- お役立ち記事
- Manufacturing Process of Heat Exchangers and Thermal Efficiency Improvement
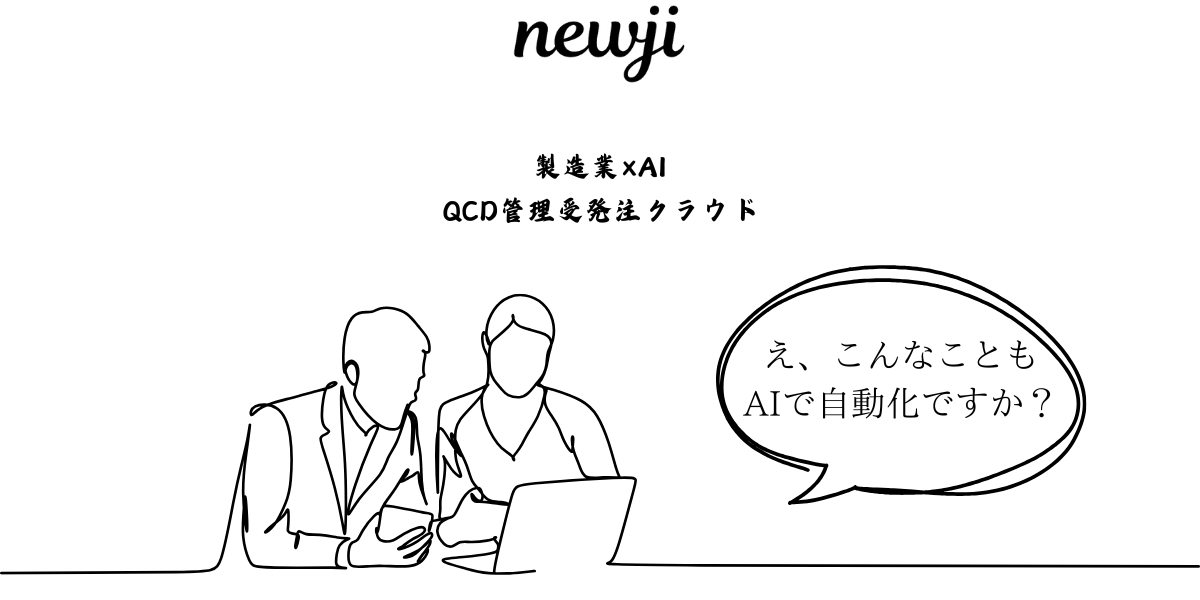
Manufacturing Process of Heat Exchangers and Thermal Efficiency Improvement
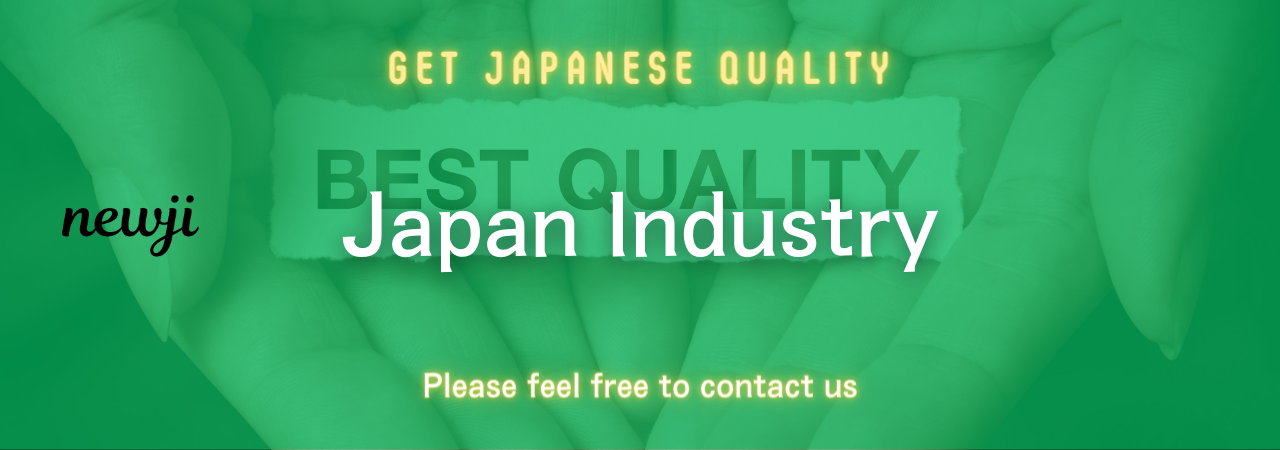
Heat exchangers are vital components in various industries, from power generation to HVAC systems, and automotive to chemical processing.
Understanding their manufacturing process and how to improve their thermal efficiency is key to optimizing performance and costs.
In this article, we will explore the manufacturing process of heat exchangers and discuss methods to enhance their thermal efficiency.
目次
Introduction to Heat Exchangers
Heat exchangers are devices used to transfer heat between two or more fluids without mixing them.
They are commonly used in heating, cooling, and energy recovery applications.
Their importance lies in their ability to improve energy efficiency and help manage temperatures in various systems and processes.
Materials and Types of Heat Exchangers
Common Materials Used
The choice of material for a heat exchanger depends on the working environment, temperature, pressure, and type of fluids involved.
Common materials include:
– Stainless Steel: Offers excellent corrosion resistance and durability, ideal for high-temperature and pressure applications.
– Copper: Known for its high thermal conductivity and ease of fabrication, suitable for applications requiring efficient heat transfer.
