- お役立ち記事
- Manufacturing Process of Transmission Gears and Durability Enhancement
月間76,176名の
製造業ご担当者様が閲覧しています*
*2025年3月31日現在のGoogle Analyticsのデータより
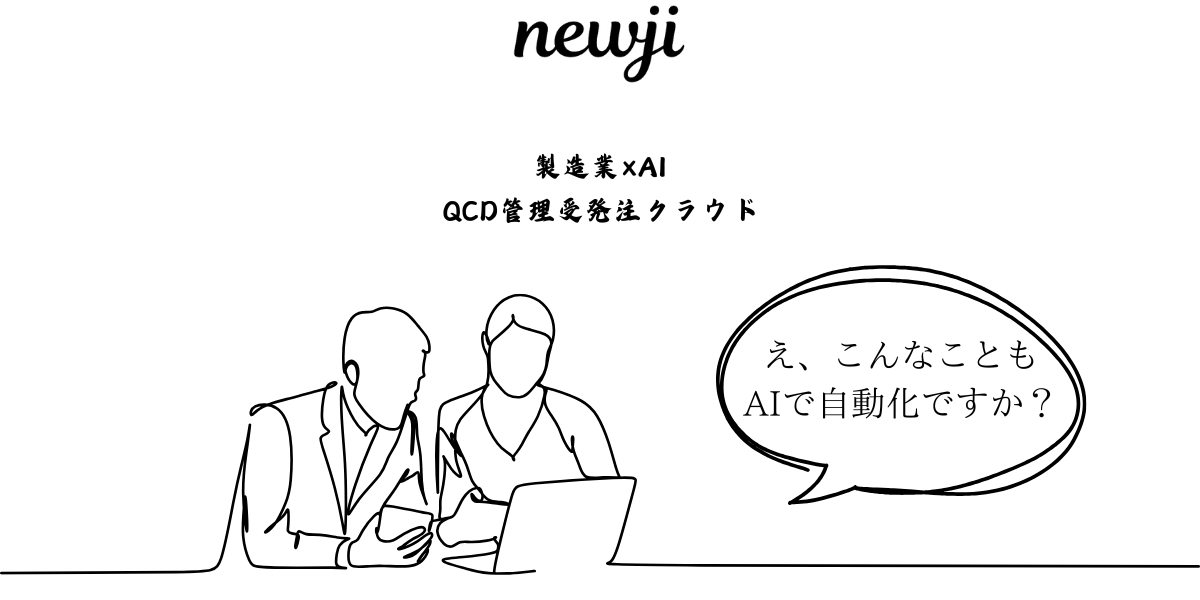
Manufacturing Process of Transmission Gears and Durability Enhancement
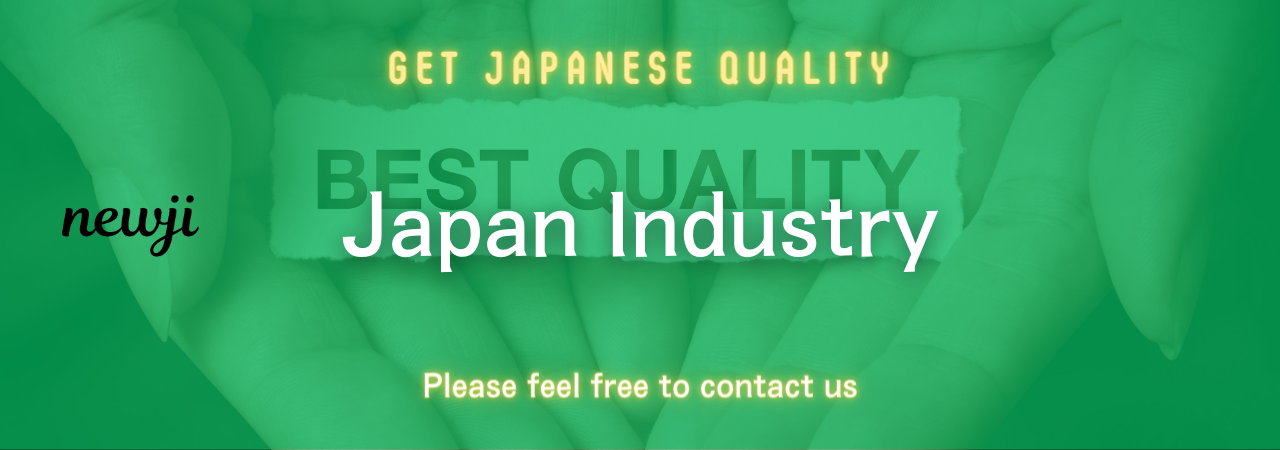
Gears play a crucial role in the functioning of various machines, from simple bicycles to complex industrial machinery. One of the critical components within these systems is the transmission gear. Understanding the manufacturing process and the methods to enhance their durability is vital for producing high-quality transmission gears. Below, we delve into the step-by-step manufacturing process of transmission gears and explore techniques to improve their longevity.
目次
The Raw Materials
The first step in manufacturing transmission gears is sourcing the right raw materials. Generally, high-grade steel alloys such as chromium, molybdenum, and nickel are preferred due to their strength and wear resistance. The raw materials must meet specific chemical and physical properties to ensure the longevity of the gears.
The Designing Phase
Before the actual manufacturing begins, a detailed design phase is necessary. Advanced computer-aided design (CAD) software is used to create precise blueprints of the gears. Factors such as gear size, teeth geometry, and load types are considered. This digital model aids in visualizing the final product and identifying any potential issues.
