- お役立ち記事
- Manufacturing Process of Steering Wheels and Grip Performance Improvement
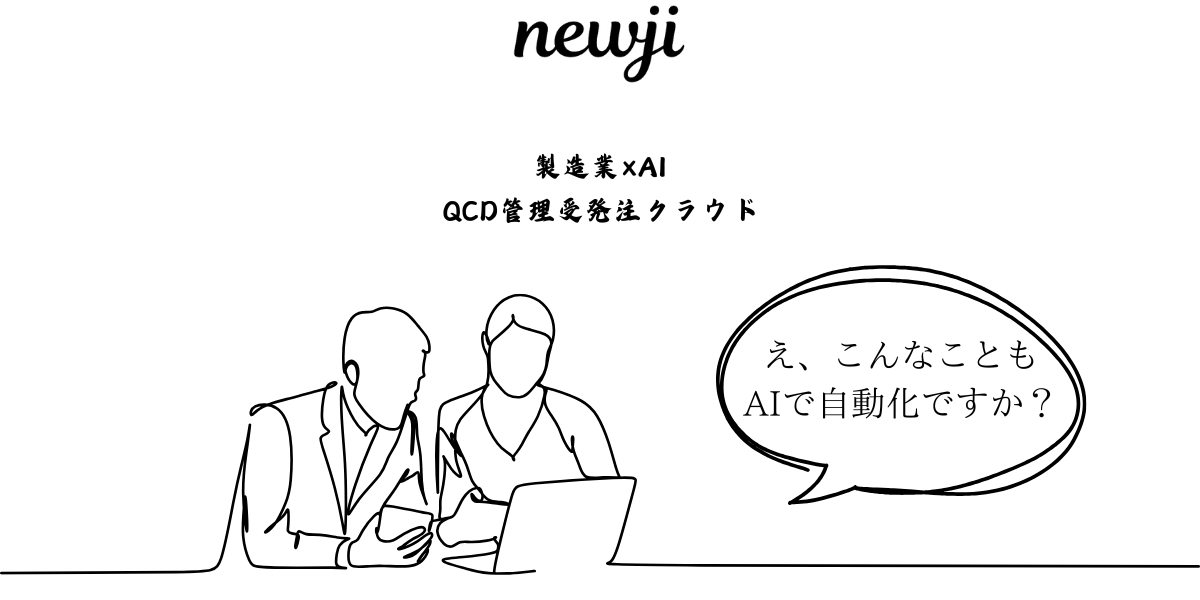
Manufacturing Process of Steering Wheels and Grip Performance Improvement
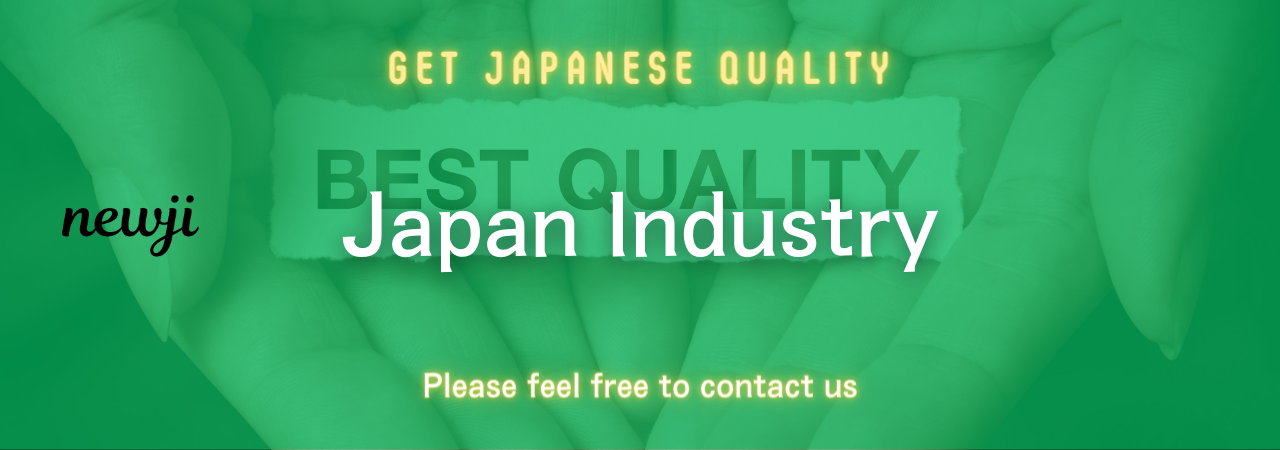
Steering wheels are essential components in any vehicle, providing drivers with control over their direction.
The process of manufacturing steering wheels involves multiple steps, each crucial to ensuring safety, reliability, and driver comfort.
In this article, we will explore the manufacturing process of steering wheels and discuss how to improve grip performance.
目次
The Basics of Steering Wheel Manufacturing
Design and Conceptualization
The manufacturing process begins with design and conceptualization.
Engineers and designers collaborate to create a blueprint that meets the functional and aesthetic needs of a vehicle.
This blueprint includes the size, shape, material selection, and any additional features such as buttons or heating elements.
Computer-Aided Design (CAD) software is commonly used to create detailed models and simulations, ensuring the design meets safety and ergonomic standards.
