- お役立ち記事
- Manufacturing Process of Scales and Improving Measurement Accuracy
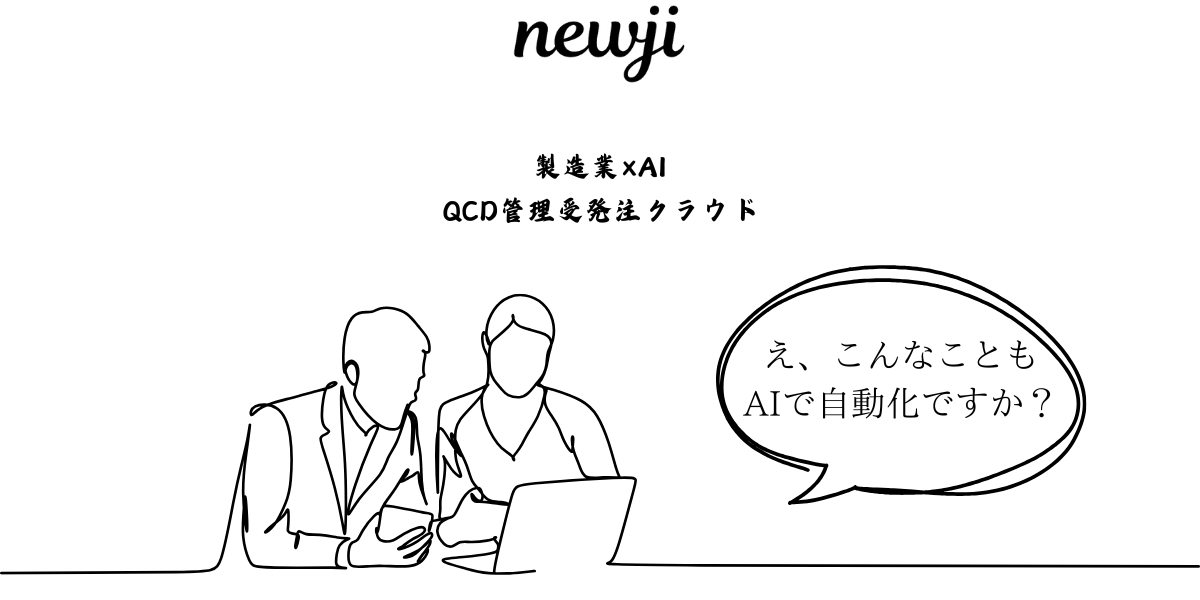
Manufacturing Process of Scales and Improving Measurement Accuracy
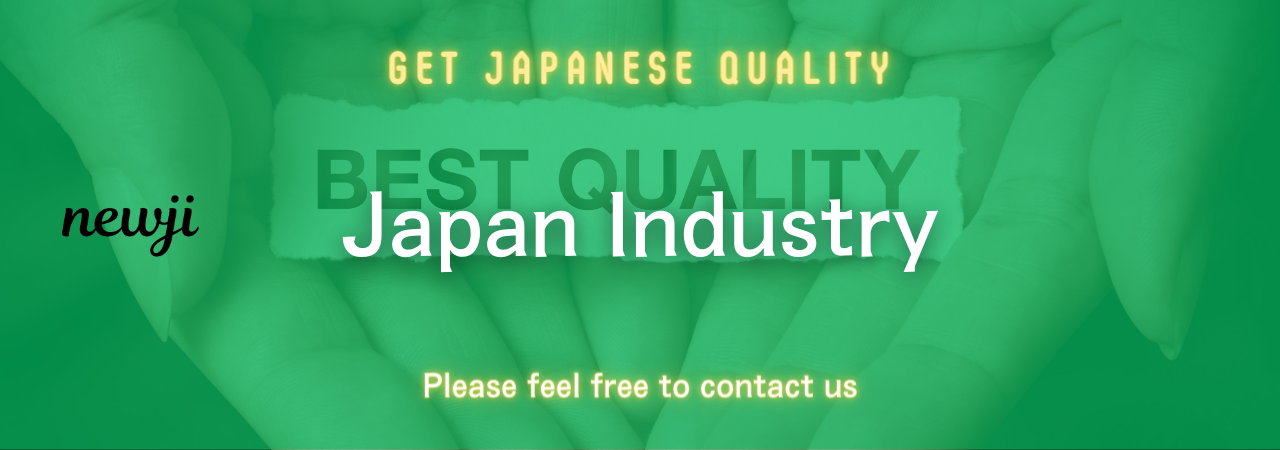
When you want to weigh something accurately, the scales you use are essential.
But have you ever wondered how these scales are made?
Understanding the manufacturing process of scales can help you appreciate the technology behind these everyday objects.
In this article, we will delve into how scales are made and how their measurement accuracy can be improved.
目次
Components of a Scale
Load Cell
One of the most critical components of a scale is the load cell.
Load cells convert the weight into an electrical signal.
There are various types of load cells, but strain gauge load cells are the most common.
