- お役立ち記事
- Manufacturing Process of Indoor Door Closers and Improving Noise Reduction
月間76,176名の
製造業ご担当者様が閲覧しています*
*2025年3月31日現在のGoogle Analyticsのデータより
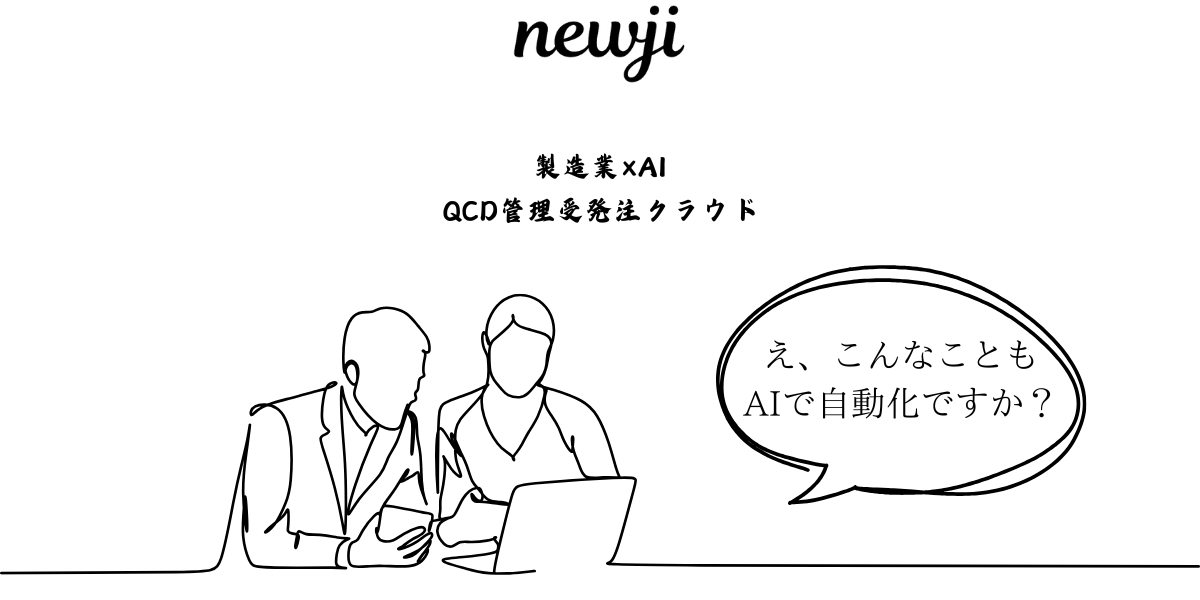
Manufacturing Process of Indoor Door Closers and Improving Noise Reduction
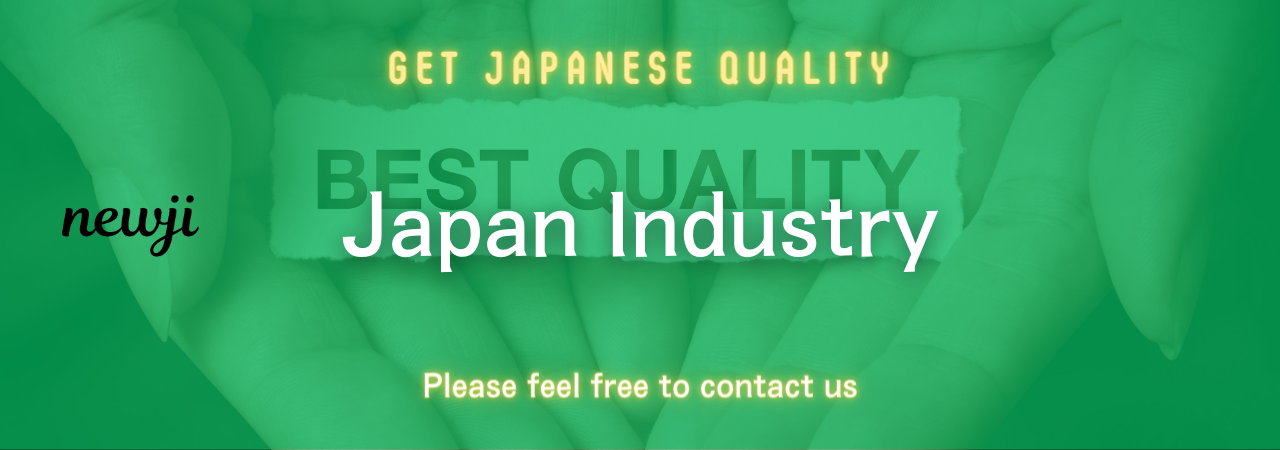
目次
Introduction to Indoor Door Closers
Indoor door closers are an essential part of modern interior design, ensuring doors close smoothly and without a slam.
They not only enhance safety by controlling the speed and force with which a door closes but also contribute to reducing noise, which can be highly beneficial in homes and offices.
Understanding the manufacturing process and the techniques to improve noise reduction can help you appreciate the intricacies involved in these devices.
