- お役立ち記事
- Manufacturing technology for high-temperature resistant ceramics and its application in the automobile market [for engineers]
月間76,176名の
製造業ご担当者様が閲覧しています*
*2025年3月31日現在のGoogle Analyticsのデータより
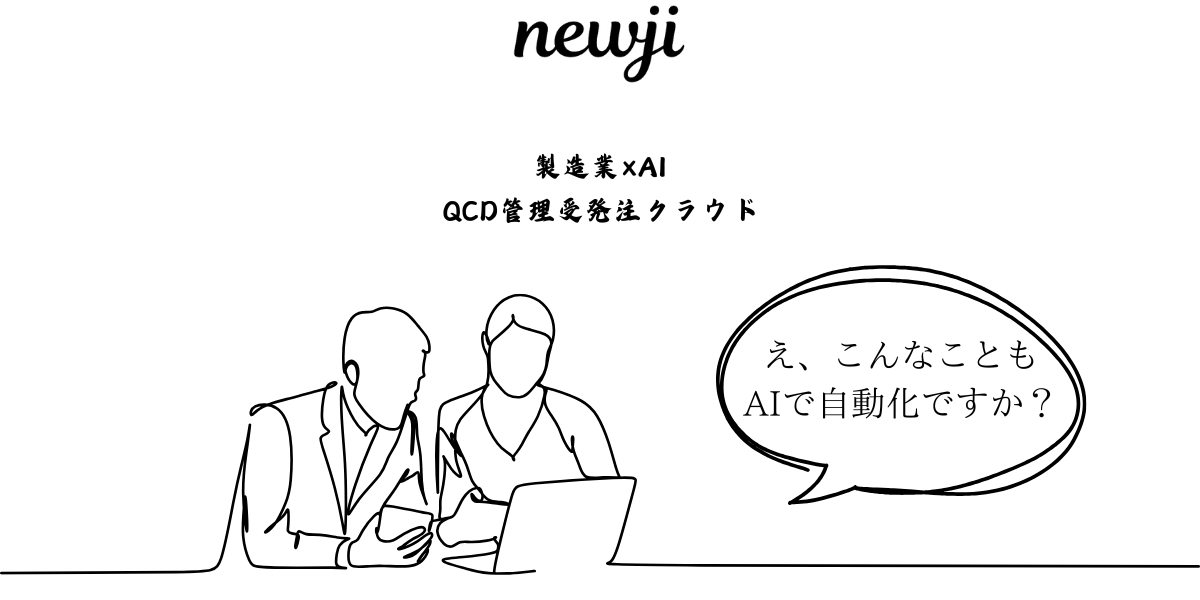
Manufacturing technology for high-temperature resistant ceramics and its application in the automobile market [for engineers]
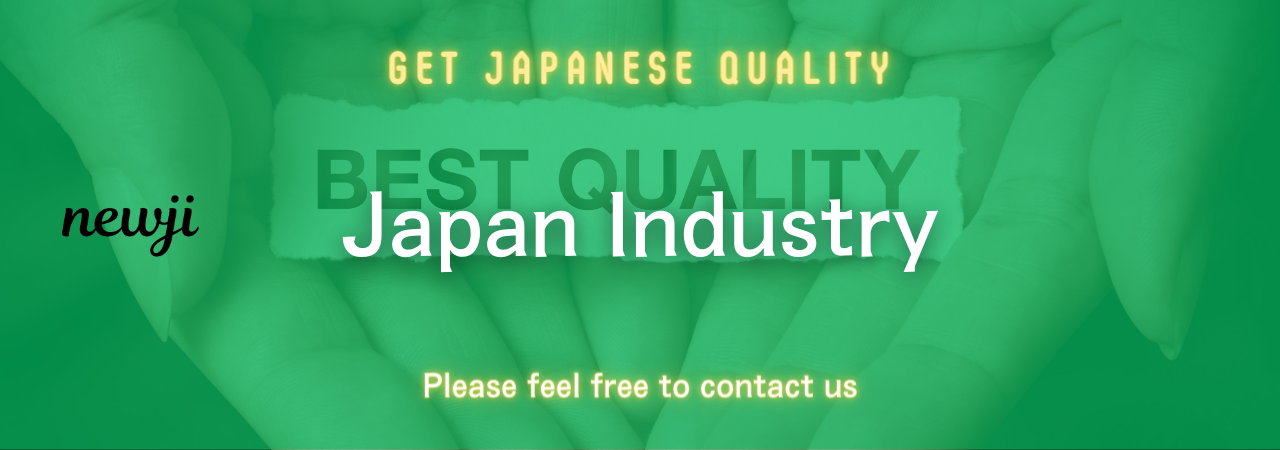
目次
Understanding High-Temperature Resistant Ceramics
In the world of manufacturing, high-temperature resistant ceramics hold a significant position, particularly in industries requiring materials that can withstand extreme heat.
These advanced materials are engineered to maintain their structural integrity and functional properties under harsh thermal conditions, making them invaluable to various sectors, including the automotive industry.
High-temperature ceramics are primarily composed of compounds like aluminum oxide, silicon carbide, and zirconium dioxide.
These compounds are selected for their ability to endure temperatures that would substantially damage more traditional materials, such as metals.
Ceramics are inorganic, non-metallic solids that are processed and used in a multitude of applications due to their outstanding material properties.
