- お役立ち記事
- Manufacturing Process of Pressure Valves and Safety Improvement
Manufacturing Process of Pressure Valves and Safety Improvement
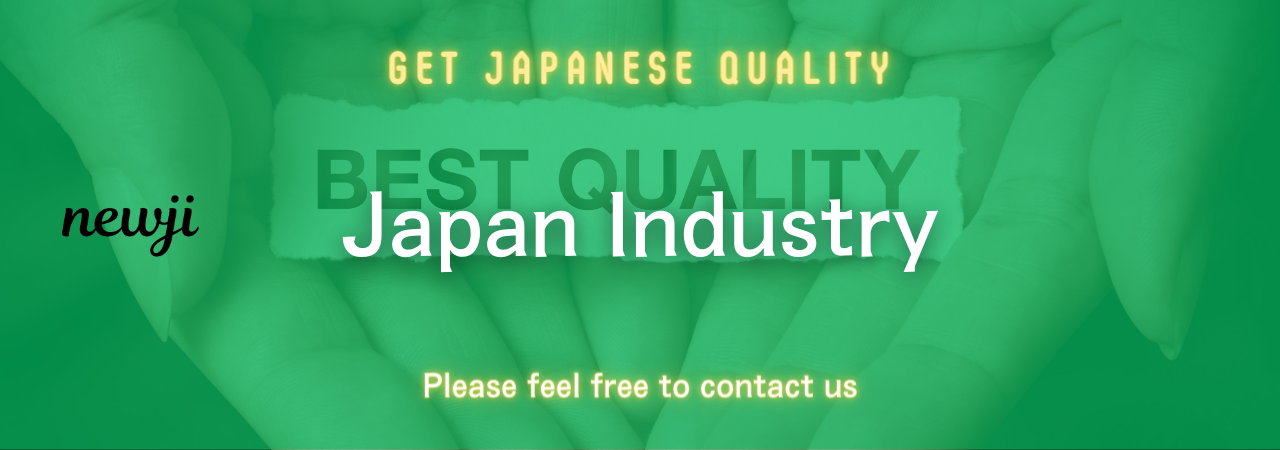
目次
Understanding Pressure Valves
Pressure valves play a crucial role in various industries by maintaining and controlling the pressure within systems.
Without these vital components, machines could experience malfunctions, leading to significant operational hazards.
In essence, pressure valves are the guardians of industrial safety and efficiency.
The Manufacturing Process of Pressure Valves
Design and Specifications
The first step in making a pressure valve involves design and specifications.
Engineers work closely with industry standards to ensure that the valve meets all required safety and performance criteria.
This process includes drafting detailed plans and creating prototypes using computer-aided design (CAD) software.
Material Selection
Selecting the right material is another crucial aspect of the manufacturing process.
Typically, manufacturers use materials like stainless steel, brass, or plastics, each chosen for its ability to withstand specific pressures and chemical exposures.
The material selection impacts the valve’s durability, corrosion resistance, and overall performance.
Forging and Casting
Once the material is selected, the next step involves forging or casting it into the required shape.
Forging involves using high-pressure machinery to shape the metal, which enhances its strength and durability.
Casting, on the other hand, involves pouring molten metal into a mold to achieve the desired shape.
Both these methods ensure the initial creation of the valve body and its components.
Machining
Following forging or casting, the valve components undergo precision machining.
This step involves using various tools to achieve the exact dimensions and tolerances specified in the design.
CNC (Computer Numerical Control) machinery is often employed to ensure high accuracy and uniformity across all components.
Assembly
In the assembly phase, all the machined parts come together.
Skilled technicians ensure that each component fits perfectly, and they often use automated assembly lines to enhance efficiency and precision.
The assembly process includes attaching seals, springs, and other internal mechanisms that allow the valve to function correctly.
Testing
Once assembled, each pressure valve undergoes rigorous testing to ensure it performs as expected.
