- お役立ち記事
- Manufacturing Techniques and Advantages of Aluminum Castings
Manufacturing Techniques and Advantages of Aluminum Castings
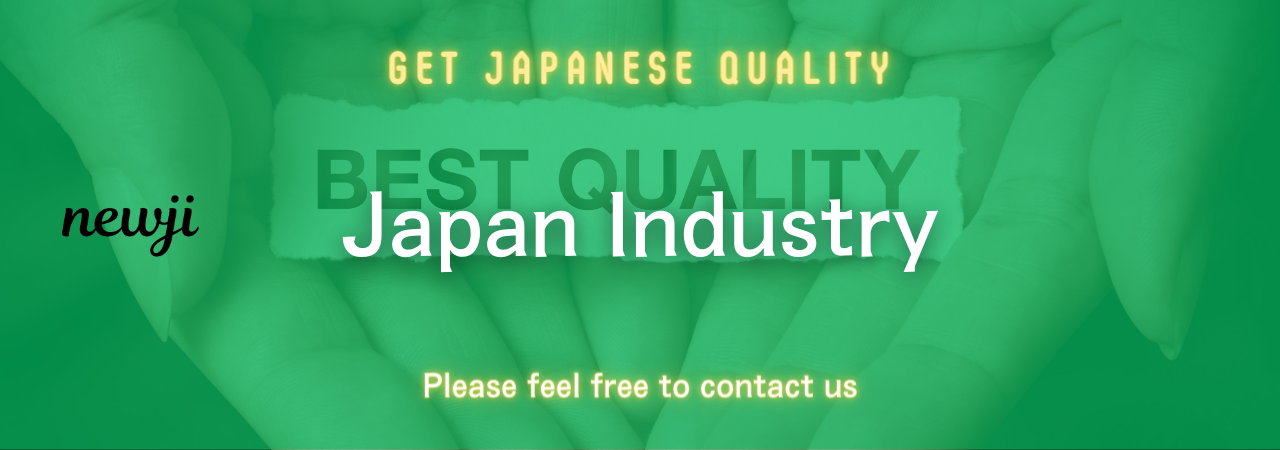
Aluminum castings play a pivotal role in modern manufacturing, thanks to their versatility, strength, and lightweight properties.
Used across various industries, from automotive to aerospace, aluminum castings are crucial components that contribute to efficient and innovative engineering solutions.
This article explores the manufacturing techniques and advantages of aluminum castings in detail.
目次
What are Aluminum Castings?
Aluminum castings involve pouring molten aluminum into a mold to create specific shapes.
These shapes can range from simple to highly complex, depending on the manufacturing requirements of different industries.
Once the aluminum cools and solidifies, it is removed from the mold, resulting in a final product that is both durable and lightweight.
Manufacturing Techniques of Aluminum Castings
The process of creating aluminum castings involves various techniques, each suited to specific applications and product demands.
Understanding these methods can help manufacturers choose the right approach to meet their needs.
1. Die Casting
Die casting is a popular technique known for its high precision and rapid production capabilities.
In this method, molten aluminum is forced into a steel die under high pressure, which allows for detailed and accurate designs.
Die casting is especially suitable for mass production because it can quickly produce large quantities of identical parts with minimal waste.
2. Sand Casting
Sand casting is one of the oldest and most versatile casting methods.
It involves compacting moist sand around a pattern to form a mold cavity.
Molten aluminum is then poured into the cavity to create the casting.
Sand casting is adaptable and cost-effective, making it ideal for producing large and heavy components or for lower production volumes.
3. Permanent Mold Casting
Permanent mold casting uses reusable molds, usually made from metal, to create aluminum castings.
This technique is excellent for medium to high-volume production runs as the molds can be used repeatedly, reducing long-term costs.
Products made using permanent mold casting often have superior mechanical properties and better surface finishes compared to sand castings.
4. Investment Casting
Investment casting, also known as lost-wax casting, involves creating a wax pattern that is coated with a ceramic material.
Once the ceramic hardens, the wax is melted and drained away, leaving a mold cavity.
Molten aluminum is then poured into the cavity to form the casting.
This method is ideal for producing intricate and detailed parts with high precision.
Advantages of Aluminum Castings
Aluminum castings offer numerous benefits, making them a preferred choice for many industries.
1. Lightweight and Strong
One of the primary advantages of aluminum is its excellent strength-to-weight ratio.
Aluminum castings provide the necessary strength while being significantly lighter than other metals like steel.
