- お役立ち記事
- Manufacturing Process of Seat Belts and Safety Reinforcement
月間76,176名の
製造業ご担当者様が閲覧しています*
*2025年3月31日現在のGoogle Analyticsのデータより
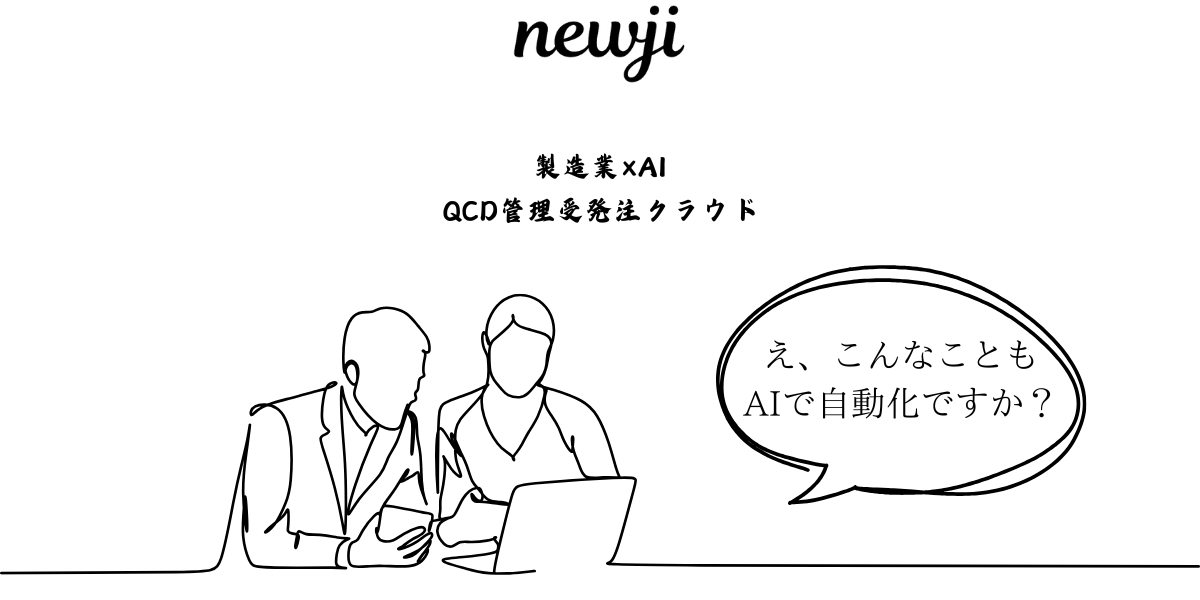
Manufacturing Process of Seat Belts and Safety Reinforcement
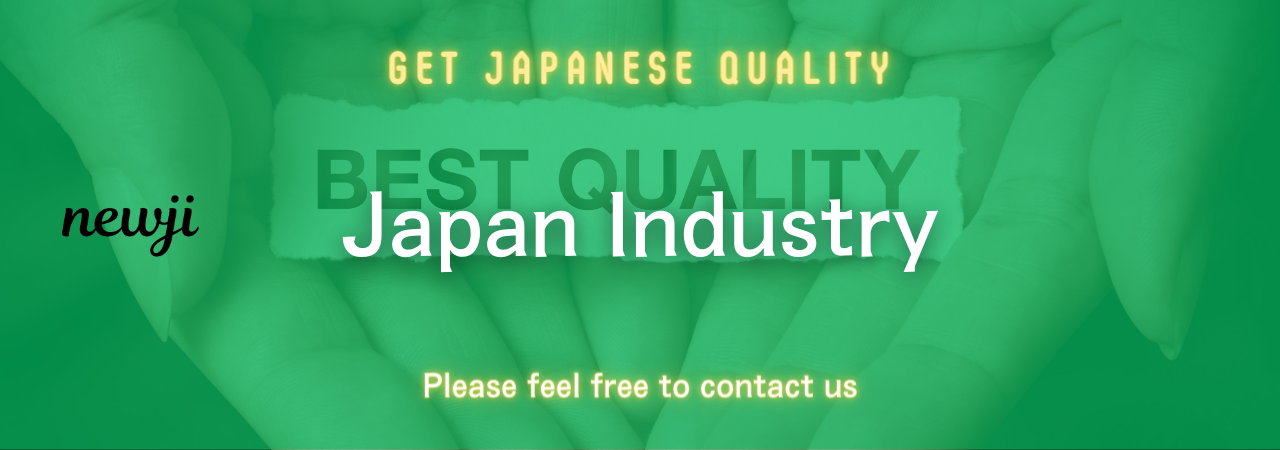
Seat belts are an essential safety feature in vehicles, saving countless lives by preventing severe injuries during accidents.
Understanding the manufacturing process of seat belts and safety reinforcement can help appreciate the complexity and effort that goes into creating these vital components.
Let’s dive into the different stages of manufacturing seat belts and safety reinforcements.
目次
Materials Used in Seat Belts
The primary material used for seat belts is high-strength polyester webbing.
This material is chosen due to its durability, tensile strength, and resistance to abrasion and UV rays.
The fibers are spun into yarn and then woven into fabric on special looms.
High-Strength Polyester Webbing: This is the most common material.
It is durable, strong, and resistant to wear and tear.
Stainless Steel and Plastic: Used for buckles and other hardware components.
Reinforcements: Made using high-strength steel or alloys to ensure maximum protection.