Forging
Forging is one of the primary methods to shape the raw materials into gear blanks. In this process, the steel material is heated until it becomes pliable and is then hammered or pressed into the rough shape of the gear. This technique improves the strength of the material by aligning the grain structure. After forging, gear blanks are allowed to cool slowly to relieve internal stresses.
Machining
Once the gear blanks are ready, they are subjected to a series of machining processes to achieve the desired shape and dimensions. The most common machining techniques include:
Turning
Turning involves rotating the gear blank on a lathe and using cutting tools to shape the outer surface. This process ensures that the exterior is smooth and uniform.
Milling
Milling processes are used for cutting teeth into the gear blank. A gear cutter or a hob is used to create the teeth according to the desired specifications. Precision is crucial in this step to ensure proper meshing with other gears.
Grinding
Grinding is the final machining process that improves surface finish and ensures high-dimensional accuracy. Abrasive wheels are used to remove any remaining material and achieve the exact measurements required.
Heat Treatment
After machining, the gears undergo heat treatment to enhance their mechanical properties. This process involves heating the gears to a specific temperature and then cooling them rapidly. Common heat treatment processes include:
Quenching
Quenching increases the hardness of the gears. The gears are heated to a high temperature and then rapidly cooled using water or oil. This forms a hard outer surface while leaving the core relatively softer.
Tempering
Tempering follows quenching to reduce brittleness and improve toughness. The gears are reheated to a lower temperature and then cooled, balancing hardness and durability.
Carburizing
Carburizing infuses the surface of the gears with carbon to create a hard outer layer while maintaining a tough core. The gears are placed in a carbon-rich environment and heated, allowing carbon atoms to diffuse into the surface.
Surface Finishing
Surface finishing processes are employed to enhance the appearance and performance of the gears. Techniques such as shot peening, coating, and polishing are used to reduce surface irregularities and improve resistance to wear and corrosion.
Shot Peening
Shot peening involves bombarding the gear surface with small spherical media to induce compressive stress. This process increases fatigue strength and resistance to cracking.
Coating
Special coatings, such as phosphate or nitride, are applied to the gear surfaces to prevent rust and reduce friction. These coatings enhance the overall durability of the gears.
Polishing
Polishing creates a smooth surface that minimizes friction and wear during operation. High-quality polishing ensures that gears run smoothly and efficiently.
Quality Control
Maintaining high-quality standards is essential throughout the manufacturing process. Quality control measures include rigorous inspections and testing to identify defects and ensure conformance to specifications. Common tests include:
Non-Destructive Testing (NDT)
NDT techniques like magnetic particle inspection and ultrasonic testing are used to detect surface and subsurface defects without damaging the gears.
Hardness Testing
Hardness testing ensures the gears achieve the desired hardness levels post-heat treatment. Methods like Rockwell and Vickers hardness tests are commonly used.
Dimensional Inspection
Dimensional inspection verifies that the gears meet the precise measurements specified in the design phase. Coordinate measuring machines (CMM) are often used for this purpose.
Assembly and Integration
Once the gears pass all quality control tests, they are ready for assembly and integration into the final machinery. Proper lubrication is applied to minimize friction and wear during their operational life.
Enhancing Durability
Several advanced techniques can further enhance the durability of transmission gears:
Advanced Materials
Research and development into new materials, such as nanostructured steel and composites, offer greater resistance to wear and fatigue.
Design Optimization
Optimizing the gear design through finite element analysis (FEA) allows for better load distribution and reduces stress concentrations.
Regular Maintenance
Regular maintenance, including proper lubrication and timely replacement of worn-out gears, ensures a prolonged lifespan.
Conclusion
The manufacturing process of transmission gears is intricate, involving multiple steps that require precision and expertise. From sourcing the right raw materials to advanced heat treatment and quality control measures, every stage is crucial to producing durable and high-performance gears.
By employing advanced materials, design optimization, and regular maintenance, manufacturers can significantly enhance the durability and efficiency of transmission gears. Understanding these processes not only helps in producing better gears but also contributes to the overall reliability and longevity of machinery that relies on them.
資料ダウンロード
QCD管理受発注クラウド「newji」は、受発注部門で必要なQCD管理全てを備えた、現場特化型兼クラウド型の今世紀最高の受発注管理システムとなります。
ユーザー登録
受発注業務の効率化だけでなく、システムを導入することで、コスト削減や製品・資材のステータス可視化のほか、属人化していた受発注情報の共有化による内部不正防止や統制にも役立ちます。
NEWJI DX
製造業に特化したデジタルトランスフォーメーション(DX)の実現を目指す請負開発型のコンサルティングサービスです。AI、iPaaS、および先端の技術を駆使して、製造プロセスの効率化、業務効率化、チームワーク強化、コスト削減、品質向上を実現します。このサービスは、製造業の課題を深く理解し、それに対する最適なデジタルソリューションを提供することで、企業が持続的な成長とイノベーションを達成できるようサポートします。
製造業ニュース解説
製造業、主に購買・調達部門にお勤めの方々に向けた情報を配信しております。
新任の方やベテランの方、管理職を対象とした幅広いコンテンツをご用意しております。
お問い合わせ
コストダウンが利益に直結する術だと理解していても、なかなか前に進めることができない状況。そんな時は、newjiのコストダウン自動化機能で大きく利益貢献しよう!
(β版非公開)