This characteristic is particularly beneficial in industries such as aerospace and automotive, where weight reduction leads to improved fuel efficiency and performance.
2. Corrosion Resistance
Aluminum naturally forms a protective oxide layer when exposed to air, which helps resist corrosion.
This makes aluminum castings ideal for applications that involve exposure to harsh environmental conditions, such as in marine and industrial settings.
3. Versatility and Design Flexibility
Aluminum castings can be produced in a wide range of shapes and sizes, from small intricate parts to large structural components.
The various casting techniques available allow for high design flexibility, enabling manufacturers to create complex geometries and features that might be challenging with other materials.
4. Excellent Thermal and Electrical Conductivity
Aluminum has superb thermal and electrical conductivity properties.
This makes aluminum castings suitable for applications in the electronics and electrical industries, where efficient heat dissipation and conductivity are critical requirements.
5. Cost-Effective Production
The casting process, particularly for aluminum, can be more cost-effective than other manufacturing methods.
Processes like die casting and permanent mold casting allow for high-volume production with a lower per-unit cost.
Furthermore, aluminum is an abundant material, which helps keep raw material costs reasonable.
6. Recyclability
Aluminum is highly recyclable, making it an environmentally friendly manufacturing option.
Recycling aluminum requires only a fraction of the energy needed to produce new aluminum from ore, leading to significant energy savings and reduced environmental impact.
This aspect is increasingly important as industries strive for sustainable manufacturing practices.
Applications of Aluminum Castings
The diverse properties of aluminum castings make them suitable for a wide range of applications across various sectors.
1. Automotive Industry
In the automotive sector, aluminum castings are used for engine blocks, transmission housings, wheels, and various other components.
The reduced weight of aluminum cast parts contributes to better fuel efficiency and lower emissions, aligning with the industry’s push for greener technologies.
2. Aerospace Industry
The aerospace industry relies heavily on aluminum castings for components that require high strength and low weight, such as aircraft fuselage parts, engine components, and landing gear assemblies.
The corrosion resistance of aluminum also makes it ideal for demanding aerospace environments.
3. Construction Industry
In construction, aluminum castings are used in structural components, building facades, and architectural features.
The material’s strength-to-weight ratio and corrosion resistance make it perfect for both structural and decorative purposes.
4. Electronics and Electrical Industries
Aluminum’s excellent thermal and electrical conductivity make it a preferred choice for electrical enclosures, heat sinks, and various electronic components.
The ability to efficiently manage heat and electrical flow is crucial for the durability and performance of electronic devices.
5. Industrial Equipment
Industrial machinery and equipment often incorporate aluminum castings due to their durability, corrosion resistance, and ease of maintenance.
Components like pumps, valves, and gear housings benefit from aluminum’s properties, leading to increased lifespan and reduced downtime.
Conclusion
Aluminum castings are indispensable in modern manufacturing, offering a combination of strength, light weight, corrosion resistance, and design flexibility.
The various casting techniques available allow manufacturers to choose the best method for their specific needs, ensuring efficient and cost-effective production.
As industries continue to advance towards sustainable and innovative solutions, the use of aluminum castings is likely to grow, further solidifying their importance in a wide range of applications.
資料ダウンロード
QCD調達購買管理クラウド「newji」は、調達購買部門で必要なQCD管理全てを備えた、現場特化型兼クラウド型の今世紀最高の購買管理システムとなります。
ユーザー登録
調達購買業務の効率化だけでなく、システムを導入することで、コスト削減や製品・資材のステータス可視化のほか、属人化していた購買情報の共有化による内部不正防止や統制にも役立ちます。
NEWJI DX
製造業に特化したデジタルトランスフォーメーション(DX)の実現を目指す請負開発型のコンサルティングサービスです。AI、iPaaS、および先端の技術を駆使して、製造プロセスの効率化、業務効率化、チームワーク強化、コスト削減、品質向上を実現します。このサービスは、製造業の課題を深く理解し、それに対する最適なデジタルソリューションを提供することで、企業が持続的な成長とイノベーションを達成できるようサポートします。
オンライン講座
製造業、主に購買・調達部門にお勤めの方々に向けた情報を配信しております。
新任の方やベテランの方、管理職を対象とした幅広いコンテンツをご用意しております。
お問い合わせ
コストダウンが利益に直結する術だと理解していても、なかなか前に進めることができない状況。そんな時は、newjiのコストダウン自動化機能で大きく利益貢献しよう!
(Β版非公開)