- お役立ち記事
- Manufacturing Process of Wooden Rocking Chairs and Durability Enhancement
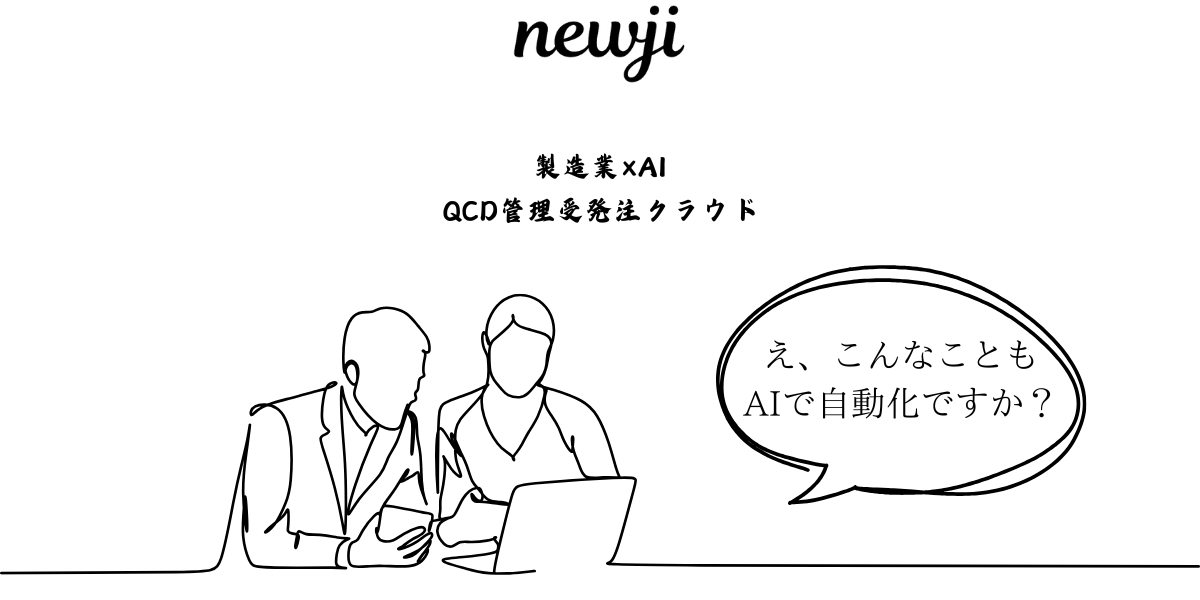
Manufacturing Process of Wooden Rocking Chairs and Durability Enhancement
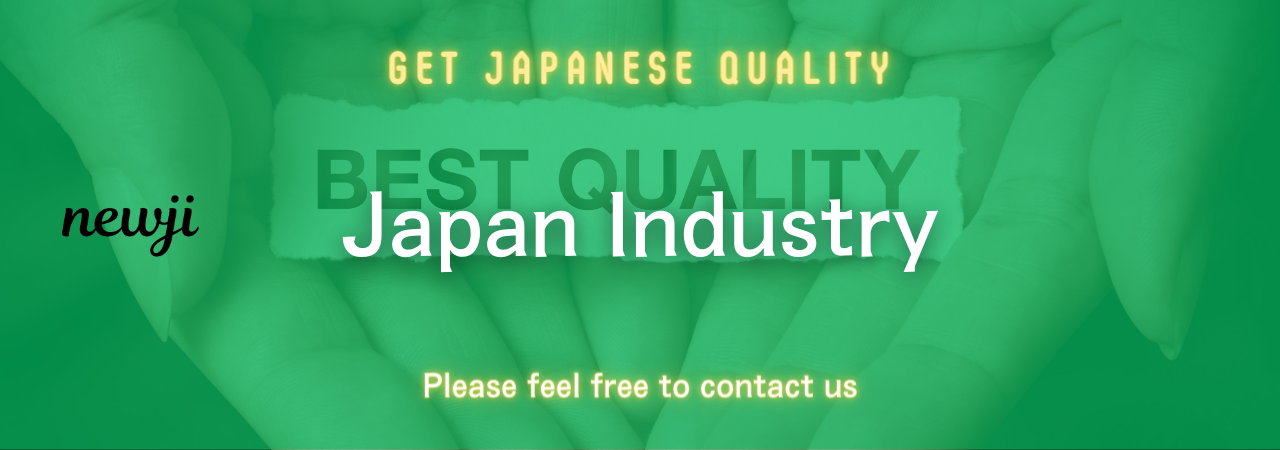
Wooden rocking chairs are timeless pieces of furniture that enhance the aesthetics of any room while providing comfort.
Behind their charming appearance lies a meticulous manufacturing process that combines traditional craftsmanship with modern woodworking techniques.
Understanding the intricate steps involved and the methods employed to enhance their durability offers insight into why these chairs remain a popular choice across generations.
目次
Selection of High-Quality Wood
The journey of crafting a wooden rocking chair begins with the selection of the right type of wood.
Hardwoods like oak, maple, and cherry are often preferred for their strength and appearance.