Materials Used in Door Closers
The manufacturing process begins with the selection of appropriate materials.
Typically, door closers are constructed from durable metals like steel and aluminum.
Steel is preferred for its strength and durability, while aluminum is chosen for its lightweight properties and resistance to corrosion.
High-quality door closers also feature components made from brass, plastic, and rubber.
Rubber and plastic parts are essential for creating seals and dampening noise, contributing to the overall function and quiet operation.
Manufacturing Process of Indoor Door Closers
The manufacturing process involves several key steps:
1. Design and Prototype Development
The first step is the design phase, where engineers create detailed blueprints and 3D models of the door closer.
Prototypes are then developed based on these designs to test functionality and identify any design flaws.
This phase is crucial for ensuring that the final product meets all performance and safety standards.
2. Casting and Forging
Once the design is finalized, the manufacturing process moves to the casting and forging stage.
Metal parts are cast or forged into the required shapes using molds.
During this stage, it’s important to maintain precision to ensure all components fit together perfectly.
3. Machining
After casting, the metal parts undergo machining to achieve the final dimensions and smooth finishes.
This process involves drilling, grinding, and milling to ensure that each component meets the exact specifications.
Precision machining is critical to the performance and longevity of the door closer.
4. Assembly
In the assembly stage, all components are carefully put together.
Springs, pistons, and other internal parts are arranged inside the housing.
This step requires careful attention to detail to ensure that the moving parts function smoothly.
High-quality door closers often undergo rigorous testing during assembly to ensure optimal performance.
5. Surface Treatment
To enhance durability and appearance, door closers undergo surface treatment processes such as painting or powder coating.
This step not only ensures that the door closer blends aesthetically with the door and its surroundings but also protects the components from wear and corrosion.
6. Quality Control
Quality control is a crucial aspect of the manufacturing process.
Each door closer is thoroughly tested to ensure it meets industry standards and works efficiently.
Tests include checking the closing force, speed, and noise levels.
Any product that fails to meet the required standards is either reworked or discarded.
Improving Noise Reduction in Door Closers
Reducing noise from door closers is vital for maintaining a peaceful indoor environment.
Here’s how manufacturers and end-users can work toward improving noise reduction:
1. High-Quality Materials
Using high-quality materials such as robust metals for the body and non-metallic materials for seals can significantly decrease noise.
Rubber or polyurethane seals and gaskets help in absorbing sound and reducing vibrations.
2. Precision Engineering
Careful engineering and precision manufacturing can minimize the gaps and misalignments that often cause noise.
Ensuring that components fit perfectly and move smoothly helps in achieving quieter operation.
3. Adjustable Closing Speed
Door closers with adjustable closing speed allow users to tailor the closing force and speed to their needs.
This feature helps in preventing slamming, which is a major source of noise.
Slow closing speed ensures a gentle and quiet closure.
4. Maintenance and Lubrication
Regular maintenance is essential to maintain the efficiency and noise-reducing capabilities of door closers.
Lubricating moving parts reduces friction and wear, leading to quieter operation.
Checking and tightening all fixtures helps in maintaining alignment and preventing unwanted noise.
5. Installation by Professionals
Proper installation is crucial for the effective functioning of door closers.
Professional installation ensures that the door closer is correctly positioned and secured, reducing the chances of noise due to misalignment or loose fixtures.
Conclusion
The manufacturing process of indoor door closers involves a series of detailed steps from design to quality control, each contributing to the functionality and durability of the product.
By choosing high-quality materials, implementing precision engineering, and ensuring proper installation and maintenance, noise reduction can be significantly improved.
Understanding these processes not only helps in selecting a reliable door closer but also in appreciating the technical expertise involved in creating a device that ensures safety, convenience, and tranquility in indoor environments.
資料ダウンロード
QCD管理受発注クラウド「newji」は、受発注部門で必要なQCD管理全てを備えた、現場特化型兼クラウド型の今世紀最高の受発注管理システムとなります。
ユーザー登録
受発注業務の効率化だけでなく、システムを導入することで、コスト削減や製品・資材のステータス可視化のほか、属人化していた受発注情報の共有化による内部不正防止や統制にも役立ちます。
NEWJI DX
製造業に特化したデジタルトランスフォーメーション(DX)の実現を目指す請負開発型のコンサルティングサービスです。AI、iPaaS、および先端の技術を駆使して、製造プロセスの効率化、業務効率化、チームワーク強化、コスト削減、品質向上を実現します。このサービスは、製造業の課題を深く理解し、それに対する最適なデジタルソリューションを提供することで、企業が持続的な成長とイノベーションを達成できるようサポートします。
製造業ニュース解説
製造業、主に購買・調達部門にお勤めの方々に向けた情報を配信しております。
新任の方やベテランの方、管理職を対象とした幅広いコンテンツをご用意しております。
お問い合わせ
コストダウンが利益に直結する術だと理解していても、なかなか前に進めることができない状況。そんな時は、newjiのコストダウン自動化機能で大きく利益貢献しよう!
(β版非公開)