Manufacturers use various tests, including pressure tests, leak tests, and functional tests, to validate the valve’s reliability and safety.
Only those valves that pass all tests are deemed suitable for use in industrial applications.
Safety Improvements in Pressure Valves
Advanced Sealing Technology
One of the significant advancements in pressure valve technology is the development of improved sealing mechanisms.
Modern seals offer better resistance to wear and tear, extreme temperatures, and chemical exposure.
These advancements result in reduced leaks and enhanced safety over the valve’s lifespan.
Smart Sensors and Monitoring
The integration of smart sensors into pressure valves marks a significant leap forward in safety.
These sensors can monitor pressure in real-time and send alerts or even shut down systems if they detect anomalies.
This proactive monitoring helps prevent accidents and ensures that systems operate within safe parameters.
Enhanced Materials
Recent innovations in materials science have led to the development of more robust and durable materials for pressure valves.
These materials offer superior resistance to corrosion, high pressures, and extreme temperatures, thereby extending the life of the valve and minimizing the risk of failure.
Compliance with International Standards
Modern pressure valves are designed to comply with stringent international safety standards.
This compliance ensures that they meet the highest safety and performance criteria, providing peace of mind to industries that depend on them.
Standards such as ISO, ASME, and API provide guidelines and regulate the manufacturing process, ensuring that only the safest and most reliable valves are used.
The Future of Pressure Valve Manufacturing
3D Printing
The future of pressure valve manufacturing holds exciting potential, one of which is the use of 3D printing technologies.
3D printing allows the creation of complex geometries that are difficult or impossible to achieve with traditional manufacturing methods.
This technology can lead to more efficient valve designs, reduced production times, and lower costs.
Nanotechnology
Nanotechnology offers promising advancements in the materials used for pressure valves.
By incorporating nanoparticles into the materials, manufacturers can produce valves with enhanced strength, durability, and corrosion resistance.
These improvements can significantly increase the safety and longevity of pressure valves.
Internet of Things (IoT)
Connecting pressure valves to the Internet of Things (IoT) allows for more sophisticated monitoring and control.
IoT-enabled valves can communicate data about their status and performance to centralized control systems, enabling more effective predictive maintenance and operational efficiency.
This connectivity ensures that potential issues are identified and addressed before they result in system failures.
In conclusion, understanding the manufacturing process of pressure valves and the significant safety improvements in recent years is essential for appreciating their role in industrial safety and efficiency.
From initial design to final assembly and testing, every step is meticulously carried out to ensure that these vital components can withstand the demands of modern industry.
With ongoing advancements in materials, technology, and standards, the future of pressure valve manufacturing promises even greater innovations in both performance and safety.
資料ダウンロード
QCD調達購買管理クラウド「newji」は、調達購買部門で必要なQCD管理全てを備えた、現場特化型兼クラウド型の今世紀最高の購買管理システムとなります。
ユーザー登録
調達購買業務の効率化だけでなく、システムを導入することで、コスト削減や製品・資材のステータス可視化のほか、属人化していた購買情報の共有化による内部不正防止や統制にも役立ちます。
NEWJI DX
製造業に特化したデジタルトランスフォーメーション(DX)の実現を目指す請負開発型のコンサルティングサービスです。AI、iPaaS、および先端の技術を駆使して、製造プロセスの効率化、業務効率化、チームワーク強化、コスト削減、品質向上を実現します。このサービスは、製造業の課題を深く理解し、それに対する最適なデジタルソリューションを提供することで、企業が持続的な成長とイノベーションを達成できるようサポートします。
オンライン講座
製造業、主に購買・調達部門にお勤めの方々に向けた情報を配信しております。
新任の方やベテランの方、管理職を対象とした幅広いコンテンツをご用意しております。
お問い合わせ
コストダウンが利益に直結する術だと理解していても、なかなか前に進めることができない状況。そんな時は、newjiのコストダウン自動化機能で大きく利益貢献しよう!
(Β版非公開)