- お役立ち記事
- Manufacturing Process of Wooden Rocking Chairs and Durability Reinforcement
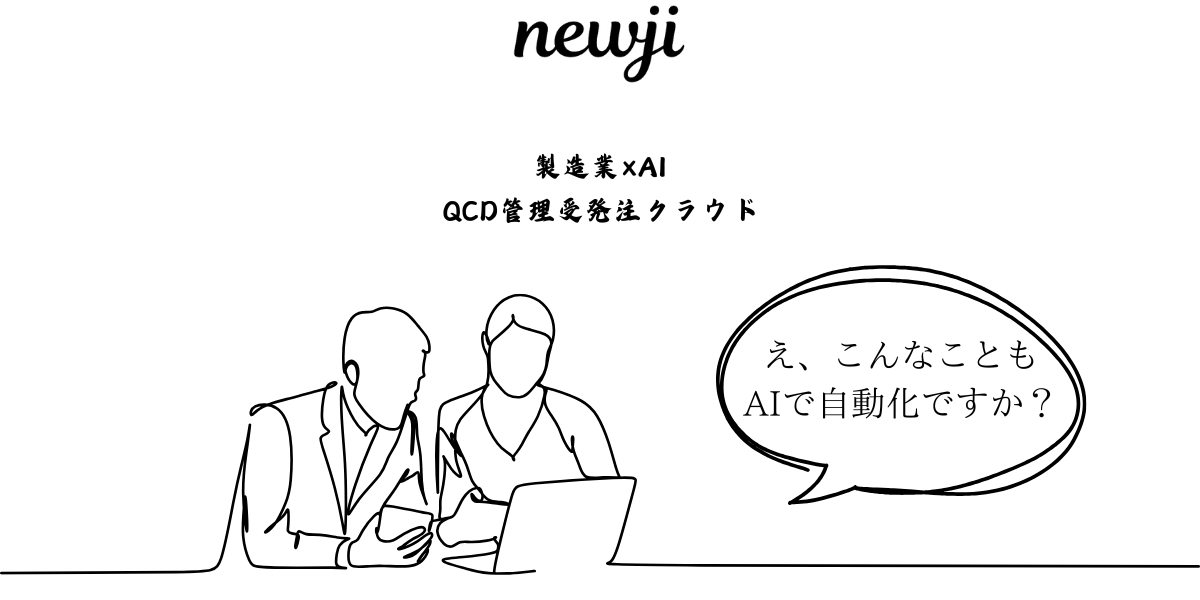
Manufacturing Process of Wooden Rocking Chairs and Durability Reinforcement
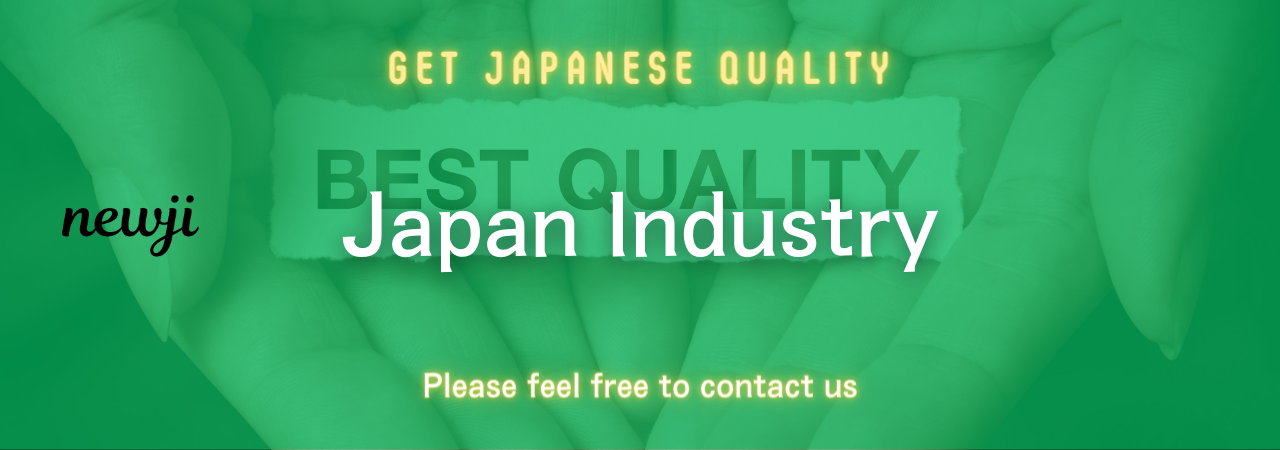
Wooden rocking chairs have been beloved for their comfort and classic charm for generations.
But how exactly are these timeless pieces crafted?
Let’s delve into the manufacturing process of wooden rocking chairs and how their durability can be reinforced.
目次
Selecting the Right Wood
To ensure a sturdy and long-lasting rocking chair, the choice of wood is crucial.
Hardwoods like oak, maple, and cherry are popular because they are durable and can withstand daily use.
These woods also offer a beautiful grain that adds to the chair’s aesthetic appeal.
After choosing the right wood, it is seasoned or kiln-dried to reduce moisture content, minimizing the risk of warping or cracking over time.
