- お役立ち記事
- Manufacturing Process of Light Switches and Durability Reinforcement
月間76,176名の
製造業ご担当者様が閲覧しています*
*2025年3月31日現在のGoogle Analyticsのデータより
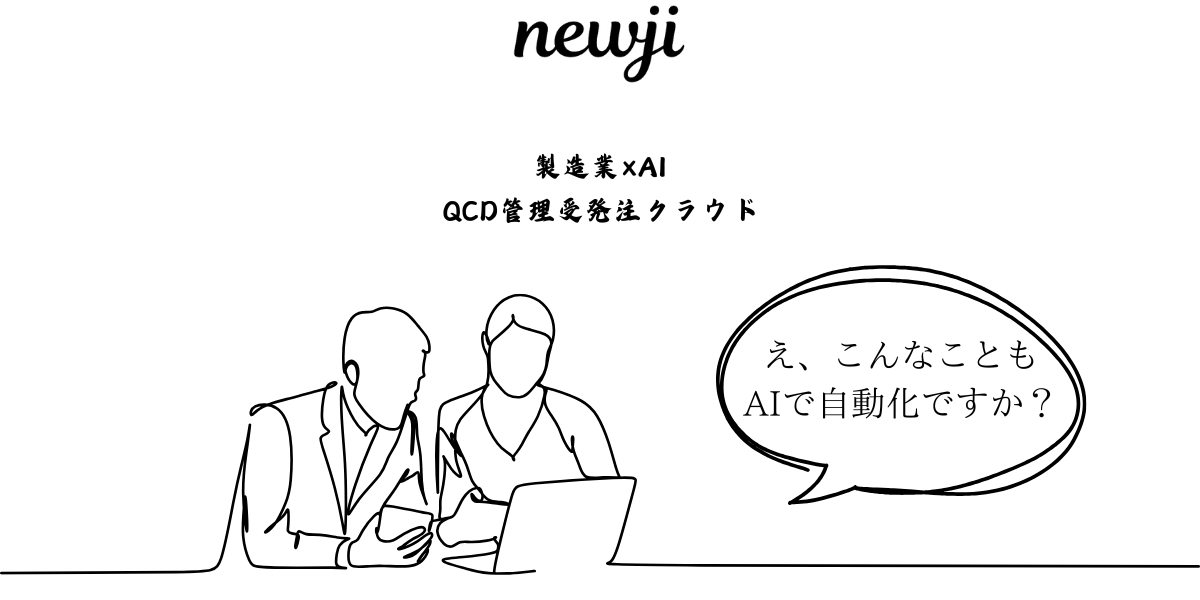
Manufacturing Process of Light Switches and Durability Reinforcement
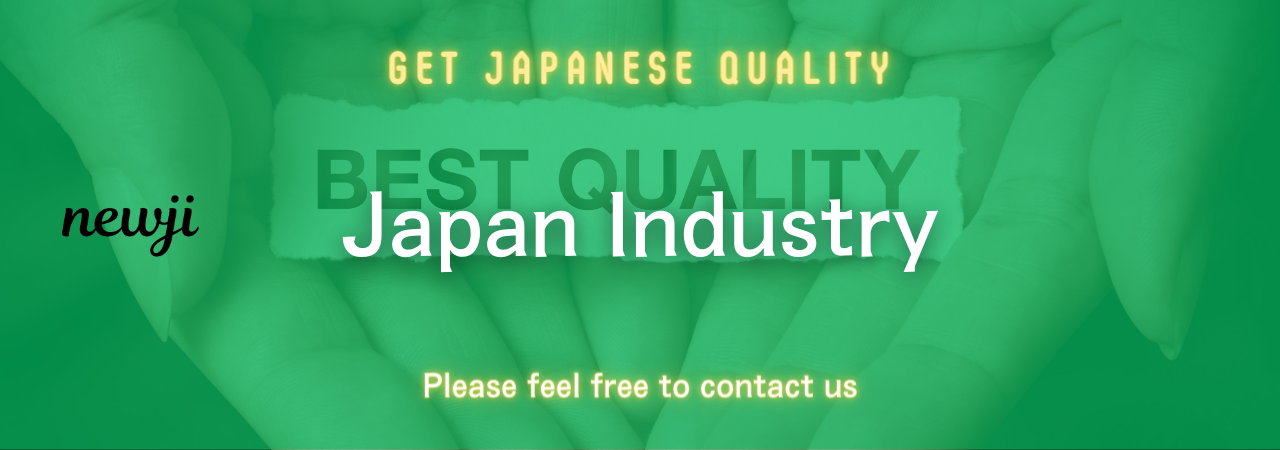
Light switches are essential components in our homes, offices, and industrial settings.
They control electrical currents, turning lights on and off with ease.
But have you ever wondered how light switches are made and how they’re designed to last for years?
In this article, we’ll explore the manufacturing process of light switches and how durability is reinforced during production.
目次
Materials Used in Light Switches
Light switches are primarily made of plastic and metal components.
The outer casing is usually made of high-quality, durable plastic like polycarbonate or ABS (Acrylonitrile Butadiene Styrene).
These plastics are chosen for their electrical insulation properties and their ability to withstand high temperatures.
For the internal components, manufacturers use metals such as copper, brass, and aluminum.
These metals are excellent conductors of electricity and resist corrosion, ensuring the switch’s longevity.
Plastic Components
The plastic parts of a light switch include the outer casing, the toggle or rocker mechanism, and various internal insulators.
