- お役立ち記事
- Manufacturing Process of Vending Machines and Cooling System Innovations
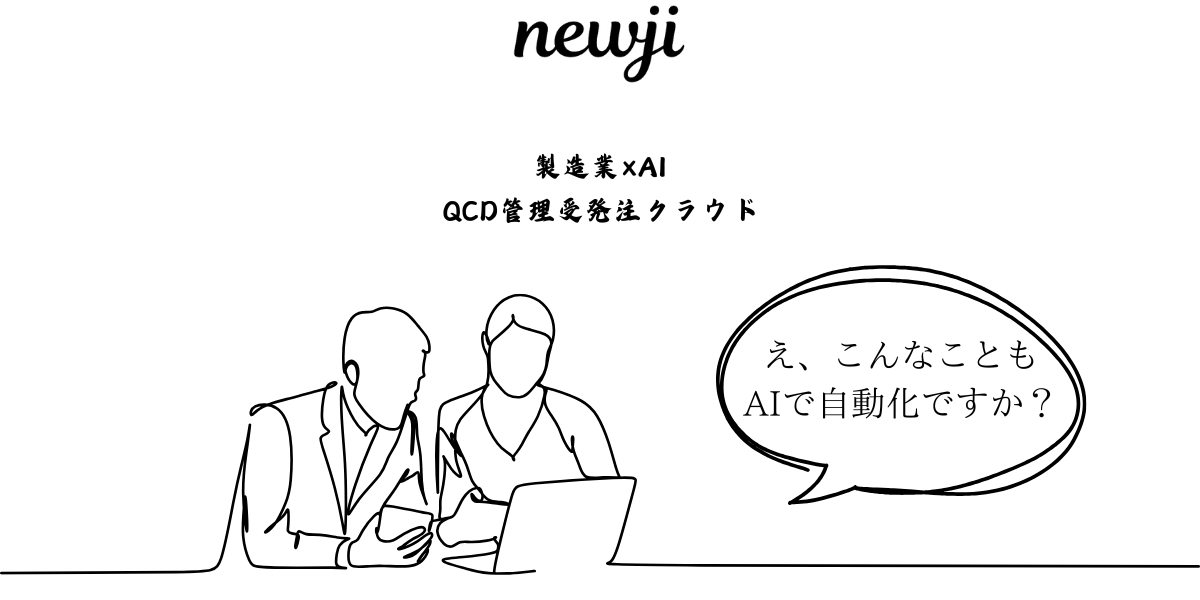
Manufacturing Process of Vending Machines and Cooling System Innovations
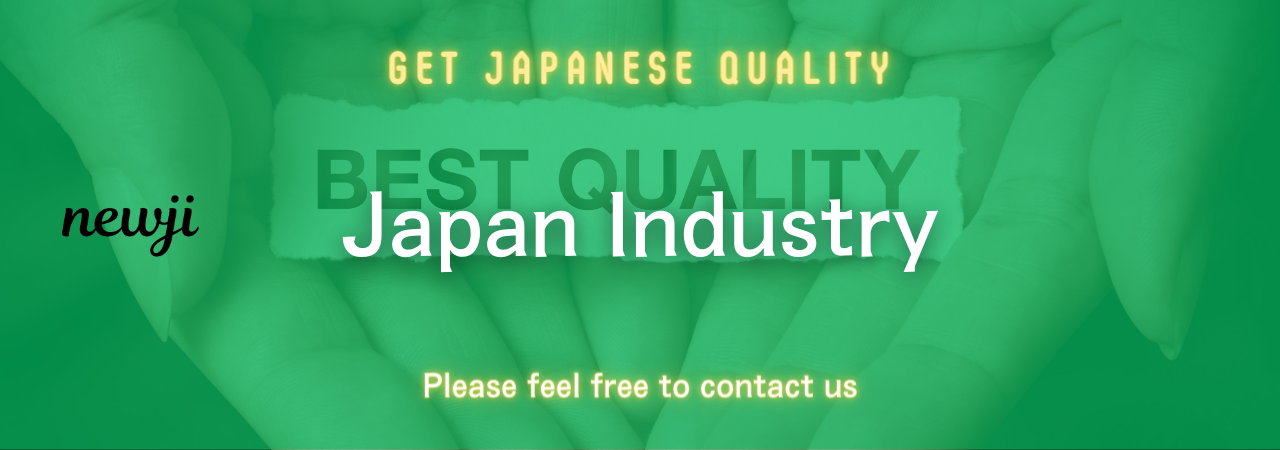
目次
Understanding the Basics of Vending Machines
Vending machines are a common sight in our daily lives.
We often see them in schools, hospitals, and office buildings, dispensing snacks, beverages, and other essentials with the push of a button.
But have you ever wondered about the manufacturing process behind these complex machines?
Let’s delve into how vending machines come to life and explore some recent innovations in their cooling systems.
Design and Planning
The creation of a vending machine starts with careful design and planning.
Companies first need to consider the purpose of the machine, the types of products it will dispense, and the target audience.
For example, a vending machine designed for snacks will differ significantly from one that dispenses hot meals or electronic gadgets.
Once the purpose is defined, engineers and designers work together to draw up detailed blueprints.