The Weaving Process
The weaving process is critical in manufacturing seat belts.
The polyester yarns are woven together to form a tightly woven fabric.
This fabric must meet stringent safety standards and undergo rigorous testing to ensure it can withstand high loads and resist wear.
Step 1: Yarn Preparation
The process begins with the preparation of polyester yarn.
The raw polyester fibers are spun into yarns using spinning machines.
These yarns are then wound onto bobbins, ready for the weaving process.
Step 2: Weaving the Webbing
The yarns are loaded onto specialized weaving looms, which interlace them to form a strong, durable webbing.
The looms create a tight weave pattern that ensures the fabric can withstand significant force during a collision.
Dyeing and Finishing
After the webbing is woven, it undergoes dyeing to achieve the desired color, typically black or gray.
The dyeing process ensures that the color penetrates evenly across the fabric and remains durable over time.
Step 1: Dyeing
The webbing is immersed in large dye baths, where it absorbs the desired color.
This process is carefully monitored to ensure consistency in color and quality.
The dyed webbing is then dried using large dryers.
Step 2: Finishing
Once dyed and dried, the webbing moves on to the finishing stage.
This involves applying special coatings that enhance the webbing’s durability, UV resistance, and resistance to fraying.
Various finishing techniques, such as heat setting and chemical treatments, are used to achieve the desired properties.
Manufacturing the Hardware Components
Seat belts consist of more than just webbing; they also include various hardware components like buckles, adjusters, and anchor points.
These components are usually made of stainless steel and high-strength plastic materials.
Step 1: Stamping and Forming
Metal components, such as buckles and anchor points, are manufactured using stamping and forming processes.
High-strength steel sheets are cut, stamped, and formed into the required shapes using specialized machinery.
Step 2: Plastic Injection Molding
Plastic components, such as adjusters and covers, are produced using injection molding.
In this process, molten plastic is injected into molds to create the desired shapes.
Once cooled and solidified, the plastic components are removed from the molds and undergo quality inspection.
Assembly of Seat Belts
The final step in the manufacturing process is assembling all the components.
This involves attaching the webbing to the hardware components and ensuring everything is securely fastened.
Step 1: Cutting and Stitching
The webbing is cut into the required lengths, and the edges are reinforced using stitching or heat sealing.
Specialized sewing machines are used to create strong, durable seams.
Step 2: Attaching Hardware
The hardware components, such as buckles and adjusters, are attached to the webbing.
This is done using high-strength stitching, riveting, or specialized fasteners to ensure the components are securely attached.
Quality Control and Testing
Quality control is a critical part of the manufacturing process.
Each seat belt undergoes rigorous testing to ensure it meets or exceeds safety standards.
Step 1: Visual Inspection
The first step in quality control is a visual inspection of the seat belts.
This involves checking the webbing for any defects, such as fraying or uneven dye, and inspecting the hardware for any flaws or damage.
Step 2: Load Testing
Each seat belt is subjected to load testing, where it is exposed to forces that simulate a collision.
This testing ensures that the seat belt can withstand high loads without failing.
Step 3: Environmental Testing
Environmental testing involves exposing the seat belts to various conditions, such as extreme temperatures, humidity, and UV light, to ensure they remain durable and effective over time.
Safety Reinforcements in Vehicles
Apart from seat belts, modern vehicles incorporate various safety reinforcements to enhance occupant protection.
These reinforcements are designed and manufactured to absorb and dissipate collision forces, minimizing the risk of injury.
Reinforced Steel Frames
The vehicle’s frame is reinforced with high-strength steel to provide a strong, rigid structure.
This helps to absorb and distribute impact forces during a collision.
Side Impact Beams
Side impact beams are installed in the doors and sides of the vehicle.
These beams are designed to absorb and distribute the force of a side collision, protecting occupants from intrusions.
Crumple Zones
Crumple zones are areas of the vehicle designed to deform and absorb energy during a collision.
These zones help to reduce the force transmitted to the occupants and minimize the risk of injury.
The process of manufacturing seat belts and safety reinforcements is a complex and meticulous one.
Each component is designed and tested to ensure maximum safety and effectiveness.
Appreciating the effort and technology involved can help us understand the crucial role these features play in keeping us safe on the roads.
資料ダウンロード
QCD管理受発注クラウド「newji」は、受発注部門で必要なQCD管理全てを備えた、現場特化型兼クラウド型の今世紀最高の受発注管理システムとなります。
ユーザー登録
受発注業務の効率化だけでなく、システムを導入することで、コスト削減や製品・資材のステータス可視化のほか、属人化していた受発注情報の共有化による内部不正防止や統制にも役立ちます。
NEWJI DX
製造業に特化したデジタルトランスフォーメーション(DX)の実現を目指す請負開発型のコンサルティングサービスです。AI、iPaaS、および先端の技術を駆使して、製造プロセスの効率化、業務効率化、チームワーク強化、コスト削減、品質向上を実現します。このサービスは、製造業の課題を深く理解し、それに対する最適なデジタルソリューションを提供することで、企業が持続的な成長とイノベーションを達成できるようサポートします。
製造業ニュース解説
製造業、主に購買・調達部門にお勤めの方々に向けた情報を配信しております。
新任の方やベテランの方、管理職を対象とした幅広いコンテンツをご用意しております。
お問い合わせ
コストダウンが利益に直結する術だと理解していても、なかなか前に進めることができない状況。そんな時は、newjiのコストダウン自動化機能で大きく利益貢献しよう!
(β版非公開)