- お役立ち記事
- Manufacturing Process of Rear Bumpers and Durability Reinforcement
月間76,176名の
製造業ご担当者様が閲覧しています*
*2025年3月31日現在のGoogle Analyticsのデータより
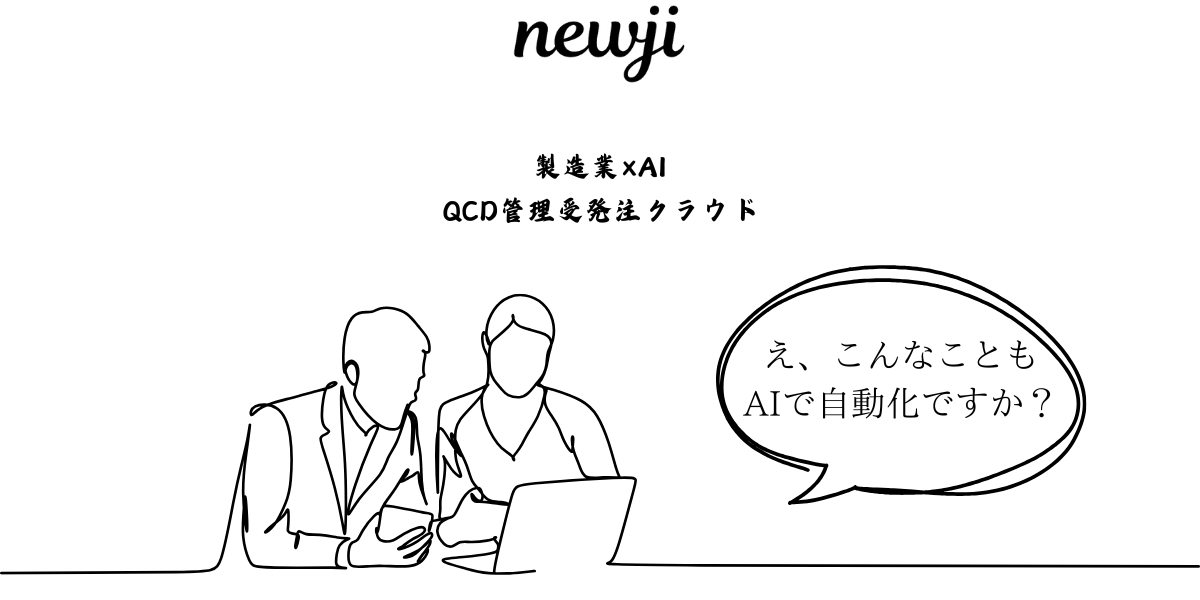
Manufacturing Process of Rear Bumpers and Durability Reinforcement
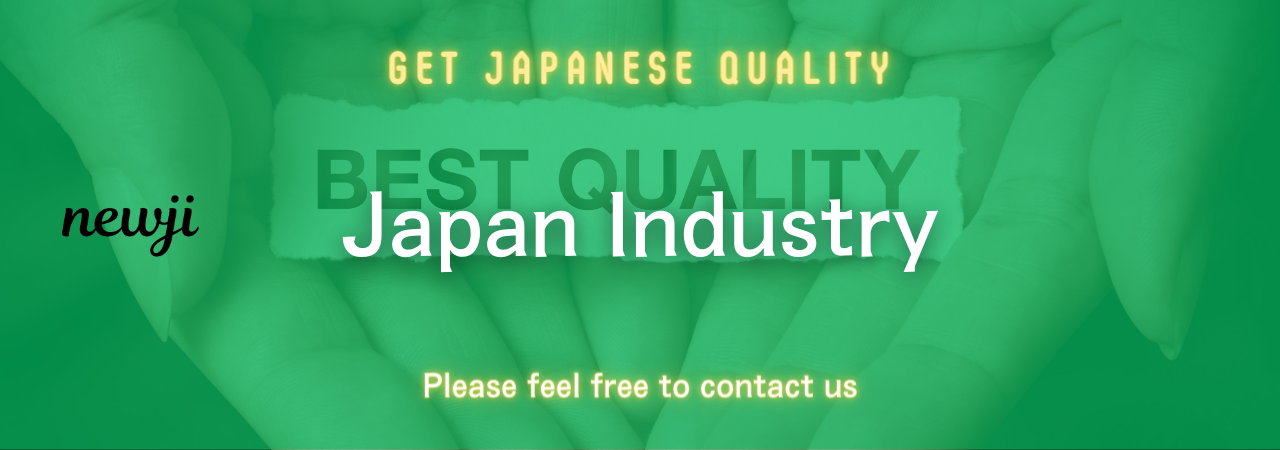
The rear bumper of a vehicle is an essential component that serves both an aesthetic and functional role.
It’s designed to protect the car from minor collisions and impacts.
Understanding the manufacturing process of rear bumpers and how they are reinforced for durability can provide valuable insights into automotive engineering.
目次
The Basics of Rear Bumper Manufacturing
Manufacturing a rear bumper begins with design and material selection.
Automakers use various materials, including plastic, steel, and aluminum, to ensure the bumper meets safety and performance standards.
Design and Material Selection
The design process starts with computer-aided design (CAD) software.
Engineers create a digital model of the bumper, which includes precise dimensions and structural details.
Once the design is finalized, the next step is choosing the material.
