- お役立ち記事
- Manufacturing Process of Ride-On Toys and Safety Standard Design
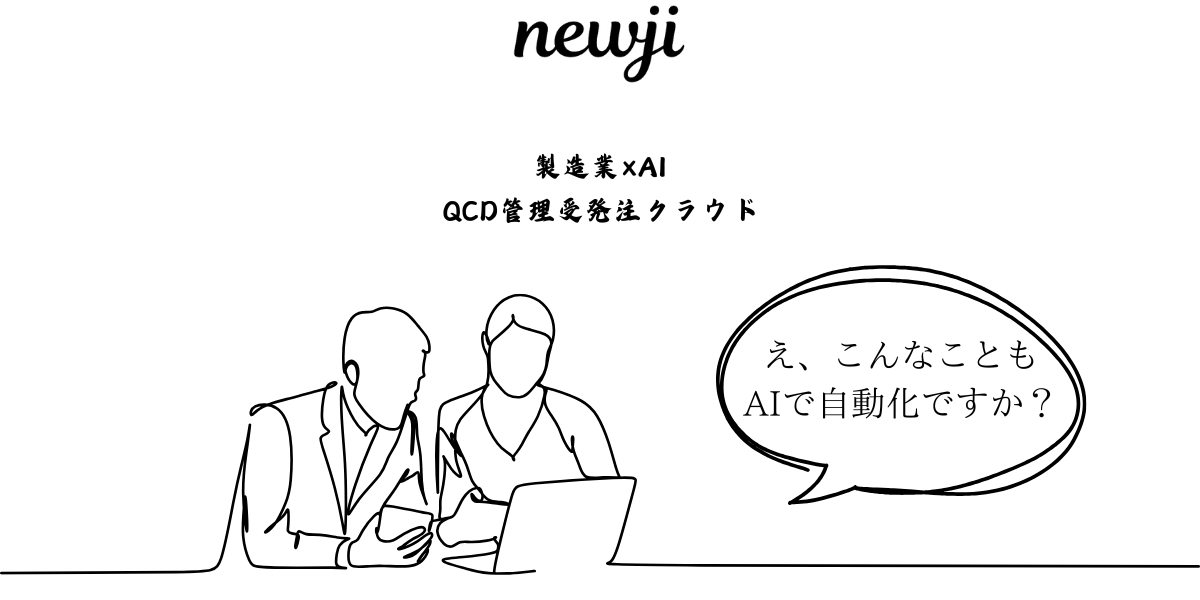
Manufacturing Process of Ride-On Toys and Safety Standard Design
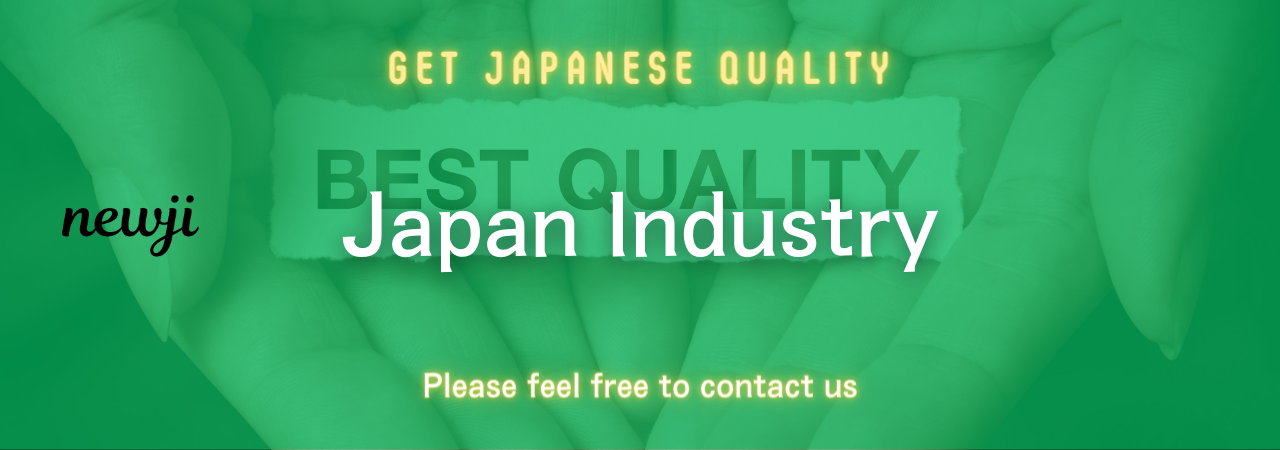
Ride-on toys are a cherished part of childhood, providing both fun and educational experiences for kids.
These toys come in various forms, from simple rocking horses to battery-powered mini cars.
But have you ever wondered what goes into making these beloved playthings and ensuring they are safe for children?
In this article, we will explore the manufacturing process of ride-on toys and the crucial safety standards that designers must adhere to.
目次
Understanding the Materials
The first step in creating ride-on toys is selecting the appropriate materials.
Manufacturers usually choose between plastic, metal, and wood, depending on the type of ride-on toy.
Plastic Ride-On Toys
Plastic is a popular choice for ride-on toys due to its durability, versatility, and cost-effectiveness.
High-density polyethylene (HDPE) and polypropylene (PP) are commonly used plastics because they are sturdy and resistant to impact.
