- お役立ち記事
- Manufacturing Process of Waterproof Camera Cases and Improved Durability Testing
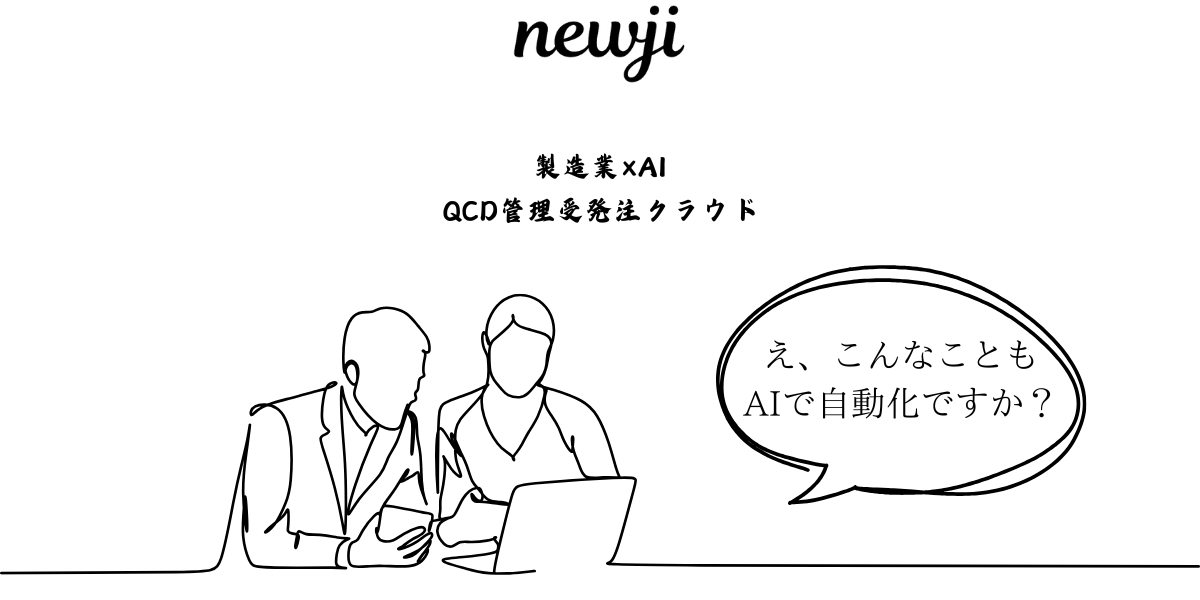
Manufacturing Process of Waterproof Camera Cases and Improved Durability Testing
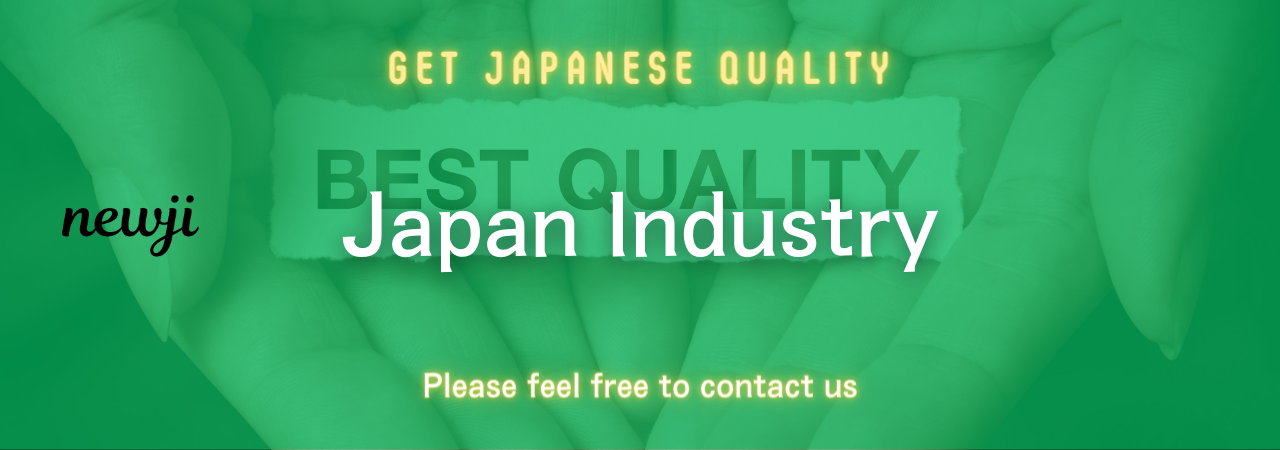
Waterproof camera cases are essential for protecting delicate camera equipment from water damage.
Whether for professional underwater photography or a leisurely beach vacation, a durable case ensures your camera performs perfectly.
This article explores the manufacturing process of waterproof camera cases and highlights the testing procedures that ensure their improved durability.
目次
Understanding the Materials Used
The first step in creating a durable waterproof camera case is selecting the right materials.
Common materials include polycarbonate, ABS plastic, and silicone rubber.
Polycarbonate is known for its impact resistance and clarity, making it an ideal choice for transparent cases.
ABS plastic provides excellent strength and resistance to physical impacts, ensuring the case can withstand rough handling.
Silicone rubber is flexible yet durable, offering good sealing capabilities to prevent water ingress.
