- お役立ち記事
- Manufacturing Process of In-Car Mobile Chargers and Safety Feature Reinforcement
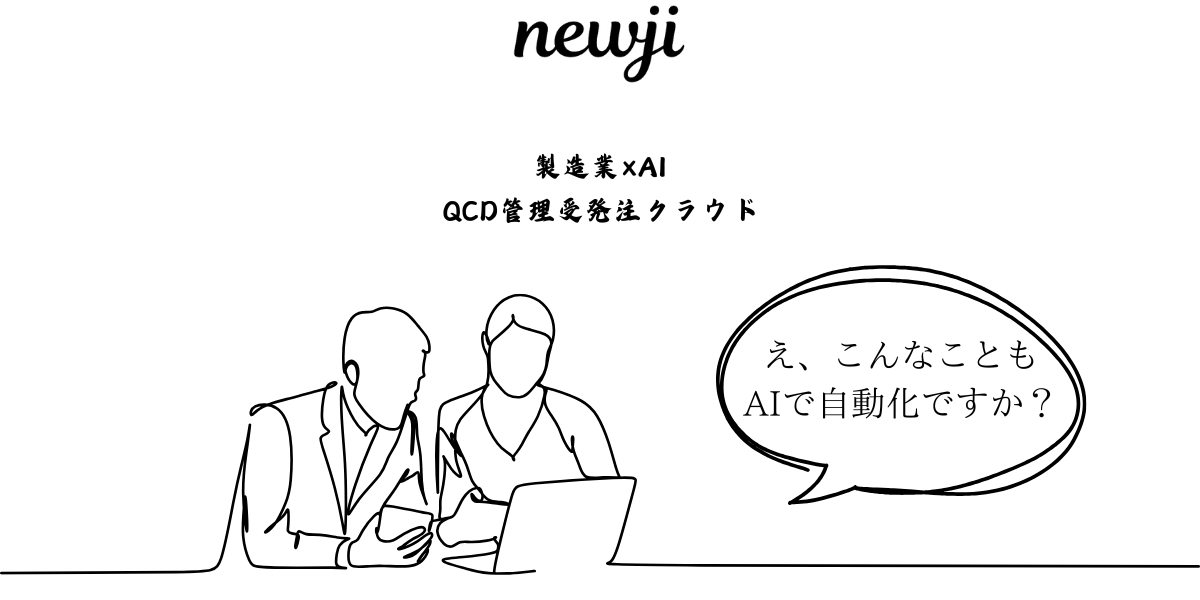
Manufacturing Process of In-Car Mobile Chargers and Safety Feature Reinforcement
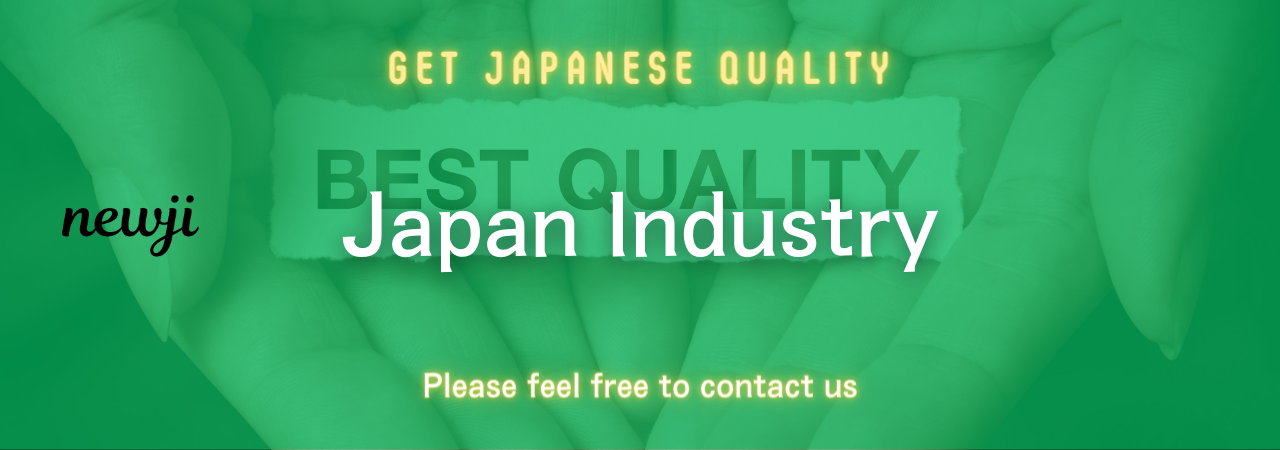
In-car mobile chargers have become essential accessories in today’s world where we depend heavily on our electronic devices.
Understanding how these chargers are made and the safety features they include can help consumers make informed decisions.
Here’s a detailed look into the manufacturing process and the safety reinforcements deployed in these devices.
