- お役立ち記事
- Manufacturing Process of Oil Filters and Filtration Accuracy Enhancement
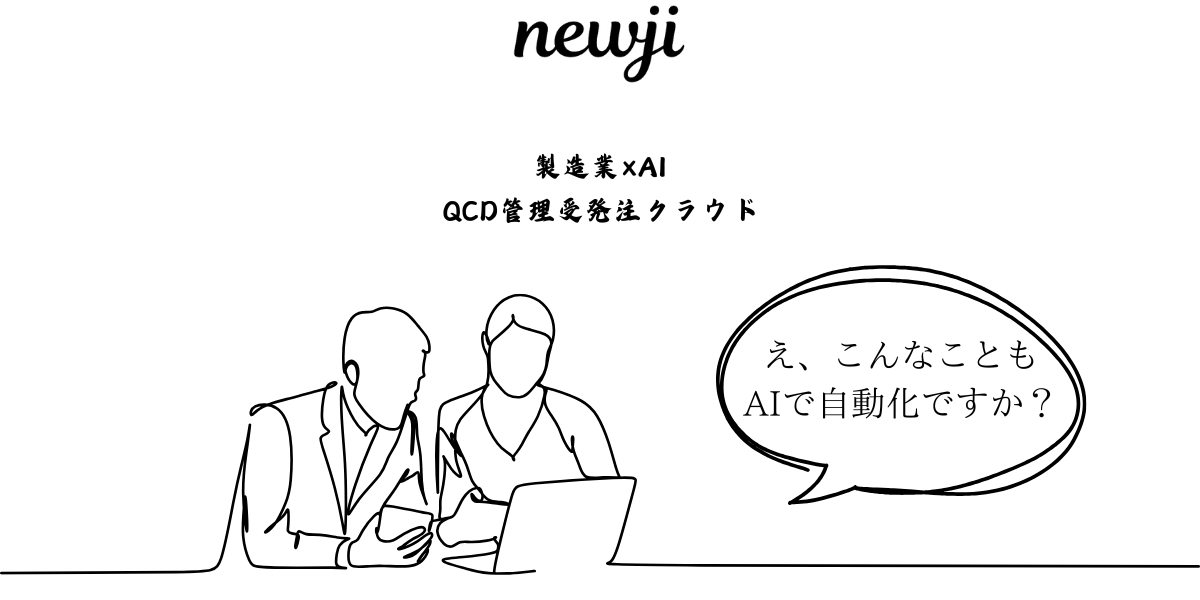
Manufacturing Process of Oil Filters and Filtration Accuracy Enhancement
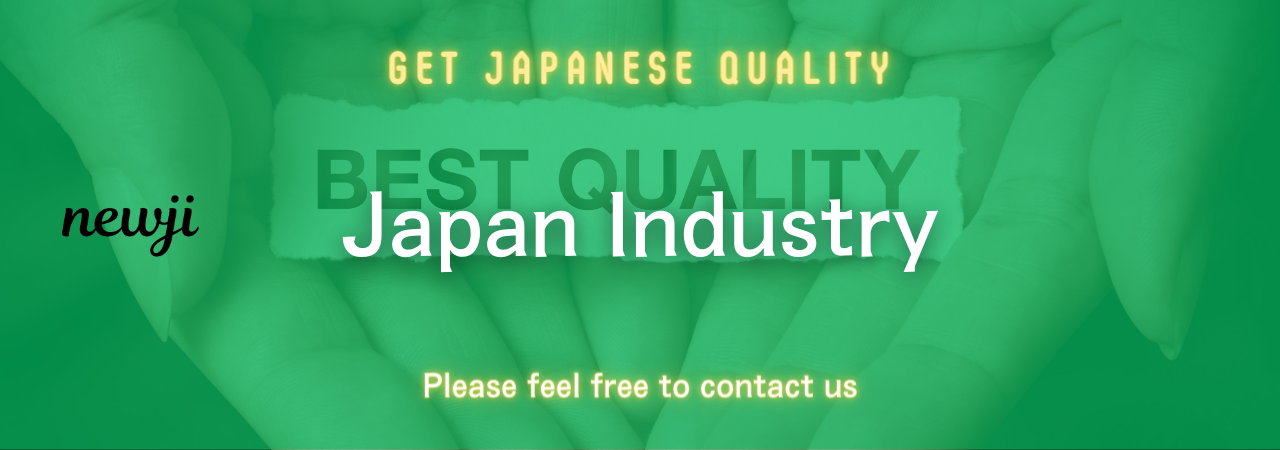
Manufacturing oil filters is a complex process that requires precision, attention to detail, and high-quality materials.
Oil filters play a crucial role in ensuring that engines run smoothly by removing contaminants from the oil, thus preventing engine damage and extending its lifespan.
In this article, we will explore the manufacturing process of oil filters and discuss how filtration accuracy can be enhanced.
目次
Raw Material Selection
The first step in manufacturing oil filters is selecting the raw materials.
The primary components of an oil filter include the filter media, the casing, the end caps, and the center tube.
The filter media is typically made from cellulose, synthetic fibers, or a blend of both.
Cellulose is a natural material derived from wood pulp that is cost-effective and provides adequate filtration.
Synthetic fibers, on the other hand, are man-made materials that offer superior filtration and durability.
The casing is usually made from metal or plastic, with metal casings being more common due to their strength and resistance to high temperatures.