Material Selection
Material selection is a critical stage in the production of steering wheels.
Common materials include plastic, polyurethane, leather, and metal.
Plastic and polyurethane are typically used for the core structure due to their durability and lightweight properties.
Leather is often selected for its luxurious feel and aesthetic appeal, especially in high-end vehicles.
In some instances, wood or carbon fiber may be used for specialty or luxury models.
Each material is chosen based on factors such as cost, weight, durability, and driver experience.
Molding and Forming
Once the design and materials are finalized, the next step is molding and forming.
The core structure of a steering wheel is created using injection molding or compression molding techniques.
In injection molding, molten plastic or polyurethane is injected into a mold cavity, which is shaped like the steering wheel’s core.
Compression molding involves placing a pre-measured amount of material into a mold, where heat and pressure are applied to form the desired shape.
These processes ensure the core structure is strong and lightweight, meeting all safety standards.
Covering and Assembly
Applying the Covering
After molding, the core structure is covered with a material that enhances grip and comfort.
For leather-wrapped steering wheels, the leather is cut to size and sewn into a cover that fits snugly over the core.
This process requires precision to ensure a smooth, wrinkle-free finish.
The leather is often treated with special coatings to enhance durability and resistance to wear and tear.
For plastic or polyurethane coverings, a similar process is followed, but without the stitching.
The covering material is applied using adhesives and pressed into place to ensure a secure fit.
Adding Functional Elements
Many modern steering wheels come with additional functional elements such as control buttons, heating elements, and sensors.
These features are integrated into the design during the assembly process.
Control buttons allow drivers to manage various functions such as audio volume, cruise control, or phone calls without taking their hands off the wheel.
Heating elements provide added comfort during cold weather.
Sensors can monitor grip force or steering angle to enhance safety and driving experience.
All these elements require precise installation to ensure they function correctly and do not compromise the integrity of the wheel.
Final Assembly and Quality Inspection
The final assembly involves attaching all components together to form the complete steering wheel.
This includes mounting the core, covering, and any additional functional elements onto the steering column.
Once assembled, each steering wheel undergoes rigorous quality inspections.
These inspections check for defects, structural integrity, and functionality.
Automated machines and human inspectors work together to ensure each steering wheel meets the high standards required for vehicle safety and driver satisfaction.
Improving Grip Performance
Ergonomic Design
One way to improve grip performance is through ergonomic design.
An ergonomic steering wheel is shaped to fit comfortably in the driver’s hands, reducing strain and enhancing control.
Designers use hand anthropometry data to create contours and finger grooves that provide a natural grip.
An ergonomic design also ensures that the steering wheel’s diameter and thickness are suitable for a wide range of drivers, promoting a better driving experience.
Material Enhancements
The choice of materials can significantly impact grip performance.
Using high-quality leather or specially designed rubber can enhance the tactile feel and grip of a steering wheel.
These materials can be treated with anti-slip coatings to further improve grip, especially in wet or sweaty conditions.
Some manufacturers also use perforated or textured surfaces to increase friction and prevent slipping.
Advanced Grip Technologies
Technological advancements have introduced new ways to enhance grip performance.
For instance, some steering wheels come equipped with heating elements that can adjust the wheel’s temperature to optimal levels, improving grip and comfort in cold weather.
Another innovation is the use of capacitive touch sensors that can detect the presence of a driver’s hands.
These sensors can be linked to driver-assistance systems for added safety.
Additionally, steering wheels with adaptive grip surfaces that change texture based on driving conditions are being researched to provide the best possible grip at all times.
Conclusion
The manufacturing process of steering wheels involves meticulous planning, material selection, and precision engineering.
From design and molding to covering and assembly, each step is crucial in creating a safe and comfortable product.
Improving grip performance through ergonomic design, material enhancements, and advanced technologies ensures that drivers have the best possible control over their vehicles.
As technology continues to evolve, we can expect even more innovative solutions to enhance the functionality and comfort of steering wheels.
資料ダウンロード
QCD調達購買管理クラウド「newji」は、調達購買部門で必要なQCD管理全てを備えた、現場特化型兼クラウド型の今世紀最高の購買管理システムとなります。
ユーザー登録
調達購買業務の効率化だけでなく、システムを導入することで、コスト削減や製品・資材のステータス可視化のほか、属人化していた購買情報の共有化による内部不正防止や統制にも役立ちます。
NEWJI DX
製造業に特化したデジタルトランスフォーメーション(DX)の実現を目指す請負開発型のコンサルティングサービスです。AI、iPaaS、および先端の技術を駆使して、製造プロセスの効率化、業務効率化、チームワーク強化、コスト削減、品質向上を実現します。このサービスは、製造業の課題を深く理解し、それに対する最適なデジタルソリューションを提供することで、企業が持続的な成長とイノベーションを達成できるようサポートします。
オンライン講座
製造業、主に購買・調達部門にお勤めの方々に向けた情報を配信しております。
新任の方やベテランの方、管理職を対象とした幅広いコンテンツをご用意しております。
お問い合わせ
コストダウンが利益に直結する術だと理解していても、なかなか前に進めることができない状況。そんな時は、newjiのコストダウン自動化機能で大きく利益貢献しよう!
(Β版非公開)