Design and Planning
The design phase is where creativity meets practicality.
Detailed blueprints are drawn to ensure that every piece fits perfectly together.
The design includes the backrest, armrests, legs, and the all-important rocking legs.
Measurements must be precise so that the chair will rock smoothly without tipping.
Prototyping
Before mass production, a prototype is often constructed to identify any potential issues.
This step allows for adjustments in size, shape, and stability.
It’s also an opportunity to test ergonomics, ensuring the chair is comfortable for a variety of users.
Cutting and Shaping the Wood
Once the design is finalized, the selected wood is cut into the required pieces.
This involves using machinery like saws, lathes, and routers.
Each piece is shaped according to the design specifications.
The seat and backrest are often curved for comfort, which requires precision shaping.
Special attention is given to the rocking chair’s legs, as their curvature is vital for smooth rocking motion.
Joinery Techniques
Joinery is the woodworking technique used to assemble the various parts of the chair.
Several methods can be employed, such as mortise and tenon joints, dowel joints, and dovetail joints.
Mortise and tenon joints are particularly strong and are frequently used in high-quality rocking chairs.
These joints are glued and often reinforced with wooden pins or screws to ensure they remain secure over time.
Sanding and Smoothing
Before the chair is assembled, each piece undergoes thorough sanding.
This step removes any rough edges or splinters, making the surface smooth and safe to touch.
Sanding also prepares the wood for finishing, ensuring that stains and varnishes adhere properly.
Multiple grits of sandpaper are used, starting with coarse and moving to fine, to achieve a silky finish.
Assembly
The assembly process involves carefully putting together all the components.
The chair is usually assembled in stages, starting with the main frame, followed by the seat and backrest, and finally the armrests and legs.
Each joint is checked for snugness and alignment to ensure the chair is sturdy and well-balanced.
Clamps are often used to hold joints in place while the glue dries.
Finishing
Finishing is a crucial step in the manufacturing process, as it not only enhances the chair’s appearance but also protects the wood.
The chair is often stained to highlight the wood’s natural grain.
This is followed by one or more layers of varnish or lacquer to provide a durable surface.
Some manufacturers use eco-friendly finishes to reduce environmental impact.
The finishing process may involve sanding between coats to achieve a flawless surface.
Quality Control
Before the chair is deemed complete, it undergoes rigorous quality control checks.
Each chair is examined for structural integrity, smoothness of finish, and overall appearance.
Any defects are addressed promptly to ensure the final product meets high-quality standards.
Durability Reinforcement
Ensuring the durability of a wooden rocking chair involves several strategies during both the manufacturing and finishing processes.
Structural Reinforcements
1. **Stronger Joints:** Using reinforced joints, such as mortise and tenon or dovetail joints, adds stability and strength.
2. **Additional Supports:** Cross braces and corner blocks can be added to critical areas to prevent wobbling and ensure longevity.
Protective Finishes
1. **High-Quality Varnishes:** Applying multiple coats of high-quality varnish or lacquer protects the wood from scratches and other damage.
2. **UV-Resistant Coatings:** For outdoor use, UV-resistant finishes help protect the wood from sun damage.
Maintenance Tips
1. **Regular Cleaning:** Dust and dirt can wear down the finish over time, so regular cleaning with a soft cloth is crucial.
2. **Polishing:** Occasional polishing with wood-specific products can maintain the chair’s luster and protect the finish.
3. **Environment Control:** Keeping the chair in a stable environment with moderate humidity and temperature will prevent wood warping and cracking.
Conclusion
The manufacturing process of wooden rocking chairs is a blend of art and science.
From selecting the right wood to reinforcing the structure for durability, every step requires precision and care.
Following these meticulous processes ensures that the final product is not only beautiful but also built to last.
By understanding and appreciating the craftsmanship involved, we can better care for these timeless pieces, ensuring they remain a cherished part of our homes for years to come.
資料ダウンロード
QCD調達購買管理クラウド「newji」は、調達購買部門で必要なQCD管理全てを備えた、現場特化型兼クラウド型の今世紀最高の購買管理システムとなります。
ユーザー登録
調達購買業務の効率化だけでなく、システムを導入することで、コスト削減や製品・資材のステータス可視化のほか、属人化していた購買情報の共有化による内部不正防止や統制にも役立ちます。
NEWJI DX
製造業に特化したデジタルトランスフォーメーション(DX)の実現を目指す請負開発型のコンサルティングサービスです。AI、iPaaS、および先端の技術を駆使して、製造プロセスの効率化、業務効率化、チームワーク強化、コスト削減、品質向上を実現します。このサービスは、製造業の課題を深く理解し、それに対する最適なデジタルソリューションを提供することで、企業が持続的な成長とイノベーションを達成できるようサポートします。
オンライン講座
製造業、主に購買・調達部門にお勤めの方々に向けた情報を配信しております。
新任の方やベテランの方、管理職を対象とした幅広いコンテンツをご用意しております。
お問い合わせ
コストダウンが利益に直結する術だと理解していても、なかなか前に進めることができない状況。そんな時は、newjiのコストダウン自動化機能で大きく利益貢献しよう!
(Β版非公開)