These consist of a metal structure that deforms when weight is applied.
The deformation changes the electrical resistance, converting the applied force into an electrical signal.
Display
Almost all modern scales have a digital display.
The display takes the electrical signal from the load cell and converts it into a readable weight measure.
Displays often show weight in different units, like pounds, kilograms, or grams.
High-quality displays are clear and easy to read, even in different lighting conditions.
Microcontroller
The microcontroller is the brain of the scale.
It processes the electrical signals from the load cell and calculates the weight.
Advanced microcontrollers can perform additional functions, like data storage and connectivity to other devices.
Some scales are capable of sending the measurements to smartphones or computers, enabling more advanced uses.
Manufacturing Process
The process of making a scale involves several steps:
design, material selection, fabrication, assembly, and quality testing.
Here, we will go through each step in detail.
Design
The design phase begins with understanding the requirements of the scale.
Will it be used in a kitchen, a lab, or an industrial setting?
Each application might require different features like capacity, precision, and durability.
Designers use software to create blueprints for the scale, considering all these factors.
Material Selection
The materials chosen significantly affect the scale’s performance and durability.
High-quality metals are commonly used for load cells to ensure they can withstand substantial weights without deforming permanently.
Plastic or glass may be used for other components like the display housing.
Fabrication
Once the design is finalized and materials are selected, the fabrication phase begins.
Specialized machinery cuts, shapes, and assembles the metal parts.
For the load cells, precision is key.
Any slight deviation can affect the scale’s accuracy.
The metal parts are cleaned and assembled to prevent any contamination or defects.
Assembly
In the assembly stage, various components are put together.
The load cell, display, and microcontroller are carefully integrated into a single unit.
Automated machines or skilled technicians may perform this task, depending on the scale’s complexity.
Wiring and other minute details are handled with care so that the electronic components function correctly together.
Quality Testing
To ensure that the scales are accurate and durable, rigorous quality testing is conducted.
This stage may involve subjecting the scales to various weights and environmental conditions.
Scales are calibrated and recalibrated to guarantee precision.
Manufacturers often perform drop tests to make sure the scale will work even if it gets accidentally dropped.
Improving Measurement Accuracy
Calibration
Calibration is perhaps the most crucial step in ensuring measurement accuracy.
Regular calibration checks are essential, especially for scales used in professional settings where precision is critical.
Advanced scales come with auto-calibration features that make them incredibly reliable.
Environmental Factors
Environmental factors like temperature and humidity can affect scale accuracy.
It is essential to place the scale on a flat, stable surface.
Some scales come with built-in systems to compensate for these environmental factors, improving their accuracy.
Software and Firmware
Modern scales are often equipped with sophisticated software and firmware.
These programs help in fine-tuning the measurements, making them more precise.
Updates to software and firmware can improve the scale’s performance over time.
Users can download these updates easily, ensuring their scales remain accurate.
Maintenance
Regular maintenance is vital for keeping a scale in top working condition.
Components like load cells can wear out over time and may need replacement.
Manufacturers usually provide guidelines for maintaining the scale.
Following these guidelines ensures long-term accuracy and reliability.
The Future of Scales
Technological advancements continue to improve the design and functionality of scales.
Internet of Things (IoT) technology allows scales to connect to other devices, enhancing their utility.
Artificial Intelligence (AI) can offer real-time adjustments and constant calibration checks.
The future looks bright, as these advancements will make scales even more reliable and versatile.
In conclusion, the process of making a scale involves intricate steps, from design to quality testing.
Each component serves a crucial function, and the importance of calibration and regular maintenance cannot be overstated.
As technology advances, we can expect even greater accuracy and utility from our scales, making them indispensable tools in various fields.
資料ダウンロード
QCD調達購買管理クラウド「newji」は、調達購買部門で必要なQCD管理全てを備えた、現場特化型兼クラウド型の今世紀最高の購買管理システムとなります。
ユーザー登録
調達購買業務の効率化だけでなく、システムを導入することで、コスト削減や製品・資材のステータス可視化のほか、属人化していた購買情報の共有化による内部不正防止や統制にも役立ちます。
NEWJI DX
製造業に特化したデジタルトランスフォーメーション(DX)の実現を目指す請負開発型のコンサルティングサービスです。AI、iPaaS、および先端の技術を駆使して、製造プロセスの効率化、業務効率化、チームワーク強化、コスト削減、品質向上を実現します。このサービスは、製造業の課題を深く理解し、それに対する最適なデジタルソリューションを提供することで、企業が持続的な成長とイノベーションを達成できるようサポートします。
オンライン講座
製造業、主に購買・調達部門にお勤めの方々に向けた情報を配信しております。
新任の方やベテランの方、管理職を対象とした幅広いコンテンツをご用意しております。
お問い合わせ
コストダウンが利益に直結する術だと理解していても、なかなか前に進めることができない状況。そんな時は、newjiのコストダウン自動化機能で大きく利益貢献しよう!
(Β版非公開)