These plans outline the machine’s size, layout, and internal mechanisms, including the storage spaces, dispensing units, and payment systems.
Modern vending machines often include digital interfaces and cashless payment options.
Materials and Components
Next, the required materials are sourced.
The main frame of the vending machine is usually made from steel or aluminum to ensure durability and stability.
The front panel is often made of glass or clear plastic, allowing customers to see the products inside.
Internal components, such as coils, motors, and electronics, are carefully selected based on their reliability and efficiency.
Companies usually order these parts from specialized suppliers.
Ensuring the quality and compatibility of each component is crucial as it affects the machine’s overall performance and lifespan.
Manufacturing and Assembly
Once all the materials and components are ready, the manufacturing process begins.
This typically involves several stages:
Cutting and Shaping
The metal frames and panels are cut and shaped according to the design specifications.
Advanced machinery like laser cutters and CNC machines are often used for precision.
Welding and Assembly
The various parts are then welded together to form the machine’s basic structure.
This step is followed by assembling the internal components, including the product storage units, dispensing mechanisms, and payment systems.
Technicians carefully install each part, ensuring they fit together seamlessly.
Electrical and Software Integration
Modern vending machines are often equipped with electronic components and software systems.
These include sensors, payment readers, and digital displays.
Technicians install and test these systems to ensure they work correctly and integrate with the mechanical components.
Software programming is also done at this stage to manage transactions, inventory tracking, and user interfaces.
Quality Control
Before a vending machine is shipped to its final destination, it undergoes rigorous quality control checks.
Technicians conduct thorough tests to ensure the machine dispenses products correctly, accepts payments smoothly, and operates efficiently.
Security features are also checked to prevent tampering and theft.
Any issues detected are promptly addressed to ensure that the final product meets industry standards and customer expectations.
Installation and Maintenance
Once the vending machines pass quality control, they are shipped to their designated locations.
Technicians install the machines, making sure they are correctly connected to power sources and secured in place.
Training may be provided to the relevant personnel to manage and restock the machines.
Regular maintenance is crucial for the longevity and optimal performance of vending machines.
This includes routine checks on the mechanical and electronic components, cleaning of internal storage units, and updating software systems as needed.
Innovations in Cooling Systems
One of the most critical parts of a vending machine, especially those that dispense drinks or perishables, is its cooling system.
Recent advancements have led to significant innovations in this area, making cooling systems more efficient and environmentally friendly.
Energy-Efficient Compressors
Modern vending machines often use energy-efficient compressors that consume less power while maintaining optimal cooling.
These compressors are designed to reduce energy waste, thereby lowering operating costs and minimizing the machine’s carbon footprint.
Advanced Insulation Techniques
Innovations in insulation materials and techniques have significantly improved the cooling efficiency of vending machines.
Advanced insulation keeps the internal temperature stable, reducing the workload on compressors and other cooling components.
Eco-Friendly Refrigerants
Traditional refrigerants used in cooling systems have been known to contribute to greenhouse gas emissions.
However, recent advancements have led to the development of eco-friendly refrigerants that are less harmful to the environment.
These new refrigerants provide effective cooling while adhering to stricter environmental regulations.
Smart Cooling Systems
Incorporating smart technology into vending machines has led to the development of intelligent cooling systems.
These systems can monitor internal temperatures and adjust cooling levels automatically based on factors like ambient temperature and usage patterns.
Smart cooling systems can also send alerts when maintenance is needed or if there is a malfunction, ensuring timely intervention and reducing downtime.
Conclusion
The manufacturing process of vending machines involves careful planning, precise engineering, and rigorous quality control to ensure a reliable and efficient final product.
With continuous advancements in cooling system technology, vending machines are becoming more energy-efficient, environmentally friendly, and easier to maintain.
Understanding these processes and innovations not only highlights the complexity behind these everyday conveniences but also underscores the importance of technological progress in improving their functionality.
資料ダウンロード
QCD調達購買管理クラウド「newji」は、調達購買部門で必要なQCD管理全てを備えた、現場特化型兼クラウド型の今世紀最高の購買管理システムとなります。
ユーザー登録
調達購買業務の効率化だけでなく、システムを導入することで、コスト削減や製品・資材のステータス可視化のほか、属人化していた購買情報の共有化による内部不正防止や統制にも役立ちます。
NEWJI DX
製造業に特化したデジタルトランスフォーメーション(DX)の実現を目指す請負開発型のコンサルティングサービスです。AI、iPaaS、および先端の技術を駆使して、製造プロセスの効率化、業務効率化、チームワーク強化、コスト削減、品質向上を実現します。このサービスは、製造業の課題を深く理解し、それに対する最適なデジタルソリューションを提供することで、企業が持続的な成長とイノベーションを達成できるようサポートします。
オンライン講座
製造業、主に購買・調達部門にお勤めの方々に向けた情報を配信しております。
新任の方やベテランの方、管理職を対象とした幅広いコンテンツをご用意しております。
お問い合わせ
コストダウンが利益に直結する術だと理解していても、なかなか前に進めることができない状況。そんな時は、newjiのコストダウン自動化機能で大きく利益貢献しよう!
(Β版非公開)