- お役立ち記事
- Manufacturing Process of Ignition Units and Ignition Performance Enhancement
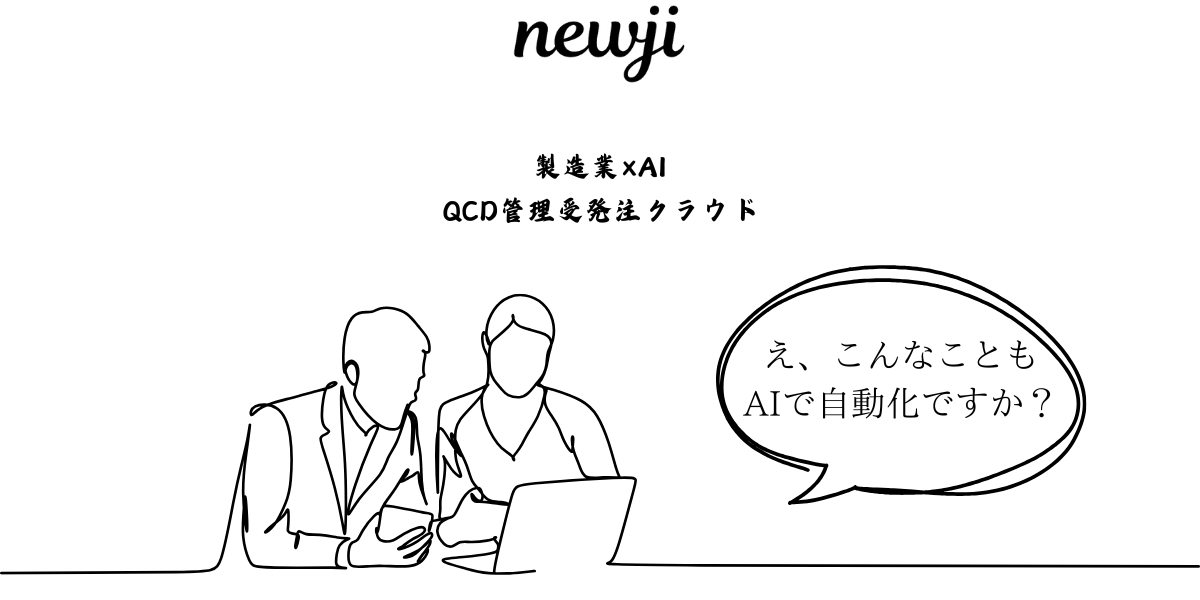
Manufacturing Process of Ignition Units and Ignition Performance Enhancement
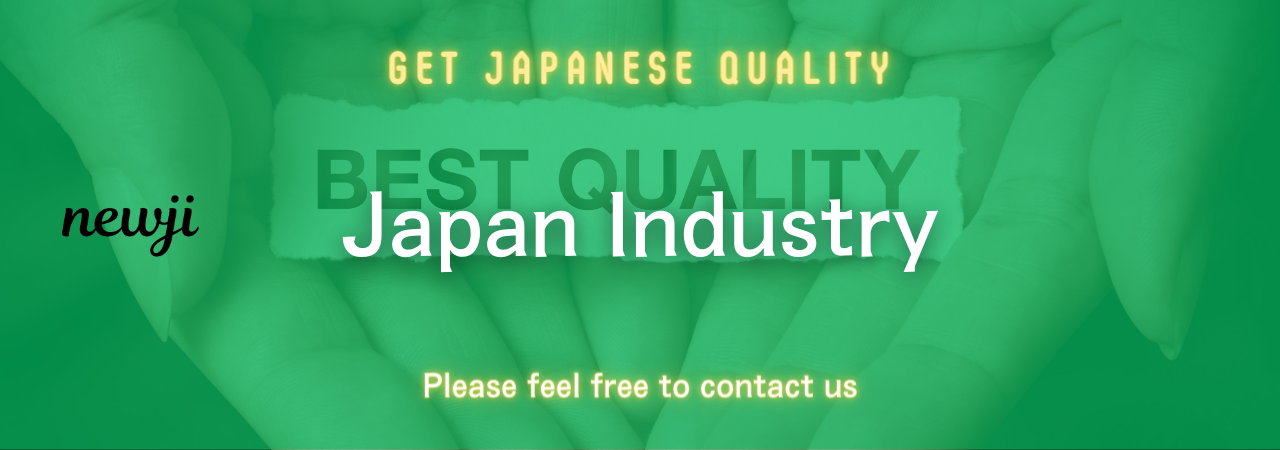
目次
Understanding Ignition Units
Ignition units are essential components in many modern engines.
They play a critical role in ensuring the proper combustion of fuel, which powers various machinery and vehicles.
In essence, ignition units help to initiate the combustion process by generating a spark that ignites the fuel mixture.
The Basic Principle of Ignition
Before diving into the manufacturing process, it’s essential to understand how ignition units work.
When the engine is running, the ignition unit sends an electric spark at the right moment to ignite the air-fuel mixture in the engine’s combustion chamber.
This controlled explosion generates power, which is transferred to the engine’s mechanical systems, driving the vehicle or machinery.
Components of an Ignition Unit
An ignition unit comprises several critical components that work together to produce that vital spark.
These components include the ignition coil, spark plugs, distributor, and control module.
Ignition Coil
The ignition coil is responsible for transforming the low voltage from the battery into the high voltage required to create an electric spark.
Spark Plugs
Spark plugs transfer the high voltage from the ignition coil to the combustion chamber, where they generate the spark.