In high-temperature scenarios, these properties include high oxidation resistance, superb thermal insulation, and low thermal expansion.
Such characteristics make these ceramics suitable for applications that metals or polymers might fail to perform under intense heat.
Manufacturing Processes of High-Temperature Ceramics
High-temperature ceramics are manufactured through various sophisticated techniques that contribute to their exemplary performance in thermal endurance.
Understanding these processes is crucial for engineers working in fields where these materials are utilized.
1. Powder Processing
The manufacturing process often begins with powder processing.
This involves the selection and mixture of raw materials in their powdered form.
This stage is vital as it determines the chemical composition and, consequently, the performance characteristics of the final ceramic product.
2. Sintering
After the powders are correctly mixed, sintering follows.
This process involves heating the compacted powder at temperatures below its melting point until the particles adhere to form a solid mass.
Sintering increases the strength and density of the ceramic, making it capable of withstanding high temperatures.
3. Hot Pressing
For applications requiring even greater density and strength, hot pressing might be used.
This technique combines the process of sintering with compressive forces applied during heating.
Hot pressing effectively reduces porosity and increases the ceramic’s resistance to extreme conditions.
4. Machining and Finishing
The final manufacturing step typically involves machining and finishing, where the ceramics are cut and shaped into their required forms.
This step is critical as it allows for precision and exact scaling, ensuring the ceramics fit their designated applications perfectly.
Applications in the Automobile Market
The automotive industry is one of the main beneficiaries of high-temperature resistant ceramics.
Their application in this field is vast and varied, leading to improvements in vehicle efficiency, safety, and performance.
1. Engine Components
A primary application of these ceramics is in engine components.
High-temperature ceramics like silicon carbide and aluminum oxide are used for parts that encounter intense thermal cycles.
These materials help in constructing components such as pistons, exhaust manifolds, and turbocharger rotors that must endure high heat.
The result is enhanced engine efficiency and longevity, as ceramic components do not degrade as fast as their metallic counterparts under thermal stress.
2. Brake Systems
In braking systems, ceramics are favored for their wear resistance and high-temperature stability.
Ceramic brake discs, for instance, offer superior performance by maintaining consistent braking performance under extreme conditions and reducing brake fade.
This not only enhances safety but also ensures durability, leading to reduced maintenance costs over the vehicle’s lifespan.
3. Insulation and Seals
Another significant application of high-temperature ceramics in automobiles is their use in insulation and sealing technologies.
Ceramic coatings provide effective thermal barriers to protect sensitive components.
Heat shields composed of ceramic materials prevent unwanted heat transfer, ensuring optimal performance of various engine parts.
These ceramics also serve in creating air-tight seals in engines and exhaust systems, preventing leaks and maintaining efficiency.
4. Electric and Hybrid Vehicles
The rise of electric and hybrid vehicles has further expanded the application of high-temperature ceramics.
In these vehicles, ceramics are used to insulate batteries and electronic components from heat, enhancing their reliability and longevity.
Ceramics support the vehicle’s thermal management systems, essential for maintaining optimal operating temperatures and ensuring efficient energy consumption.
Future Prospects and Innovations
The evolving landscape of manufacturing technology and automotive design continuously propels innovation in the field of high-temperature resistant ceramics.
As engineers push the boundaries of what’s possible, the future looks promising for these materials.
Advancements in nanotechnology and material science are anticipated to lead to even more resilient ceramic composites.
These innovations might reduce production costs, making high-performance ceramics more accessible to broader automotive applications.
Moreover, the integration of smart technologies and sensors into ceramic materials could provide real-time monitoring capabilities for vehicles.
This could lead to further advancements in predictive maintenance and overall vehicle performance optimization.
In conclusion, high-temperature resistant ceramics are indispensable to the modern automotive market.
Their advanced manufacturing processes and application in critical areas of vehicle design and engineering underscore their importance.
As technology advances, the role of these ceramics in ensuring efficiency, safety, and sustainability in automobiles will only continue to grow, offering exciting opportunities for engineers and manufacturers alike.
資料ダウンロード
QCD管理受発注クラウド「newji」は、受発注部門で必要なQCD管理全てを備えた、現場特化型兼クラウド型の今世紀最高の受発注管理システムとなります。
ユーザー登録
受発注業務の効率化だけでなく、システムを導入することで、コスト削減や製品・資材のステータス可視化のほか、属人化していた受発注情報の共有化による内部不正防止や統制にも役立ちます。
NEWJI DX
製造業に特化したデジタルトランスフォーメーション(DX)の実現を目指す請負開発型のコンサルティングサービスです。AI、iPaaS、および先端の技術を駆使して、製造プロセスの効率化、業務効率化、チームワーク強化、コスト削減、品質向上を実現します。このサービスは、製造業の課題を深く理解し、それに対する最適なデジタルソリューションを提供することで、企業が持続的な成長とイノベーションを達成できるようサポートします。
製造業ニュース解説
製造業、主に購買・調達部門にお勤めの方々に向けた情報を配信しております。
新任の方やベテランの方、管理職を対象とした幅広いコンテンツをご用意しております。
お問い合わせ
コストダウンが利益に直結する術だと理解していても、なかなか前に進めることができない状況。そんな時は、newjiのコストダウン自動化機能で大きく利益貢献しよう!
(β版非公開)