- お役立ち記事
- Manufacturing Process of Precision Screwdrivers and Grip Performance Improvement
月間76,176名の
製造業ご担当者様が閲覧しています*
*2025年3月31日現在のGoogle Analyticsのデータより
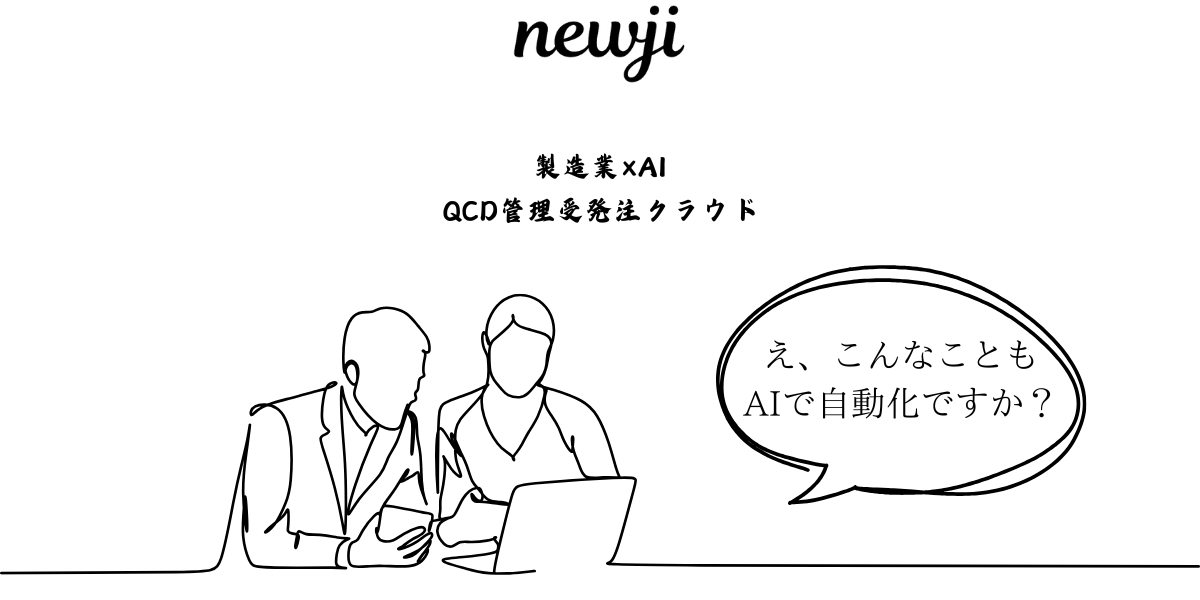
Manufacturing Process of Precision Screwdrivers and Grip Performance Improvement
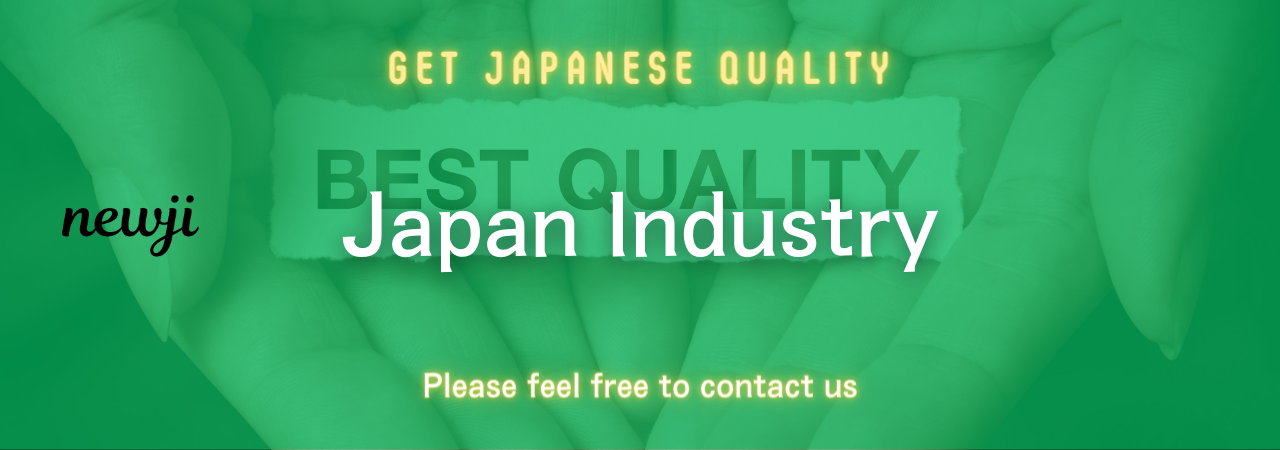
Precision screwdrivers are essential tools for professionals and hobbyists alike, providing accurate and reliable results for various tasks. Understanding how these tools are made and how their grip performance can be improved is crucial. This knowledge helps you make informed choices when selecting the best precision screwdriver for your needs.
目次
Raw Materials and Initial Design
The manufacturing process of precision screwdrivers begins with the selection of high-quality raw materials. Typically, the shaft of the screwdriver is made of durable steel, such as chrome vanadium or stainless steel. These materials are chosen for their strength, resistance to wear and tear, and corrosion resistance.
The handle of the screwdriver is often made from impact-resistant plastic, rubber, or a combination of both. These materials provide a comfortable grip and reduce hand fatigue during prolonged use.
