- お役立ち記事
- Manufacturing Process of Washing Machines and Drum Design Innovations
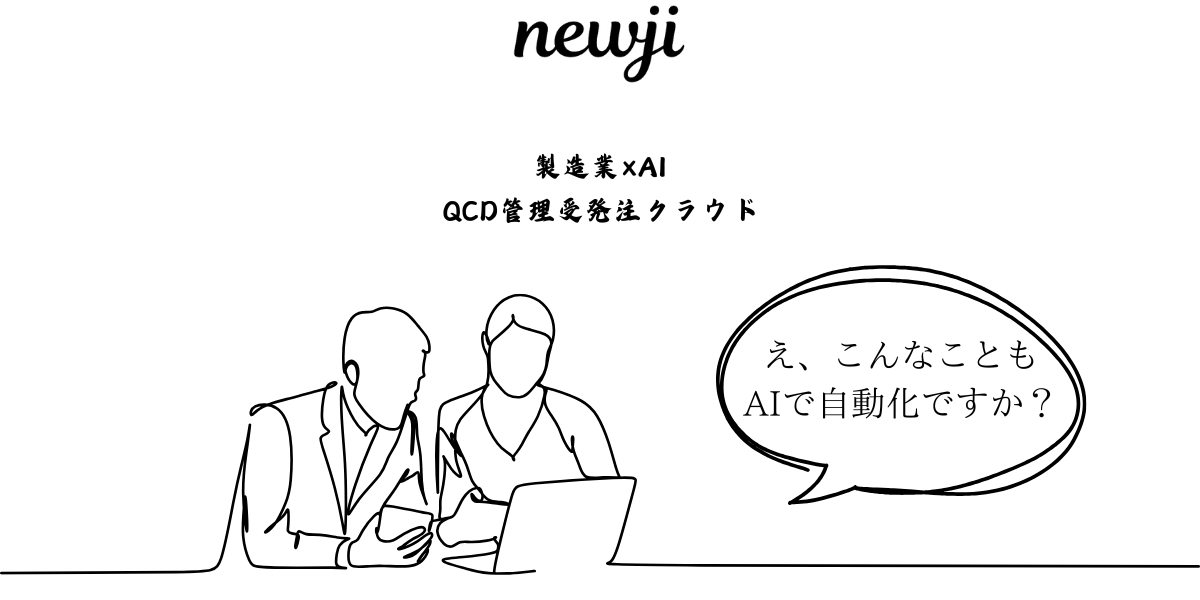
Manufacturing Process of Washing Machines and Drum Design Innovations
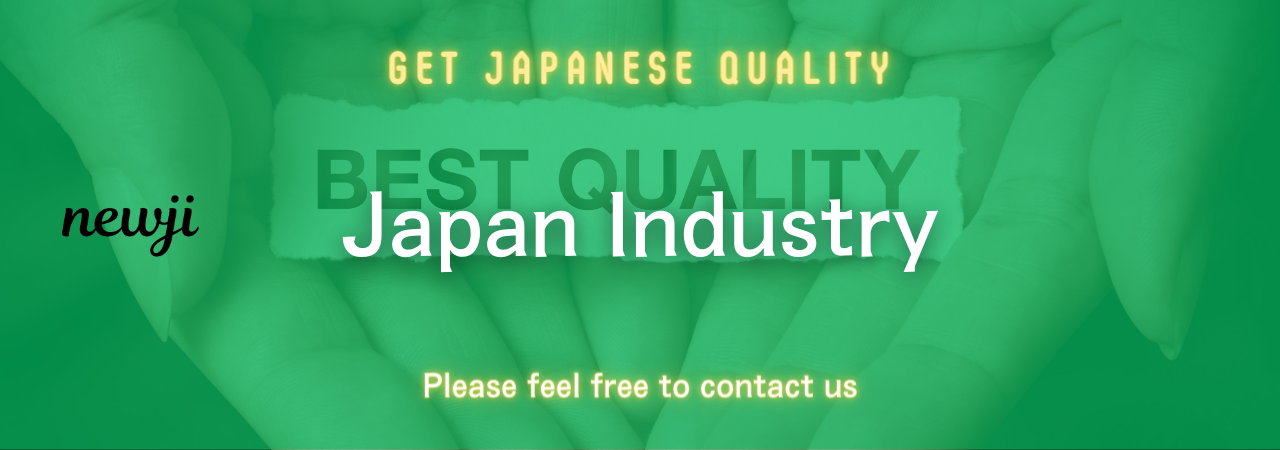
Manufacturing washing machines involves several intricate steps, from the initial design to the final assembly. Understanding the process provides insight into the complexities behind such household appliances. Additionally, innovations in drum design have significantly improved the efficiency and effectiveness of washing machines over the years.
目次
Initial Design and Planning
The journey of a washing machine begins with the design phase. Engineers and designers brainstorm to create a model that meets consumer needs while remaining cost-effective and environmentally friendly. This step involves computer-aided design (CAD) to develop detailed blueprints.
After a prototype is created, it undergoes rigorous testing to ensure functionality and durability. If successful, the design moves forward to the next phase, where it is refined further for large-scale production.
