- お役立ち記事
- Manufacturing Process of Trunk Hinges and Durability Reinforcement
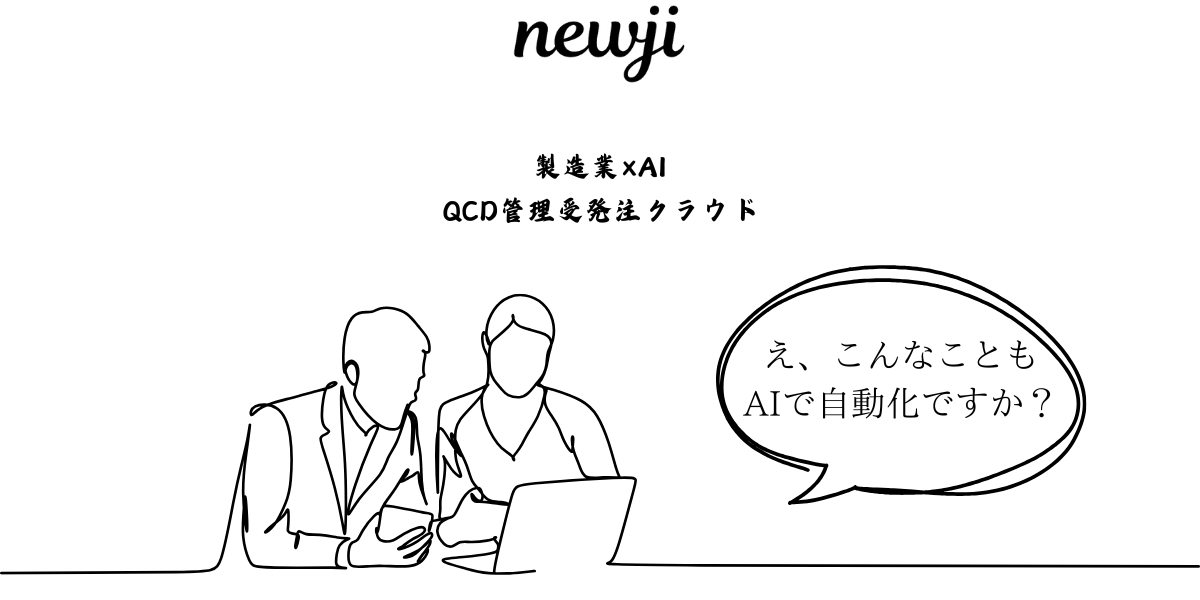
Manufacturing Process of Trunk Hinges and Durability Reinforcement
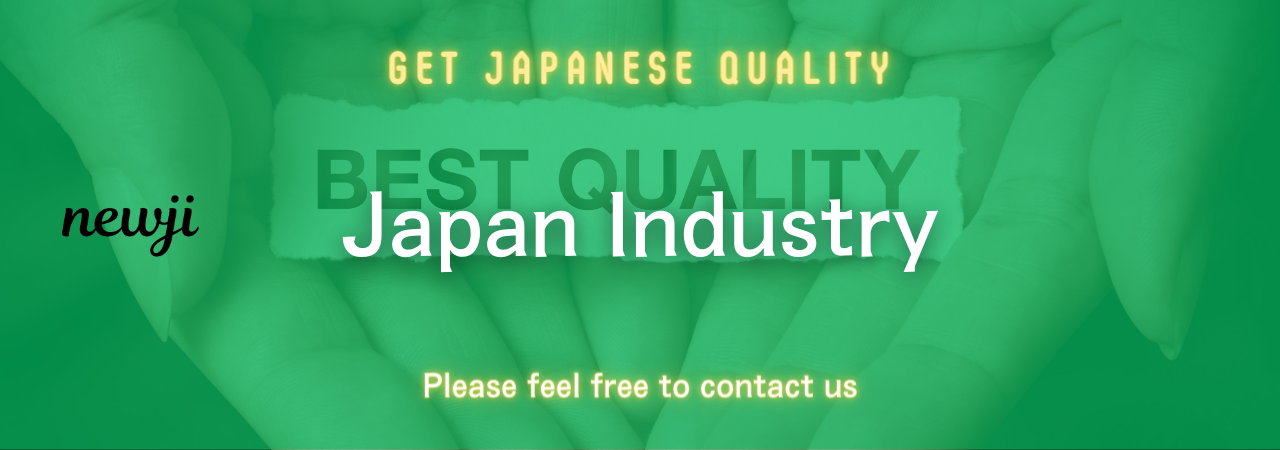
目次
Introduction
Trunk hinges play a pivotal role in the functionality of a car’s trunk, providing the necessary pivot to open and close smoothly.
Understanding the manufacturing process of trunk hinges and how their durability is reinforced can offer valuable insights into automotive engineering.
In this article, we will explore the various stages of trunk hinge production and the measures taken to enhance their longevity.
The Importance of Trunk Hinges
Trunk hinges might seem like minor components, but they are crucial for the overall utility and safety of a vehicle.