– Aluminum: Lightweight and cost-effective, often used in automotive and HVAC systems.
– Titanium: Highly resistant to corrosion, especially in seawater applications.
Types of Heat Exchangers
There are several types of heat exchangers, each designed for specific applications:
– **Shell and Tube Heat Exchangers:** Consist of a series of tubes enclosed within a cylindrical shell. These are suitable for high-pressure applications and large-scale industrial use.
– **Plate Heat Exchangers:** Comprised of multiple thin, corrugated plates stacked together. They offer a high surface area for heat transfer and are compact, making them ideal for HVAC and refrigeration systems.
– **Air Cooled Heat Exchangers:** Use air to cool fluids, eliminating the need for a cooling medium. These are commonly used in power plants and petrochemical industries.
– **Double Pipe Heat Exchangers:** Feature two concentric pipes, one inside the other. They are simple in design and used for smaller-scale applications or where space is limited.
Manufacturing Process of Heat Exchangers
Design and Engineering
The manufacturing process begins with the design phase.
Engineers use computer-aided design (CAD) software to create detailed blueprints.
They consider factors such as fluid properties, flow rates, temperatures, pressures, and the thermal conductivity of materials.
Material Selection and Procurement
Once the design is finalized, the materials required are selected and procured.
This includes ordering metal sheets, tubes, plates, or other components based on the specific type of heat exchanger being manufactured.
Forming and Shaping
The next step involves forming and shaping the raw materials into the required components.
For shell and tube heat exchangers, this might include fabricating the shell and tubes through processes like cutting, bending, and welding.
In plate heat exchangers, metal sheets are pressed into thin, corrugated plates using hydraulic presses.
Assembly
The formed and shaped components are then assembled according to the design specifications.
For shell and tube heat exchangers, tubes are placed inside the shell and fastened securely.
In plate heat exchangers, plates are stacked and clamped together in a specific sequence.
Welding and Brazing
Welding and brazing are critical steps to ensure a leak-proof assembly.
Tubes, shells, and plates are often welded or brazed together at joints to provide a stable and durable structure.
This process requires skilled technicians to ensure precision and compliance with safety standards.
Quality Control and Testing
After assembly, heat exchangers undergo stringent quality control and testing.
This includes pressure testing to detect any leaks, thermal performance testing to ensure efficient heat transfer, and inspections for any manufacturing defects.
Non-destructive testing methods such as X-ray or ultrasonic testing may also be employed.
Improving Thermal Efficiency
Optimized Design
One of the most effective ways to improve thermal efficiency is through optimized design.
This entails calculating the ideal surface area, fluid flow paths, and compactness to maximize heat transfer while minimizing pressure drop.
Advanced simulation tools can help engineers model and predict the performance of the heat exchanger.
Enhanced Surface Treatments
Surface treatments such as fins, coatings, or micro-structuring can significantly increase the heat transfer surface area.
Fins are added to the exterior of tubes or plates to create additional surface for heat exchange.
Special coatings can enhance surface wettability, improving the heat transfer rate.
High-Efficiency Materials
Using materials with higher thermal conductivity can directly enhance the performance of heat exchangers.
For instance, incorporating copper or aluminum fins can improve thermal efficiency due to their superior heat transfer properties.
Minimizing Fouling
Fouling, which refers to the accumulation of deposits on heat exchanger surfaces, can impede heat transfer and reduce efficiency.
Regular maintenance, the use of anti-fouling coatings, or choosing materials less susceptible to fouling can help maintain optimal performance.
Advanced Manufacturing Techniques
Employing advanced manufacturing techniques such as additive manufacturing (3D printing) can lead to more efficient heat exchanger designs.
Additive manufacturing allows for complex geometries that traditional methods cannot achieve, leading to optimized fluid flow and heat transfer.
Conclusion
The manufacturing process of heat exchangers is a complex but crucial aspect of various industries.
From material selection to forming, welding, and quality testing, each step ensures the final product is efficient and reliable.
Improving thermal efficiency involves optimized design, enhanced surface treatments, high-efficiency materials, minimizing fouling, and adopting advanced manufacturing techniques.
As technology continues to evolve, the future of heat exchangers promises even greater efficiency and cost-effectiveness, contributing significantly to energy conservation and industrial progress.
資料ダウンロード
QCD調達購買管理クラウド「newji」は、調達購買部門で必要なQCD管理全てを備えた、現場特化型兼クラウド型の今世紀最高の購買管理システムとなります。
ユーザー登録
調達購買業務の効率化だけでなく、システムを導入することで、コスト削減や製品・資材のステータス可視化のほか、属人化していた購買情報の共有化による内部不正防止や統制にも役立ちます。
NEWJI DX
製造業に特化したデジタルトランスフォーメーション(DX)の実現を目指す請負開発型のコンサルティングサービスです。AI、iPaaS、および先端の技術を駆使して、製造プロセスの効率化、業務効率化、チームワーク強化、コスト削減、品質向上を実現します。このサービスは、製造業の課題を深く理解し、それに対する最適なデジタルソリューションを提供することで、企業が持続的な成長とイノベーションを達成できるようサポートします。
オンライン講座
製造業、主に購買・調達部門にお勤めの方々に向けた情報を配信しております。
新任の方やベテランの方、管理職を対象とした幅広いコンテンツをご用意しております。
お問い合わせ
コストダウンが利益に直結する術だと理解していても、なかなか前に進めることができない状況。そんな時は、newjiのコストダウン自動化機能で大きく利益貢献しよう!
(Β版非公開)