- お役立ち記事
- Manufacturing Process of Temperature Sensors and Accuracy Enhancement
月間76,176名の
製造業ご担当者様が閲覧しています*
*2025年3月31日現在のGoogle Analyticsのデータより
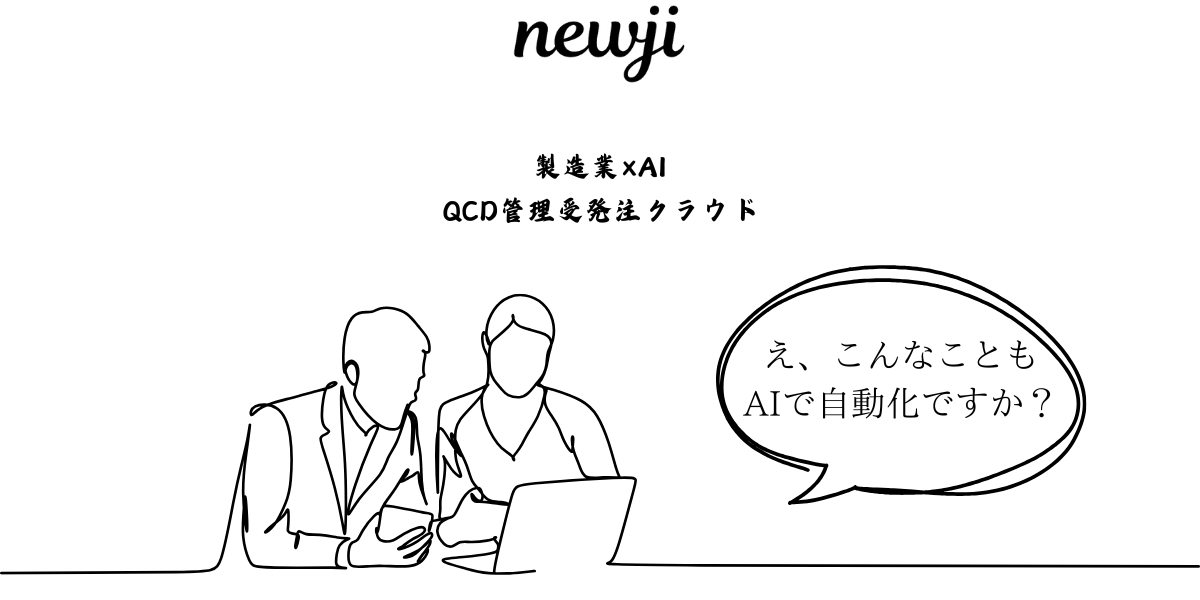
Manufacturing Process of Temperature Sensors and Accuracy Enhancement
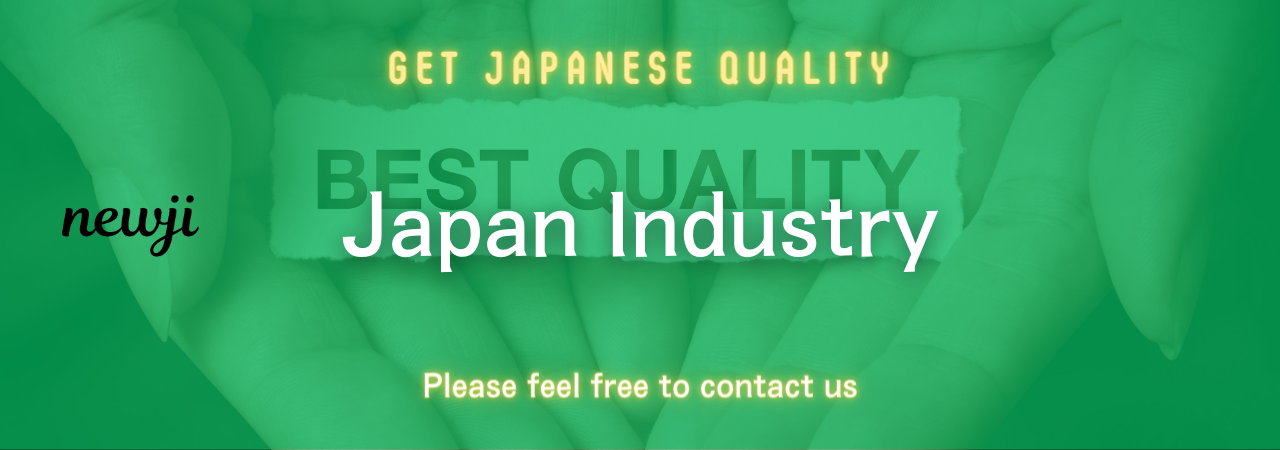
目次
Introduction to Temperature Sensors
Temperature sensors play a crucial role in a wide range of applications, from household appliances to industrial manufacturing processes.
They help in measuring temperature changes and ensuring that processes operate within safe and efficient parameters.
In this article, we will discuss the manufacturing process of temperature sensors and explore ways to enhance their accuracy.
Understanding the Basics of Temperature Sensors
Temperature sensors are devices that measure temperature by sensing some physical characteristic change.
Common types of temperature sensors include thermocouples, resistance temperature detectors (RTDs), thermistors, and infrared sensors.
Each type works using different principles and materials, making them suitable for specific applications.
Types of Temperature Sensors
Thermocouples are made of two different metals joined at one end.
They generate a voltage in response to temperature differences between the joined end and the other end.
