- お役立ち記事
- Manufacturing Process of Wooden Flooring and Wear Resistance Enhancement
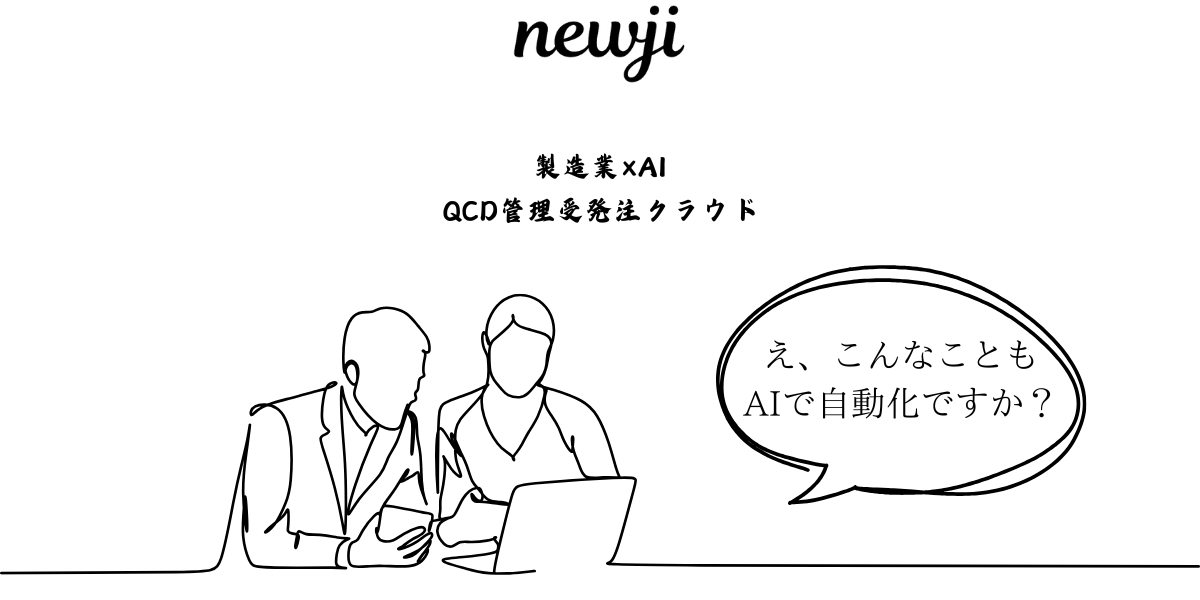
Manufacturing Process of Wooden Flooring and Wear Resistance Enhancement
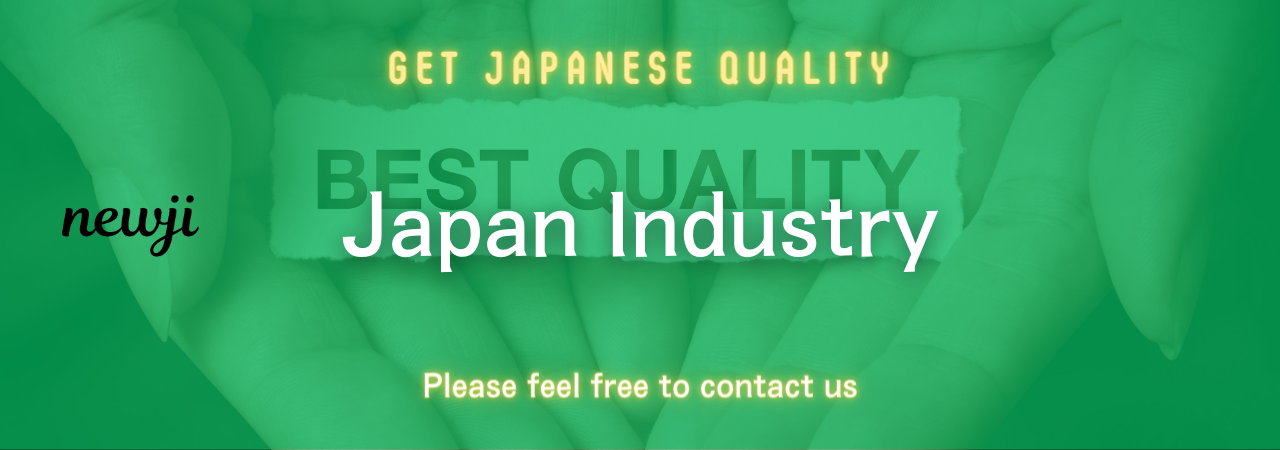
Wooden flooring is a popular choice in homes and offices due to its aesthetic appeal and durability. To understand why wooden flooring is so highly regarded, let’s delve into its manufacturing process and how its wear resistance is enhanced. Knowing more about these processes will help appreciate why wooden floors are a long-lasting and visually appealing investment.
目次
Selection of Raw Materials
The first step in manufacturing wooden flooring is selecting the raw materials. The type of wood used affects the floor’s durability, appearance, and wear resistance. Commonly used woods include oak, maple, cherry, and walnut. These woods are favored for their hardness, stability, and attractive grain patterns.
Once the type of wood is chosen, logs are carefully inspected to ensure they are free from defects. They are then transported to the milling facility. It’s essential to select high-quality logs to produce flooring that can withstand daily wear and tear.
