help in managing the heat generated by high-capacity data transfer processes.
Future Prospects and Challenges
The future of heat-dissipating composite materials using rotating electrode electric field alignment technology holds promise for the electronics industry.
Continued research and development aim to enhance the efficiency and reliability of these materials.
However, challenges remain, particularly concerning the cost-effectiveness and complexity of the manufacturing process.
Overcoming these challenges requires innovations in electrode design and material processing techniques.
Ultimately, as technology evolves, the demand for more advanced heat-dissipating solutions will grow, driving further advancements in this field.
By continuing to refine these techniques, manufacturers can produce highly efficient, customizable composite materials that meet the demands of future electronic systems.
資料ダウンロード
QCD管理受発注クラウド「newji」は、受発注部門で必要なQCD管理全てを備えた、現場特化型兼クラウド型の今世紀最高の受発注管理システムとなります。
ユーザー登録
受発注業務の効率化だけでなく、システムを導入することで、コスト削減や製品・資材のステータス可視化のほか、属人化していた受発注情報の共有化による内部不正防止や統制にも役立ちます。
NEWJI DX
製造業に特化したデジタルトランスフォーメーション(DX)の実現を目指す請負開発型のコンサルティングサービスです。AI、iPaaS、および先端の技術を駆使して、製造プロセスの効率化、業務効率化、チームワーク強化、コスト削減、品質向上を実現します。このサービスは、製造業の課題を深く理解し、それに対する最適なデジタルソリューションを提供することで、企業が持続的な成長とイノベーションを達成できるようサポートします。
製造業ニュース解説
製造業、主に購買・調達部門にお勤めの方々に向けた情報を配信しております。
新任の方やベテランの方、管理職を対象とした幅広いコンテンツをご用意しております。
お問い合わせ
コストダウンが利益に直結する術だと理解していても、なかなか前に進めることができない状況。そんな時は、newjiのコストダウン自動化機能で大きく利益貢献しよう!
(β版非公開)