Once the materials are selected, the design phase begins. Precision screwdrivers are designed with meticulous attention to detail. Engineers create detailed blueprints, outlining the exact dimensions and specifications of the screwdriver to ensure consistent performance and accuracy.
Forging and Machining the Shaft
The next step in the manufacturing process involves forging and machining the shaft of the screwdriver. The steel is heated to a high temperature and then forged into the basic shape of the shaft. This process enhances the strength and durability of the metal.
After forging, the shaft undergoes precision machining. Computer Numerical Control (CNC) machines are used to cut and shape the shaft to the exact dimensions specified in the design. This step is crucial as it ensures the shaft’s accuracy and fit, allowing it to turn screws with precision.
Heat Treatment and Plating
To further enhance the strength and durability of the shaft, it undergoes heat treatment. The shaft is heated to a specific temperature to alter its molecular structure, increasing its hardness and resilience. This process ensures that the shaft can withstand the rigors of regular use without deforming or breaking.
Once the heat treatment is complete, the shaft is plated with a protective coating. Common coatings include chrome, nickel, or black oxide. These coatings provide additional corrosion resistance and improve the overall appearance of the screwdriver.
Crafting the Handle
While the shaft is being forged and machined, the handle of the precision screwdriver is also being crafted. Handles are typically made using injection molding, a process in which molten plastic or rubber is injected into a mold to form the desired shape.
Engineers design the molds to include ergonomic features that enhance grip performance. This can include textured surfaces, contoured shapes, and rubberized coatings. These features ensure that the screwdriver is comfortable to hold and reduces the likelihood of slipping during use.
Assembling the Screwdriver
With the shaft and handle complete, the next step is to assemble the precision screwdriver. The shaft is inserted into the handle and securely fastened in place. This can be done using adhesives, mechanical fasteners, or a combination of both.
Quality control measures are implemented throughout the assembly process to ensure that each screwdriver meets the required standards. Each unit is inspected for defects and tested for performance to guarantee that it functions as intended.
Improving Grip Performance
One of the most critical aspects of a precision screwdriver is its grip performance. A comfortable and secure grip not only enhances the user’s experience but also improves the accuracy and efficiency of the tool. Manufacturers employ several techniques to improve grip performance.
Ergonomic Design
Ergonomic design plays a significant role in enhancing grip performance. Handles are designed to fit comfortably in the hand and reduce strain on the user’s wrist and fingers. Engineers consider factors such as handle shape, size, and material to create a design that offers maximum comfort and control.
Textured Surfaces
Textured surfaces are added to the handle to improve grip performance. These surfaces can include ribbed patterns, knurled textures, or soft rubberized coatings. Textured surfaces provide additional traction, reducing the likelihood of slipping, even when using the screwdriver in wet or oily conditions.
Rubberized Coatings
Many precision screwdrivers feature rubberized coatings on the handle. These coatings provide a soft, comfortable grip and enhance the user’s control over the tool. Rubberized coatings are particularly beneficial for reducing hand fatigue during extended use.
Contoured Shapes
Contoured handle shapes are designed to fit the natural curves of the hand. These shapes provide a more secure and comfortable grip, allowing the user to apply more force and precision when turning screws. Contoured designs distribute pressure evenly across the hand, reducing strain and discomfort.
Weight Distribution
Proper weight distribution is crucial for enhancing grip performance. Precision screwdrivers are designed to have a balanced weight distribution, preventing the tool from feeling too heavy or unbalanced in the hand. This balance allows for greater control and accuracy when using the screwdriver.
Conclusion
Understanding the manufacturing process of precision screwdrivers and the techniques used to improve grip performance provides valuable insights into what makes these tools reliable and efficient. From selecting high-quality materials to implementing ergonomic designs, manufacturers take great care to ensure that precision screwdrivers meet the demands of their users.
When choosing a precision screwdriver, consider factors such as material quality, handle design, and grip features. By doing so, you can select a tool that not only meets your needs but also provides a comfortable and enjoyable user experience.
資料ダウンロード
QCD管理受発注クラウド「newji」は、受発注部門で必要なQCD管理全てを備えた、現場特化型兼クラウド型の今世紀最高の受発注管理システムとなります。
ユーザー登録
受発注業務の効率化だけでなく、システムを導入することで、コスト削減や製品・資材のステータス可視化のほか、属人化していた受発注情報の共有化による内部不正防止や統制にも役立ちます。
NEWJI DX
製造業に特化したデジタルトランスフォーメーション(DX)の実現を目指す請負開発型のコンサルティングサービスです。AI、iPaaS、および先端の技術を駆使して、製造プロセスの効率化、業務効率化、チームワーク強化、コスト削減、品質向上を実現します。このサービスは、製造業の課題を深く理解し、それに対する最適なデジタルソリューションを提供することで、企業が持続的な成長とイノベーションを達成できるようサポートします。
製造業ニュース解説
製造業、主に購買・調達部門にお勤めの方々に向けた情報を配信しております。
新任の方やベテランの方、管理職を対象とした幅広いコンテンツをご用意しております。
お問い合わせ
コストダウンが利益に直結する術だと理解していても、なかなか前に進めることができない状況。そんな時は、newjiのコストダウン自動化機能で大きく利益貢献しよう!
(β版非公開)