- お役立ち記事
- Manufacturing Process of Relief Valves and Overpressure Protection Improvement
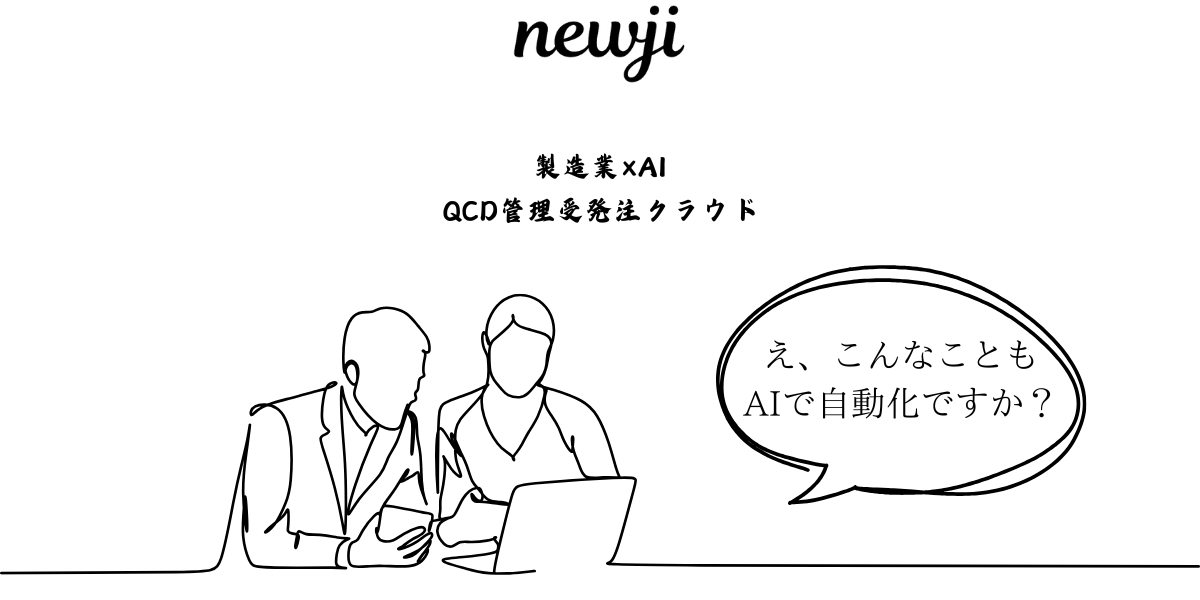
Manufacturing Process of Relief Valves and Overpressure Protection Improvement
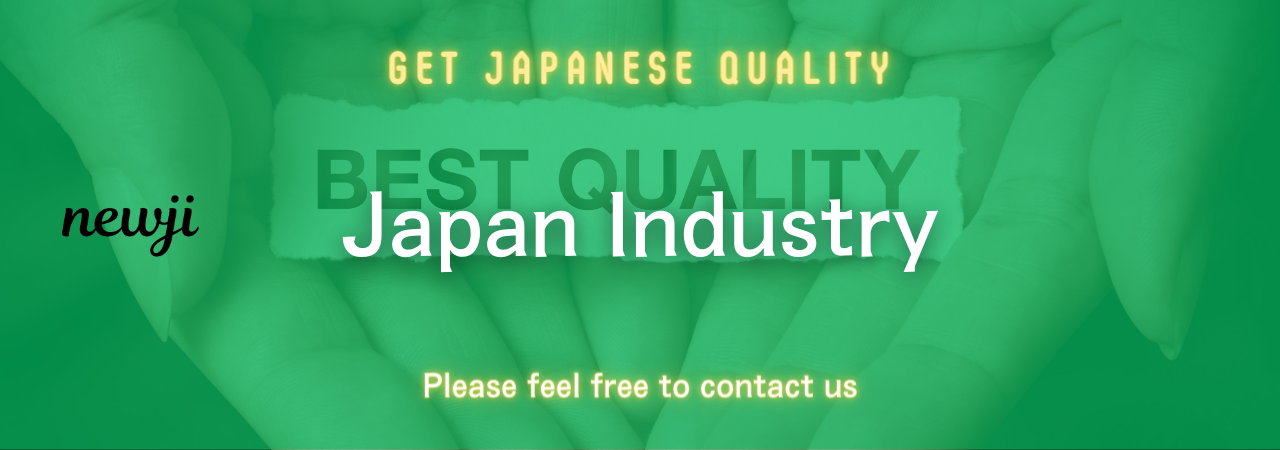
Relief valves are essential components in various industrial applications.
They serve the crucial role of safeguarding equipment and personnel from the dangers of overpressure.
In this article, we’ll delve into the manufacturing process of relief valves and explore ways to improve overpressure protection.
目次
Understanding Relief Valves
Relief valves are safety devices designed to relieve excess pressure in a system.
They automatically discharge fluid or gas when the pressure exceeds a predetermined limit, ensuring that the system operates within safe parameters.
