- お役立ち記事
- Manufacturing Process of Toothbrush Stands and Innovations in Material Selection
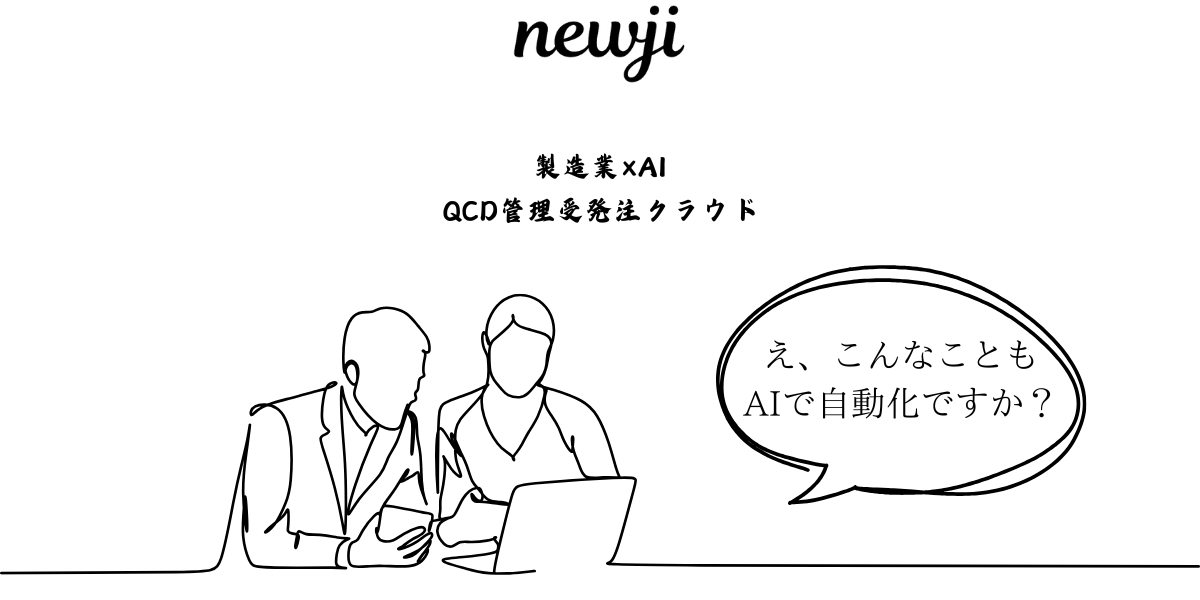
Manufacturing Process of Toothbrush Stands and Innovations in Material Selection
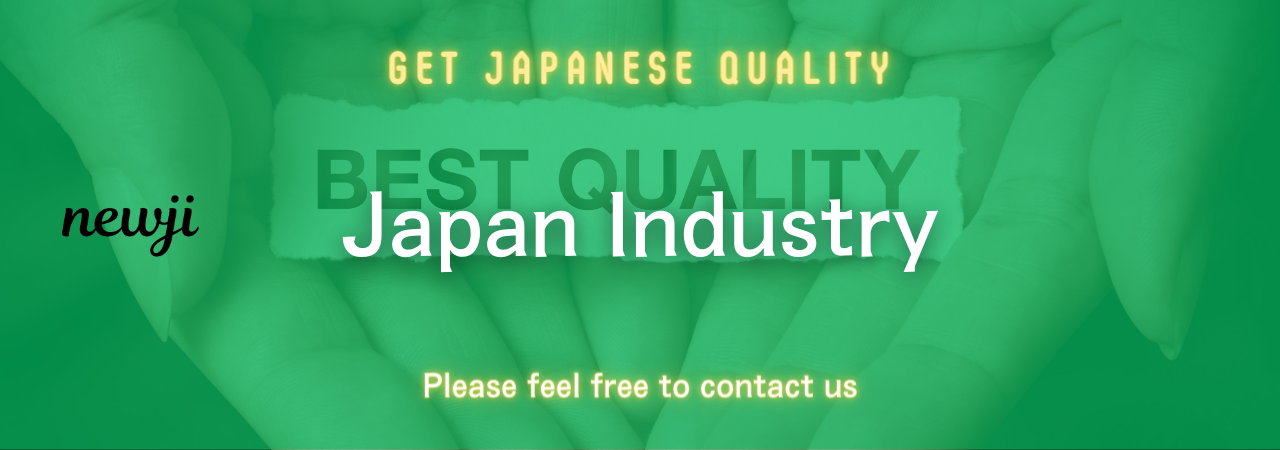
Toothbrush stands are an essential item in every household, helping to keep our toothbrushes clean and organized.
But have you ever wondered how these handy products are made and how manufacturers are innovating in material selection?
Let’s dive into the manufacturing process of toothbrush stands and explore recent innovations in materials used.
目次
The Manufacturing Process of Toothbrush Stands
The process of creating a toothbrush stand starts with designing, followed by material selection, molding, finishing, and packaging.
Each step is crucial to ensure a high-quality product that meets consumer needs.
Design and Prototyping
Design is the first and crucial step in manufacturing toothbrush stands.
Designers consider factors like functionality, aesthetics, and ease of use.
