- お役立ち記事
- Manufacturing Process of Intake Manifolds and Airflow Enhancement
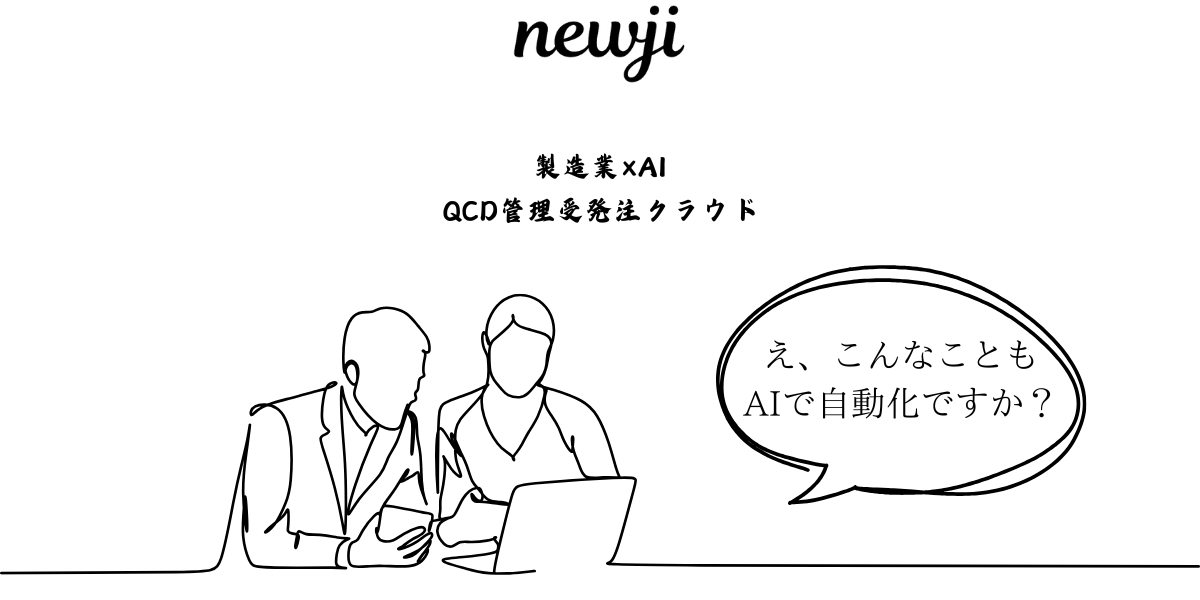
Manufacturing Process of Intake Manifolds and Airflow Enhancement
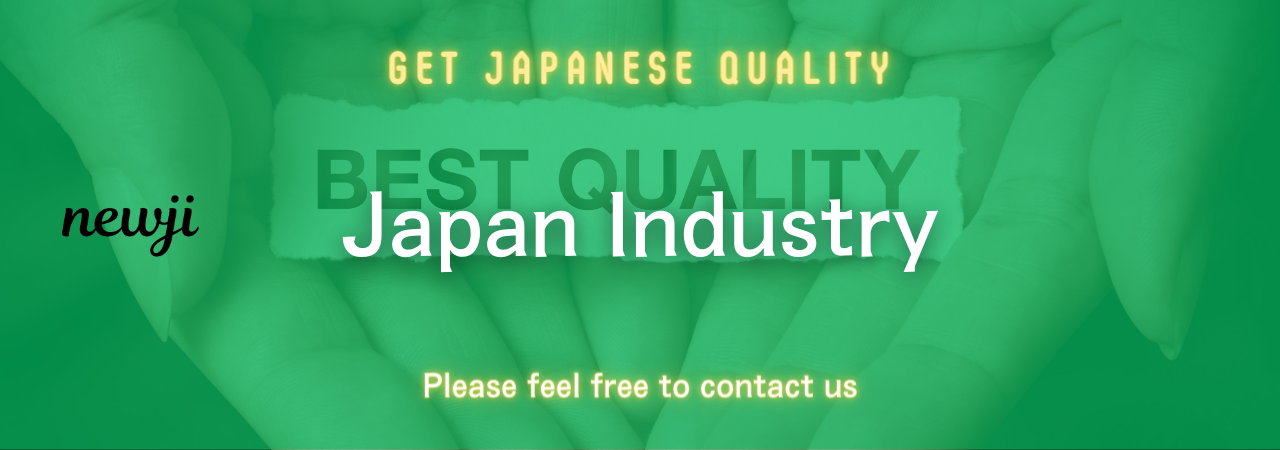
The intake manifold is a crucial part of an automobile engine that ensures proper distribution of air to the cylinders.
It’s essential for maximizing engine performance and efficiency.
This article will delve into the manufacturing process of intake manifolds and various methods to enhance airflow.
目次
Raw Material Selection
The process begins with the selection of raw materials.
Intake manifolds are generally made from aluminum, plastic, and sometimes composite materials.
Aluminum is favored for its strength and lightweight attributes.
Plastic manifolds are chosen for their cost-effectiveness and ability to be molded into complex shapes.
Every material comes with its set of pros and cons, depending on the application’s requirements.
Design and Prototyping
Once the raw material is selected, the design phase begins.
Engineers use Computer-Aided Design (CAD) software to create a detailed blueprint of the intake manifold.
The design process includes simulations to analyze airflow and stress points.