The wood must be thoroughly inspected to ensure it is free from cracks, knots, and other imperfections that could weaken the chair.
Seasoning and Drying
Once the wood is selected, it undergoes a seasoning process.
This involves drying the wood to reduce its moisture content.
Seasoning prevents the wood from warping or shrinking over time.
Kiln drying is a common method used, as it provides consistent and controlled drying conditions.
Design and Blueprint Creation
The next step is designing the rocking chair.
Modern craftsmen use computer-aided design (CAD) software to create precise blueprints.
These designs include detailed measurements and specifications for each part of the chair.
Traditional artisans may hand-draw their designs, relying on their experience and skill to ensure accuracy.
Prototype Development
Before mass production, a prototype is often created.
This prototype helps in identifying any potential design flaws and allows for adjustments to be made.
It serves as a physical model that guides the production process.
Cutting and Shaping the Components
With the design finalized, the wood is cut into the various components that will make up the chair.
This includes the legs, seat, backrest, armrests, and the curved rockers.
Precision is key, as each piece must fit together perfectly.
Using Jigs and Templates
To ensure consistency, jigs and templates are used during the cutting and shaping process.
These tools help replicate the same shapes and sizes across multiple pieces, maintaining the integrity of the design.
Assembling the Chair
Once all the components are ready, assembly begins.
Traditional joinery techniques such as mortise and tenon joints, dowels, and dovetails are commonly used to connect the pieces.
These methods provide strong, durable connections without relying solely on screws or nails.
Glue and Fasteners
Wood glue is often used in conjunction with joinery techniques to enhance the strength of the connections.
In some cases, screws or nails may be used for additional reinforcement, but they are usually concealed to maintain the aesthetic appeal.
Sanding and Smoothing
After the chair is assembled, it undergoes a thorough sanding process.
This involves smoothing out any rough edges and surfaces to prepare the chair for finishing.
Sanding also helps in highlighting the natural beauty of the wood.
Progressive Sanding
Starting with coarse-grit sandpaper and progressively moving to finer grits ensures a smooth, even surface.
This step is crucial for creating a flawless finish that showcases the quality of the craftsmanship.
Finishing the Chair
Finishing is the final step in the manufacturing process.
It involves applying stains, sealants, or paints to protect the wood and enhance its appearance.
The type of finish used depends on the desired look and the level of protection needed.
Sealants and Varnishes
Sealants and varnishes provide a protective layer that guards against moisture, scratches, and UV damage.
These finishes not only prolong the life of the chair but also highlight the natural grain and color of the wood.
Enhancing Durability
Durability is a crucial factor in the longevity of wooden rocking chairs.
Several techniques are employed to ensure that these chairs withstand the test of time.
Reinforcing Stress Points
Areas of the chair that experience the most stress, such as the joints between the legs and the seat, are reinforced.
Additional support mechanisms, such as metal brackets or extra dowels, may be used to prevent weakening over time.
Weatherproofing
For outdoor rocking chairs, weatherproofing is essential.
Applying specialized coatings that resist moisture, heat, and cold ensures that the chair remains in good condition despite exposure to the elements.
Quality Control and Testing
Before a wooden rocking chair reaches the market, it undergoes rigorous quality control and testing.
Each chair is inspected for structural integrity, ensuring that it meets safety standards and can support the intended weight load.
Load Testing
Load testing involves applying weight to the chair to simulate regular use.
This test helps identify any weaknesses and ensures that the chair can handle everyday wear and tear.
Conclusion
The manufacturing process of wooden rocking chairs and the techniques used to enhance their durability are testaments to the skill and dedication of craftsmen.
From selecting high-quality wood to the meticulous assembly and finishing, each step is carefully executed to create a timeless piece of furniture.
By understanding this process, one can appreciate the intricate craftsmanship that goes into every rocking chair, ensuring they remain a beloved fixture in homes for many years.
資料ダウンロード
QCD調達購買管理クラウド「newji」は、調達購買部門で必要なQCD管理全てを備えた、現場特化型兼クラウド型の今世紀最高の購買管理システムとなります。
ユーザー登録
調達購買業務の効率化だけでなく、システムを導入することで、コスト削減や製品・資材のステータス可視化のほか、属人化していた購買情報の共有化による内部不正防止や統制にも役立ちます。
NEWJI DX
製造業に特化したデジタルトランスフォーメーション(DX)の実現を目指す請負開発型のコンサルティングサービスです。AI、iPaaS、および先端の技術を駆使して、製造プロセスの効率化、業務効率化、チームワーク強化、コスト削減、品質向上を実現します。このサービスは、製造業の課題を深く理解し、それに対する最適なデジタルソリューションを提供することで、企業が持続的な成長とイノベーションを達成できるようサポートします。
オンライン講座
製造業、主に購買・調達部門にお勤めの方々に向けた情報を配信しております。
新任の方やベテランの方、管理職を対象とした幅広いコンテンツをご用意しております。
お問い合わせ
コストダウンが利益に直結する術だと理解していても、なかなか前に進めることができない状況。そんな時は、newjiのコストダウン自動化機能で大きく利益貢献しよう!
(Β版非公開)