- お役立ち記事
- Manufacturing Process of Spark Plugs and Ignition Performance Enhancement
月間76,176名の
製造業ご担当者様が閲覧しています*
*2025年3月31日現在のGoogle Analyticsのデータより
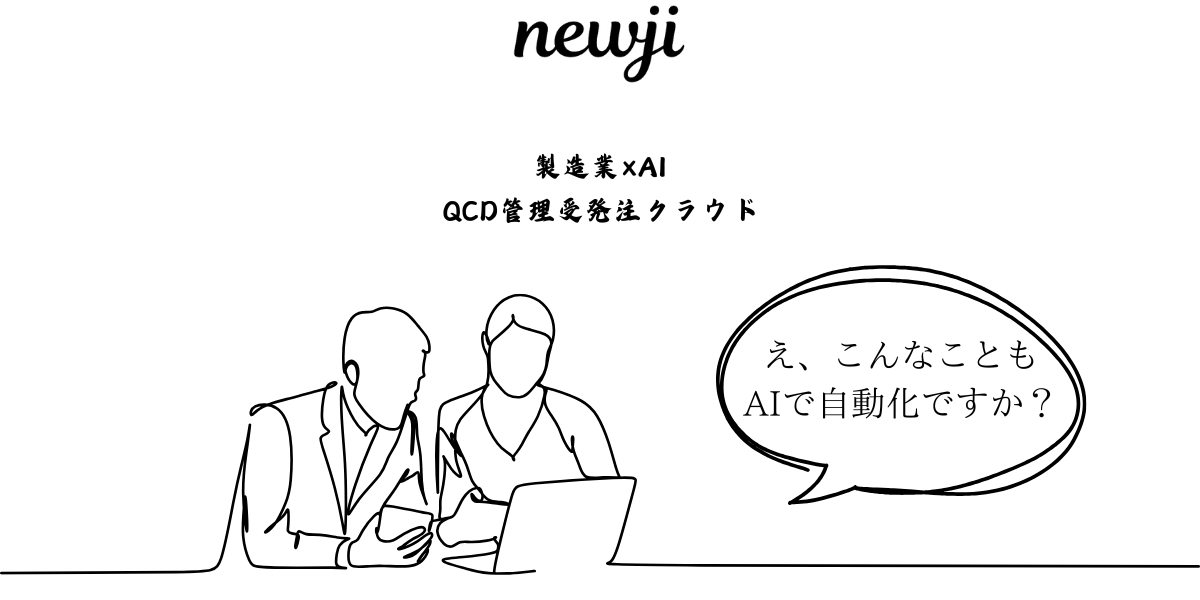
Manufacturing Process of Spark Plugs and Ignition Performance Enhancement
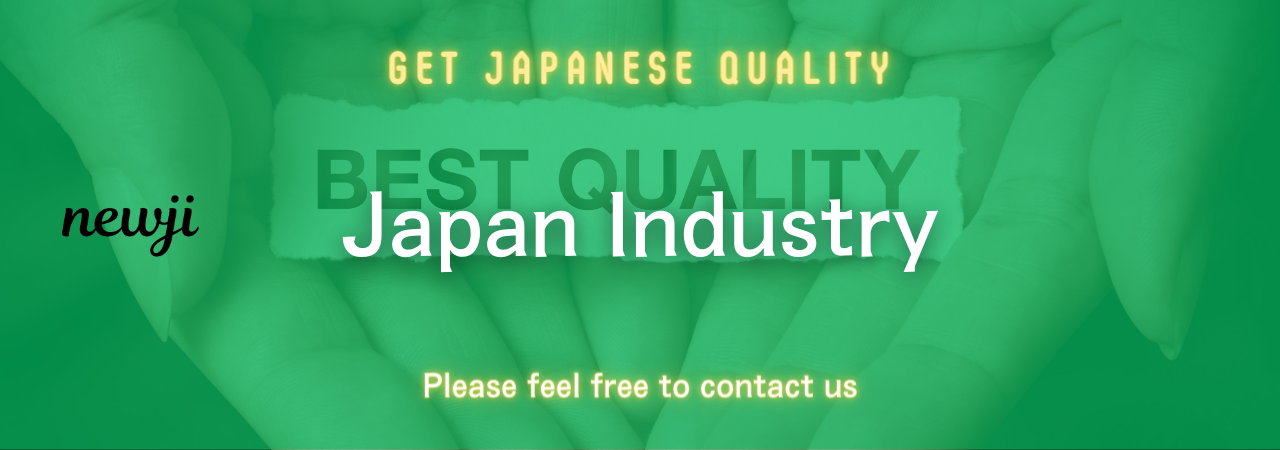
Spark plugs play a crucial role in the internal combustion engine by igniting the air-fuel mixture.
To ensure optimal engine performance, the manufacturing process of spark plugs must be meticulous.
In this article, we’ll explore the detailed steps involved in creating spark plugs and discuss techniques to enhance ignition performance.
目次
Materials Used in Spark Plug Manufacturing
The foundation of a high-quality spark plug lies in the selection of materials.
Typically, spark plugs are made of three primary components: the insulator, the center electrode, and the outer shell.