These hinges support the weight of the trunk lid and ensure it remains securely closed during travel.
Durable hinges also contribute to preventing wear and tear, thereby extending the life of the trunk and the car itself.
Raw Material Selection
The first step in the manufacturing process is the selection of raw materials.
Typically, high-strength steel or aluminum alloys are chosen due to their durability and resistance to corrosion.
The material must be able to withstand various stresses, including direct impacts and weather-related degradations like rust and corrosion.
Steel vs. Aluminum
Steel is often preferred for its high durability and tensile strength.
However, aluminum is gaining popularity because of its lighter weight, which can improve fuel efficiency.
The choice between the two materials depends on the specific requirements of the vehicle and the preferences of the manufacturer.
Design and Engineering
Once the material is selected, the next step is design and engineering.
Computer-aided design (CAD) software is commonly used to create blueprints.
These designs undergo multiple iterations and simulations to determine the optimum shape and size for durability and functionality.
Stress Analysis
During this phase, stress analysis is conducted to identify potential weak points in the hinge.
Finite Element Analysis (FEA) is often used to simulate how the hinge will perform under various conditions.
This helps engineers make necessary adjustments to enhance durability and performance.
Prototyping
After the design phase, a prototype is created.
This involves machining the raw material into the preliminary shape of the trunk hinge.
The prototype is then tested for various performance metrics, including strength, flexibility, and resistance to corrosion.
Based on the results, the design may undergo further modifications.
3D Printing Prototypes
In recent years, 3D printing has become an integral part of prototyping.
This technology allows for rapid creation and testing of multiple design variations, speeding up the overall development process.
Mass Production
Once the prototype is approved, the process moves to mass production.
This typically involves several steps, including stamping, forming, welding, and assembly.
Stamping and Forming
Stamping uses large presses to cut the raw material into the basic shape of the hinge.
Forming processes like bending and folding are then used to create the final shape.
Welding
For steel hinges, welding is often required to join various parts together.
Robotic arms are usually employed for precision and consistency in welding, ensuring each hinge meets stringent quality standards.
Assembly
Finally, the hinge components are assembled.
Automated assembly lines are commonly used to ensure efficiency and uniformity.
Quality control checks are performed at this stage to catch any defects or inconsistencies.
Durability Reinforcement Techniques
To enhance the durability of trunk hinges, several reinforcement techniques are employed.
These methods help protect hinges from wear and tear, prolonging their functional lifespan.
Coatings and Plating
Protective coatings like powder coating or galvanization are applied to shield the metal from rust and corrosion.
These coatings add an extra layer of protection, ensuring the hinge remains in good condition even in harsh environments.
Heat Treatment
Heat treatment processes like annealing or quenching are used to strengthen the metal.
By altering the metal’s microstructure, these treatments enhance its hardness and resistance to deformation and fatigue.
Load Testing
Before entering the market, hinges undergo rigorous load testing.
This involves simulating real-world conditions to ensure the hinge can withstand various stresses without failing.
Load testing helps guarantee that only high-quality, durable hinges are installed in vehicles.
Maintenance and Longevity
Even the most durable trunk hinges require some level of maintenance to ensure their long-term functionality.
Regular lubrication is essential to keep the hinge’s moving parts operating smoothly.
Periodic inspections can also help identify any signs of wear early, allowing for timely intervention and replacement if necessary.
Conclusion
Understanding the manufacturing process of trunk hinges and the measures taken to reinforce their durability provides valuable insights into their crucial role in automotive engineering.
From raw material selection to final assembly and reinforcement techniques, each step is meticulously planned and executed to ensure the highest quality hinges.
By adhering to these intricate processes, manufacturers can produce trunk hinges that are both functional and durable, contributing to the vehicle’s overall safety and longevity.
資料ダウンロード
QCD調達購買管理クラウド「newji」は、調達購買部門で必要なQCD管理全てを備えた、現場特化型兼クラウド型の今世紀最高の購買管理システムとなります。
ユーザー登録
調達購買業務の効率化だけでなく、システムを導入することで、コスト削減や製品・資材のステータス可視化のほか、属人化していた購買情報の共有化による内部不正防止や統制にも役立ちます。
NEWJI DX
製造業に特化したデジタルトランスフォーメーション(DX)の実現を目指す請負開発型のコンサルティングサービスです。AI、iPaaS、および先端の技術を駆使して、製造プロセスの効率化、業務効率化、チームワーク強化、コスト削減、品質向上を実現します。このサービスは、製造業の課題を深く理解し、それに対する最適なデジタルソリューションを提供することで、企業が持続的な成長とイノベーションを達成できるようサポートします。
オンライン講座
製造業、主に購買・調達部門にお勤めの方々に向けた情報を配信しております。
新任の方やベテランの方、管理職を対象とした幅広いコンテンツをご用意しております。
お問い合わせ
コストダウンが利益に直結する術だと理解していても、なかなか前に進めることができない状況。そんな時は、newjiのコストダウン自動化機能で大きく利益貢献しよう!
(Β版非公開)