- お役立ち記事
- Mass Production Line Construction and Effectiveness: Improving Production Efficiency and Cost Reduction Methods
Mass Production Line Construction and Effectiveness: Improving Production Efficiency and Cost Reduction Methods
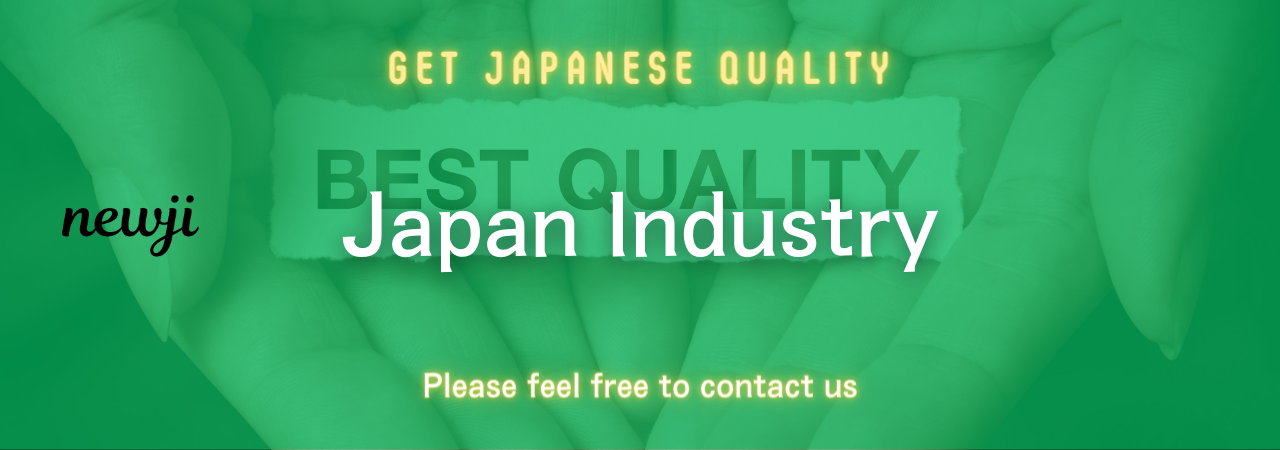
In today’s fast-paced industrial world, mass production lines are essential for manufacturing many types of products quickly and efficiently. From cars to electronics, the ability to produce large quantities of items consistently and at a low cost is crucial for companies to stay competitive. Understanding how to build and maintain an effective mass production line can lead to significant improvements in production efficiency and cost reduction.
目次
What is a Mass Production Line?
A mass production line involves a series of workstations connected by a conveyor system, where each station completes a specific task on the product. This method allows for the production of large volumes of identical products. The key principle behind mass production is division of labor, where tasks are divided into smaller, repetitive actions that can be performed quickly by specialized workers or machines.
Benefits of Mass Production
1. **Higher Efficiency**: By standardizing tasks and using an assembly line, companies can significantly reduce production time. This leads to faster turnaround times and the ability to meet high consumer demand.
2. **Cost Reduction**: Mass production often reduces the cost per unit as the fixed costs are spread over a larger number of units. Bulk purchasing of raw materials also benefits from economies of scale, further driving down costs.
3. **Consistency and Quality Control**: With each worker or machine responsible for a specific task, the risk of errors decreases. This specialization ensures a consistent level of quality in all produced items.
4. **Scalability**: Mass production lines can be adjusted to produce more or fewer items by simply adding or removing certain workstations or adjusting the pace of the conveyor belt.
Steps to Building an Effective Mass Production Line
1. **Planning**: The first step involves detailed planning. Understanding the product requirements, the necessary equipment, and the layout of the production line is crucial. This stage may involve creating prototypes and testing different line designs.
2. **Acquiring Equipment**: The next step is obtaining the machines and tools needed for production. This can include conveyor belts, robotic arms, and specialized machinery for tasks like welding or painting.
3. **Hiring and Training Workers**: Skilled labor is essential for operating and maintaining the production line. Employees should be trained on their specific roles, safety procedures, and how to handle any potential issues that may arise during production.
