- お役立ち記事
- Manufacturing Process of Pipe Fittings and Pressure Resistance Improvement
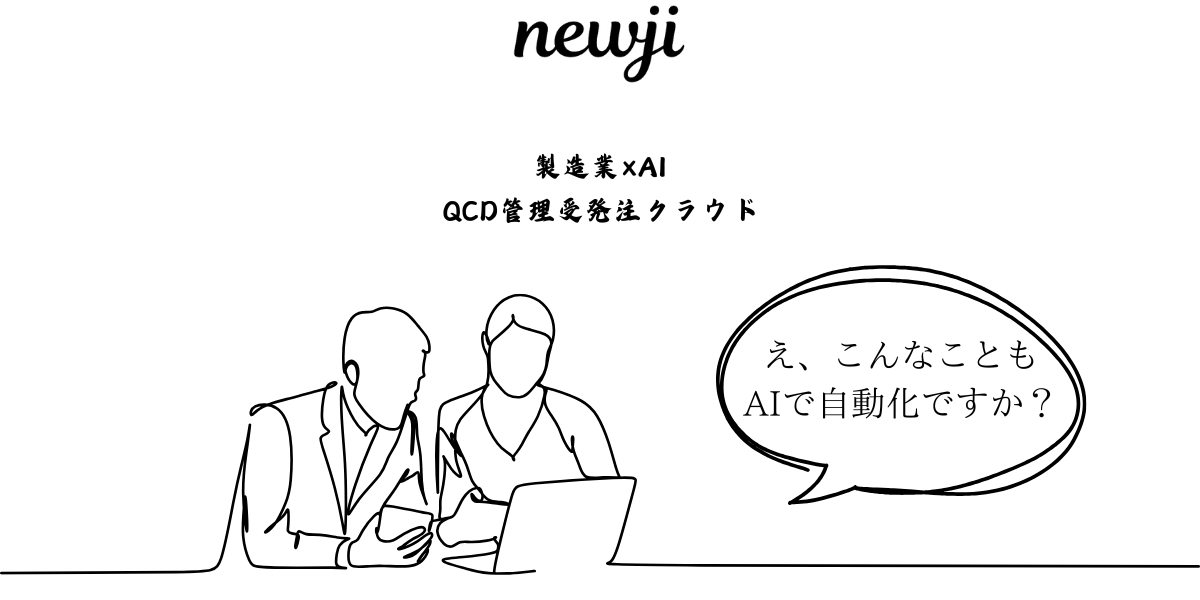
Manufacturing Process of Pipe Fittings and Pressure Resistance Improvement
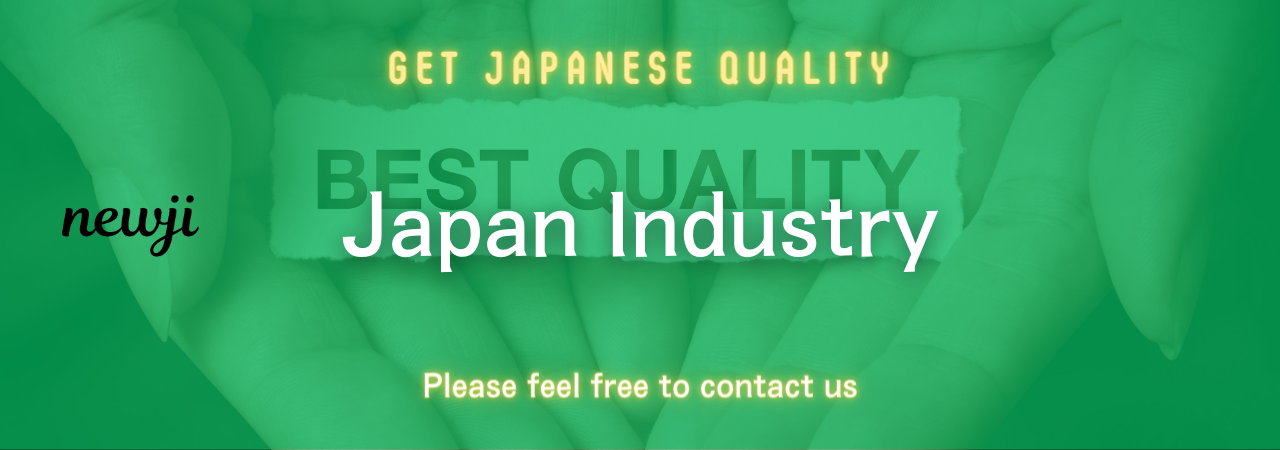
Pipe fittings are essential components in various industries, ensuring that fluid flows are appropriately directed, controlled, and connected. They come in different shapes, sizes, and materials, each uniquely designed to fit specific applications. The manufacturing process and pressure resistance of these pipe fittings are critical factors in their effectiveness and reliability.
目次
Types of Pipe Fittings
Pipe fittings come in a variety of types, each serving a specific function. Some common types include elbows, tees, reducers, caps, flanges, and couplings. Elbows change the direction of the fluid flow, while tees split or combine flows. Reducers adjust the pipe diameter, and caps close the end of a pipe. Flanges connect pipes and fittings, and couplings join two pipes together.
