- お役立ち記事
- Manufacturing Process of Heat Exchange Fins and Durability Improvement
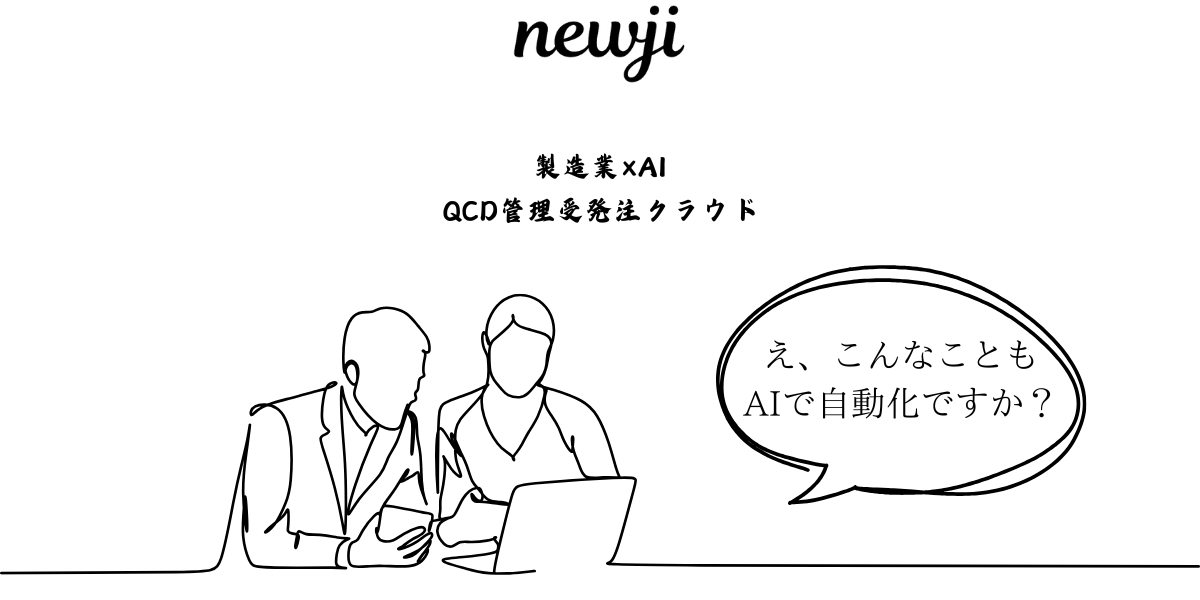
Manufacturing Process of Heat Exchange Fins and Durability Improvement
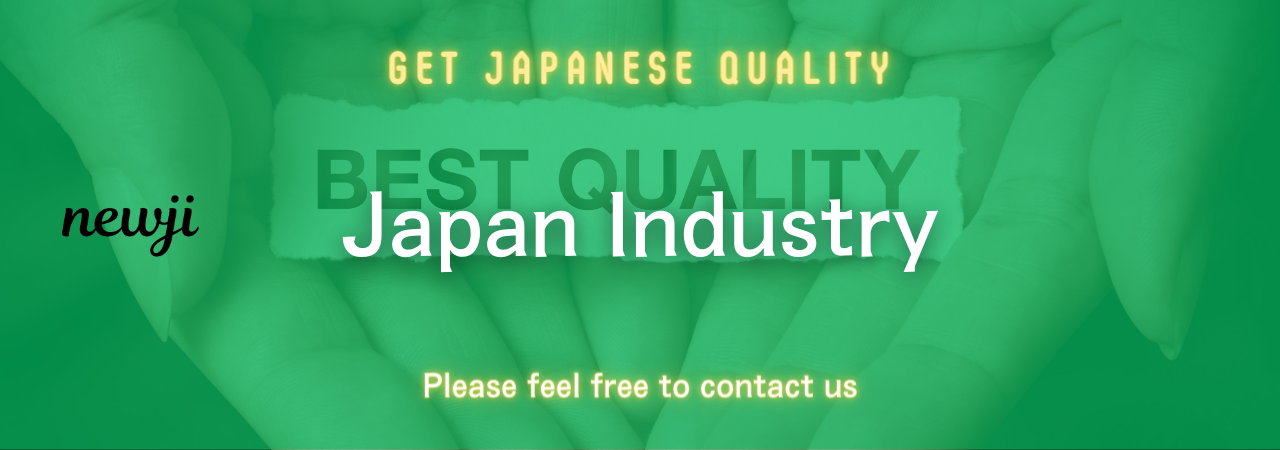
Heat exchange fins are critical components in systems designed to transfer heat efficiently.
They are used in various applications, including air conditioners, refrigerators, radiators, and industrial heat exchangers.
The manufacturing process of these fins and the measures taken to improve their durability play a crucial role in their performance and lifespan.
目次
The Importance of Heat Exchange Fins
Heat exchange fins increase the surface area available for heat transfer, allowing heat to be dissipated more efficiently.
This results in enhanced thermal performance and energy efficiency.
Without these fins, devices would have to work much harder to achieve the same cooling or heating effect, leading to higher energy consumption and operational costs.
Therefore, understanding the manufacturing process and durability improvement strategies for heat exchange fins is essential for developing more efficient thermal management systems.
Manufacturing Process of Heat Exchange Fins
The manufacturing process of heat exchange fins involves several steps, each critical to ensuring the final product’s efficiency and durability.