Modern designs often incorporate multiple slots for toothbrushes, toothpaste, and other oral hygiene items.
Prototyping is then performed using 3D printing or similar methods to create a physical model of the stand.
This step allows designers and engineers to make adjustments and improvements before mass production begins.
Material Selection
The choice of material is vital for the durability and functionality of toothbrush stands.
Traditionally, plastics have been widely used due to their versatility, ease of molding, and cost-effectiveness.
However, environmental concerns are pushing manufacturers to explore more sustainable materials.
Let’s explore how material selection has evolved over the years.
Innovations in Material Selection
As consumers become more environmentally conscious, the demand for eco-friendly products has risen.
Manufacturers are now innovating in material selection by turning to sustainable and biodegradable options.
Bamboo and Wood
Bamboo and wood have emerged as popular alternatives to plastic.
Bamboo, in particular, grows quickly and does not require pesticides, making it an eco-friendly option.
Wood is also renewable and biodegradable.
Manufacturers process these materials into fine particles, mix them with eco-friendly binders, and then mold them into the desired shape.
This process results in a sturdy and sustainable toothbrush stand.
Recycled Plastics
Plastic waste has been a significant environmental issue.
To address this, manufacturers are increasingly using recycled plastics.
These plastics are sourced from post-consumer waste, such as water bottles and packaging.
The recycled material is cleaned, melted, and remolded into new products.
By using recycled plastics, companies reduce their carbon footprint and contribute to a circular economy.
Biodegradable Materials
Biodegradable materials are another innovative option.
Polylactic acid (PLA) is a popular biodegradable polymer derived from renewable resources like corn starch or sugarcane.
PLA can be molded into various shapes and decomposes naturally over time.
This makes it an excellent choice for eco-friendly toothbrush stands.
Manufacturing Techniques
Different manufacturing techniques are employed depending on the chosen material.
Let’s look at some common methods used in producing toothbrush stands.
Injection Molding
Injection molding is widely used for plastic stands.
The process involves melting plastic pellets and injecting the molten material into a mold.
Once cooled, the plastic hardens and takes the shape of the mold.
This method is efficient for mass production and allows for intricate designs.
Compression Molding
Compression molding is suitable for materials like bamboo and wood composites.
The material is placed into a heated mold, and pressure is applied to compress it into the desired shape.
This technique ensures the material is densely packed, resulting in a durable product.
3D Printing
3D printing is revolutionizing the manufacturing of toothbrush stands.
It offers unparalleled design flexibility and minimizes material waste.
3D printing involves layer-by-layer deposition of material to create a three-dimensional object.
While it is currently more suitable for prototyping and small-scale production, technological advancements are making it increasingly feasible for mass production.
Quality Control and Finishing
After molding, stands undergo quality control to ensure they meet specified standards.
Manufacturers inspect for defects, such as cracks, warping, or surface imperfections.
Any faulty products are rejected.
The stands are then cleaned, polished, and sometimes painted to enhance their appearance.
Additional features like anti-slip pads or drainage holes may also be added during this stage.
Packaging and Environmental Considerations
The final step is packaging, where toothbrush stands are packed in eco-friendly packaging.
Sustainable materials, such as recycled cardboard or biodegradable bags, are often used to reduce environmental impact.
Many companies are also adopting minimalist packaging to further minimize waste.
Conclusion
The manufacturing process of toothbrush stands has evolved significantly, with innovations in material selection playing a key role.
From traditional plastics to eco-friendly materials like bamboo, wood, recycled plastics, and biodegradable polymers, manufacturers are making strides toward sustainability.
Advanced manufacturing techniques, such as injection molding, compression molding, and 3D printing, are used to produce high-quality stands.
As consumer demand for environmentally friendly products grows, the industry will continue to innovate, ensuring that everyday items like toothbrush stands are both functional and eco-conscious.
資料ダウンロード
QCD調達購買管理クラウド「newji」は、調達購買部門で必要なQCD管理全てを備えた、現場特化型兼クラウド型の今世紀最高の購買管理システムとなります。
ユーザー登録
調達購買業務の効率化だけでなく、システムを導入することで、コスト削減や製品・資材のステータス可視化のほか、属人化していた購買情報の共有化による内部不正防止や統制にも役立ちます。
NEWJI DX
製造業に特化したデジタルトランスフォーメーション(DX)の実現を目指す請負開発型のコンサルティングサービスです。AI、iPaaS、および先端の技術を駆使して、製造プロセスの効率化、業務効率化、チームワーク強化、コスト削減、品質向上を実現します。このサービスは、製造業の課題を深く理解し、それに対する最適なデジタルソリューションを提供することで、企業が持続的な成長とイノベーションを達成できるようサポートします。
オンライン講座
製造業、主に購買・調達部門にお勤めの方々に向けた情報を配信しております。
新任の方やベテランの方、管理職を対象とした幅広いコンテンツをご用意しております。
お問い合わせ
コストダウンが利益に直結する術だと理解していても、なかなか前に進めることができない状況。そんな時は、newjiのコストダウン自動化機能で大きく利益貢献しよう!
(Β版非公開)