Distributor
The distributor directs the high voltage from the ignition coil to the correct cylinder in the engine via the spark plug leads.
Control Module
The control module monitors various engine parameters and ensures the spark is delivered at the optimum moment for efficient combustion.
The Manufacturing Process
Ignition units undergo a precise and detailed manufacturing process to ensure they function correctly and reliably.
Design and Engineering
The manufacturing process begins with the design and engineering phase.
In this phase, engineers create detailed blueprints and specifications for the ignition unit’s components.
Advanced computer-aided design (CAD) software is often used to create highly accurate designs.
These designs must meet strict industry standards to ensure the ignition units will function properly under various conditions.
Material Selection
Choosing the right materials is crucial for producing high-quality ignition units.
Manufacturers select materials that can withstand high temperatures and pressures while providing excellent electrical conductivity and durability.
Common materials used in ignition units include copper for the wiring, porcelain for the spark plug insulators, and high-strength alloys for the electrodes.
Component Manufacturing
Once materials are selected, the next step is to manufacture individual components.
Each part, from the ignition coil to the spark plugs, is produced using specialized machinery and techniques.
Ignition Coil Manufacturing
The ignition coil consists of two windings – primary and secondary – made from copper wire.
The primary winding has a few turns of thicker wire, whereas the secondary winding has thousands of turns of thinner wire.
These windings are wrapped around a magnetic core and then encapsulated in an insulating material to prevent electrical short circuits.
Spark Plug Manufacturing
Spark plug production involves creating the central electrode, the insulator, and the outer shell.
The central electrode is made from high-strength alloys, while the insulator is typically made from porcelain.
These components are assembled, and the completed spark plug undergoes rigorous testing to ensure it meets performance standards.
Assembly
After individual components are manufactured, assembly of the ignition unit begins.
This stage involves putting together the ignition coil, spark plugs, distributor, and control module into a single, functioning unit.
The assembly process often combines automated systems and skilled human labor to ensure precision and quality.
During assembly, all connections are securely fastened, and components are aligned to prevent any malfunction.
Quality Control and Testing
Quality control is a critical part of the manufacturing process.
Ignition units undergo extensive testing to ensure they meet all performance and safety standards.
Tests may include electrical conductivity checks, thermal stability assessments, and physical inspections.
Any unit that fails to meet the required standards is discarded or sent back for reworking.
Packaging and Distribution
After passing quality control, ignition units are packaged securely to prevent damage during transport.
Labels with important information, such as part numbers and manufacturing dates, are affixed to each unit.
The packaged units are then shipped to distributors, retailers, or directly to consumers.
Enhancing Ignition Performance
High-performance ignition units can significantly improve an engine’s efficiency, power, and durability.
Several strategies can be used to enhance ignition performance.
High-Energy Ignition Systems
High-energy ignition systems produce stronger sparks, leading to more complete combustion of the air-fuel mixture.
This can result in better fuel economy, higher power output, and lower emissions.
Upgrading to a high-energy ignition system often involves replacing standard ignition components with higher-quality parts designed to handle increased electrical loads.
Optimized Timing
Proper timing ensures the spark occurs at the optimal moment in the engine’s cycle.
Modern ignition units often include advanced timing control systems that adjust the spark timing based on engine speed, load, and other factors.
Optimized timing can lead to smoother engine operation, increased power, and improved fuel efficiency.
Regular Maintenance
Regular maintenance is crucial for ensuring consistent ignition performance.
This includes regularly inspecting and replacing spark plugs, ignition coils, and other components prone to wear and tear.
Using high-quality replacement parts and following the manufacturer’s recommended maintenance schedule can extend the life of an ignition unit and maintain peak performance.
Using High-Quality Fuel
The type of fuel used can also impact ignition performance.
High-quality fuels with proper additives can promote cleaner combustion and reduce the buildup of deposits on ignition components.
Cleaner combustion leads to more efficient power generation and reduced emissions.
Conclusion
Ignition units are vital for the reliable operation of engines, and their manufacturing process involves meticulous design, precise material selection, and rigorous testing.
Enhancing ignition performance through high-energy ignition systems, optimized timing, regular maintenance, and high-quality fuel can significantly improve an engine’s efficiency, power, and longevity.
Understanding these aspects can help consumers and professionals make informed decisions about ignition systems and their role in engine performance.
資料ダウンロード
QCD調達購買管理クラウド「newji」は、調達購買部門で必要なQCD管理全てを備えた、現場特化型兼クラウド型の今世紀最高の購買管理システムとなります。
ユーザー登録
調達購買業務の効率化だけでなく、システムを導入することで、コスト削減や製品・資材のステータス可視化のほか、属人化していた購買情報の共有化による内部不正防止や統制にも役立ちます。
NEWJI DX
製造業に特化したデジタルトランスフォーメーション(DX)の実現を目指す請負開発型のコンサルティングサービスです。AI、iPaaS、および先端の技術を駆使して、製造プロセスの効率化、業務効率化、チームワーク強化、コスト削減、品質向上を実現します。このサービスは、製造業の課題を深く理解し、それに対する最適なデジタルソリューションを提供することで、企業が持続的な成長とイノベーションを達成できるようサポートします。
オンライン講座
製造業、主に購買・調達部門にお勤めの方々に向けた情報を配信しております。
新任の方やベテランの方、管理職を対象とした幅広いコンテンツをご用意しております。
お問い合わせ
コストダウンが利益に直結する術だと理解していても、なかなか前に進めることができない状況。そんな時は、newjiのコストダウン自動化機能で大きく利益貢献しよう!
(Β版非公開)