4. **Setting Up the Production Line**: Once the planning, equipment, and workforce are in place, setting up the production line begins. This often involves physically assembling the machinery and setting up the conveyor system.
5. **Testing and Optimization**: Before full-scale production begins, the line should be tested to identify any inefficiencies or problems. Continuous monitoring and adjustments ensure that the production line operates at optimal efficiency.
Improving Production Efficiency
1. **Automation**: Incorporating automation can drastically improve efficiency. Robots and automated systems can work faster than humans and perform repetitive tasks without fatigue.
2. **Lean Manufacturing**: Adopting lean manufacturing principles focuses on waste reduction and continuous improvement. Techniques such as Just-in-Time (JIT) inventory systems ensure materials are only ordered and received as they are needed, reducing storage costs and waste.
3. **Maintenance**: Regular maintenance of machines and equipment prevents breakdowns and ensures smooth operation. A well-maintained production line is less likely to face unexpected downtime.
4. **Employee Training**: Continuously training employees on the latest techniques and technologies can lead to process improvements and innovation on the production floor.
5. **Data Analysis**: Using data analytics to monitor the production process can help identify bottlenecks and areas for improvement. Real-time data allows for quick adjustments and more informed decision-making.
Cost Reduction Methods
1. **Outsourcing**: Certain parts of the production process can be outsourced to companies that specialize in them. This can reduce labor costs and increase efficiency.
2. **Energy Efficiency**: Implementing energy-efficient practices and investing in energy-saving equipment can lower utility costs. Measures can include using energy-efficient lighting, optimizing heating and cooling systems, and using renewable energy sources.
3. **Bulk Purchasing**: Buying raw materials in large quantities can lower the unit cost. Companies should negotiate with suppliers to get the best deals for bulk purchases.
4. **Minimizing Waste**: Waste in both materials and time can be a significant cost. Implementing recycling programs and optimizing material usage helps reduce waste.
5. **Supplier Relationships**: Building strong relationships with suppliers can lead to better terms and more reliable deliveries, which can reduce costs associated with delays or quality issues.
Conclusion
Mass production lines are a cornerstone of modern manufacturing, offering enhanced efficiency, cost reduction, and consistent quality. By understanding the principles of mass production and continuously looking for ways to improve and streamline the process, companies can maintain a competitive edge in the market. From detailed planning to embracing automation and lean manufacturing techniques, various strategies can lead to significant improvements in production efficiency and cost reduction.
Whether a company is just starting to build its first production line or looking to optimize an existing one, continual assessment, and adaptation are crucial. By embracing advancements in technology and maintaining a focus on efficient practices, businesses can sustainably grow and meet market demands.
資料ダウンロード
QCD調達購買管理クラウド「newji」は、調達購買部門で必要なQCD管理全てを備えた、現場特化型兼クラウド型の今世紀最高の購買管理システムとなります。
ユーザー登録
調達購買業務の効率化だけでなく、システムを導入することで、コスト削減や製品・資材のステータス可視化のほか、属人化していた購買情報の共有化による内部不正防止や統制にも役立ちます。
NEWJI DX
製造業に特化したデジタルトランスフォーメーション(DX)の実現を目指す請負開発型のコンサルティングサービスです。AI、iPaaS、および先端の技術を駆使して、製造プロセスの効率化、業務効率化、チームワーク強化、コスト削減、品質向上を実現します。このサービスは、製造業の課題を深く理解し、それに対する最適なデジタルソリューションを提供することで、企業が持続的な成長とイノベーションを達成できるようサポートします。
オンライン講座
製造業、主に購買・調達部門にお勤めの方々に向けた情報を配信しております。
新任の方やベテランの方、管理職を対象とした幅広いコンテンツをご用意しております。
お問い合わせ
コストダウンが利益に直結する術だと理解していても、なかなか前に進めることができない状況。そんな時は、newjiのコストダウン自動化機能で大きく利益貢献しよう!
(Β版非公開)