Material Selection
The first step in the manufacturing process is selecting the appropriate material for the fins.
Common materials include aluminum, copper, and stainless steel.
Aluminum is often preferred due to its excellent thermal conductivity, lightweight nature, and cost-effectiveness.
Copper, while more expensive, offers superior thermal conductivity and corrosion resistance.
Stainless steel is used when durability and corrosion resistance are paramount, such as in industrial applications.
Fin Design
The design of the fins is another critical aspect that affects their performance.
Fins can be manufactured in various shapes, including flat, wavy, louvered, or even serrated styles.
Each design offers different advantages regarding airflow, thermal efficiency, and manufacturing ease.
The choice of design depends on the specific application and performance requirements.
Stamping or Extrusion
Once the material and design are finalized, the next step is to shape the fins.
This can be done through stamping or extrusion methods.
Stamping involves using a die to cut and shape the fins from a metal sheet.
This method is efficient and cost-effective for producing high volumes of fins with consistent quality.
On the other hand, extrusion involves forcing the metal through a die to create long, continuous fins with complex shapes.
Extruded fins can offer better performance due to their superior structural integrity and precise geometry.
However, this method tends to be more expensive and is typically used for specialized applications.
Surface Treatment
After shaping, the fins undergo surface treatment to enhance their performance and durability.
Common treatments include anodizing, electroplating, or applying a protective coating.
Anodizing increases the thickness of the natural oxide layer on the aluminum fins, improving corrosion resistance and durability.
Electroplating can add a layer of another metal, such as zinc or nickel, to improve corrosion resistance and conductivity.
Protective coatings can offer additional protection against corrosion, fouling, and wear.
Fin Assembly
The final step in the manufacturing process is assembling the fins into the heat exchange unit.
This can involve soldering, brazing, or mechanical assembly methods.
The choice of assembly method depends on the fin material, design, and application requirements.
Proper assembly is crucial to ensure that the fins maintain optimal thermal performance and structural integrity.
Improving Durability of Heat Exchange Fins
Improving the durability of heat exchange fins is essential to ensure that they perform efficiently over a long period.
Several strategies can be employed to enhance the durability of heat exchange fins.
Material Selection and Treatment
Choosing the right material and surface treatment is critical to improving the durability of heat exchange fins.
Materials with better corrosion resistance, such as copper or stainless steel, can significantly extend the lifespan of the fins.
Surface treatments, such as anodizing or electroplating, can also enhance durability by providing an additional layer of protection against environmental factors.
Corrosion Inhibitors
Applying corrosion inhibitors can further protect the fins from degradation due to exposure to moisture, chemicals, and other corrosive elements.
These inhibitors can be applied during the manufacturing process or as part of regular maintenance.
Protective Coatings
Advanced protective coatings can provide a barrier against corrosion and wear, enhancing the durability of the fins.
These coatings are designed to withstand harsh environments and maintain their protective properties over time.
Examples include epoxy-based coatings, polyurethane coatings, and ceramic coatings.
Regular Maintenance
Regular maintenance is essential to ensure the longevity of heat exchange fins.
This includes cleaning the fins to remove dirt, debris, and corrosive contaminants that can accumulate over time.
Periodic inspections can help identify signs of wear or damage and allow for timely repairs or replacements.
Optimized Design
Optimizing the design of the fins can also contribute to their durability.
This can involve using thicker materials, reinforcing critical areas, or incorporating features that reduce stress and wear.
Advanced simulation tools can be used to analyze the performance of different designs and identify the best options for enhancing durability.
Conclusion
The manufacturing process of heat exchange fins and the strategies employed to improve their durability play a vital role in the efficiency and lifespan of heat transfer systems.
Careful selection of materials, precise shaping, and proper surface treatments are crucial to producing high-quality fins.
Additionally, incorporating corrosion inhibitors, protective coatings, regular maintenance, and optimized designs can significantly enhance the durability of these essential components.
By understanding these processes and applying the best practices, manufacturers can produce heat exchange fins that deliver optimal performance and longevity, ultimately contributing to more efficient and cost-effective thermal management solutions.
資料ダウンロード
QCD調達購買管理クラウド「newji」は、調達購買部門で必要なQCD管理全てを備えた、現場特化型兼クラウド型の今世紀最高の購買管理システムとなります。
ユーザー登録
調達購買業務の効率化だけでなく、システムを導入することで、コスト削減や製品・資材のステータス可視化のほか、属人化していた購買情報の共有化による内部不正防止や統制にも役立ちます。
NEWJI DX
製造業に特化したデジタルトランスフォーメーション(DX)の実現を目指す請負開発型のコンサルティングサービスです。AI、iPaaS、および先端の技術を駆使して、製造プロセスの効率化、業務効率化、チームワーク強化、コスト削減、品質向上を実現します。このサービスは、製造業の課題を深く理解し、それに対する最適なデジタルソリューションを提供することで、企業が持続的な成長とイノベーションを達成できるようサポートします。
オンライン講座
製造業、主に購買・調達部門にお勤めの方々に向けた情報を配信しております。
新任の方やベテランの方、管理職を対象とした幅広いコンテンツをご用意しております。
お問い合わせ
コストダウンが利益に直結する術だと理解していても、なかなか前に進めることができない状況。そんな時は、newjiのコストダウン自動化機能で大きく利益貢献しよう!
(Β版非公開)