目次
Raw Material Selection
The production of in-car mobile chargers begins with the selection of raw materials.
Key components include plastic for the outer casing, metals for connectors, electronic chips, and wiring for internal circuit structures.
These materials must meet high quality and heat resistance standards to ensure durability and efficiency.
Molding and Casing Creation
Next, the plastic material is melted and injected into molds to create the outer casing of the charger.
This process, known as injection molding, ensures that the casing is sturdy and can withstand regular use.
Once molded, the casings undergo a cooling phase to solidify and take shape.
Component Assembly
The internal components of the charger are then assembled.
This stage involves soldering electronic parts, such as resistors, capacitors, and integrated circuits, onto a printed circuit board (PCB).
Connectors, usually made of metal such as brass or stainless steel, are then attached to the PCB.
These connectors link the charger to the car’s power outlet and the mobile device.
Usage of Smart Chips
Modern in-car chargers often include smart chips that regulate voltage and current output.
These chips are crucial for protecting both the charger and the connected mobile device from electrical damage.
They ensure the device is charged efficiently while preventing overcharging, overheating, and short-circuiting.
Quality Control and Testing
Once assembled, the chargers undergo rigorous testing.
Quality control measures include checking for electrical safety, proper voltage and current output, and physical durability.
Automated testing systems simulate extensive usage to validate the reliability of each charger.
Only units that pass these stringent tests proceed to the next phase.
Reinforcement of Safety Features
Adding safety features is a critical step in the production process.
Here’s how manufacturers ensure in-car chargers are safe for use:
Over-Current Protection
Over-current protection circuits are installed to prevent excessive current from damaging the charger or connected devices.
These circuits automatically shut off the charger if the current exceeds safe levels.
Over-Voltage Protection
Over-voltage protection safeguards against voltage spikes that could harm electronic devices.
It cuts off power to the charger when input voltage surpasses a set threshold, thus protecting both the car’s electrical system and the mobile device.
Temperature Sensors
Temperature sensors are used to monitor the heat generated during charging.
If the charger reaches a dangerously high temperature, the sensor will trigger an automatic shutdown to prevent overheating and potential fire hazards.
Surge Protection
Surge protection ensures that sudden spikes in electrical power do not damage the charger or connected devices.
Components like metal oxide varistors (MOVs) are used to absorb and dissipate excess electricity.
Final Assembly and Packaging
In the final assembly stage, all components are brought together.
The outer casing is secured around the internal components, and the complete unit is inspected one more time to ensure all parts fit perfectly.
Finally, the chargers are packaged, labeled, and prepared for distribution.
Importance of Certifications
Manufacturers must obtain various certifications to ensure their products meet industry standards.
Certifications such as CE, FCC, and RoHS compliance indicate that the charger has passed health, safety, and environmental protection standards.
Consumers should look out for these certifications to ensure they are purchasing safe and reliable chargers.
Environmental Considerations
Sustainable practices have become integral to the manufacturing of electronic devices.
Manufacturers are increasingly adopting eco-friendly materials and processes.
For example, many companies are reducing the use of hazardous chemicals and opting for recyclable materials in the production of in-car chargers.
Future Innovations
The future of in-car mobile chargers promises technological advancements.
We can expect features like wireless charging, faster charging speeds, and enhanced safety mechanisms to become more prevalent.
Ongoing research and development in the field will ensure these chargers become even more efficient and user-friendly.
In conclusion, the manufacturing process of in-car mobile chargers is a multi-step procedure that emphasizes quality and safety.
With advancements in technology and a growing emphasis on sustainability, these devices are set to become more reliable and efficient, catering to the needs of modern users.
資料ダウンロード
QCD調達購買管理クラウド「newji」は、調達購買部門で必要なQCD管理全てを備えた、現場特化型兼クラウド型の今世紀最高の購買管理システムとなります。
ユーザー登録
調達購買業務の効率化だけでなく、システムを導入することで、コスト削減や製品・資材のステータス可視化のほか、属人化していた購買情報の共有化による内部不正防止や統制にも役立ちます。
NEWJI DX
製造業に特化したデジタルトランスフォーメーション(DX)の実現を目指す請負開発型のコンサルティングサービスです。AI、iPaaS、および先端の技術を駆使して、製造プロセスの効率化、業務効率化、チームワーク強化、コスト削減、品質向上を実現します。このサービスは、製造業の課題を深く理解し、それに対する最適なデジタルソリューションを提供することで、企業が持続的な成長とイノベーションを達成できるようサポートします。
オンライン講座
製造業、主に購買・調達部門にお勤めの方々に向けた情報を配信しております。
新任の方やベテランの方、管理職を対象とした幅広いコンテンツをご用意しております。
お問い合わせ
コストダウンが利益に直結する術だと理解していても、なかなか前に進めることができない状況。そんな時は、newjiのコストダウン自動化機能で大きく利益貢献しよう!
(Β版非公開)