These parts are typically created using injection molding.
During this process, molten plastic is injected into a mold cavity, where it cools and solidifies into the desired shape.
The finished plastic components are then trimmed and polished to remove any excess material or rough edges.
Metal Components
The metal parts within a light switch include contacts, terminals, and actuators.
These components are manufactured through processes like stamping, forming, and metal casting.
Stamping involves pressing flat metal sheets into specific shapes using a die and press machine.
Forming, on the other hand, bends and shapes the metal without removing any material.
Casting involves pouring molten metal into a mold, where it cools and hardens into the desired shape.
These metal components are then coated or treated to enhance their resistance to wear, corrosion, and electrical arcing, ensuring they function reliably over the switch’s lifespan.
Assembly of Light Switch Components
Once the plastic and metal components are prepared, they are assembled to create the finished light switch.
Assembly typically involves several steps.
Component Insertion
First, the metal contacts and terminals are inserted into the plastic casing.
These metal parts are carefully positioned to ensure proper alignment and connection.
Precision is vital here, as any misalignment can affect the switch’s performance or safety.
Securing the Mechanism
Next, the toggle or rocker mechanism, often made of a more flexible plastic material, is attached to the main body.
This mechanism allows users to easily flick the switch on and off.
It’s designed to fit snugly into the casing while providing enough flexibility for smooth operation.
Electrical Connection
The light switch’s internal contacts and terminals are then connected using specialized tools.
These connections must be secure to maintain electrical continuity and prevent any potential hazards.
Manufacturers often use soldering or mechanical fastening methods, such as screws or clamps, to achieve these robust connections.
Quality Testing
Once assembled, each light switch undergoes rigorous quality testing to ensure it meets safety and performance standards.
Tests may include checking for proper electrical operation, inspecting the alignment of components, and subjecting the switch to mechanical stress to evaluate its durability.
Switches that pass these tests are then packaged and shipped to retailers or wholesalers.
Reinforcing Durability in Light Switches
Ensuring the long-term durability of light switches is crucial.
Several steps in the manufacturing process help achieve this goal.
Material Selection
Choosing high-quality materials, such as corrosion-resistant metals and heat-resistant plastics, is the first line of defense against wear and tear.
Manufacturers also select materials that can withstand high temperatures without degrading, which is essential for safety in electrical applications.
Design Optimization
The design of a light switch plays a significant role in its durability.
Manufacturers employ advanced design techniques, such as finite element analysis (FEA), to simulate the stresses and strains the switch will encounter during its lifespan.
This helps identify potential weak points and allows designers to make necessary adjustments to enhance the switch’s robustness.
Surface Treatments
To further enhance durability, metal components often undergo surface treatments.
These treatments can include electroplating, anodizing, or applying protective coatings.
Such treatments provide an additional layer of protection against corrosion, wear, and electrical arcing.
Environmental Testing
Before mass production, light switches are subjected to environmental testing.
This includes exposing them to extreme temperatures, humidity, and electrical loads to ensure they can withstand harsh conditions.
Environmental testing helps identify any potential issues that could cause premature failure, allowing manufacturers to address them before the product reaches consumers.
Maintenance and Proper Usage
Even the most durable light switches require proper maintenance and usage to extend their lifespan.
Regular Cleaning
Dust and dirt can accumulate on light switches over time, affecting their functionality.
Regular cleaning with a soft, dry cloth helps keep the switch in good working condition.
Avoid using harsh chemicals or abrasive materials, as they can damage the switch’s surface.
Avoid Overloading
Exceeding the switch’s rated electrical load can lead to overheating and potential failure.
Always check the switch’s load rating and ensure it’s suitable for the intended application.
If in doubt, consult an electrician for advice.
Periodic Inspection
Periodically inspect light switches for any signs of wear, such as loose connections or discoloration.
If you notice any issues, replace the switch promptly to maintain safety and functionality.
By understanding the manufacturing process and the steps taken to reinforce durability, we gain a greater appreciation for the seemingly simple light switch.
Through careful material selection, precision assembly, and rigorous testing, manufacturers ensure these devices provide reliable and safe operation in our daily lives.
資料ダウンロード
QCD管理受発注クラウド「newji」は、受発注部門で必要なQCD管理全てを備えた、現場特化型兼クラウド型の今世紀最高の受発注管理システムとなります。
ユーザー登録
受発注業務の効率化だけでなく、システムを導入することで、コスト削減や製品・資材のステータス可視化のほか、属人化していた受発注情報の共有化による内部不正防止や統制にも役立ちます。
NEWJI DX
製造業に特化したデジタルトランスフォーメーション(DX)の実現を目指す請負開発型のコンサルティングサービスです。AI、iPaaS、および先端の技術を駆使して、製造プロセスの効率化、業務効率化、チームワーク強化、コスト削減、品質向上を実現します。このサービスは、製造業の課題を深く理解し、それに対する最適なデジタルソリューションを提供することで、企業が持続的な成長とイノベーションを達成できるようサポートします。
製造業ニュース解説
製造業、主に購買・調達部門にお勤めの方々に向けた情報を配信しております。
新任の方やベテランの方、管理職を対象とした幅広いコンテンツをご用意しております。
お問い合わせ
コストダウンが利益に直結する術だと理解していても、なかなか前に進めることができない状況。そんな時は、newjiのコストダウン自動化機能で大きく利益貢献しよう!
(β版非公開)