This prevents potential damage to equipment, thus averting costly accidents and downtimes.
Materials Used in Manufacturing
Metal Alloys
The primary materials used in the construction of relief valves are metal alloys.
Stainless steel, carbon steel, and brass are commonly used due to their high strength, corrosion resistance, and durability.
Elastomers and Plastics
In addition to metal alloys, elastomers and plastics are used for seals and gaskets within relief valves.
These materials ensure a tight seal, preventing leaks under high-pressure conditions.
Examples include Teflon, Viton, and nitrile rubber.
Design and Engineering
Initial Design
The design phase begins with understanding the specific requirements of the system where the relief valve will be used.
Engineers assess factors such as temperature, pressure, and fluid type to determine the appropriate design specifications.
CAD software is often employed to create detailed models of the valve.
Prototyping
Once the initial design is complete, a prototype is created.
This prototype undergoes rigorous testing to identify any design flaws and to ensure that it meets performance expectations.
Adjustments are made as necessary until the prototype performs optimally.
Manufacturing Process
Casting and Machining
The manufacturing process begins with casting, where molten metal is poured into molds to form the basic shape of the valve.
After casting, the components undergo machining to achieve precise dimensions and smooth surfaces.
Lathes, milling machines, and CNC machines are commonly used for this purpose.
Assembly
After machining, the components are assembled.
This process involves careful alignment and fitting of parts, including the valve body, spring, and sealing elements.
Assembly technicians ensure that all components are correctly positioned to guarantee proper functioning.
Inspection and Testing
Once assembled, each relief valve undergoes thorough inspection and testing.
Pressure tests are conducted to ensure that the valve opens and closes at the specified set pressure.
Leak tests check for any potential leaks that could compromise the valve’s performance.
Improving Overpressure Protection
Regular Maintenance
One of the most effective ways to improve overpressure protection is through regular maintenance.
Routine inspections and cleaning help to identify and address wear and tear before it leads to failure.
Replacing worn-out components in a timely manner enhances the reliability of relief valves.
Advanced Materials
Incorporating advanced materials can significantly enhance the performance of relief valves.
Modern alloys and high-performance polymers offer superior strength and corrosion resistance, extending the lifespan of valves in demanding environments.
Smart Technology Integration
With the advent of Industry 4.0, integrating smart technology into relief valves has become increasingly feasible.
Sensors and monitoring systems can be installed to provide real-time data on valve performance.
This enables predictive maintenance and quick responses to potential issues, minimizing the risk of overpressure incidents.
Training and Certification
Proper Training
Ensuring that personnel are well-trained in the operation and maintenance of relief valves is crucial for effective overpressure protection.
Training programs should cover the basics of valve operation, maintenance procedures, and safety protocols.
Certification
Certification programs for personnel handling relief valves can further enhance their competence.
Certified professionals are better equipped to handle the complexities of valve maintenance and troubleshooting, reducing the likelihood of failures.
The Future of Relief Valves
Innovation and Research
The future of relief valves lies in continuous innovation and research.
Advancements in material science, fluid dynamics, and manufacturing techniques will lead to the development of more robust and efficient relief valves.
Regulations and Standards
Stricter regulations and standards will drive the industry towards higher quality and performance benchmarks.
Compliance with these regulations ensures that relief valves provide reliable overpressure protection in all applications.
Relief valves play a crucial role in maintaining the safety and efficiency of industrial systems.
By understanding their manufacturing process and exploring ways to improve overpressure protection, we can ensure that these essential components continue to perform at their best.
Regular maintenance, advanced materials, smart technology, and proper training are key factors in achieving this goal.
資料ダウンロード
QCD調達購買管理クラウド「newji」は、調達購買部門で必要なQCD管理全てを備えた、現場特化型兼クラウド型の今世紀最高の購買管理システムとなります。
ユーザー登録
調達購買業務の効率化だけでなく、システムを導入することで、コスト削減や製品・資材のステータス可視化のほか、属人化していた購買情報の共有化による内部不正防止や統制にも役立ちます。
NEWJI DX
製造業に特化したデジタルトランスフォーメーション(DX)の実現を目指す請負開発型のコンサルティングサービスです。AI、iPaaS、および先端の技術を駆使して、製造プロセスの効率化、業務効率化、チームワーク強化、コスト削減、品質向上を実現します。このサービスは、製造業の課題を深く理解し、それに対する最適なデジタルソリューションを提供することで、企業が持続的な成長とイノベーションを達成できるようサポートします。
オンライン講座
製造業、主に購買・調達部門にお勤めの方々に向けた情報を配信しております。
新任の方やベテランの方、管理職を対象とした幅広いコンテンツをご用意しております。
お問い合わせ
コストダウンが利益に直結する術だと理解していても、なかなか前に進めることができない状況。そんな時は、newjiのコストダウン自動化機能で大きく利益貢献しよう!
(Β版非公開)