Ceramic Insulator
The insulator is made of high-purity alumina, which provides excellent electrical insulation.
Alumina’s high thermal conductivity helps dissipate heat effectively.
During manufacturing, powdered alumina is mixed with other additives to form a paste, which is then shaped into insulator bodies using isostatic pressing.
Center Electrode
The center electrode is often made of nickel alloy or precious metals like iridium and platinum.
These materials are chosen for their high melting points and corrosion resistance.
Precious metals ensure longevity and stable performance.
Outer Shell
The outer shell, also known as the metal body, is usually made of stainless steel.
Stainless steel offers strength and resistance to thermal and mechanical stress.
It also provides a good ground connection for the spark.
Step-by-Step Manufacturing Process
The manufacturing process involves several stages, each ensuring the quality and precision of the final product.
1. Insulator Preparation
The insulator paste is molded into cylindrical shapes using isostatic pressing.
These blanks are then sintered in a kiln at high temperatures to achieve the required hardness and strength.
After sintering, the insulators are machined to precise dimensions.
2. Electrode Production
For the center electrode, the nickel alloy or precious metal is drawn into fine wires.
These wires are then cut into the desired length and machined to form the electrode tip.
If precious metals are used, they are welded onto the nickel alloy core.
3. Shell Manufacturing
The stainless steel outer shell is formed through a process called cold extrusion.
In this method, stainless steel rods are forced through a die to achieve the required shape.
Threads are then machined into the shell to allow the spark plug to be screwed into the engine.
4. Assembly
The insulator, center electrode, and outer shell are carefully assembled.
The center electrode is inserted into the insulator, and the outer shell is then placed over the insulator.
A process called crimping ensures that all components are securely fastened together.
5. Sealing
Sealing is crucial to prevent gas leakage and ensure reliable performance.
A glass or ceramic sealant is applied between the insulator and the shell.
This sealant is then heated to form a hermetic seal.
6. Testing and Quality Control
Each spark plug undergoes rigorous testing to ensure it meets performance standards.
Tests include electrical resistance, heat resistance, and mechanical strength.
Only spark plugs that pass these stringent tests are deemed suitable for use.
Enhancing Ignition Performance
To maximize ignition performance, certain enhancements can be applied during the spark plug manufacturing process.
Using Precious Metals
Using precious metals like iridium and platinum for the center electrode significantly enhances performance.
These metals have high melting points, which allow for a finer electrode tip.
A finer tip reduces the voltage required for ignition, resulting in more efficient combustion.
Optimizing Electrode Gap
The gap between the center and ground electrodes is critical for proper ignition.
Manufacturers can optimize this gap to ensure a strong and consistent spark.
During the manufacturing process, precision tools are used to set the gap to exact specifications.
Multi-Ground Electrodes
Some spark plugs feature multiple ground electrodes.
This design provides several paths for the spark to travel, ensuring consistent ignition even under adverse conditions.
Multi-ground electrodes also distribute electrode wear, prolonging the life of the spark plug.
Advanced Insulator Coatings
Innovative coatings on the insulator can further enhance ignition performance.
For example, some manufacturers use yttrium oxide coatings to improve thermal conductivity and reduce heat retention.
Such coatings prevent pre-ignition and ensure stable performance.
Conclusion
The manufacturing process of spark plugs is a meticulous and intricate procedure.
From selecting high-quality materials to precision assembly and rigorous testing, each step ensures the production of reliable and efficient spark plugs.
By incorporating advanced materials and optimizing component design, ignition performance can be significantly enhanced, contributing to better engine efficiency and longevity.
Readers interested in more detailed information about the specific techniques and technologies employed in spark plug manufacturing should consult industry-specific resources or reach out to manufacturers directly.
Understanding the intricate production methods behind such crucial engine components can instill greater appreciation for the technology that powers our vehicles.
資料ダウンロード
QCD管理受発注クラウド「newji」は、受発注部門で必要なQCD管理全てを備えた、現場特化型兼クラウド型の今世紀最高の受発注管理システムとなります。
ユーザー登録
受発注業務の効率化だけでなく、システムを導入することで、コスト削減や製品・資材のステータス可視化のほか、属人化していた受発注情報の共有化による内部不正防止や統制にも役立ちます。
NEWJI DX
製造業に特化したデジタルトランスフォーメーション(DX)の実現を目指す請負開発型のコンサルティングサービスです。AI、iPaaS、および先端の技術を駆使して、製造プロセスの効率化、業務効率化、チームワーク強化、コスト削減、品質向上を実現します。このサービスは、製造業の課題を深く理解し、それに対する最適なデジタルソリューションを提供することで、企業が持続的な成長とイノベーションを達成できるようサポートします。
製造業ニュース解説
製造業、主に購買・調達部門にお勤めの方々に向けた情報を配信しております。
新任の方やベテランの方、管理職を対象とした幅広いコンテンツをご用意しております。
お問い合わせ
コストダウンが利益に直結する術だと理解していても、なかなか前に進めることができない状況。そんな時は、newjiのコストダウン自動化機能で大きく利益貢献しよう!
(β版非公開)