Material Selection
Selecting the right materials is crucial for manufacturing robust and reliable washing machines. The outer casing is usually made from high-quality, corrosion-resistant metals or durable plastics. The internal components, such as the drum and motor, require materials that can withstand high levels of wear and tear.
Stainless steel is commonly used for drums because it is not only durable but also resists rust and stains. Other components may include a combination of metals and plastics, carefully selected based on their properties to ensure the machine’s long-term performance.
Component Manufacturing
Once materials are selected, the manufacturing of individual components begins. This stage involves several processes, including stamping, casting, and injection molding. Metal sheets are stamped and bent to create the outer casing, while injection molding produces plastic parts like knobs and panels.
Motor manufacturing is another critical aspect. The motor powers the drum’s rotation, often using advanced technologies to optimize energy consumption and reduce noise. These motors are designed, tested, and assembled in specialized facilities.
Assembly Line Production
The next phase is the assembly of the washing machine. This process typically takes place on an assembly line, where various components are systematically put together.
The framework and outer casing are assembled first, followed by the installation of the drum. The motor and electrical components, such as the control panel and wiring, are then fitted. The assembly line is designed to maximize efficiency, with each worker or robot responsible for specific tasks.
Once assembled, each unit undergoes thorough quality control checks. Testing includes running the machine to ensure it operates correctly, assessing noise levels, and checking for any leaks or defects. Only machines that pass these stringent tests are packaged and prepared for distribution.
Innovations in Drum Design
The drum is a pivotal part of the washing machine, directly influencing its washing efficiency and user experience. Over the years, significant advancements have been made in drum design, enhancing performance and energy efficiency.
Stainless Steel Drums
Traditional drums were made from porcelain-coated steel, which could chip and rust over time. Modern washing machines often feature stainless steel drums, known for their durability and resistance to stains and odors. Stainless steel ensures a longer lifespan for the drum, maintaining its integrity even after many wash cycles.
Honeycomb Drum Design
One notable innovation is the honeycomb drum design. This design features a hexagonal pattern that mimics the structure of a honeycomb. The honeycomb surface creates a thin layer of water between the drum and the laundry, which cushions fabrics, reducing wear and tear.
This design not only protects delicate clothes but also enhances the machine’s washing efficiency, as water flows more evenly throughout the drum.
Wave Drum Technology
Another advancement is wave drum technology, characterized by a wave-like pattern on the drum’s surface. This design ensures gentle yet effective cleaning, ideal for delicate fabrics. The wave design also improves the drum’s movement, optimizing water usage and improving energy efficiency.
Eco Drum Clean
Environmental considerations have led to the development of features like the Eco Drum Clean. This function maintains the cleanliness of the drum without the need for harsh chemicals. By using a combination of high temperatures and rapid drum movement, it effectively removes detergent residue and bacteria, extending the drum’s lifespan and enhancing hygiene.
Future Trends in Washing Machine Manufacturing
The future of washing machine manufacturing looks promising, with ongoing research and innovation driving continuous improvement. Smart technologies are increasingly integrated, allowing for features like remote control via smartphone apps and automatic adjustment of wash settings based on load size and fabric type.
Sustainability is also a key focus. Manufacturers are developing machines that use less water and energy, reduce noise pollution, and incorporate recyclable materials. These innovations not only benefit the environment but also lead to cost savings for consumers.
Conclusion
The manufacturing process of washing machines involves a combination of meticulous planning, material selection, precision engineering, and innovative design. From the initial design phase to assembly and quality control, each step ensures that the final product is efficient, durable, and user-friendly.
Innovations in drum design, such as stainless steel construction, honeycomb patterns, and eco-clean technologies, have significantly enhanced the effectiveness and longevity of washing machines. As technology and sustainability continue to advance, the future holds even more exciting developments in the manufacturing of these essential household appliances.
資料ダウンロード
QCD調達購買管理クラウド「newji」は、調達購買部門で必要なQCD管理全てを備えた、現場特化型兼クラウド型の今世紀最高の購買管理システムとなります。
ユーザー登録
調達購買業務の効率化だけでなく、システムを導入することで、コスト削減や製品・資材のステータス可視化のほか、属人化していた購買情報の共有化による内部不正防止や統制にも役立ちます。
NEWJI DX
製造業に特化したデジタルトランスフォーメーション(DX)の実現を目指す請負開発型のコンサルティングサービスです。AI、iPaaS、および先端の技術を駆使して、製造プロセスの効率化、業務効率化、チームワーク強化、コスト削減、品質向上を実現します。このサービスは、製造業の課題を深く理解し、それに対する最適なデジタルソリューションを提供することで、企業が持続的な成長とイノベーションを達成できるようサポートします。
オンライン講座
製造業、主に購買・調達部門にお勤めの方々に向けた情報を配信しております。
新任の方やベテランの方、管理職を対象とした幅広いコンテンツをご用意しております。
お問い合わせ
コストダウンが利益に直結する術だと理解していても、なかなか前に進めることができない状況。そんな時は、newjiのコストダウン自動化機能で大きく利益貢献しよう!
(Β版非公開)