End caps, which seal the ends of the filter media, are often made from metal or plastic as well.
The center tube, which supports the filter media and allows oil to flow through, is typically made from metal.
Filter Media Manufacturing
Once the raw materials are selected, the filter media is manufactured.
This process begins with producing a large sheet of filter media from cellulose or synthetic fibers.
The sheet is then cut into the desired shape and size for the specific oil filter being produced.
In some cases, the filter media is treated with a resin to enhance its filtration capabilities and durability.
The treated filter media is then cured in an oven to set the resin.
Center Tube Production
The center tube, which is a critical component of the oil filter, is produced next.
Metal sheets are cut and rolled into tubes, and then perforations are added to allow oil to flow through.
These perforations must be precise to ensure optimal flow and filtration.
The center tubes are then formed and welded to maintain their shape and strength.
Assembly of Filter Components
With the filter media and center tube ready, the assembly process begins.
The filter media is first pleated to increase the surface area available for filtration.
Pleating involves folding the filter media into a zigzag pattern, which allows it to capture more contaminants.
The pleated filter media is then wrapped around the center tube, holding it securely in place.
End caps are attached to the ends of the filter media, ensuring a tight seal.
The assembly is then inserted into the casing.
Sealing and Testing
To ensure no oil leaks around the filter media, sealing is critical.
The casing is typically crimped or welded to seal the ends securely.
Some filters also use gaskets or O-rings to provide an additional layer of protection against leaks.
Once the sealing is complete, the oil filters undergo rigorous testing.
This testing includes checking for leaks, ensuring the filter media is securely attached, and verifying that the filter meets all specifications.
Enhancing Filtration Accuracy
Advanced Filter Media
One of the most effective ways to enhance filtration accuracy is by using advanced filter media.
Synthetic fibers, for example, provide superior filtration compared to traditional cellulose filter media.
They can capture smaller particles and have a longer lifespan, which makes them ideal for high-performance engines.
Additionally, some manufacturers incorporate nanofiber technology into their filter media, which can trap even the finest particles with high efficiency.
Multi-Layer Filtration
Another method to improve filtration accuracy is by using multi-layer filtration.
This involves layering different types of filter media to achieve optimal filtration performance.
For instance, a filter might have a coarse layer to capture larger particles and a fine layer to trap smaller contaminants.
By combining multiple layers, the filter can provide a higher level of filtration accuracy and extend its service life.
Innovative Design and Engineering
Innovative design and engineering practices also play a vital role in enhancing filtration accuracy.
Some manufacturers use advanced computational fluid dynamics (CFD) and finite element analysis (FEA) to design oil filters.
These tools help optimize the filter’s design, ensuring it provides maximum filtration efficiency while maintaining proper oil flow.
Additionally, engineers may incorporate features such as bypass valves, anti-drainback valves, and pressure relief valves to enhance the filter’s performance and reliability.
Stringent Quality Control
Implementing stringent quality control measures throughout the manufacturing process is crucial for enhancing filtration accuracy.
Manufacturers should conduct regular inspections and tests at various stages of production to ensure the filter components meet all specifications.
This includes testing the filter media for its filtration efficiency, tensile strength, and resistance to chemicals.
Additionally, manufacturers should verify that the filter assembly is leak-proof and can withstand the pressures and temperatures experienced during engine operation.
Continuous Research and Development
Finally, continuous research and development (R&D) is essential for improving filtration accuracy.
Manufacturers should invest in R&D to explore new materials, technologies, and manufacturing processes that can enhance oil filters’ performance.
This might involve developing new filter media, improving pleating techniques, or designing innovative filter configurations.
By staying at the forefront of technological advancements, manufacturers can produce oil filters that meet the evolving needs of modern engines.
In conclusion, the manufacturing process of oil filters involves several crucial steps, including raw material selection, filter media manufacturing, assembly, sealing, and testing.
To enhance filtration accuracy, manufacturers can use advanced filter media, multi-layer filtration, innovative design, stringent quality control, and continuous research and development.
By prioritizing these factors, manufacturers can produce high-quality oil filters that ensure engines run smoothly and efficiently for extended periods.
資料ダウンロード
QCD調達購買管理クラウド「newji」は、調達購買部門で必要なQCD管理全てを備えた、現場特化型兼クラウド型の今世紀最高の購買管理システムとなります。
ユーザー登録
調達購買業務の効率化だけでなく、システムを導入することで、コスト削減や製品・資材のステータス可視化のほか、属人化していた購買情報の共有化による内部不正防止や統制にも役立ちます。
NEWJI DX
製造業に特化したデジタルトランスフォーメーション(DX)の実現を目指す請負開発型のコンサルティングサービスです。AI、iPaaS、および先端の技術を駆使して、製造プロセスの効率化、業務効率化、チームワーク強化、コスト削減、品質向上を実現します。このサービスは、製造業の課題を深く理解し、それに対する最適なデジタルソリューションを提供することで、企業が持続的な成長とイノベーションを達成できるようサポートします。
オンライン講座
製造業、主に購買・調達部門にお勤めの方々に向けた情報を配信しております。
新任の方やベテランの方、管理職を対象とした幅広いコンテンツをご用意しております。
お問い合わせ
コストダウンが利益に直結する術だと理解していても、なかなか前に進めることができない状況。そんな時は、newjiのコストダウン自動化機能で大きく利益貢献しよう!
(Β版非公開)