Thermoplastic Polyolefins (TPOs) and thermoplastic elastomers (TPEs) are commonly used materials for plastic bumpers.
These materials are flexible, lightweight, and can absorb impacts efficiently.
For higher-end vehicles, aluminum or steel may be used, offering greater durability and rigidity.
Injection Molding Process
For plastic bumpers, the injection molding process is employed.
This involves heating pellets of the chosen material until they melt.
The molten material is then injected into a mold, which shapes it into the form of a bumper.
The mold is designed with precision to ensure that the final product meets the required specifications.
Once the material cools and solidifies, it is removed from the mold.
Any excess material, known as flash, is trimmed away.
Die-Casting for Metal Bumpers
For metal bumpers, die-casting is the preferred method.
In this process, molten metal is poured into a die – a specialized mold made from steel.
High pressure is applied to ensure the metal fills every cavity of the die, resulting in a precise shape.
After the metal cools and hardens, the bumper is extracted from the die, and any excess material is removed through machining.
The final product is then polished to remove rough edges and achieve a smooth finish.
Durability Reinforcement Techniques
Ensuring that rear bumpers are durable and capable of withstanding impacts is a critical aspect of the manufacturing process.
Several reinforcement techniques are employed to enhance the strength and longevity of rear bumpers.
Internal Reinforcements
One common method is the use of internal reinforcements.
These are typically metal or composite elements inserted within the bumper structure.
They provide extra strength and rigidity, ensuring that the bumper can withstand higher impacts without deforming.
For plastic bumpers, a metal reinforcement bar, also known as a crash bar, is often integrated into the design.
This bar absorbs and distributes the force of an impact, reducing the stress on the plastic shell and protecting the vehicle’s frame.
Energy Absorption Features
Energy absorption features are another vital aspect of rear bumper design.
These include crumple zones and collapsible brackets that deform in a controlled manner during a collision.
By absorbing the energy of an impact, these features minimize damage to the vehicle and ensure the safety of its occupants.
Foam inserts are also used to enhance energy absorption.
These inserts are placed between the bumper cover and the reinforcement bar.
In the event of a collision, the foam compresses, absorbing and dissipating the impact energy.
Advanced Material Technologies
Advancements in material technologies have greatly contributed to bumper durability.
For instance, high-strength plastics reinforced with glass or carbon fibers are now being used.
These materials offer greater resistance to impacts while maintaining a lightweight profile.
Metal bumpers are also benefiting from new alloy compositions that provide enhanced strength without adding significant weight.
These alloys are tested rigorously to ensure they meet safety standards and performance requirements.
Quality Control and Testing
The final step in the manufacturing process involves rigorous quality control and testing to ensure that the rear bumpers meet the required safety and durability standards.
This is an essential phase to confirm that the bumpers can perform effectively in real-world conditions.
Impact Testing
One of the primary tests conducted on rear bumpers is impact testing.
This involves subjecting the bumper to various impact scenarios to assess its performance.
High-speed and low-speed collision tests are performed to determine how well the bumper absorbs and dissipates impact energy.
Computer simulations are also used to predict the behavior of the bumper under different impact conditions.
These simulations help identify potential weaknesses in the design and enable engineers to make necessary adjustments.
Environmental Testing
Rear bumpers must withstand a range of environmental conditions, including extreme temperatures, humidity, and exposure to chemicals.
Environmental testing subjects the bumpers to these conditions to ensure they maintain their integrity and performance over time.
This includes UV testing to assess the bumper’s resistance to sunlight and prevent fading or cracking.
Salt spray testing is also conducted to evaluate the bumper’s resistance to corrosion, especially for metal components.
Conclusion
The manufacturing process of rear bumpers is intricate and involves several stages, from design and material selection to reinforcement and quality testing.
Each step is crucial to ensuring that the final product is not only aesthetically pleasing but also capable of protecting the vehicle and its occupants.
With advancements in materials and technology, rear bumpers have become more robust and efficient in absorbing impacts.
Understanding this process highlights the importance of continuous innovation in automotive safety and design.
資料ダウンロード
QCD管理受発注クラウド「newji」は、受発注部門で必要なQCD管理全てを備えた、現場特化型兼クラウド型の今世紀最高の受発注管理システムとなります。
ユーザー登録
受発注業務の効率化だけでなく、システムを導入することで、コスト削減や製品・資材のステータス可視化のほか、属人化していた受発注情報の共有化による内部不正防止や統制にも役立ちます。
NEWJI DX
製造業に特化したデジタルトランスフォーメーション(DX)の実現を目指す請負開発型のコンサルティングサービスです。AI、iPaaS、および先端の技術を駆使して、製造プロセスの効率化、業務効率化、チームワーク強化、コスト削減、品質向上を実現します。このサービスは、製造業の課題を深く理解し、それに対する最適なデジタルソリューションを提供することで、企業が持続的な成長とイノベーションを達成できるようサポートします。
製造業ニュース解説
製造業、主に購買・調達部門にお勤めの方々に向けた情報を配信しております。
新任の方やベテランの方、管理職を対象とした幅広いコンテンツをご用意しております。
お問い合わせ
コストダウンが利益に直結する術だと理解していても、なかなか前に進めることができない状況。そんな時は、newjiのコストダウン自動化機能で大きく利益貢献しよう!
(β版非公開)