Sawing and Drying
Upon arrival at the milling facility, the logs are sawn into planks using large saws. The sawing process can be done in various ways, such as plain sawing, quarter sawing, or rift sawing. Each method determines the wood grain’s final appearance and stability.
After the planks are cut, they must be dried to reduce their moisture content. This step is crucial because wood tends to expand and contract with changes in humidity. Kiln drying is the most common method, where planks are placed in a controlled environment with carefully regulated temperature and humidity. This process can take several days or even weeks, but it ensures that the wood reaches a stable moisture content suitable for flooring.
Milling and Profiling
Once the wood is adequately dried, it proceeds to the milling stage. During this phase, the planks are planed and sanded to achieve a smooth surface. This ensures the planks are of uniform thickness, which is vital for a seamless installation.
Next, the planks are profiled. Profiling involves cutting grooves and tongues into the edges of the planks. This tongue-and-groove system allows the planks to interlock securely during installation, creating a stable and gap-free floor.
Surface Finishing
The surface finishing process significantly influences the wooden flooring’s wear resistance. There are different finishing options available, each providing varying levels of protection and aesthetics. The most common finishes include polyurethane, oil-based, and water-based finishes.
Polyurethane finishes are highly popular because they form a tough, protective layer that resists scratches and stains. Oil-based finishes penetrate deep into the wood, enhancing its natural beauty and providing a high level of protection. Water-based finishes are chosen for their fast drying times and low VOC (volatile organic compounds) emissions, making them an eco-friendly option.
Before the chosen finish is applied, the planks are sanded once more to ensure a smooth surface. The finish is then applied in multiple coats, allowing each coat to dry and cure completely. This multi-coat process ensures maximum durability and enhances the wood’s natural beauty.
Enhancing Wear Resistance
Even though wood is a durable material, additional treatments can enhance its wear resistance. One of the primary methods is to apply a hardening treatment. This involves using substances like aluminum oxide, which is infused into the finish. Aluminum oxide significantly increases the surface hardness, making the floor more resistance to daily wear and tear.
Another method is UV curing. UV-cured finishes use ultraviolet light to cure the finish rapidly. This process creates an exceptionally durable surface that is more resistant to scratches, chemicals, and general wear compared to traditional finishes.
Some manufacturers also use a technique called “hand scraping.” While primarily done for aesthetic purposes, hand scraping creates texture and depth in the wood, which can help hide future wear and tear. It gives the flooring a distressed look that can mask minor scratches and dents that occur over time.
Quality Control
Quality control is a vital step throughout the manufacturing process to ensure the final product meets high standards. Each plank goes through rigorous inspections to check for defects, consistency in color, and overall quality. This ensures that only the best planks make it to the final packaging stage.
Additionally, tests for durability, moisture content, and fitting accuracy are conducted. These tests guarantee that the wooden flooring will not only look good but will also stand the test of time.
Packaging and Distribution
Once the wooden flooring planks pass quality control, they are ready for packaging. Each plank is carefully wrapped and secured to prevent damage during transportation. Proper labeling ensures that installers can easily identify the type of wood, finish, and any special features of the flooring.
After packaging, the planks are distributed to retailers and customers. It’s important that the transportation process is handled carefully to avoid any moisture or temperature variations, which can affect the wood’s stability.
Installation and Maintenance
While the manufacturing process ensures high-quality wooden flooring, proper installation and maintenance are crucial for its longevity. Professional installation guarantees that the flooring is laid correctly, minimizing gaps and uneven surfaces. Installers often acclimate the wood to the room’s temperature and humidity before installation to prevent issues related to expansion or contraction.
Regular maintenance, such as cleaning and periodic refinishing, can significantly extend the life of wooden flooring. Using the right cleaning products and techniques helps preserve the finish and protect the wood from damage.
In conclusion, the manufacturing process of wooden flooring is meticulous and involves several stages to ensure a durable and aesthetically pleasing product. From selecting high-quality raw materials to enhancing wear resistance through advanced finishing techniques, each step plays a critical role in the final product’s performance.
Understanding these processes can help consumers make informed decisions and appreciate the value of investing in high-quality wooden flooring.
資料ダウンロード
QCD調達購買管理クラウド「newji」は、調達購買部門で必要なQCD管理全てを備えた、現場特化型兼クラウド型の今世紀最高の購買管理システムとなります。
ユーザー登録
調達購買業務の効率化だけでなく、システムを導入することで、コスト削減や製品・資材のステータス可視化のほか、属人化していた購買情報の共有化による内部不正防止や統制にも役立ちます。
NEWJI DX
製造業に特化したデジタルトランスフォーメーション(DX)の実現を目指す請負開発型のコンサルティングサービスです。AI、iPaaS、および先端の技術を駆使して、製造プロセスの効率化、業務効率化、チームワーク強化、コスト削減、品質向上を実現します。このサービスは、製造業の課題を深く理解し、それに対する最適なデジタルソリューションを提供することで、企業が持続的な成長とイノベーションを達成できるようサポートします。
オンライン講座
製造業、主に購買・調達部門にお勤めの方々に向けた情報を配信しております。
新任の方やベテランの方、管理職を対象とした幅広いコンテンツをご用意しております。
お問い合わせ
コストダウンが利益に直結する術だと理解していても、なかなか前に進めることができない状況。そんな時は、newjiのコストダウン自動化機能で大きく利益貢献しよう!
(Β版非公開)