Designing the Waterproof Camera Case
Before manufacturing begins, engineers and designers work together to create a detailed blueprint of the camera case.
This involves meticulous planning to ensure that all parts fit seamlessly and that the case is practical for every camera model it is intended to protect.
Computer-Aided Design (CAD) software is commonly used at this stage to create precise 3D models of the case.
Ergonomics and Usability
User-friendliness is paramount.
The design must allow easy access to camera controls while preventing any water from seeping in.
Buttons, levers, and other control mechanisms are integrated carefully, ensuring users can operate their cameras without needing to open the case.
Attention to ergonomics ensures that photographers can use their equipment comfortably and intuitively, even when underwater.
Manufacturing Process
Once the design is finalized, the manufacturing process begins.
This involves several key steps to ensure each case meets strict quality standards.
Injection Molding
Most waterproof camera cases are produced using injection molding.
In this process, the chosen materials—such as polycarbonate or ABS plastic—are melted and injected into molds.
These molds are meticulously crafted to match the design specifications, ensuring each case is an exact replica of the blueprint.
Once the material cools and solidifies, it takes the shape of the mold, resulting in a uniform and precise case structure.
Silicone Sealing
Silicone rubber is often used to create watertight seals around the case edges and control buttons.
This is a crucial step in the manufacturing process as it ensures no water can penetrate the case.
Advanced sealing techniques, such as vulcanization, are employed to bond the silicone to the case.
This ensures the seals remain robust and effective even after prolonged use.
Assembly
After individual components are molded and sealed, they are assembled to create the final product.
Quality control teams meticulously check each assembled case to ensure that all parts fit perfectly and function as intended.
Any defects detected at this stage are immediately rectified to maintain high standards of quality.
Durability Testing
To ensure that each waterproof camera case offers the highest level of protection, rigorous durability testing is conducted.
This involves subjecting the cases to various stress tests designed to simulate real-world conditions.
Water Pressure Testing
One of the critical tests is the water pressure test.
Cases are submerged in water at varying depths and subjected to different pressure levels.
This helps identify any potential weak points where water might leak into the case.
Cameras placed inside the cases during this test are checked afterward to ensure no water damage.
Drop Testing
Accidental drops and impacts can occur frequently, especially in adventurous settings.
Drop tests involve dropping the cases from different heights onto hard surfaces.
This test ensures the case can withstand physical shocks without cracking or breaking.
Cases that pass the drop test offer reliable protection for cameras even in rugged environments.
Temperature Testing
Extreme temperatures can affect the materials and seals in a waterproof camera case.
Temperature tests involve exposing the cases to both high and low temperatures to check for any degradation in performance.
This ensures the case will protect the camera in various environmental conditions, from hot beaches to cold mountain tops.
Improving Durability
Manufacturers constantly innovate to improve the durability and performance of their waterproof camera cases.
Advances in material science and manufacturing processes contribute to the development of more robust and reliable cases.
Material Enhancements
New materials with superior strength and sealing properties are continually being researched.
For example, newer blends of polycarbonate and ABS plastic offer better impact resistance and longer-lasting durability.
Enhanced silicone formulations provide improved sealing even after repeated use.
Design Innovations
Refinements in design also contribute to improved durability.
For example, more efficient seal placements and advanced locking mechanisms ensure that cases remain watertight even under significant stress.
Ergonomic enhancements make the cases easier to handle, reducing the likelihood of accidental drops.
Quality Control Improvements
Advanced quality control techniques, including automated inspection systems, ensure that each case produced meets the highest standards.
This reduces the likelihood of defects, ensuring that every case offers reliable protection for sensitive camera equipment.
In conclusion, the manufacturing process of waterproof camera cases involves carefully choosing materials, precise designing, and rigorous testing to ensure durability.
Ongoing innovations in materials and design help create even more robust and reliable cases.
By understanding the detailed process behind these essential accessories, photographers can have confidence that their equipment will remain safe and functional in any environment.
資料ダウンロード
QCD調達購買管理クラウド「newji」は、調達購買部門で必要なQCD管理全てを備えた、現場特化型兼クラウド型の今世紀最高の購買管理システムとなります。
ユーザー登録
調達購買業務の効率化だけでなく、システムを導入することで、コスト削減や製品・資材のステータス可視化のほか、属人化していた購買情報の共有化による内部不正防止や統制にも役立ちます。
NEWJI DX
製造業に特化したデジタルトランスフォーメーション(DX)の実現を目指す請負開発型のコンサルティングサービスです。AI、iPaaS、および先端の技術を駆使して、製造プロセスの効率化、業務効率化、チームワーク強化、コスト削減、品質向上を実現します。このサービスは、製造業の課題を深く理解し、それに対する最適なデジタルソリューションを提供することで、企業が持続的な成長とイノベーションを達成できるようサポートします。
オンライン講座
製造業、主に購買・調達部門にお勤めの方々に向けた情報を配信しております。
新任の方やベテランの方、管理職を対象とした幅広いコンテンツをご用意しております。
お問い合わせ
コストダウンが利益に直結する術だと理解していても、なかなか前に進めることができない状況。そんな時は、newjiのコストダウン自動化機能で大きく利益貢献しよう!
(Β版非公開)