Metal Ride-On Toys
Metal ride-on toys, typically made from steel or aluminum, are known for their strength and durability.
These materials are often used for more robust toys like scooters and bicycles.
Wooden Ride-On Toys
Wooden ride-on toys bring a classic and timeless appeal.
Manufacturers use high-quality hardwoods such as beech, maple, and oak to ensure longevity and safety.
The Design Phase
Once the materials are chosen, the design phase begins.
This stage involves creating detailed plans and prototypes to ensure the toy is both fun and safe to play with.
Conceptualization and Sketches
Designers start by brainstorming ideas and making preliminary sketches.
These sketches help visualize the toy’s form and function.
Computer-Aided Design (CAD)
After sketching, designers create detailed 3D models using computer-aided design (CAD) software.
This allows for precise visualization and modification before production begins.
Prototyping
Prototypes are then made to test the toy’s design and functionality.
These prototypes undergo rigorous testing to identify potential issues and areas for improvement.
Manufacturing Process
Once the design is finalized, the manufacturing process begins.
This stage involves several steps to bring the ride-on toy to life.
Injection Molding (For Plastic Toys)
In the case of plastic ride-on toys, injection molding is commonly used.
Molten plastic is injected into molds to create the different parts of the toy.
Once cooled, these parts are assembled to form the final product.
Metal Fabrication (For Metal Toys)
Metal ride-on toys are made using various fabrication techniques such as cutting, bending, and welding.
These processes shape the metal into the required components, which are then assembled and painted if necessary.
Woodwork (For Wooden Toys)
Wooden ride-on toys are crafted using CNC machines and hand tools.
Each piece is sanded, painted, and assembled to create the finished toy.
Ensuring Safety Standards
Safety is paramount when it comes to children’s toys.
Manufacturers must adhere to stringent safety standards to ensure their products are safe for use.
Material Safety
All materials used in ride-on toys must be non-toxic and free from harmful chemicals.
This ensures that even if a child comes into contact with or ingests parts of the toy, they will not be harmed.
Structural Integrity
The structural integrity of ride-on toys is crucial to prevent accidents.
Products must be built to support the weight and activity level of children without breaking or collapsing.
Small Parts and Choking Hazards
Manufacturers must ensure that ride-on toys do not have small parts that can detach and pose choking risks.
This involves rigorous testing to ensure all components remain securely fastened.
Sharp Edges and Points
All ride-on toys must be free from sharp edges and points to prevent cuts and injuries.
Edges are smoothed, and any potential hazards are eliminated during production.
Stability
Stability is another critical aspect of safety.
Toys must be designed to remain upright during use to prevent tipping and falls.
This involves testing the toy’s balance and making necessary adjustments to the design.
Quality Control and Testing
Before ride-on toys hit the market, they must undergo extensive quality control and testing.
Factory Inspections
Manufacturers conduct regular inspections to ensure that all production processes meet safety standards.
This includes checking the quality of materials, assembly methods, and final products.
Third-Party Testing
Many companies send their ride-on toys to third-party testing labs for additional scrutiny.
These labs perform a series of tests to verify that the toys meet all relevant safety standards.
Field Testing
Some manufacturers conduct field testing, where children use the toys in supervised settings.
This provides real-world feedback about the toy’s functionality and safety.
Packaging and Labeling
Once ride-on toys pass all safety tests, they are ready to be packaged and labeled.
Clear and informative labels are essential to guide consumers in proper use and maintenance.
Age Recommendations
Packaging must include age recommendations to ensure that the toy is suitable for the intended age group.
This helps prevent inappropriate use by younger children.
Usage Instructions
Clear usage instructions are provided to help parents and caregivers understand how to assemble and use the toy safely.
Safety Warnings
All potential hazards and safety warnings must be clearly indicated on the packaging.
This includes warnings about choking hazards, weight limits, and supervision requirements.
Ride-on toys bring joy and excitement to children around the world.
Understanding the detailed manufacturing process and the rigorous safety standards involved can provide peace of mind to parents and caregivers.
By prioritizing safety from design to distribution, manufacturers ensure that children can enjoy these toys without compromising their well-being.
資料ダウンロード
QCD調達購買管理クラウド「newji」は、調達購買部門で必要なQCD管理全てを備えた、現場特化型兼クラウド型の今世紀最高の購買管理システムとなります。
ユーザー登録
調達購買業務の効率化だけでなく、システムを導入することで、コスト削減や製品・資材のステータス可視化のほか、属人化していた購買情報の共有化による内部不正防止や統制にも役立ちます。
NEWJI DX
製造業に特化したデジタルトランスフォーメーション(DX)の実現を目指す請負開発型のコンサルティングサービスです。AI、iPaaS、および先端の技術を駆使して、製造プロセスの効率化、業務効率化、チームワーク強化、コスト削減、品質向上を実現します。このサービスは、製造業の課題を深く理解し、それに対する最適なデジタルソリューションを提供することで、企業が持続的な成長とイノベーションを達成できるようサポートします。
オンライン講座
製造業、主に購買・調達部門にお勤めの方々に向けた情報を配信しております。
新任の方やベテランの方、管理職を対象とした幅広いコンテンツをご用意しております。
お問い合わせ
コストダウンが利益に直結する術だと理解していても、なかなか前に進めることができない状況。そんな時は、newjiのコストダウン自動化機能で大きく利益貢献しよう!
(Β版非公開)