RTDs use a material, usually platinum, whose resistance changes with temperature.
Thermistors are made of ceramic materials that exhibit a significant change in resistance with temperature.
Infrared sensors detect the infrared radiation emitted by objects.
Manufacturing Process of Temperature Sensors
The manufacturing process of temperature sensors varies based on the type, but the main steps generally include material selection, component fabrication, assembly, and calibration.
Material Selection
Choosing the right materials is crucial for the performance and durability of a temperature sensor.
For instance, thermocouples require specific metal combinations for the thermoelectric effect.
RTDs typically use platinum due to its stable resistance-temperature relationship.
Thermistors use ceramic materials such as oxides of manganese, nickel, or cobalt because of their high sensitivity to temperature changes.
Component Fabrication
Once the materials are selected, the next step is to fabricate the components.
For thermocouples, the metals are formed into wires and then joined at one end using welding or brazing.
In the case of RTDs, precision winding of platinum wire or deposition of platinum film onto a substrate is required.
Thermistors involve forming ceramic powders into desired shapes through pressing, sintering, and coating processes.
Infrared sensors may require microfabrication techniques such as photolithography to create the necessary semiconductor structures.
Assembly
Assembling the components into a finished sensor involves integrating the sensing element with other parts like electrical leads, protective housings, and connectors.
This step also includes ensuring the sensor is properly sealed to prevent contamination and damage.
For instance, thermocouples are assembled with junctions protectively encapsulated to shield from environmental harm.
RTDs and thermistors are often encased in stainless steel probes for durability.
Calibration
Calibration is crucial for ensuring the accuracy of temperature sensors.
This process involves comparing the sensor’s readings with a known standard and making necessary adjustments.
Thermocouples are typically calibrated by placing them in a controlled environment and measuring the voltage produced.
RTDs and thermistors are calibrated in temperature-controlled baths to verify their resistance against standard values.
Infrared sensors are calibrated using blackbody reference sources to ensure their measurements are accurate.
Accuracy Enhancement in Temperature Sensors
While initial manufacturing processes aim to produce highly precise sensors, there are several techniques to further enhance their accuracy.
Material Purity
Increasing the purity of materials used in sensors can significantly improve their accuracy.
In particular, using high-purity platinum in RTDs reduces impurities that could affect resistance.
Thermocouples benefit from using homogeneous metal alloys to ensure a consistent voltage response.
Advanced Manufacturing Techniques
Employing advanced manufacturing techniques, such as laser trimming, can enhance the accuracy of temperature sensors.
Laser trimming allows for precise adjustments to be made to the sensor’s components, ensuring more exact readings.
Additionally, microfabrication techniques can produce more consistent and uniform sensor elements, which contribute to better accuracy.
Enhanced Calibration Methods
More sophisticated calibration methods can also improve sensor accuracy.
For example, multi-point calibration involves calibrating the sensor at several temperature points, which helps correct non-linearities and provides a more accurate response over a wider temperature range.
Automated calibration systems can increase precision and repeatability by minimizing human error during the calibration process.
Temperature Compensation
Implementing temperature compensation techniques helps mitigate the effects of external factors on sensor accuracy.
For instance, RTDs can use compensation circuits to correct for self-heating errors.
Thermistors often include linearization circuits to adjust their non-linear resistance response.
Advanced software algorithms can also be integrated to correct for environmental conditions that may affect sensor performance.
Regular Maintenance and Recalibration
Regular maintenance and recalibration are essential for maintaining the accuracy of temperature sensors over time.
Periodic checks and recalibrations ensure that sensor readings remain reliable and precise.
Implementing a routine maintenance schedule can significantly prolong the service life and performance of the sensors.
Conclusion
The manufacturing process of temperature sensors involves careful material selection, precision fabrication, meticulous assembly, and thorough calibration.
Each step is designed to produce accurate and reliable sensors essential for various applications.
Enhancing the accuracy of these sensors can be achieved through material purity, advanced manufacturing techniques, improved calibration methods, and implementing temperature compensation.
Regular maintenance and recalibration also play a vital role in ensuring long-term accuracy.
By understanding these processes and techniques, industries can ensure the efficient and safe operation of their systems and applications.
資料ダウンロード
QCD管理受発注クラウド「newji」は、受発注部門で必要なQCD管理全てを備えた、現場特化型兼クラウド型の今世紀最高の受発注管理システムとなります。
ユーザー登録
受発注業務の効率化だけでなく、システムを導入することで、コスト削減や製品・資材のステータス可視化のほか、属人化していた受発注情報の共有化による内部不正防止や統制にも役立ちます。
NEWJI DX
製造業に特化したデジタルトランスフォーメーション(DX)の実現を目指す請負開発型のコンサルティングサービスです。AI、iPaaS、および先端の技術を駆使して、製造プロセスの効率化、業務効率化、チームワーク強化、コスト削減、品質向上を実現します。このサービスは、製造業の課題を深く理解し、それに対する最適なデジタルソリューションを提供することで、企業が持続的な成長とイノベーションを達成できるようサポートします。
製造業ニュース解説
製造業、主に購買・調達部門にお勤めの方々に向けた情報を配信しております。
新任の方やベテランの方、管理職を対象とした幅広いコンテンツをご用意しております。
お問い合わせ
コストダウンが利益に直結する術だと理解していても、なかなか前に進めることができない状況。そんな時は、newjiのコストダウン自動化機能で大きく利益貢献しよう!
(β版非公開)