This ensures that the manifold will meet the required performance standards.
Following the design, a prototype is developed, often through 3D printing or machining techniques.
The prototype allows engineers to test and refine the design before moving on to mass production.
Manufacturing Methods
Die-Casting for Aluminum Manifolds
For aluminum manifolds, die-casting is the most common manufacturing method.
Molten aluminum is injected into a steel mold under high pressure, forming the manifold shape.
After cooling, the manifold is removed from the mold and sent for further processing.
Injection Molding for Plastic Manifolds
Plastic manifolds are usually produced through injection molding.
A thermoplastic polymer is melted and injected into a mold.
Once it cools and solidifies, the manifold is ejected from the mold, ready for finishing touches.
Composite Fabrication
Composite intake manifolds are less common but offer unique benefits like enhanced durability and heat resistance.
The manufacturing process involves layering materials like carbon fiber and resin, then curing them under heat and pressure.
Finishing Processes
After the manifold has been cast or molded, it needs to go through several finishing processes to meet specifications.
These processes include deburring, machining, and surface treatment.
Deburring removes any rough edges or excess material from the manifold.
Machining helps achieve the necessary dimensional accuracy and surface finish.
Finally, various surface treatments, like anodizing or powder coating, are applied to protect the manifold from corrosion and wear.
Quality Control
Quality control is an essential part of the manufacturing process.
Each intake manifold goes through rigorous testing to ensure it meets performance and safety standards.
Non-destructive testing methods, such as X-ray and ultrasonic inspection, are used to detect any internal flaws.
Additionally, each manifold undergoes airflow testing to confirm that it will perform optimally when installed in an engine.
Airflow Enhancement Techniques
Porting
Porting is the process of modifying the intake manifold’s internal pathways to improve airflow.
This involves enlarging the ports and smoothing the surfaces to reduce air resistance.
Expert machinists use specialized tools and equipment for this task.
Porting can significantly improve engine efficiency and power output, making it a popular modification among performance enthusiasts.
Variable Length Intake Manifolds (VLIM)
Variable length intake manifolds (VLIM) are designed to change the length of the air intake pathway based on engine speed.
At lower speeds, a longer pathway helps improve torque, while at higher speeds, a shorter pathway enhances power.
This adaptability can optimize engine performance across various driving conditions.
Aftermarket Cold Air Intakes
Cold air intakes are a popular aftermarket modification aimed at improving airflow.
These systems replace the stock air filter and intake tube with a design that lets more cold air into the engine.
Cold air is denser than warm air, providing more oxygen for combustion.
This results in increased power and efficiency.
Maintenance and Upkeep
An optimized intake manifold requires regular maintenance to maintain its performance benefits.
Simple practices like cleaning the manifold, ensuring the gasket is in good condition, and checking for any cracks or damage can go a long way.
Periodic inspections can catch issues early, preventing more severe damage and costly repairs down the line.
Environmental Considerations
The manufacturing process of intake manifolds must also account for environmental impact.
Using recyclable materials like aluminum and plastic can help reduce waste.
Energy-efficient manufacturing techniques and pollution control measures are also essential.
By adopting these practices, manufacturers can produce high-quality intake manifolds while minimizing their environmental footprint.
Future Trends
The future of intake manifold manufacturing is likely to see advancements in materials and technologies.
For instance, the advent of 3D printing allows for more complex designs that could further enhance airflow and performance.
Additionally, the continuous development of advanced composites offers the potential for lighter, stronger, and more heat-resistant manifolds.
As the automotive industry shifts towards more eco-friendly vehicles, intake manifold designs will also evolve to meet new engine requirements and regulations.
In conclusion, the manufacturing process of intake manifolds involves several steps, from raw material selection and design to finishing and quality control.
Various techniques such as porting, VLIM, and cold air intakes can enhance airflow and improve engine performance.
Regular maintenance and environmental considerations are essential to ensure the manifold’s longevity and compliance with regulations.
With ongoing advancements in technology and materials, the future of intake manifolds holds exciting possibilities for further performance enhancements.
資料ダウンロード
QCD調達購買管理クラウド「newji」は、調達購買部門で必要なQCD管理全てを備えた、現場特化型兼クラウド型の今世紀最高の購買管理システムとなります。
ユーザー登録
調達購買業務の効率化だけでなく、システムを導入することで、コスト削減や製品・資材のステータス可視化のほか、属人化していた購買情報の共有化による内部不正防止や統制にも役立ちます。
NEWJI DX
製造業に特化したデジタルトランスフォーメーション(DX)の実現を目指す請負開発型のコンサルティングサービスです。AI、iPaaS、および先端の技術を駆使して、製造プロセスの効率化、業務効率化、チームワーク強化、コスト削減、品質向上を実現します。このサービスは、製造業の課題を深く理解し、それに対する最適なデジタルソリューションを提供することで、企業が持続的な成長とイノベーションを達成できるようサポートします。
オンライン講座
製造業、主に購買・調達部門にお勤めの方々に向けた情報を配信しております。
新任の方やベテランの方、管理職を対象とした幅広いコンテンツをご用意しております。
お問い合わせ
コストダウンが利益に直結する術だと理解していても、なかなか前に進めることができない状況。そんな時は、newjiのコストダウン自動化機能で大きく利益貢献しよう!
(Β版非公開)