Materials Used in Pipe Fittings
The materials used in the manufacturing of pipe fittings play a significant role in their strength, durability, and resistance to corrosion. Stainless steel, carbon steel, brass, copper, and PVC are some of the commonly used materials. Stainless steel and carbon steel are known for their high strength and resistance to corrosion. Brass and copper offer good conductivity and resistance to corrosion, making them ideal for plumbing applications. PVC is lightweight, corrosion-resistant, and suitable for low-pressure applications.
Manufacturing Process of Pipe Fittings
The manufacturing process of pipe fittings involves several steps, each ensuring that the final product meets the required standards and specifications. Here’s a breakdown of the typical process:
1. Designing
The first step in the manufacturing process is designing the pipe fittings. Engineers create detailed designs and specifications, considering factors such as material, size, shape, and pressure ratings. Computer-Aided Design (CAD) software is often used to create precise and accurate designs.
2. Raw Material Selection
Selecting the right raw material is crucial for the manufacturing of high-quality pipe fittings. The material is chosen based on the design specifications and the application requirements. Once the material is selected, it goes through a series of tests to ensure it meets the necessary quality standards.
3. Cutting
The raw material is then cut into the required lengths and shapes using cutting machines. This step is critical in ensuring that the material is prepared for the subsequent forming processes. Precision cutting tools and techniques are used to achieve accurate and clean cuts.
4. Forming
Forming is a crucial step in the manufacturing process. Depending on the type of fitting, different forming techniques are used. Common forming methods include hot forming, cold forming, and machining. Hot forming involves heating the material to make it more malleable and then shaping it into the desired shape. Cold forming involves shaping the material at room temperature, while machining involves using precision tools to cut and shape the material into the required form.
5. Welding and Joining
For welded fittings, the formed pieces are joined together using welding techniques. Welding ensures a strong and leak-proof connection between the pieces. Various welding methods, such as TIG welding, MIG welding, and arc welding, are used depending on the material and application requirements.
6. Heat Treatment
Heat treatment is an essential step in enhancing the strength and durability of the pipe fittings. The fittings are subjected to controlled heating and cooling processes to improve their mechanical properties and resistance to wear and corrosion.
Pressure Resistance Improvement
Enhancing the pressure resistance of pipe fittings is crucial for ensuring their reliability and safety in high-pressure applications. Several techniques are used to improve the pressure resistance of pipe fittings:
1. Material Selection
Using high-strength materials with excellent mechanical properties can significantly improve the pressure resistance of pipe fittings. Materials such as stainless steel, carbon steel, and high-grade alloys are often chosen for high-pressure applications.
2. Heat Treatment
As mentioned earlier, heat treatment enhances the strength and durability of the pipe fittings. Proper heat treatment processes improve the material’s resistance to pressure, making the fittings more robust and reliable.
3. Wall Thickness
Increasing the wall thickness of the pipe fittings can also improve their pressure resistance. Thicker walls provide greater strength and support, enabling the fittings to withstand higher pressures without failing.
4. Reinforcement
Reinforcing critical areas of the pipe fittings with additional material or support structures can enhance their pressure resistance. This is especially important for fittings subjected to high-stress and high-pressure conditions.
5. Quality Control
Implementing rigorous quality control measures throughout the manufacturing process ensures that the pipe fittings meet the required standards and specifications. Regular inspections, testing, and quality assurance processes help identify and address any potential issues before the fittings are used in high-pressure applications.
Conclusion
The manufacturing process of pipe fittings involves a series of steps, each critical in ensuring the quality and reliability of the final product. From designing and raw material selection to forming and heat treatment, every step plays a vital role in producing high-quality pipe fittings.
Enhancing the pressure resistance of pipe fittings through material selection, heat treatment, wall thickness, reinforcement, and quality control ensures their reliability and safety in various applications.
Understanding the manufacturing process and pressure resistance improvement techniques is essential for selecting the right pipe fittings for your specific needs, ensuring the efficient and safe operation of your systems.
資料ダウンロード
QCD調達購買管理クラウド「newji」は、調達購買部門で必要なQCD管理全てを備えた、現場特化型兼クラウド型の今世紀最高の購買管理システムとなります。
ユーザー登録
調達購買業務の効率化だけでなく、システムを導入することで、コスト削減や製品・資材のステータス可視化のほか、属人化していた購買情報の共有化による内部不正防止や統制にも役立ちます。
NEWJI DX
製造業に特化したデジタルトランスフォーメーション(DX)の実現を目指す請負開発型のコンサルティングサービスです。AI、iPaaS、および先端の技術を駆使して、製造プロセスの効率化、業務効率化、チームワーク強化、コスト削減、品質向上を実現します。このサービスは、製造業の課題を深く理解し、それに対する最適なデジタルソリューションを提供することで、企業が持続的な成長とイノベーションを達成できるようサポートします。
オンライン講座
製造業、主に購買・調達部門にお勤めの方々に向けた情報を配信しております。
新任の方やベテランの方、管理職を対象とした幅広いコンテンツをご用意しております。
お問い合わせ
コストダウンが利益に直結する術だと理解していても、なかなか前に進めることができない状況。そんな時は、newjiのコストダウン自動化機能で大きく利益貢献しよう!
(Β版非公開)